- Product Details
- {{item.text}}
Quick Details
-
Place of Origin:
-
Uttar Pradesh, India
-
Brand Name:
-
HAQ Decor
-
Model Number:
-
WS14
-
Product Weight(kg):
-
0.5
-
Product Dimension:
-
customized
-
Packing Dimension:
-
customized
-
PCs/ Ctn:
-
1
-
Lamp Luminous Efficiency(lm/w):
-
720
-
Lamp Luminous Flux(lm):
-
7200
-
Product name:
-
Modern Wall Lamp Light Fixtures
-
Style:
-
Modern Decorative
-
Material:
-
Aluminum Body
-
Color:
-
Grey
-
Type:
-
Modern Wall Mounted Light
-
Size:
-
Customizd
-
Power:
-
20W
-
MOQ:
-
10 Pcs
-
Shape:
-
Square Shape
-
Bulb:
-
E26/E27 1*Max.60W(not Included)
Quick Details
-
Application:
-
Outdoor
-
Design Style:
-
Modern
-
Lamp Body Material:
-
Aluminum
-
Place of Origin:
-
Uttar Pradesh, India
-
Brand Name:
-
HAQ Decor
-
Model Number:
-
WS14
-
Product Weight(kg):
-
0.5
-
Product Dimension:
-
customized
-
Packing Dimension:
-
customized
-
PCs/ Ctn:
-
1
-
Lamp Luminous Efficiency(lm/w):
-
720
-
Lamp Luminous Flux(lm):
-
7200
-
Product name:
-
Modern Wall Lamp Light Fixtures
-
Style:
-
Modern Decorative
-
Material:
-
Aluminum Body
-
Color:
-
Grey
-
Type:
-
Modern Wall Mounted Light
-
Size:
-
Customizd
-
Power:
-
20W
-
MOQ:
-
10 Pcs
-
Shape:
-
Square Shape
-
Bulb:
-
E26/E27 1*Max.60W(not Included)
Products Description
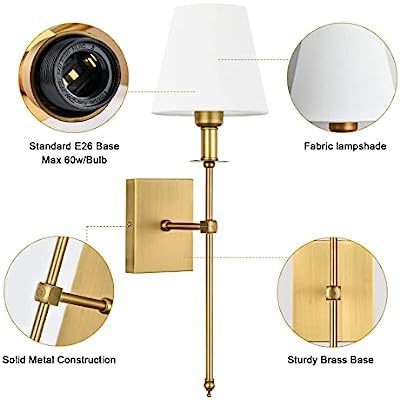
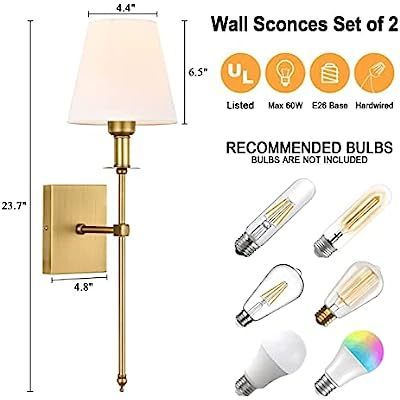
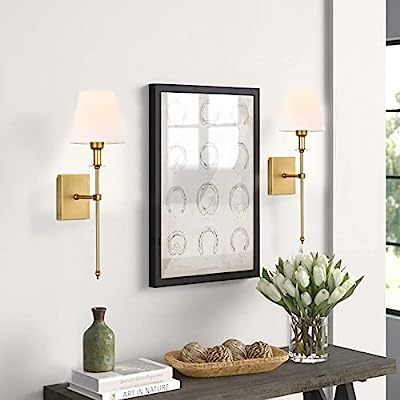
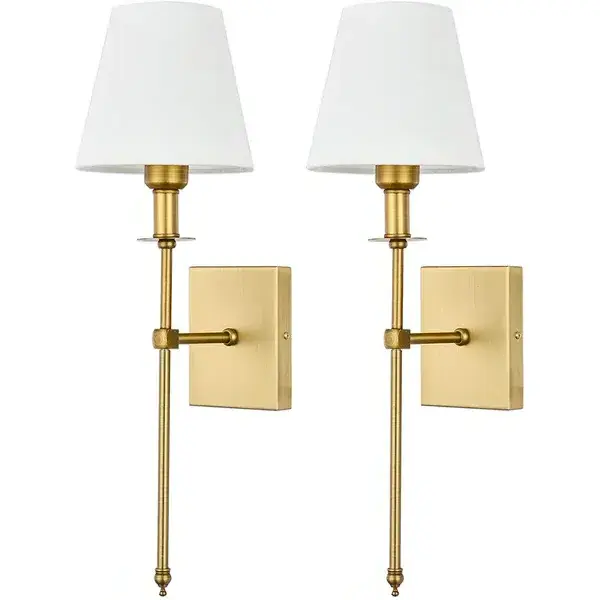
Product Name
|
Wall Scone
|
Usage
------->
|
Home Hotel Lightning
|
Material
Customized Metal White Fabric
|
Materail
|
Material Type
|
Aluminium
|
Brass
|
Copper
|
Size (cms)
|
L
|
W
|
H
|
LXBXH= Volume
|
|
16.5
|
13
|
61
|
12278
|
Moq
|
50
|
100
|
500
|
1000
|
Manufacturing Technique
Powder Coating
Powder coating
is a type of coating that is applied as a free-flowing, dry powder. Unlike conventional liquid paint which is delivered via an evaporating solvent, powder coating is typically applied electrostatically and then cured under heat or with ultraviolet light. The powder may be a thermoplastic or a thermoset polymer. It is usually used to create a hard finish that is tougher than conventional paint.
Powder coating is mainly used for coating of metals, such as household appliances, aluminium extrusions, drum hardware, Automobiles, and bicycle frames.
Advancements in powder coating technology like UV curable powder
coatings allow for other materials such as plastics, composites, carbon fiber, and MDF (medium-density fibreboard) to be powder coated due to the minimum heat and oven dwell time required to process these components
coatings allow for other materials such as plastics, composites, carbon fiber, and MDF (medium-density fibreboard) to be powder coated due to the minimum heat and oven dwell time required to process these components
Electro Plating
Electroless deposition (ED)
or electroless plating is defined as the autocatalytic process through which metals and metal alloys are deposited onto conductive and nonconductive surfaces.
These nonconductive surfaces include plastics, ceramics, and glass etc.
which can then become decorative, anti-corrosive, and conductive depending on their final functions.
Electroplating unlike
electroless deposition only deposits on other conductive or semi-conductive when a external current is applied. Electroless deposition deposits metals onto 2D and 3D structures such as screws, nanofibers, and carbon nanotubes unlike other plating methods such as Physical Vapor Deposition ( PVD), Chemical Vapor Deposition (CVD), and electroplating which are limited to 2D surfaces. Commonly the surface of the substrate is Characterized via pXRD, SEM-EDS, and XPS which relay set parameters based their final Funtionality.These parameters are referred to a Key Performaance Indicators crucial for a researcher’ or company's purpose.Electroless deposition continues to rise in importance within the microelectronic industry, oil and gas, and aerospace industry
electroless deposition only deposits on other conductive or semi-conductive when a external current is applied. Electroless deposition deposits metals onto 2D and 3D structures such as screws, nanofibers, and carbon nanotubes unlike other plating methods such as Physical Vapor Deposition ( PVD), Chemical Vapor Deposition (CVD), and electroplating which are limited to 2D surfaces. Commonly the surface of the substrate is Characterized via pXRD, SEM-EDS, and XPS which relay set parameters based their final Funtionality.These parameters are referred to a Key Performaance Indicators crucial for a researcher’ or company's purpose.Electroless deposition continues to rise in importance within the microelectronic industry, oil and gas, and aerospace industry
Brass Sand Casting
The task of making a brassware comprise of many stages like pattern making (making of master piece) the pattern is exact replica of the object to be cast. The pattern is used to create the mould in which the molten metal is poured. Then, sand which is also
called as masala or balu is used for moulding. Sand casting is the traditional process in which sand is used to make the mould in which metal is cast and from this traditional process brass wares are made. The mould is made using moulding boxes, the moulding boxes are generally divided into two segments which supports the mould when the molten metal is poured in it. The mould is made by packing the sand around a pattern and the sand contains chemical binder (molasses) which aids in holding the shape of the
pattern.After the mould is made the pattern is removed. Simultaneously melting is the process in which the metal (brass) scrap is meltedto very high temperature using furnace. The furnace is a device used to heat the metal which is generally fired using fuels. Inbrass sand casting coal is used to fire the furnace and then casting (dhalai) of the molten metal is poured into the cavity. Themolten metal poured into the mould fills the cavity in the mould and it is allowed to cool for few minutes. After cooling, the cast metal is been removed from the dried mould and the sand is broken form the cast metal. The gating (path way made in the mould\ for directing the flow of molten metal into the cavity) is removed form the cast metal using hammer.
called as masala or balu is used for moulding. Sand casting is the traditional process in which sand is used to make the mould in which metal is cast and from this traditional process brass wares are made. The mould is made using moulding boxes, the moulding boxes are generally divided into two segments which supports the mould when the molten metal is poured in it. The mould is made by packing the sand around a pattern and the sand contains chemical binder (molasses) which aids in holding the shape of the
pattern.After the mould is made the pattern is removed. Simultaneously melting is the process in which the metal (brass) scrap is meltedto very high temperature using furnace. The furnace is a device used to heat the metal which is generally fired using fuels. Inbrass sand casting coal is used to fire the furnace and then casting (dhalai) of the molten metal is poured into the cavity. Themolten metal poured into the mould fills the cavity in the mould and it is allowed to cool for few minutes. After cooling, the cast metal is been removed from the dried mould and the sand is broken form the cast metal. The gating (path way made in the mould\ for directing the flow of molten metal into the cavity) is removed form the cast metal using hammer.
Product packaging
Hot Searches