- Product Details
- {{item.text}}
Quick Details
-
Model Number:
-
OEM/ODM
-
Name:
-
Roto molding mould fishing kayak with single seat aluminum boat mold
-
Mould material:
-
Aluminium
-
Plastic product material:
-
LLDPE, MDPE and HDPE
-
Cooler mould lead time:
-
15--60 days
-
Design software:
-
AutoCAD, UG, Solidworks, PROE
-
Mould life:
-
Ten thousand cycles
-
Surface treatment:
-
Mirror Polishing, Sand Blasting, Customized
-
Color and Size:
-
Customized
Quick Details
-
Shaping Mode:
-
Sand casting
-
Place of Origin:
-
Shanghai, China
-
Brand Name:
-
Customized
-
Model Number:
-
OEM/ODM
-
Name:
-
Roto molding mould fishing kayak with single seat aluminum boat mold
-
Mould material:
-
Aluminium
-
Plastic product material:
-
LLDPE, MDPE and HDPE
-
Cooler mould lead time:
-
15--60 days
-
Design software:
-
AutoCAD, UG, Solidworks, PROE
-
Mould life:
-
Ten thousand cycles
-
Surface treatment:
-
Mirror Polishing, Sand Blasting, Customized
-
Color and Size:
-
Customized
Name: Roto molding mould fishing kayak with single seat aluminum boat mold
|
|
|
|
|||
Material of mold
|
Aluminium
|
|
|
|||
Material of products
|
LLDPE, LDPE, MDPE, HDPE
|
|
|
|||
Shaping model
|
Rotomolding
|
|
|
|||
Production process
|
Rotomolded cooler products making process is: filling material→heating the mould→cooling the mould→demolding→inspecting→packing
|
|
|
|||
After treatment
|
Common polishing, or sand blasting, or mirror polishing, or finishing the mould surface according to your requirements.
|
|
|
|||
Workflow
|
Checking drawing → Mould 3D drawing designing →Patten processing →Aluminum casting →Aluminum CNC processing → Mould assembling →Aluminum mould surface finishing
→Sample testing...
|
|
|
|||
MOQ
|
Rotomolded Cooler Mould MOQ: 1set, Rotomolded Cooler Product MOQ: 20pcs.
|
|
|
|||
Payment terms
|
T/T, 50% deposit in advance, balance before shipping
|
|
|
Kayak Mould
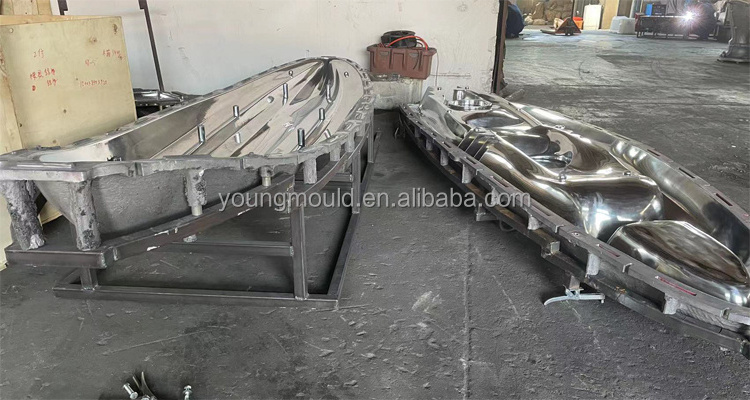
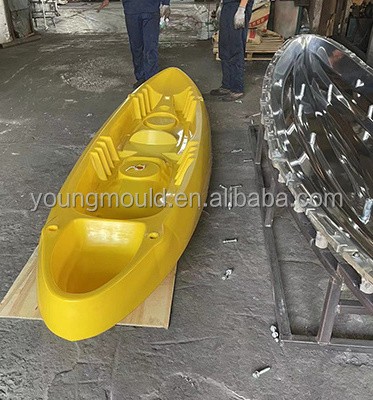
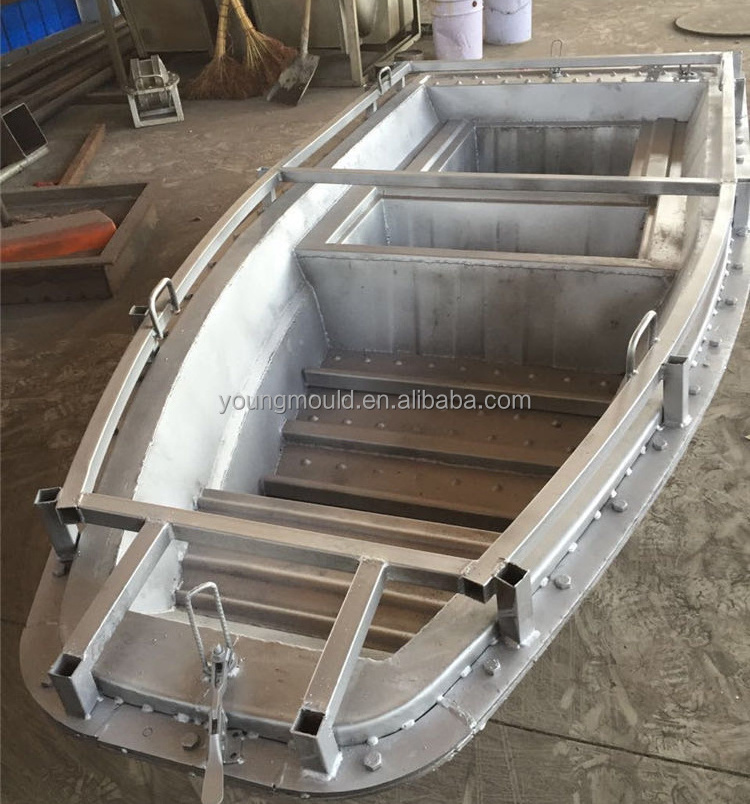
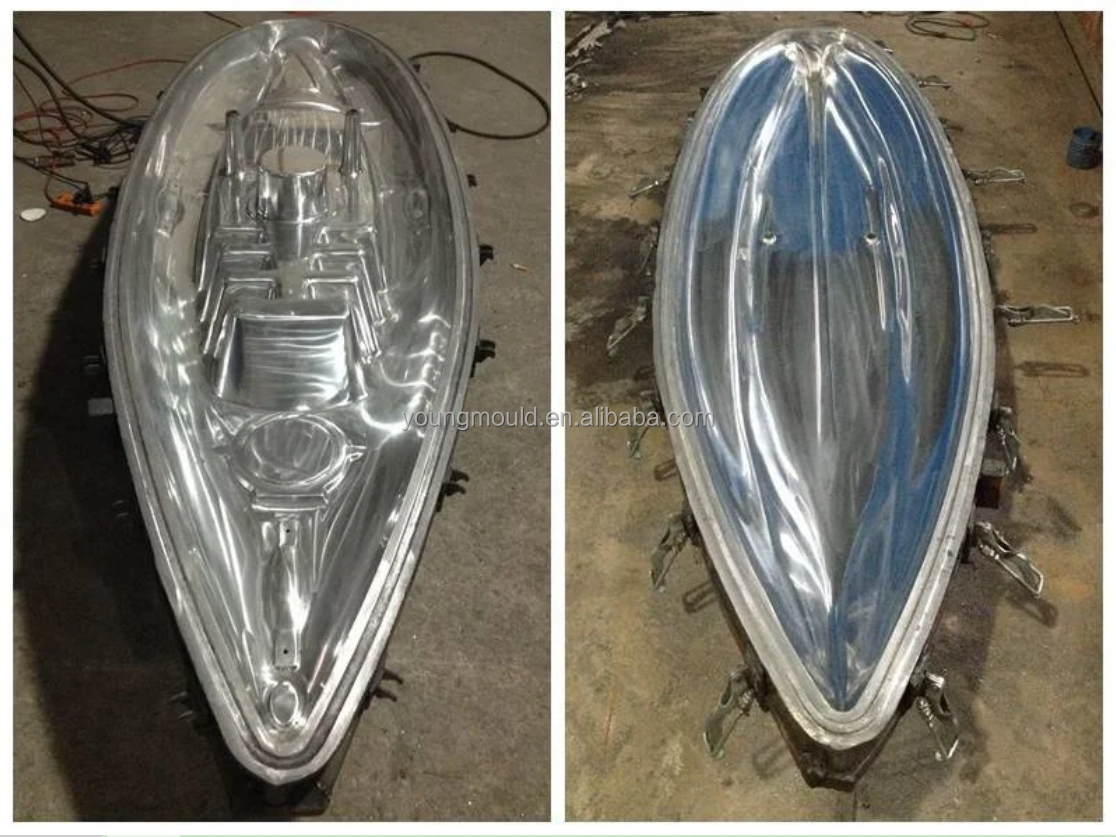
In very general terms, the rotational molding process looks like this:
|
|
|
|
|||
Step1
|
Plastic raw material (typically in powder form) is placed inside a mold (cast aluminum, CNC machined aluminum)
|
|
|
|||
Step2
|
The mold is attached to an arm of a rotational molding machine, and enters the oven where it rotates (rotational molding) on two axes.
|
|
|
|||
Step3
|
As the plastic material melts, it begins to adhere to the inside mold walls, building wall thickness and taking on the shape and texture of the interior mold surface.
|
|
|
|||
Step4
|
After rotating in the oven, the mold enters the cooling phase, where the molten material eventually solidifies into the finished, hollow plastic part.
|
|
|
|||
Step5
|
The part is then removed from the mold, where it undergoes a variety of secondary operations (trimming, foam-filling, assembly, etc.) prior to shipment.
|
|
|
Hot Searches