- Product Details
- {{item.text}}
Quick Details
-
Model Number:
-
60
-
Thickness:
-
0.8-50mm
-
Size:
-
1300*900mm
-
Density:
-
30-150kg/m3
-
Advantage:
-
light weight
-
Colour:
-
white
-
Usage:
-
bike. UAV/marine
-
Surface:
-
plain
-
Keyword:
-
PMI foam
-
Sample:
-
allowed
-
Product name:
-
PMI foam as composite sandwich panel
-
Shape:
-
rectangle
-
Feature:
-
High Impact Resistance
Quick Details
-
Processing Service:
-
Cutting, Moulding
-
Place of Origin:
-
SHN
-
Brand Name:
-
Binnggo
-
Model Number:
-
60
-
Thickness:
-
0.8-50mm
-
Size:
-
1300*900mm
-
Density:
-
30-150kg/m3
-
Advantage:
-
light weight
-
Colour:
-
white
-
Usage:
-
bike. UAV/marine
-
Surface:
-
plain
-
Keyword:
-
PMI foam
-
Sample:
-
allowed
-
Product name:
-
PMI foam as composite sandwich panel
-
Shape:
-
rectangle
-
Feature:
-
High Impact Resistance
Product Description
Polymethacrylimide (PMI) foam is a closed-cell rigid foam material with excellent performance and first-class quality. It can be used as a core material for high-performance fiber composite sandwich structure to solve general foam core materials. The problem is low specific strength, low specific modulus, and low heat resistance.
PMI foam cores have mainly been used in higher performance composite parts such as helicopter rotor blades, ailerons and stringer profiles in pressure bulkheads, high speed trains, UAVs, medical equipments, radome and antennas
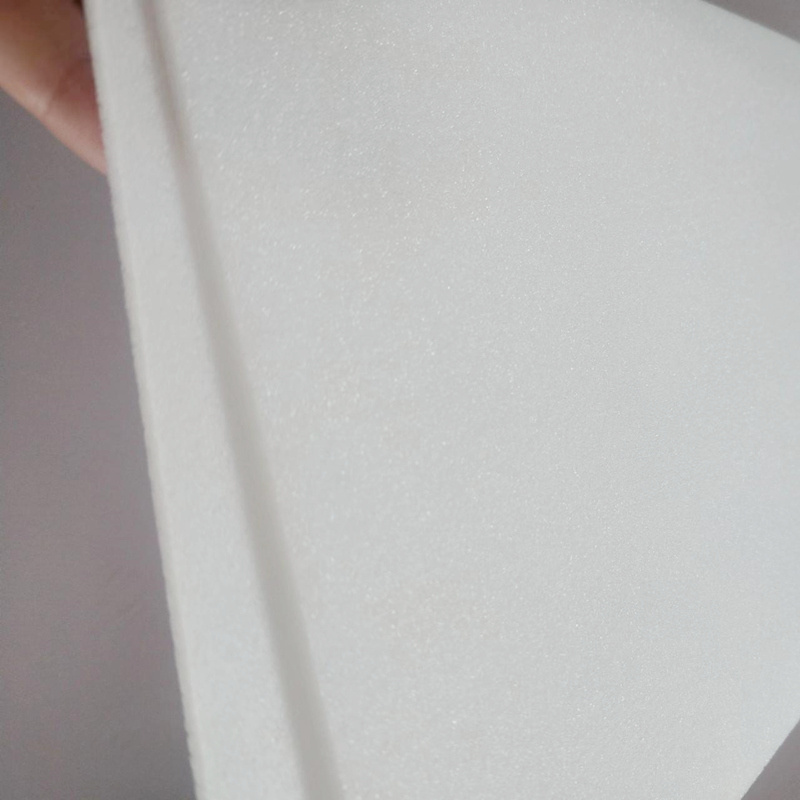
Company Introduction
PMI stands for polymethacrylimide. PMI foam cores are one of the strongest options for building Sandwich composite panels. For the same density, PMI foam cores offer some of the highest overall strengths and stiffnesses of foam cores.
Their characteristics also include high dimensional stability, a closed cell structure and high fatigue life. They can be cured
and used at elevated temperatures
Their characteristics also include high dimensional stability, a closed cell structure and high fatigue life. They can be cured
and used at elevated temperatures
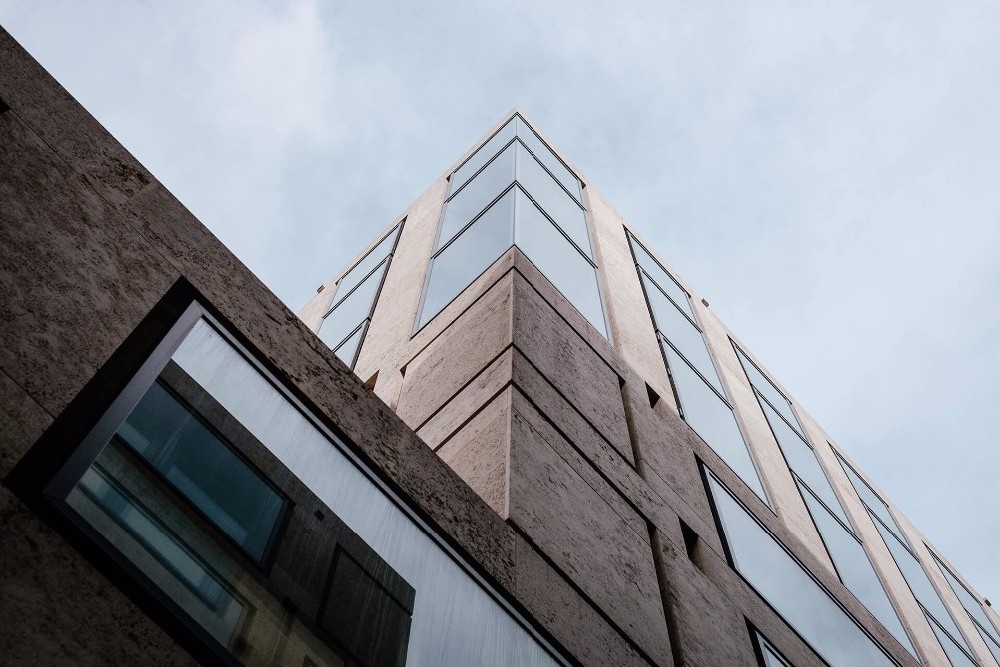
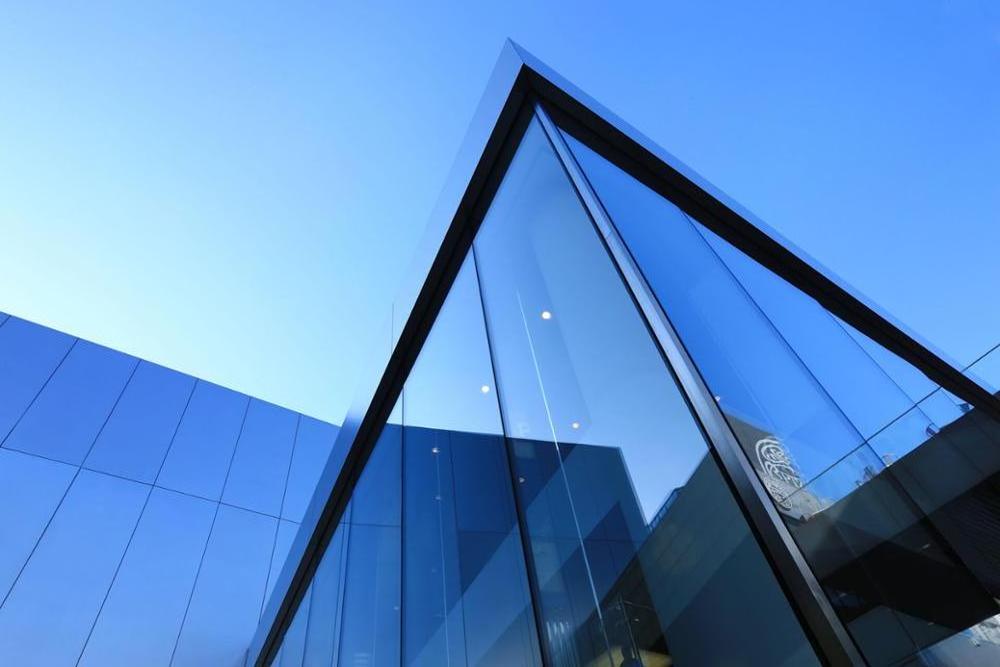
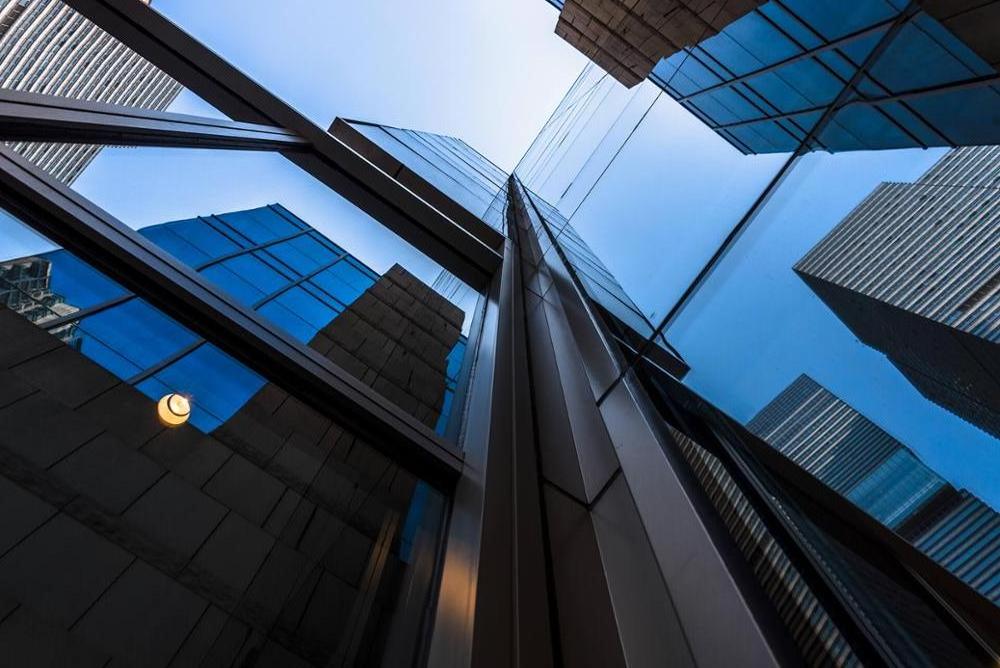
why choose PMI foam?
* High mechanical properties: It has high specific strength and high specific modulus. Its tensile, compressive, bending and shear strength and modulus are far superior to those of other foams or light wood cores, such as PVC, PU, PET, and are isotropic. It can improve strength, improve rigidity and reduce weight.
* High heat resistance: It has unique cross-linking structure, imide ring structure, high temperature stability and good pressure resistance. The hot deformation temperature is over 200 C. It is suitable for high temperature moulding or vacuum hot pressing tank co-curing process, shortening process time, improving production efficiency and improving structural performance.
* High closure rate: 95%-98% closure rate. Used in composite sandwich structure, it can avoid moisture absorption and degumming problems of honeycomb core material, improve safety performance and prolong service life. Because of its high porosity and water pressure resistance, it can be used as underwater buoyancy material.
* Barrier performance: Because of its high closed porosity and fine and uniform bubbles, the material has good sound insulation, heat insulation and moisture insulation performance.
* Easy to bond: suitable for epoxy, unsaturated polyester and other resin systems, high bonding strength.
* Processing convenience: It is easy to machine, and can bend into various curved surfaces under heating conditions, which improves the degree of freedom of design.
* Fatigue resistance: The unique molecular structure gives it good fatigue resistance, especially for composite sandwich
structures under dynamic loads.
* Aluminum Equivalent and Dielectric Transmittance: Aluminum Equivalent is low, suitable for medical equipment industry. It has low dielectric constant, low dielectric loss and good electrical insulation in a wide range of frequencies. It is suitable for radar equipment.
* High heat resistance: It has unique cross-linking structure, imide ring structure, high temperature stability and good pressure resistance. The hot deformation temperature is over 200 C. It is suitable for high temperature moulding or vacuum hot pressing tank co-curing process, shortening process time, improving production efficiency and improving structural performance.
* High closure rate: 95%-98% closure rate. Used in composite sandwich structure, it can avoid moisture absorption and degumming problems of honeycomb core material, improve safety performance and prolong service life. Because of its high porosity and water pressure resistance, it can be used as underwater buoyancy material.
* Barrier performance: Because of its high closed porosity and fine and uniform bubbles, the material has good sound insulation, heat insulation and moisture insulation performance.
* Easy to bond: suitable for epoxy, unsaturated polyester and other resin systems, high bonding strength.
* Processing convenience: It is easy to machine, and can bend into various curved surfaces under heating conditions, which improves the degree of freedom of design.
* Fatigue resistance: The unique molecular structure gives it good fatigue resistance, especially for composite sandwich
structures under dynamic loads.
* Aluminum Equivalent and Dielectric Transmittance: Aluminum Equivalent is low, suitable for medical equipment industry. It has low dielectric constant, low dielectric loss and good electrical insulation in a wide range of frequencies. It is suitable for radar equipment.
Hot Searches