- Product Details
- {{item.text}}
Quick Details
-
Elongation (≥ %):
-
30
-
Place of Origin:
-
Hebei, China
-
Application:
-
Glass sealing alloy
-
Grade:
-
fe-ni-co
-
Ni (Min):
-
28.5
-
Model Number:
-
Kovar
-
Brand Name:
-
ChengYuan
-
Product name:
-
kovar tube
-
Curie point(Tc/ ℃):
-
430
-
Usage:
-
Electric vacuum devices
-
Density:
-
8.2g/cm3
-
Elastic Modulus(E/ Gpa):
-
138
-
Technique:
-
cold rolled
-
Feature:
-
Typical Fe-Ni-Co hard glass sealing alloys
-
Other name:
-
29HK,Kovar, Nilo K, KV-1, Dilver Po, Vacon 12
-
MOQ:
-
10kg
-
Keywords:
-
4j29 tube
Quick Details
-
Resistance (μΩ.m):
-
0.48
-
Powder Or Not:
-
Not Powder
-
Ultimate Strength (≥ MPa):
-
520
-
Elongation (≥ %):
-
30
-
Place of Origin:
-
Hebei, China
-
Application:
-
Glass sealing alloy
-
Grade:
-
fe-ni-co
-
Ni (Min):
-
28.5
-
Model Number:
-
Kovar
-
Brand Name:
-
ChengYuan
-
Product name:
-
kovar tube
-
Curie point(Tc/ ℃):
-
430
-
Usage:
-
Electric vacuum devices
-
Density:
-
8.2g/cm3
-
Elastic Modulus(E/ Gpa):
-
138
-
Technique:
-
cold rolled
-
Feature:
-
Typical Fe-Ni-Co hard glass sealing alloys
-
Other name:
-
29HK,Kovar, Nilo K, KV-1, Dilver Po, Vacon 12
-
MOQ:
-
10kg
-
Keywords:
-
4j29 tube
Product Paramenters
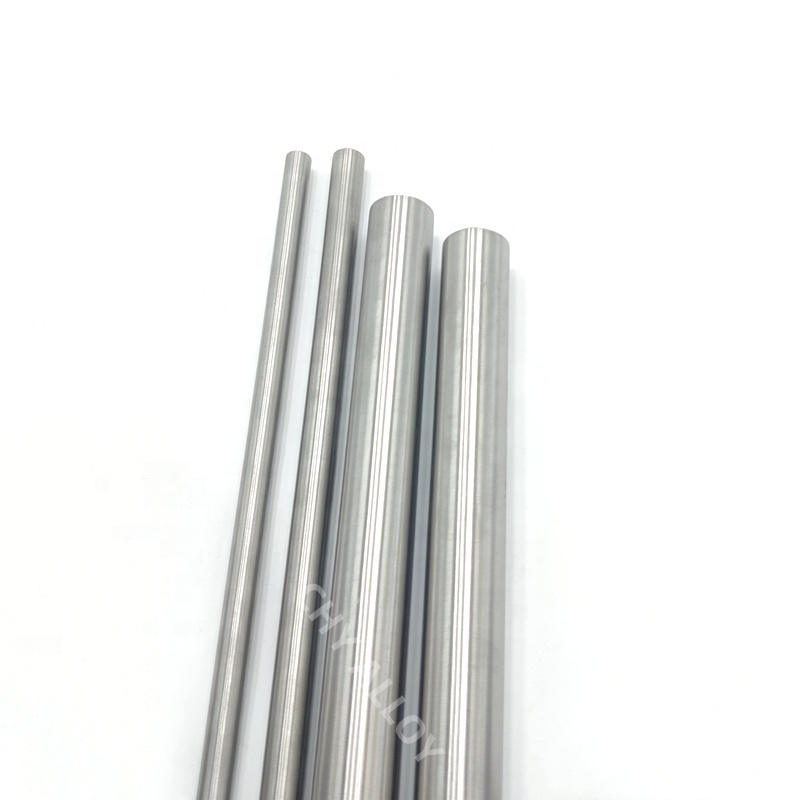
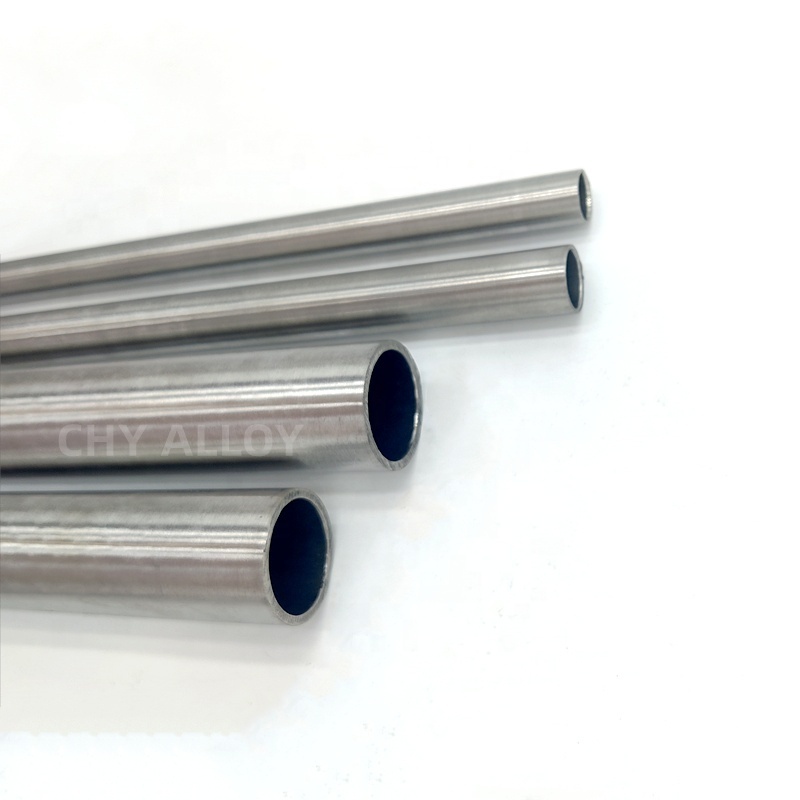
Spesification
Alloy Type
|
Trade Name
|
UNS No.
|
RUS Grade
|
FR Grade
|
Sdandard
|
Forms Of Supply
|
|
|
|
|||
|
|
|
|
|
|
Rod
|
Strip
|
Wire
|
Sheet
|
|||
Ni29Co17
|
Kovar
|
Kovar
|
29HK
|
Nilo K
|
ASTM F15
|
√
|
√
|
√
|
√
|
|||
FeNi36
|
Invar 36
|
Invar
|
36H
|
Invar standard
|
ASTM 1684
|
√
|
√
|
√
|
√
|
|||
FeNi42
|
Alloy 42
|
Glass sealing42
|
42H
|
N42
|
ASTM F30
|
√
|
√
|
√
|
√
|
|||
FeNi48
|
Alloy 48
|
K94800
|
47ND
|
—
|
ASTM F30
|
√
|
√
|
√
|
√
|
|||
Ni33Co17
|
—
|
—
|
—
|
—
|
—
|
√
|
√
|
√
|
√
|
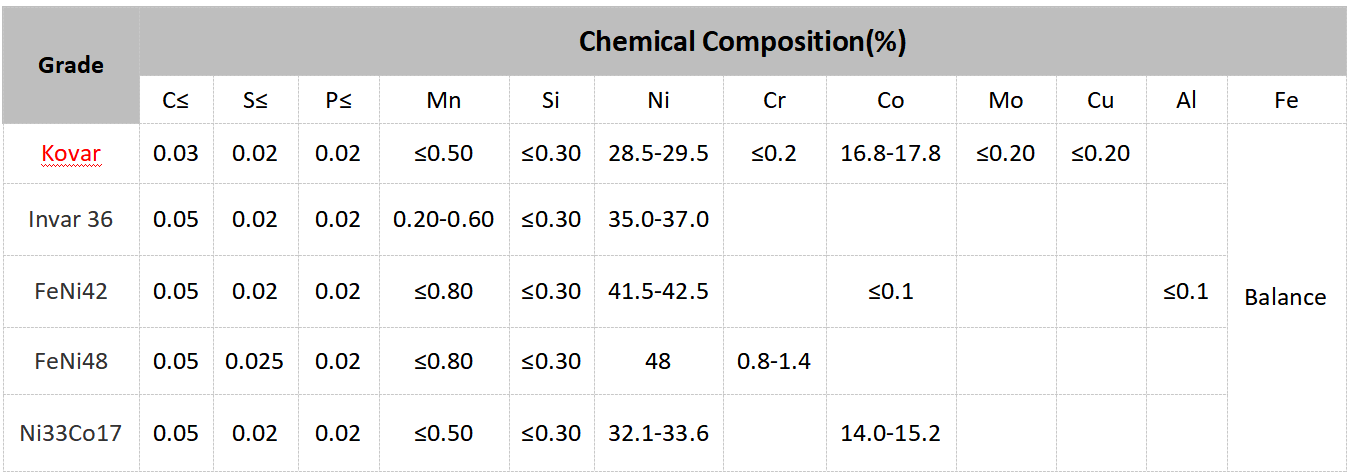
Kovar Physical properties
Density (g/cm3)
|
Resistivity at 20℃(Ωmm2/m)
|
Temperature Coefficient of Resistance
(20℃~100℃)X10
-5
/℃
|
Curie point
(Tc/ ℃)
|
Elastic Modulus
(E/ Gpa)
|
8.2
|
0.48
|
3.7~3.9
|
430
|
138
|
Kovar Tensile strength, MPa
Status number
|
State
|
Wire
|
Strip
|
R
|
Soft
|
≤585
|
≤570
|
1/4I
|
1/4 Hard
|
585~725
|
520~630
|
1/2I
|
1/2 Hard
|
655~795
|
590~700
|
3/4I
|
3/4 Hard
|
725~860
|
600~770
|
I
|
Hard
|
≥850
|
≥700
|
Kovar Coefficient of expansion
θ/℃
|
α1/10
-6
℃
-1
|
θ/℃
|
α1/10
-6
℃
-1
|
20~60
|
7.8
|
20~500
|
6.2
|
20~100
|
6.4
|
20~550
|
7.1
|
20~200
|
5.9
|
20~600
|
7.8
|
20~300
|
5.3
|
20~700
|
9.2
|
20~400
|
5.1
|
20~800
|
10.2
|
20~450
|
5.3
|
20~900
|
11.4
|
Kovar Thermal conductivity
θ/℃
|
100
|
200
|
300
|
400
|
500
|
λ/ W/(m*℃)
|
20.6
|
21.5
|
22.7
|
23.7
|
25.4
|
Supply category
Type
|
Size
|
|
|
Wire
|
D= 0.1~8mm
|
|
|
Strip
|
W= 5~250mm
|
T= 0.1mm~2.5mm
|
|
Foil
|
W= 10~100mm
|
T= 0.01~0.1mm
|
|
Bar
|
Dia= 8~100mm
|
L= 50~1000mm
|
Product Description
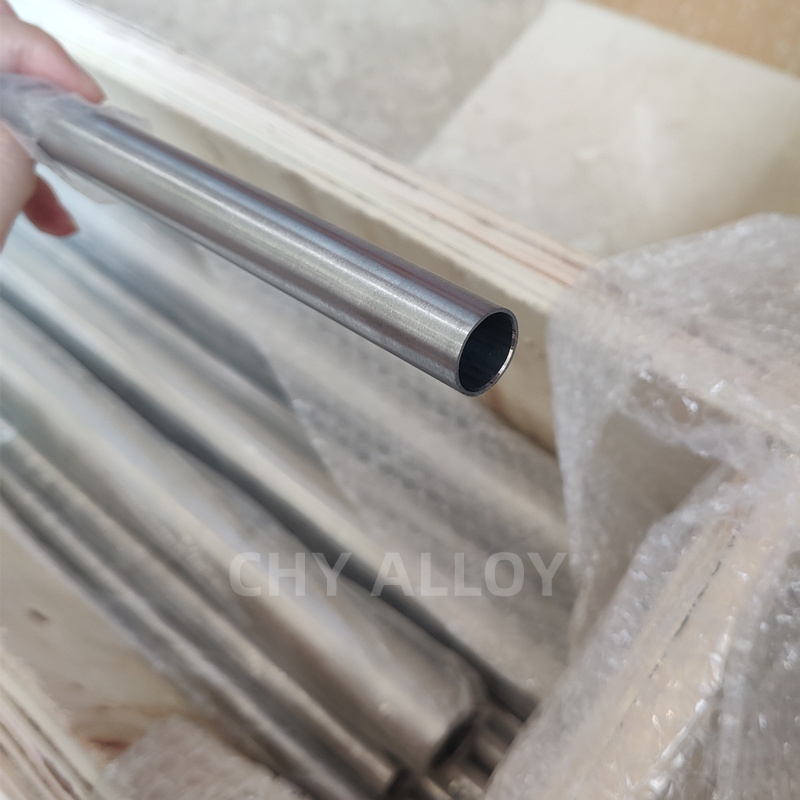
Kovar alloy; it has a linear expansion coefficient similar to that of silicon boron hard glass at 20 to 450°C, so it is often called a glass seal alloy in production and processing. This alloy is a typical Fe-Ni-Co hard glass sealing alloy used internationally, with a high Curie point and good low-temperature microstructure stability. The alloy's oxide film is dense, can be well infiltrated by glass, and does not interact with mercury. It is suitable for use in mercury-containing discharge meters. It is the main sealing structure material for electric vacuum devices. It is mainly used for electric vacuum components and emission tubes. Glass sealing of oscillating tube, ignition tube, magnetron, transistor, sealing plug, relay, integrated circuit lead wire, chassis, housing bracket, etc.
In the application, it should be ensured that the selected glass matches the expansion coefficient of the alloy, and its low-temperature structural stability can be strictly checked according to the temperature of use. Appropriate heat treatment should be carried out during processing to ensure that the material has good deep drawing elongation. The alloy is heated to 900°C±20°C in a hydrogen atmosphere for 1 hour, then heated to 1100°C±20°C, held for 15 minutes, and cooled to below 200°C at a rate of no more than 5°C/min.When forging materials are used, their air tightness should be strictly inspected.
Heat treatment process
Stress relief annealing
|
Heat to 470~540℃, keep for 1~2 h. Cool in the furnace
|
annealing
|
Heating to 750~900℃ in vacuum
|
Holding time
|
14 min~1h.
|
Cooling method
|
Cool down to 200 ℃ at a rate not exceeding 10 ℃/min
|
Hot Searches