- Product Details
- {{item.text}}
Quick Details
-
Warranty:
-
3
-
CB:
-
66.6mm
-
Wheel Sizes:
-
17X7.5J/18X8J/18x9J/19x8.5J/19X9.5J
-
Application:
-
Automotive Spare Parts
-
Item:
-
BCT33
-
Color:
-
Black,Pewter Grey
-
Manufacturing Craft:
-
Low Pressure Casting
-
Finish:
-
Casting
Quick Details
-
Finishing:
-
Bright
-
Width:
-
7.5J/8J//8.5/9.0J/9.5J
-
Place of Origin:
-
China
-
Warranty:
-
3
-
CB:
-
66.6mm
-
Wheel Sizes:
-
17X7.5J/18X8J/18x9J/19x8.5J/19X9.5J
-
Application:
-
Automotive Spare Parts
-
Item:
-
BCT33
-
Color:
-
Black,Pewter Grey
-
Manufacturing Craft:
-
Low Pressure Casting
-
Finish:
-
Casting
Details Images
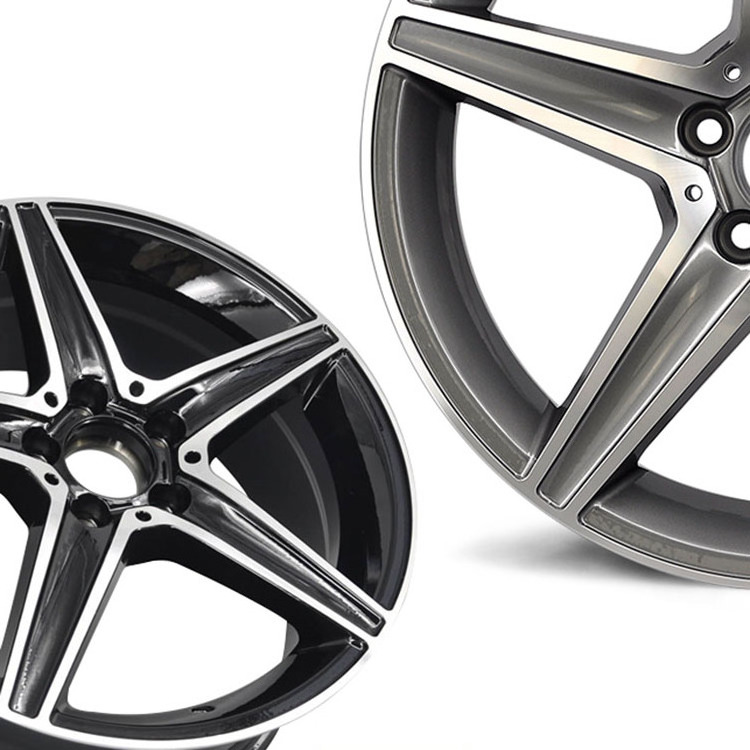
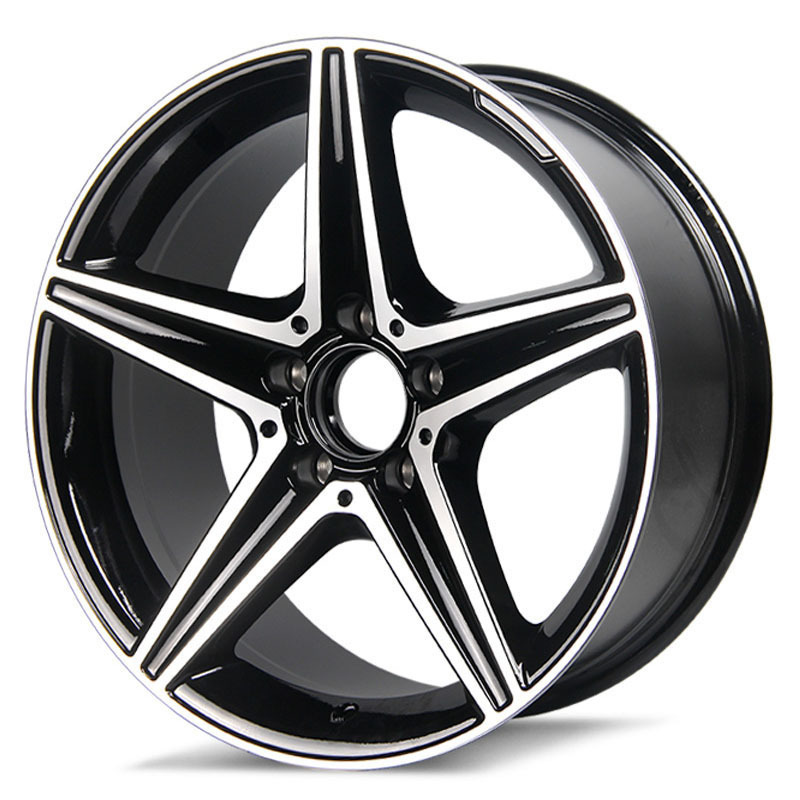
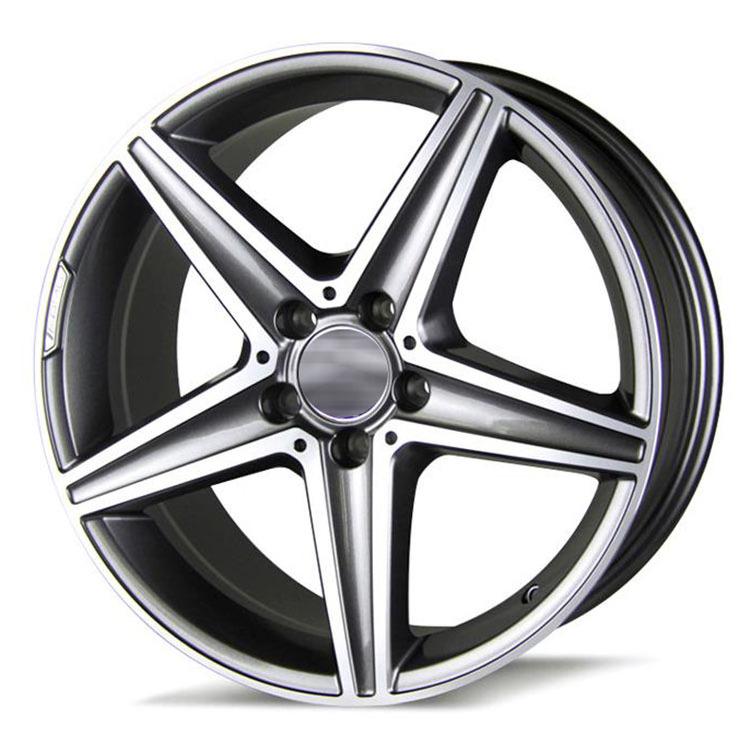
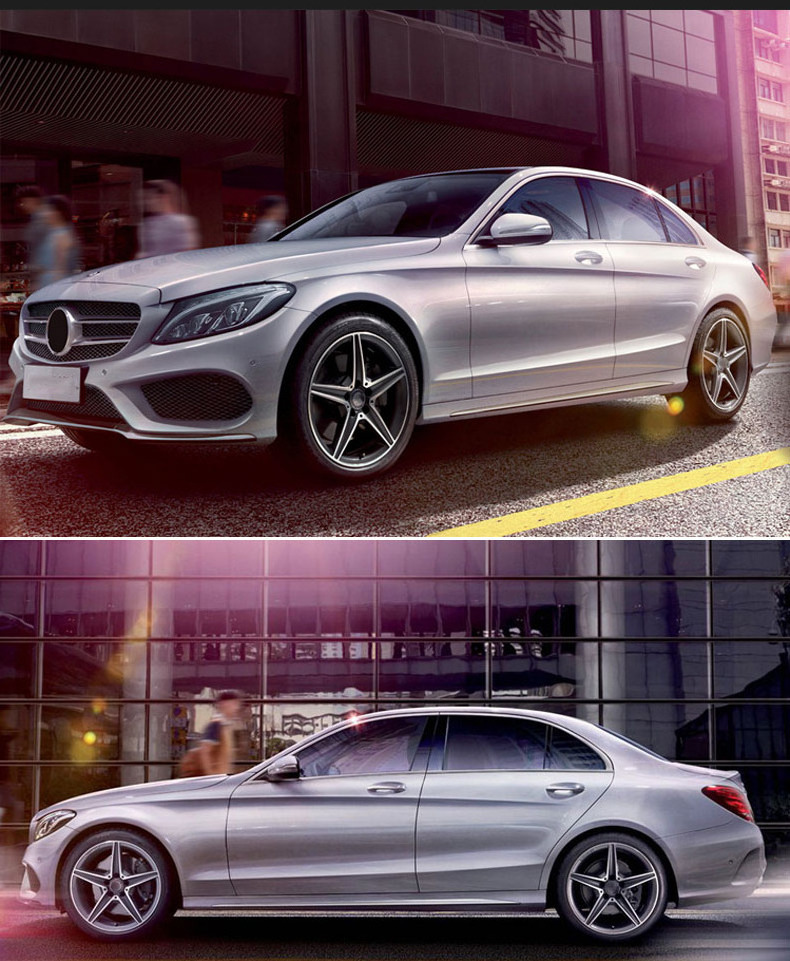
Products Description
Control checkpoints, real stuff
We will carry out strict screening of raw materials. Our wheels are made of high quality aviation aluminum, which has high strength, hardness and durability. Compared with casting aluminum, it is better in material, strength, ductility and durability.
Meticulous craftsmanship
The use of high precision automation process, every detail through strict detection and processing, all products after processing, the wheel ring surface to apply a certain amount of prestress to eliminate the stress concentration of the wheel ring, improve the anti-fatigue strength of the product.
Meticulous pursuit of products
We have carried out numerous tests on the durability and strength of the wheels to improve our design line to meet higher requirements. After strict inspection, we ensure that the wheels meet our standards.
1. Security
All products through the industry quality certification (VIA, TUV, OHSAS, ISO, etc.) worldwide marketing, at the same time for our products product liability insurance. Strict inspection and control of each ring casting.
2. Advanced technology
Cooperate with global advanced rim manufacturing suppliers, discuss and introduce production equipment and technology. There are casting, MAT spinning, forging, 3PCS and other diversified production processes.
3. Serialized services
Professional team from research and development, design, testing, production, sales, training, after-sales integration, covering high and low car matching, multiple style selection, personalized consumption. Light weight, low carbon, environmental protection concept!
Detailed explanation of hub structure
Offset value
ET is the distance from the hub center line to the installation plane. The larger the ET value is, the more the hub moves inward until it hits the fender.
Commonly used hub width matching tire comparison table
Wheel hub width
|
Adaptive tyre width(MM)
|
|
|
Wheel hub width
|
Adaptive tyre width(MM)
|
|
|
||||
5
|
155
|
165
|
175
|
8
|
225
|
235
|
245
|
||||
5.5
|
165
|
175
|
185
|
8.5
|
235
|
245
|
255
|
||||
6
|
185
|
195
|
205
|
9
|
245
|
255
|
265
|
||||
6.5
|
195
|
205
|
215
|
9.5
|
255
|
265
|
275
|
||||
7
|
205
|
215
|
225
|
10
|
265
|
275
|
285
|
||||
7.5
|
215
|
225
|
235
|
10.5
|
275
|
285
|
295
|
Manufacturing Technique
Top equipment, twice the result with half the effort
Advanced technology 10000T hot die forging press, continuous heat treatment furnace, automatic robot and control platform, automatic aluminum bar cutting line, Precision strong spinning machine, five-axis machining center and spectral detector, ultrasonic detection, fluorescence detection, radial fatigue performance testing machine, bending fatigue performance testing machine and impact testing machine and other kinds of testing equipment and a series of world advanced equipment, are only to achieve better and stronger hub products.
1. Raw material testing and cutting
Chemical analysis of raw materials, and then into the cutting workshop for ultrasonic inspection, to ensure that the raw materials have no defects, and finally cut into aluminum rods for the next processing
2. Preheat aluminum bars
Put the cut aluminum rod into the heating furnace for heating. After heating to the set temperature and making the material reach the equilibrium temperature, take it out for forging operation.
3. Forging and pressing into embryo
The preheated aluminum is forged into raw embryo by direct forging with a forging press of more than 10000 tons. After multiple stages of pressure forging, the material results in a more compact structure.
4. Spinning molding
The hair embryo is spun into shape by an upright spinning machine with 3 wheels up to 25 tons per wheel
5. Heat treatment
After spinning molding, aluminum wheel needs heat treatment to strengthen, and the process of heat treatment includes high temperature, solution treatment, quenching treatment, and low temperature aging treatment.
6. Lathe processing
The prototype of the wheel hub will be processed with a lathe, and its shape will be directly processed.
7. Inspection and flaw detection
After the completion of processing hub will be tested and audited, each product will be through the cleaning line coloring flaw detection inspection, to ensure that the product is perfect.
8. Painting marking
After polishing the hub, after multi-channel high-pressure cleaning, into the painting workshop, and then after the paint drying, one hub to complete the line.
9. Package and deliver
Before leaving the factory, the final quality inspection will be carried out. After checking the size and dynamic balance, the products will be packaged and shipped.
Hot Searches