3M 5925 tape's unique adhesion and stress dispersion characteristics, as well as its superior resistance to different environmental conditions and plasticizers, result in long-lasting practical results. It is mainly used for fixing and bonding of automobile external components and ornaments.
- Product Details
- {{item.text}}
Quick Details
-
Design Printing:
-
No printing
-
Material:
-
Acrylic foam
-
Feature:
-
Heat-Resistant
-
Use:
-
MASKING
-
Place of Origin:
-
Guangdong, China
-
Brand Name:
-
3M
-
Model Number:
-
5925
-
Product name:
-
3M 5925 Double Sided Adhesive Thickened Tape
Quick Details
-
Adhesive:
-
Acrylic
-
Adhesive Side:
-
Double Sided
-
Adhesive Type:
-
Pressure Sensitive, Water Activated
-
Design Printing:
-
No printing
-
Material:
-
Acrylic foam
-
Feature:
-
Heat-Resistant
-
Use:
-
MASKING
-
Place of Origin:
-
Guangdong, China
-
Brand Name:
-
3M
-
Model Number:
-
5925
-
Product name:
-
3M 5925 Double Sided Adhesive Thickened Tape
Products Description
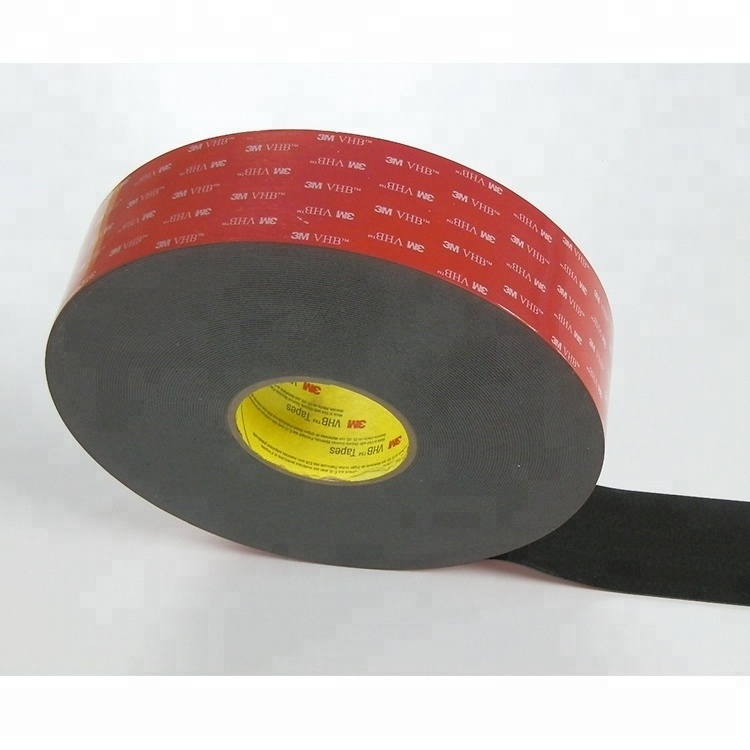
3M 5925 Double Sided Adhesive Thickened Tape
Product name
|
3M 5925 acrylic adhesive foam tape
|
Color
|
Black
|
Thickness
|
0.65mm
|
Jumbo roll size
|
600mm*33m (Custom size accepted)
|
Long term temperature resistance
|
90℃
|
Short term temperature resistance
|
120℃
|
Custom service
|
Slitting / Die cutting / Packaging
|
Free sample
|
A4 size
|
Advantage
|
1. Excellent stress dispersion and absorption capacity
2. High adhesion 3. Absorb plasticizers that will invalidate the adhesive 4. Excellent chemical resistance 5. Excellent weather resistance and durability |
Details Images
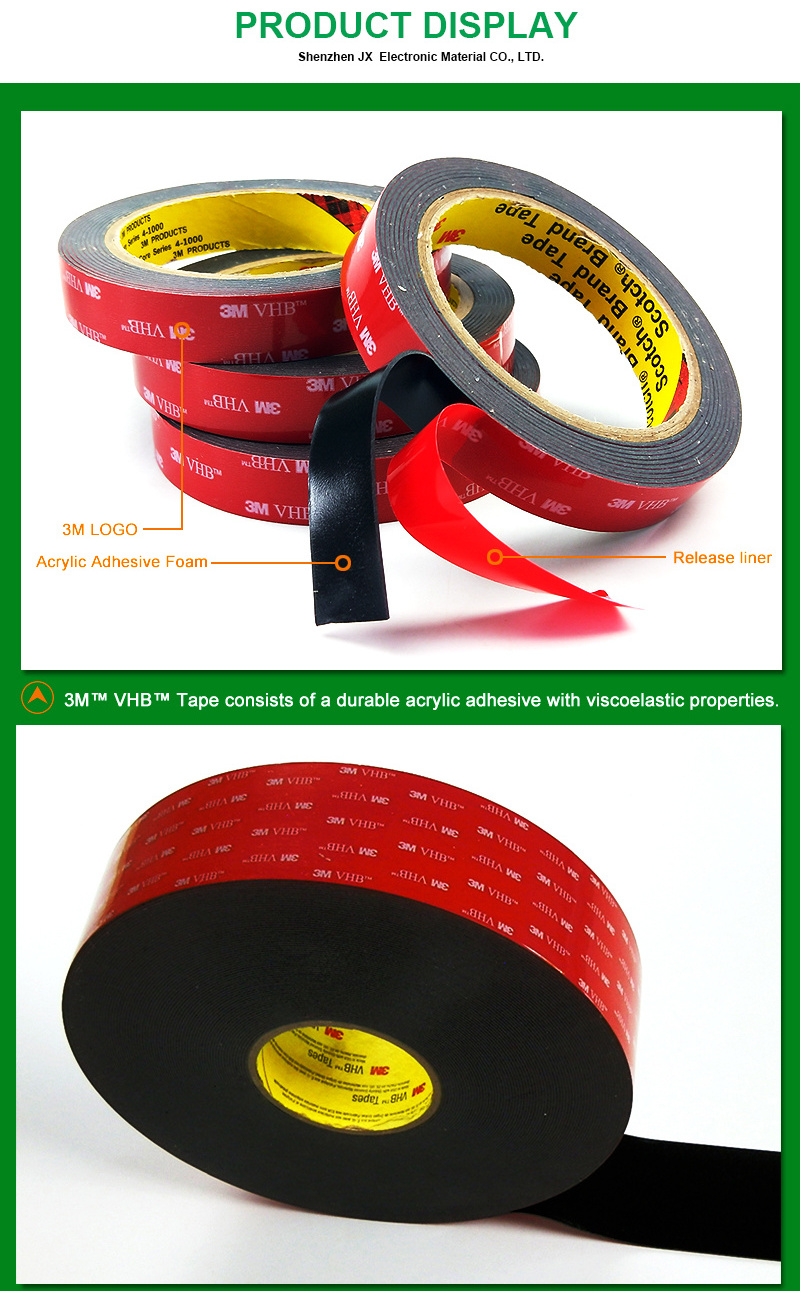
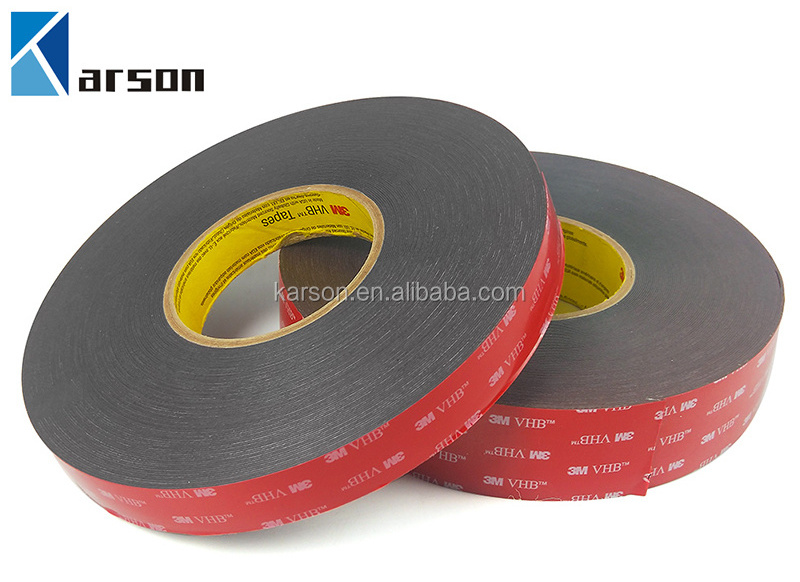
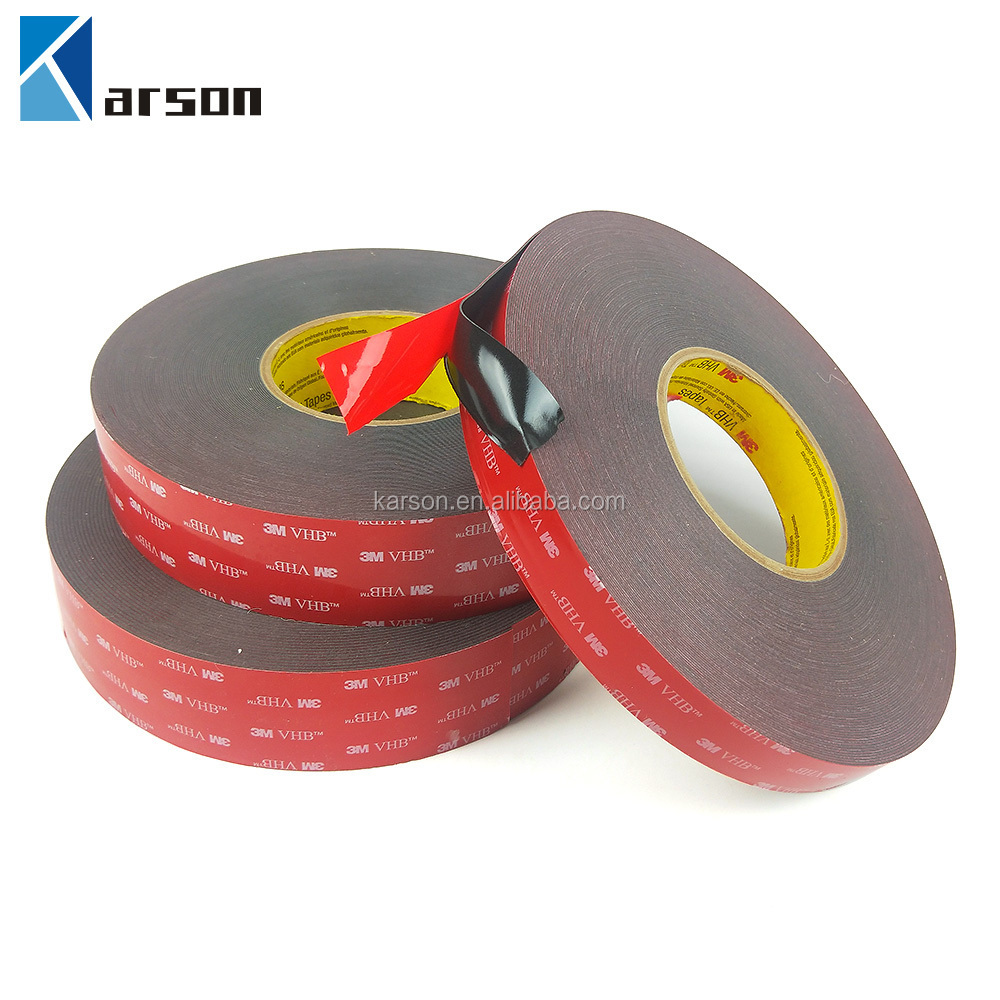
More products
Application
Manufacturing Technique
Packing&shipping
About Package:
Standard packing: Inner packaging poly bags, and then into cartons or as your requirement.
About the shipment:
1. All orders are dispatched within 1~2 weeks after confirmation of order.
2.Transportation modes EMS,TNT,DHL,UPS,FEDEX are available.
3.Tracking Number will be sent to you via e-mail after your order has been shipped.
Precision Tape Slitting
Die Cutting Services
Tape Lamination Services
Customized size and shape is available
About Samples:Normally, we offer A4 size for free, and the freight charges will be on your account.
Standard packing: Inner packaging poly bags, and then into cartons or as your requirement.
About the shipment:
1. All orders are dispatched within 1~2 weeks after confirmation of order.
2.Transportation modes EMS,TNT,DHL,UPS,FEDEX are available.
3.Tracking Number will be sent to you via e-mail after your order has been shipped.
Precision Tape Slitting
Die Cutting Services
Tape Lamination Services
Customized size and shape is available
About Samples:Normally, we offer A4 size for free, and the freight charges will be on your account.
FAQ
Q: What percent of the final bond strength can I expect immediately after application? After 24 hours? After 72 hours?
A: Immediately after an application is made, about 60% of the bond strength is achieved. As the adhesive continues to wet-out the surface, you can expect the bond to be at about 75% - 80% after 24 hours. After 72 hours, 95%+ of the bond strength is achieved. The bond will continue to build with time.
Q:The part is not adhering to the vehicle. What might be wrong?
A: Areas to investigate for poor adhesion or performance include: Check for surface contamination. The substrates must be clean and free of any contaminant. This is the most common cause of poor adhesion.
(1) Check for surface match. Are the two surfaces to be bonded a good match?
(2) Check for proper application pressure and wet-out.
(3) Check the back of the component for flatness.
(4).Check the installation process for proper procedures.
A: Immediately after an application is made, about 60% of the bond strength is achieved. As the adhesive continues to wet-out the surface, you can expect the bond to be at about 75% - 80% after 24 hours. After 72 hours, 95%+ of the bond strength is achieved. The bond will continue to build with time.
Q:The part is not adhering to the vehicle. What might be wrong?
A: Areas to investigate for poor adhesion or performance include: Check for surface contamination. The substrates must be clean and free of any contaminant. This is the most common cause of poor adhesion.
(1) Check for surface match. Are the two surfaces to be bonded a good match?
(2) Check for proper application pressure and wet-out.
(3) Check the back of the component for flatness.
(4).Check the installation process for proper procedures.
Hot Searches