- Product Details
- {{item.text}}
Quick Details
-
Frequency:
-
27.12MHZ
-
Welding Area:
-
700*800mm
-
Dimensions:
-
1200*950*1950
-
Use:
-
pvc cleats, side wall
-
Weight (KG):
-
600 KG
-
Power (kW):
-
12
-
key word:
-
cleat, side wall welding machine
-
Power:
-
12KW
-
Weight:
-
570KG
-
After Warranty Service:
-
Online support
-
Showroom Location:
-
None
Quick Details
-
Place of Origin:
-
Shanghai, China
-
Brand Name:
-
Jiuluo
-
Voltage:
-
380V, 3AC, 50/60HZ
-
Frequency:
-
27.12MHZ
-
Welding Area:
-
700*800mm
-
Dimensions:
-
1200*950*1950
-
Use:
-
pvc cleats, side wall
-
Weight (KG):
-
600 KG
-
Power (kW):
-
12
-
key word:
-
cleat, side wall welding machine
-
Power:
-
12KW
-
Weight:
-
570KG
-
After Warranty Service:
-
Online support
-
Showroom Location:
-
None
JIULUO is professional high frequency welding machine manufacture with more than 15 years experiences, offering PVC/TPU cleats, profile, side wall, V guide welding machine.
Product Name
|
HF conveyor belt welding machine for PVC/PU cleat sidewall belts
|
Model
|
JL-12000T
|
Power output
|
12000W
|
Voltage
|
380V
|
Upper pressure plate size
|
400*650mm
|
Electrode stroke
|
460mm
|
Machine size
|
1200*850*1950mm
|
Net weight
|
570kg
|
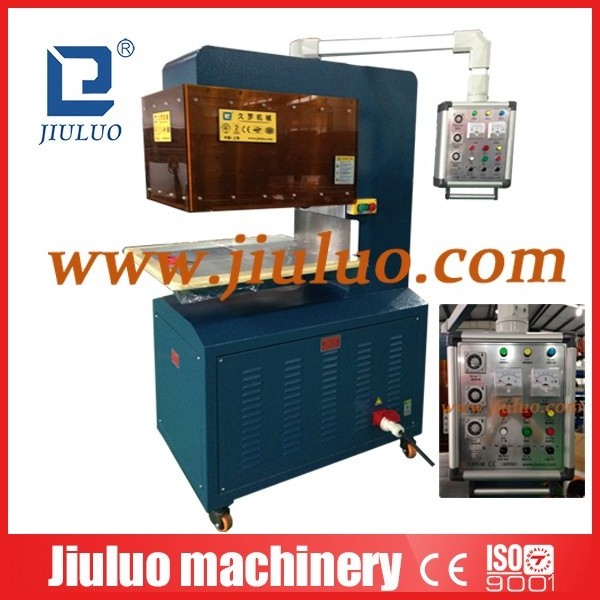
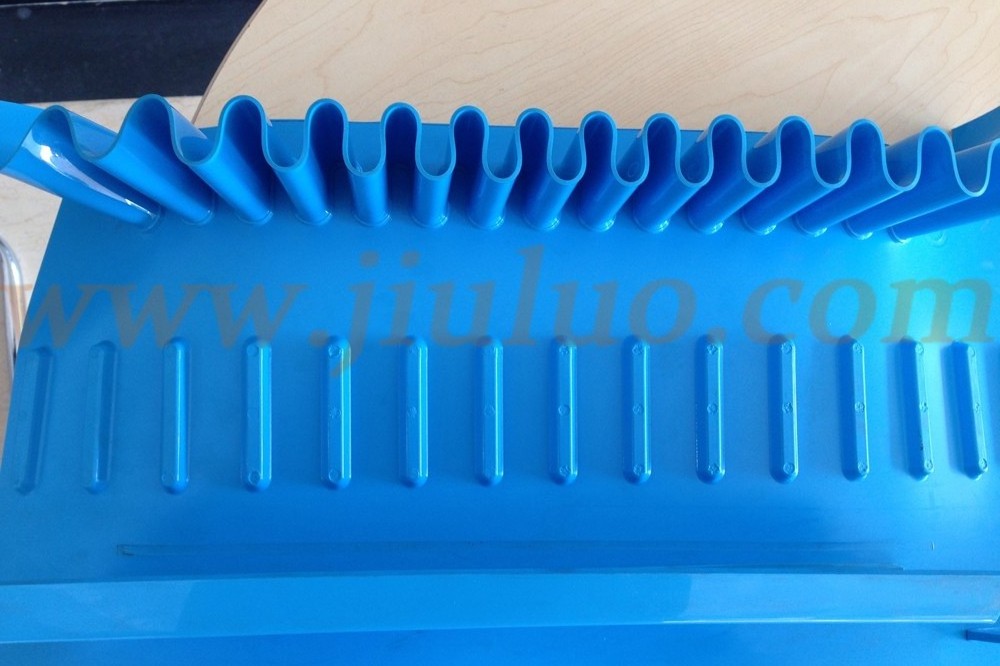
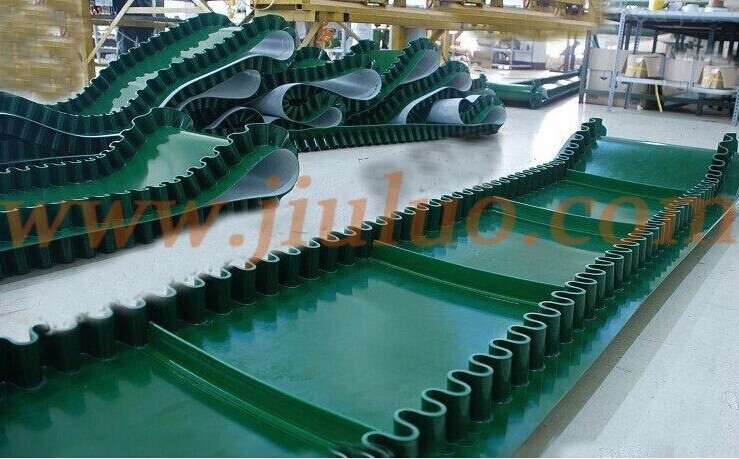
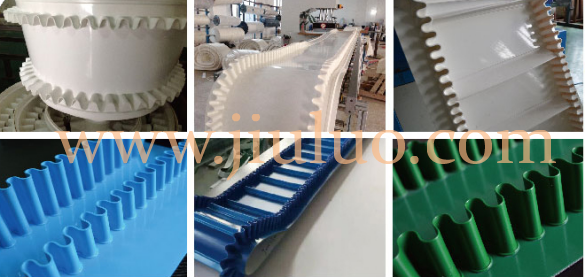
Pre-Sales Service
* Inquiry and consulting support.
* Sample testing support.
* View our Factory.
After-Sales Service
* Training how to install the machine, training how to use the machine.
* Engineers available to service machinery overseas.
Factory
Workshop
Our Workshop
Office
Our Office
Team
Our Team
What is HF welding?
High frequency (HF) welding is the joining of material by supplying HF energy in the form of an electromagnetic field (27.12 MHz) and pressure to the material surfaces to be joined. A generator produces the energy. The tool used to supply the energy is called an electrode. The electrical energy causes the molecules within the material to start moving, which generates heat that causes the material to soften and thereby fuse together. No outside heat is applied. It is instead generated within the material. After cooling the welded surface under maintained pressure, the material is fused and a weld has been created. The weld seam can be at least as strong as the surrounding material – or even stronger.
Four important factors that affect the final weld result are pressure, welding effect, welding time and cooling time. These parameters can be adjusted and combined in different ways to achieve the optimal welding result for a specific material.
The material most commonly used with HF welding is PVC (polyvinyl chloride), sometimes called vinyl and PU (Polyurethane). The material can be thick or thin, reinforced or coated. It can also be plain, coloured or patterned.
JIULUO customers manufacture a great variety of end products in these materials, such as truck and boat covers, tarps, tents, structures, pool liners, sunshades, billboards, inflatable products, liquid tanks, film screens, waterbeds, stretch ceilings, valve membranes and oil booms.
Why HF?
Below we have provided some comparisons between HF welding and a few alternative joining techniques.
Hot air/hot wedge
Two alternatives to HF welding are welding with hot air or hot wedge. These techniques involve heat being transferred to the material surfaces from the outside and are limited to thin sheets of material because the heat must be transported from the outer to the inner material surfaces in order to fuse them. If the material is too thick, it takes time and the outer material surfaces will be overheated before the inner ones have been heated sufficiently.
The HF technique overcomes this problem because the electrical field that generates the heat in an HF welding machine has the highest effect in the centre of the sheets being welded. This eliminates the risk of overheating and damage to surrounding material.
HF is also faster and produces a more durable and more uniform weld. HF welding does not discharge any gases and consumes less energy, which is better for the environment and of course saves money.
Gluing
Compared to gluing, HF welding saves a lot of time and produces a seam that is significantly stronger than a glued seam. Customers of ours in the advertising industry in the Middle East have switched to our machines for this very reason – burst seams caused glued billboards to fall down in strong winds, resulting in personal injury. HF welding also eliminates the use of adhesive, which contains solvents that could be harmful to production personnel and is not good for the environment.
Sewing
Materials joined with a sewing machine are of course held together, but are neither air-tight nor waterproof, which are often mandatory requirements for products like tents or products that are designed to be filled with air or water. When a sewn joint is stressed, the load is put on the thread holding the joined material together. However, when an HF-welded seam is stressed, the load is absorbed by the material surfaces, which of course means that the HF-welded seam is stronger. Furthermore, the seam created with HF can be welded in a manner that provides a uniform transition without splices between the joined materials. There is no space through which dirt, moisture or bacteria can penetrate and impair the product's strength and durability.