- Product Details
- {{item.text}}
Quick Details
-
Place of Origin:
-
Guangdong, China
-
Brand Name:
-
HONGMING
-
Voltage:
-
380V
-
Power:
-
750~800kw
-
Dimension(L*W*H):
-
9500mm8100mmx3650mm, 9500mm8100mmx3650mm
-
Weight:
-
34000 kg
-
Product name:
-
Two - stage three - station pulp molding machine
-
Brand:
-
Hongming
-
Name:
-
Pulp molding machine
-
Control system:
-
PLC)
-
After Warranty Service:
-
Video technical support, Online support, Spare parts, Field maintenance and repair service
-
Local Service Location:
-
Viet Nam, India, Malaysia, South Korea
-
Certification:
-
ce
-
After-sales Service Provided:
-
Video technical support, Field maintenance and repair service, Online support
Quick Details
-
Production Capacity:
-
45 ~ 150 seconds/die
-
Product Type:
-
Paper machine
-
Processing Type:
-
Pulp molding machine
-
Place of Origin:
-
Guangdong, China
-
Brand Name:
-
HONGMING
-
Voltage:
-
380V
-
Power:
-
750~800kw
-
Dimension(L*W*H):
-
9500mm8100mmx3650mm, 9500mm8100mmx3650mm
-
Weight:
-
34000 kg
-
Product name:
-
Two - stage three - station pulp molding machine
-
Brand:
-
Hongming
-
Name:
-
Pulp molding machine
-
Control system:
-
PLC)
-
After Warranty Service:
-
Video technical support, Online support, Spare parts, Field maintenance and repair service
-
Local Service Location:
-
Viet Nam, India, Malaysia, South Korea
-
Certification:
-
ce
-
After-sales Service Provided:
-
Video technical support, Field maintenance and repair service, Online support
Product Description
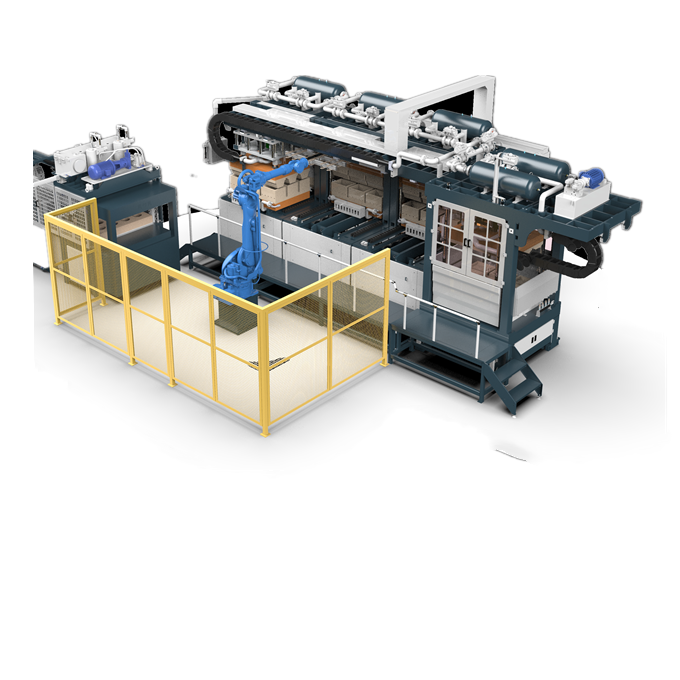
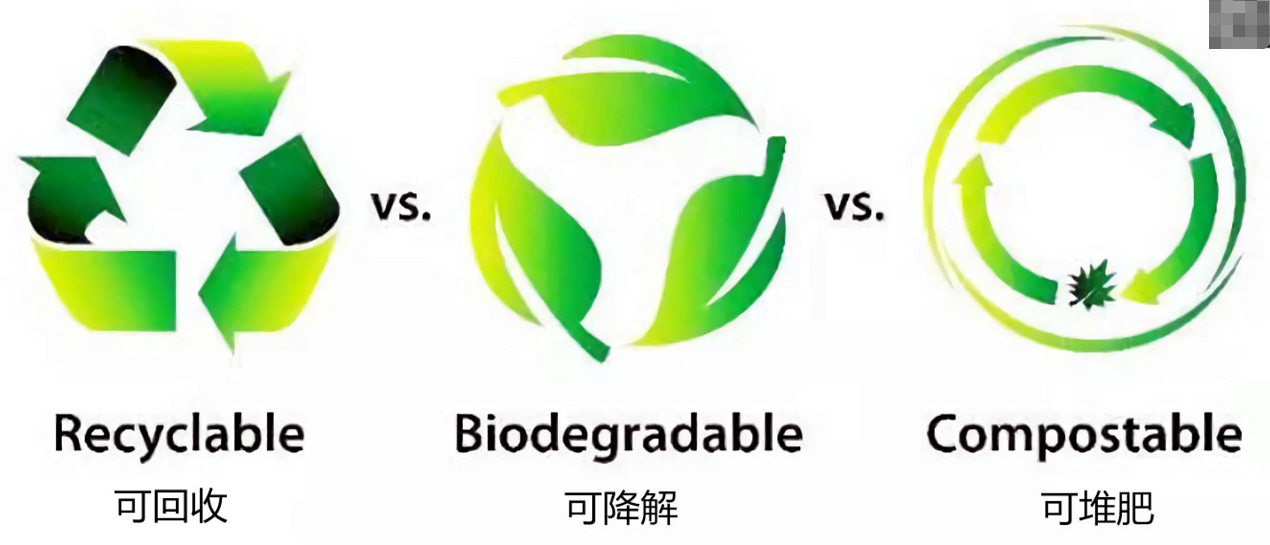
Overview of the machine: Operator is divided into four parts, fish paste, hot pressing, hot pressing 2, hot-pressing three parts, wet after they were fished out slurry pumping pressure intervention, preloading die out after preloading, preloading (mould here only do) and then hot pressing the preloading wet handling to hot pressing mould (2 of hot-pressing a here, hot pressing, hot pressing three) Shared wet billet handling module, wet handling module and servo drive, one to three. The machine adopts direct hot pressing drying forming technology, no need to use oven. After hot pressing, the die exits, the handling robot will be formed after the semi product is directly absorbed and transported to the cutting machine under the die, the cutting machine after cutting, the single shaft manipulator will suck out the finished product placed on the assembly line. This production line can be widely used in the production of moulded tableware, quality work bag drawing die slope 1.5 degrees and other products.
Specification
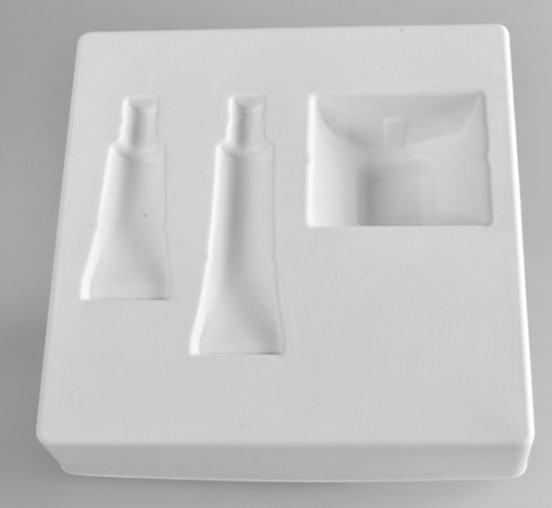
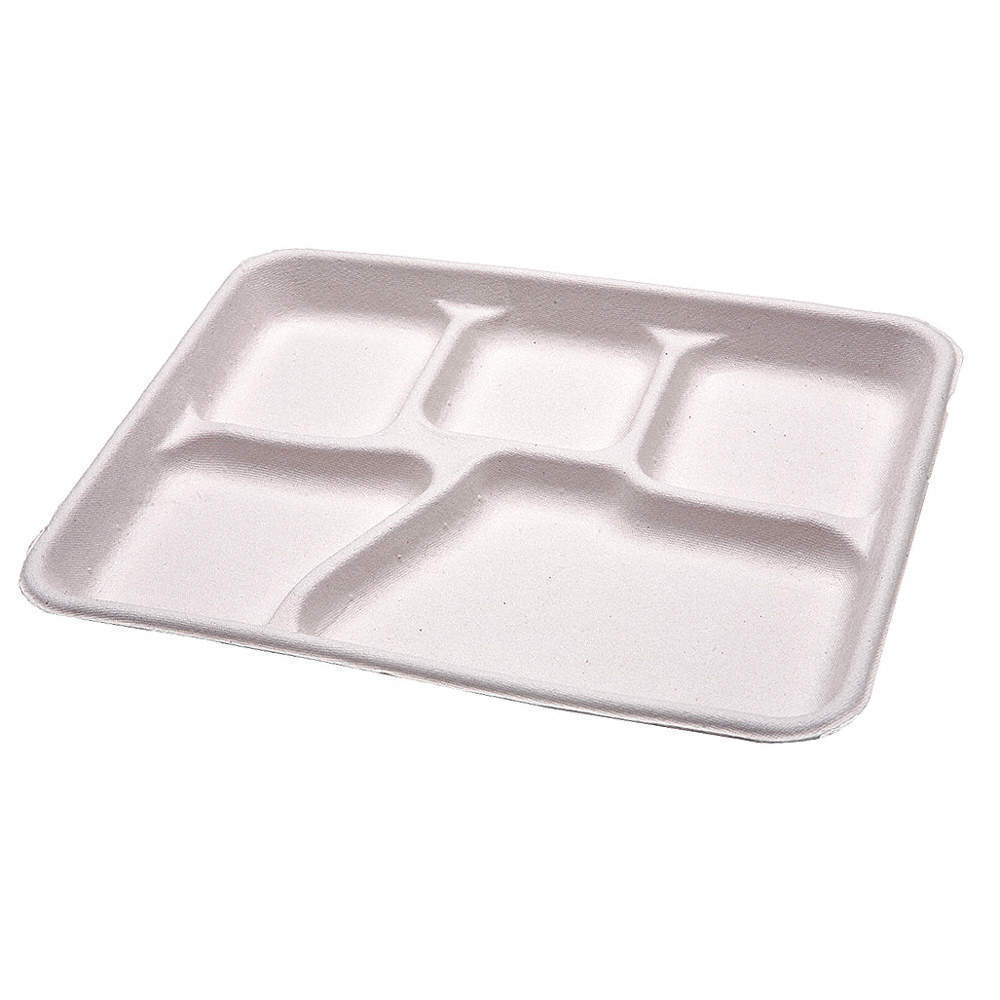
1.Steel beam structure: use high density carbon steel after welding and then annealing process to enhance the stability of the machine.
2.
The parts in direct contact with the wet pulp are made of stainless steel: such as the forming platform, the storage barrel.. Etc.
3.M
achine template area: length: 1300mm; Width: 1000 mm
4.
The upper two connecting platforms (forming and hot pressing platforms) are driven by servomotor to ensure fast and stable operation of the equipment
5.
Before and after the movement distance: 1100mm
6.
The moving power of the platform is driven by oil pressure pump, the moving distance is 500mm, and the mold closing pressure is 10 tons.
7.
The vertical moving power of the hot pressing platform is driven by oil pressure pump, and the clamping force is 28-30 tons. Vertical movement distance: 450mm
8.
Maximum product 120 mm
9.
The hot pressing platform of the machine is equipped with water cold plate to increase the precision of clamping.
10.
The machine is equipped with stable blowing and suction system and vacuum system to facilitate semi-finished product mold crossing and finished product demolding.
11.
Production capacity 45~150 seconds/mold (different product cycle cycle) Actual power consumption varies from product to product.
12.
Machine heating source: electric heating 48.
Hot Searches