2. Lightly remove chips and particles from the inside and outside cut edges of tube. Bevel up to 0.2mm × 45 is permissible.
3. For tube bend, the minimum height from the straight pipe end to the bending radius must be at least twice the
height of the nut.
4. Lubricate thread and cone of the fitting body, ring and thread of nut.
- Product Details
- {{item.text}}
Quick Details
-
Weight:
-
10
-
Bore diameter:
-
60-100
-
Rod diameter:
-
25-45
-
Stroke:
-
32-1500
-
Installation distance:
-
109-1808
-
working pressure:
-
18Mpa
-
Interface dimensions:
-
2-M14*1.5
-
weight:
-
3.4kg-46kg
Quick Details
-
Warranty:
-
1 Year
-
Brand Name:
-
ever-power
-
Place of Origin:
-
Zhejiang, China
-
Weight:
-
10
-
Bore diameter:
-
60-100
-
Rod diameter:
-
25-45
-
Stroke:
-
32-1500
-
Installation distance:
-
109-1808
-
working pressure:
-
18Mpa
-
Interface dimensions:
-
2-M14*1.5
-
weight:
-
3.4kg-46kg
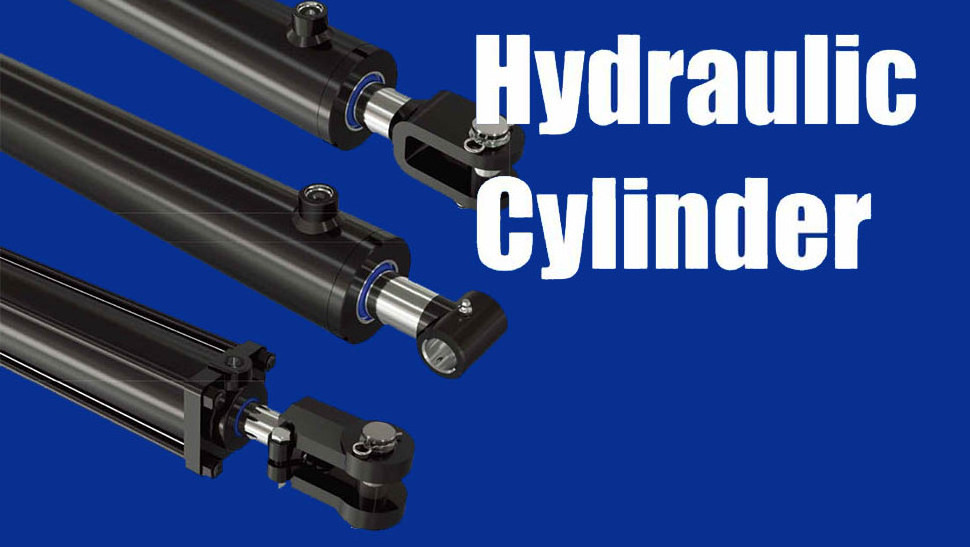
Product Description
The term "High Pressure Banjo Elbow - WH-M" does not correspond to a widely recognized or standard hydraulic fitting designation.
It is possible that it refers to a specific type or design of hydraulic banjo elbow fitting, but without further information or
context, it is difficult to provide specific details about its application.
However, in general, banjo fittings are commonly used in hydraulic systems to provide a secure and leak-free connection between a hydraulic hose or pipe and a component, such as a cylinder, valve, or pump. Banjo fittings typically have a hollow bolt or tube with a hole through the side, allowing fluid to flow through the fitting.
It is possible that it refers to a specific type or design of hydraulic banjo elbow fitting, but without further information or
context, it is difficult to provide specific details about its application.
However, in general, banjo fittings are commonly used in hydraulic systems to provide a secure and leak-free connection between a hydraulic hose or pipe and a component, such as a cylinder, valve, or pump. Banjo fittings typically have a hollow bolt or tube with a hole through the side, allowing fluid to flow through the fitting.
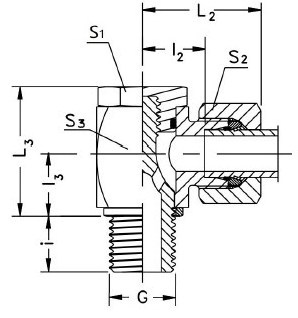
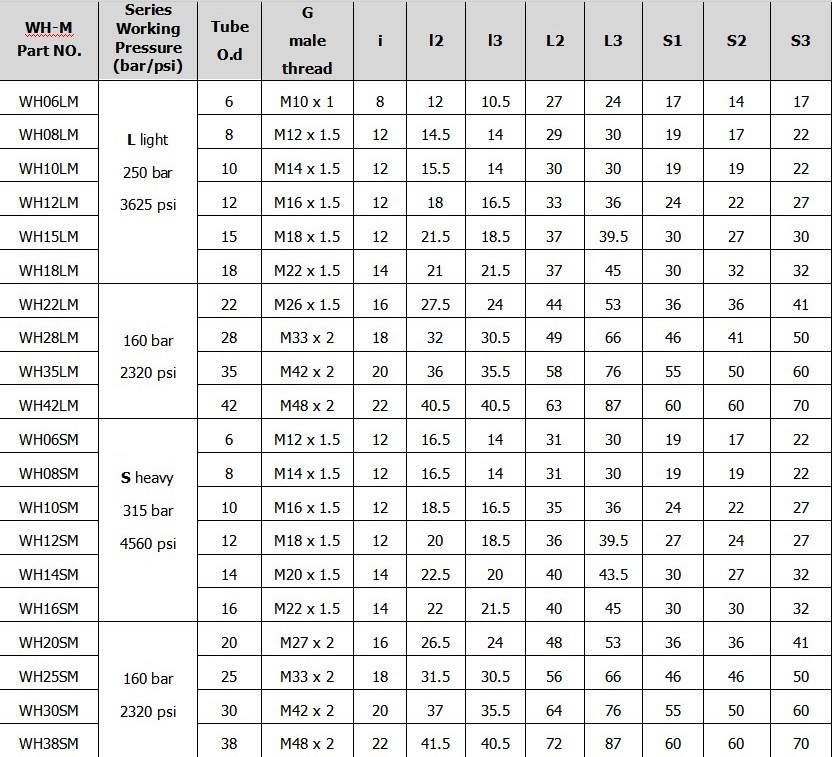
Here are some general applications where banjo fittings, including banjo elbow fittings, may be used:
1.Hydraulic Brake Systems: Banjo fittings are commonly used in hydraulic brake systems in automotive vehicles, motorcycles, and other applications. They provide a connection between the brake lines and the brake calipers or wheel cylinders.
2.Fuel Injection Systems: Banjo fittings can be found in high-pressure fuel injection systems in automotive engines. They help connect the fuel lines to the fuel injectors, ensuring proper fuel delivery and pressure.
3.Hydraulic Power Steering Systems: Banjo fittings may be used in hydraulic power steering systems to connect the power steering hoses to the steering gear or steering rack, allowing for smooth and precise steering operation.
4.Hydraulic Clutch Systems: Banjo fittings can be employed in hydraulic clutch systems, connecting the hydraulic lines to the clutch slave cylinder or master cylinder.
5.Industrial Machinery: Banjo fittings may be used in various industrial machinery and equipment that utilize hydraulic systems, such as hydraulic presses, machine tools, and hydraulic power units.
It's important to note that the specific application and compatibility of hydraulic fittings, including banjo fittings, can vary depending on factors such as system requirements, operating conditions, and hydraulic system specifications. It is always recommended to consult the manufacturer's guidelines or seek assistance from a hydraulic expert to ensure the proper selection and application of hydraulic fittings for a specific system.
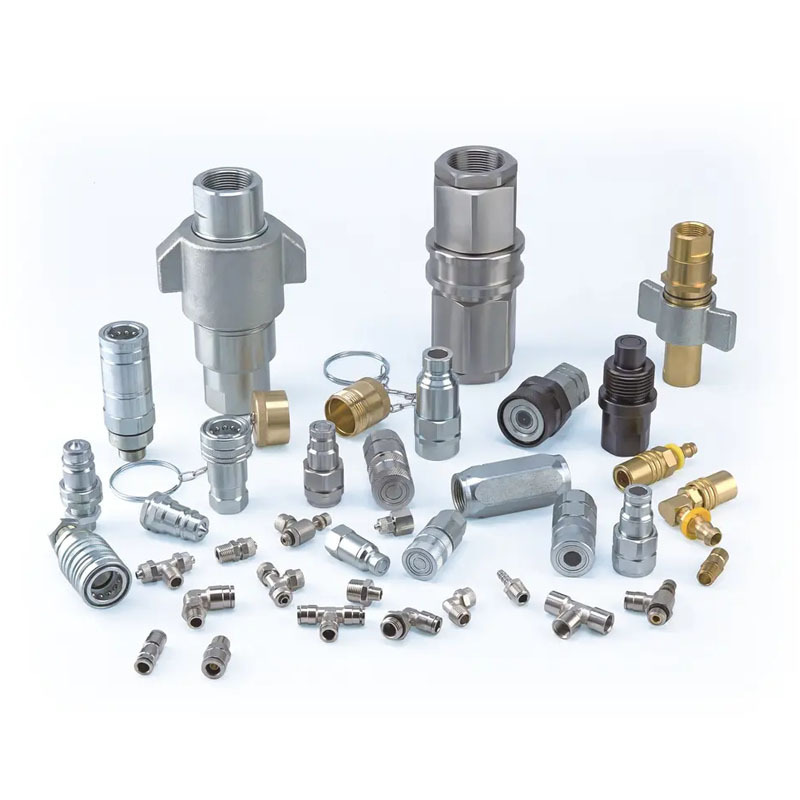
Installation instructions
The nuts of ROKE hydraulic connectors are all silver plated and coated with our patented nano lubricating layer. Through this method, the installation torque can be controlled within a reasonable range.
Especially in narrow spaces or suspended operations, installation is very easy.
In order to assemble correctly, the assembly instructions should be followed. Improper assembly may cause malfunctions or damage safety.
1. Cut the tube: 1/2 angle tolerance to the tube axis is permissible. Tube cutter is not recommendable.
Assembly
5. Slip nut and then ring onto the tube end. Ensure that the ring is placed correctly.
6. Screw nut manually onto fitting body until finger tight. Hold the tube against the shoulder in the cone of the fitting body.
7. Mark nut and tube for measuring the prescribed turns of the nut.
8. Tighten the nut 1 1/4 turns. Tube must not turn with tube. Stop edge of the ring limits over-tightening by increasing tightening torque.
5. Slip nut and then ring onto the tube end. Ensure that the ring is placed correctly.
6. Screw nut manually onto fitting body until finger tight. Hold the tube against the shoulder in the cone of the fitting body.
7. Mark nut and tube for measuring the prescribed turns of the nut.
8. Tighten the nut 1 1/4 turns. Tube must not turn with tube. Stop edge of the ring limits over-tightening by increasing tightening torque.
Check & Final Assembly
9. Loosen nut and remove ring-mounted tube from fitting. And check if a visivle collar has formed on the pipe in
front of the first cutting edge. If not, tighten slightly more.
10. Insert the pre-assembled tube into the fitting.
While holding fitting body with a wrench, tighten nut approx. 1/4 revolution beyond the point of a clearly perceptible resistance.
9. Loosen nut and remove ring-mounted tube from fitting. And check if a visivle collar has formed on the pipe in
front of the first cutting edge. If not, tighten slightly more.
10. Insert the pre-assembled tube into the fitting.
While holding fitting body with a wrench, tighten nut approx. 1/4 revolution beyond the point of a clearly perceptible resistance.
Hot Searches