- Product Details
- {{item.text}}
Quick Details
-
Brand Name:
-
MINX
-
Model Number:
-
MINX002
-
Surface Treatment:
-
Concave,gritted,smooth
-
Product name:
-
Fiber Glass Grating, Plastic Floor Grid, Fiberglass Mini Mesh Grating
-
Color:
-
Customized Colors
-
Material:
-
Ortho,ISO,V/E or Phenolic resin
-
Length:
-
Less 12m
-
Thickness:
-
Customized Thickness
-
Usage:
-
Building/construction/gutter cover plate, car wash,etc
-
MOQ:
-
100 Meters
-
Packing:
-
Customized Packings
-
Feature:
-
Fire Retardant
-
Sample:
-
Sample Avaliable
Quick Details
-
Application:
-
Flooring walkway/drainage/chemcial plant/driveway
-
Technique:
-
Pultrusion Process
-
Place of Origin:
-
Hebei, China
-
Brand Name:
-
MINX
-
Model Number:
-
MINX002
-
Surface Treatment:
-
Concave,gritted,smooth
-
Product name:
-
Fiber Glass Grating, Plastic Floor Grid, Fiberglass Mini Mesh Grating
-
Color:
-
Customized Colors
-
Material:
-
Ortho,ISO,V/E or Phenolic resin
-
Length:
-
Less 12m
-
Thickness:
-
Customized Thickness
-
Usage:
-
Building/construction/gutter cover plate, car wash,etc
-
MOQ:
-
100 Meters
-
Packing:
-
Customized Packings
-
Feature:
-
Fire Retardant
-
Sample:
-
Sample Avaliable
Products Description
Product descriptions from the supplier
Fiber Glass Reinforced Plastic Grating, Plastic Floor Grid, Fiberglass Mini Mesh Grating
Fiberglass Gratings
Molded fiberglass grating and pultruded fiberglass grating from WellGRID provides unmatched corrosion resistance properties, especially when compared to steel flooring products.
FRP gratings, also known as glass steel gratings, is a kind of glass fiber reinforced material, unsaturated polyester resin
matrix, after special processing composite into a kind of plate material with many Spaces, glass steel gratings can be used as structural materials, corrosion environment floor, trench cover plate, platform, ship deck, stairs, plank road, etc. It has the characteristics of corrosion resistance, flame retardant, no magnetic insulation, bright color, a variety of styles and forms. FRP grating is extremely durable, non-corrosive and doesn't conduct electricity, which often makes it a safer alternative to other flooring materials traditionally used in harsh and high-risk environments.
matrix, after special processing composite into a kind of plate material with many Spaces, glass steel gratings can be used as structural materials, corrosion environment floor, trench cover plate, platform, ship deck, stairs, plank road, etc. It has the characteristics of corrosion resistance, flame retardant, no magnetic insulation, bright color, a variety of styles and forms. FRP grating is extremely durable, non-corrosive and doesn't conduct electricity, which often makes it a safer alternative to other flooring materials traditionally used in harsh and high-risk environments.
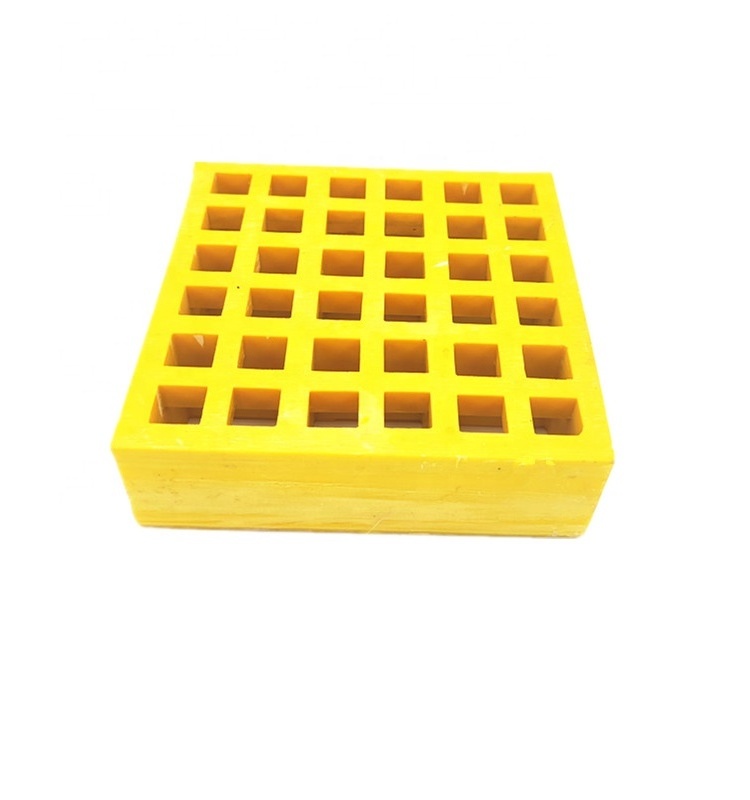
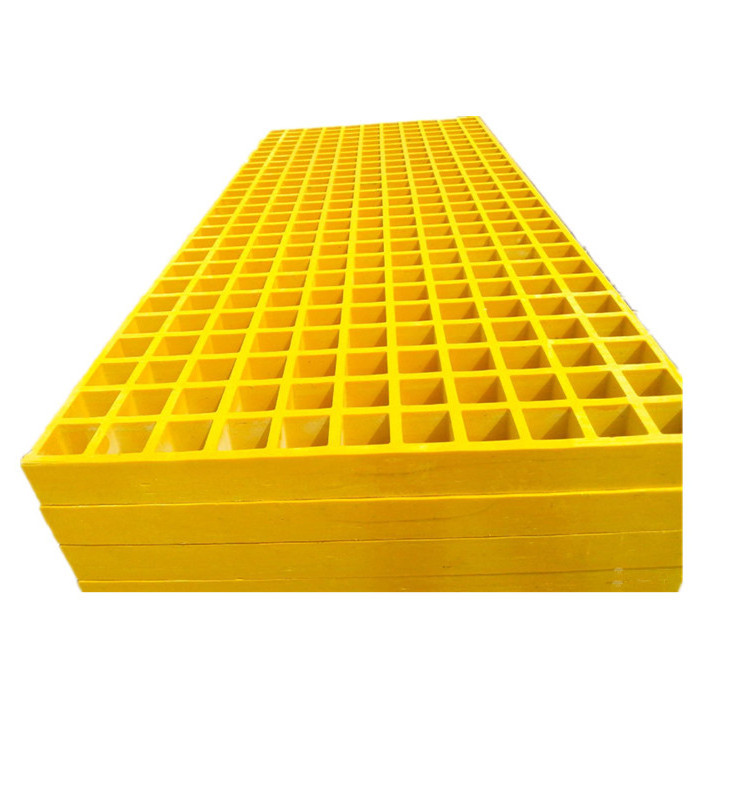
Specification
Mesh size
|
Height
|
Bar thickness
Top/Bottom
|
Panel size
|
Open area
|
Weight(kg/m2)
|
38*38
|
25/38/50
|
6.4/5.0
7.0/5.0
11.0/9.0
|
1220*4000/1220*3660/1220*2440
|
68/68/56
|
12.3/19.5/42
|
40*40
|
25
|
7.0/5.0
|
1247*1247/1007*4047
|
67
|
14.6
|
50*50
|
25/50
|
7.5/6.0
7.0/5.0
|
1220*3660 or customization
|
78/78
|
11.5/20.8
|
38*38/19*19
|
25/38
|
6.5/5.0
7.0/5.0
|
1220*3660 or customization
|
40/40
|
16.8/23.5
|
25*100
|
25
|
6.5/5.0
|
1220*3660 or customization
|
67
|
13.83
|
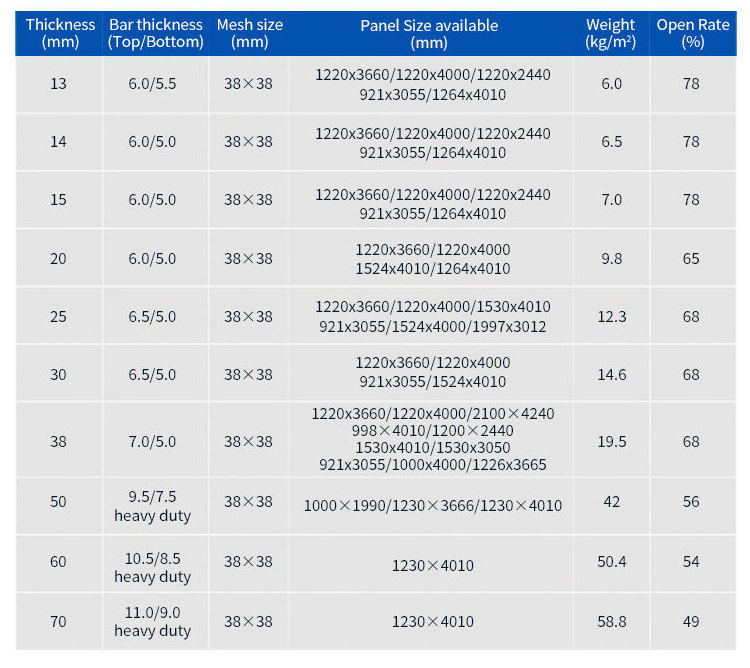
Production steps
Production Process
1. Stirring raw materials Resin, fiberglass fiber yarn, calcium powder filling, color paste, reagents, etc. are arranged in
proportion, stirring for 20 minutes.
2. Pouring material Pouring the mixed raw materials onto the mold machine corresponding to the FRP grating.
3. Draw yarn Lay the alkali-free yarn layer by layer to improve the strength of the FRP grating.
4. Compression mold The stirred raw materials are poured into the mold and compacted mechanically or manually.
5. Heat curing After the grating is heated for 20 minutes, the raw materials and yarn are fused together.
6. Cooling demoulding, mold lifting After the above process is completed, cooling for 10 minutes demolding, mold lifting,
semi-finished grating finished.
7. Grinding, painting and washing The FRP grating is polished and washed with a layer of varnish or water.
FRP grating is made by combining fibreglass and resin. The fibreglass gives the finished product its strength, while the resin makes it resistant to corrosive substances.
proportion, stirring for 20 minutes.
2. Pouring material Pouring the mixed raw materials onto the mold machine corresponding to the FRP grating.
3. Draw yarn Lay the alkali-free yarn layer by layer to improve the strength of the FRP grating.
4. Compression mold The stirred raw materials are poured into the mold and compacted mechanically or manually.
5. Heat curing After the grating is heated for 20 minutes, the raw materials and yarn are fused together.
6. Cooling demoulding, mold lifting After the above process is completed, cooling for 10 minutes demolding, mold lifting,
semi-finished grating finished.
7. Grinding, painting and washing The FRP grating is polished and washed with a layer of varnish or water.
FRP grating is made by combining fibreglass and resin. The fibreglass gives the finished product its strength, while the resin makes it resistant to corrosive substances.
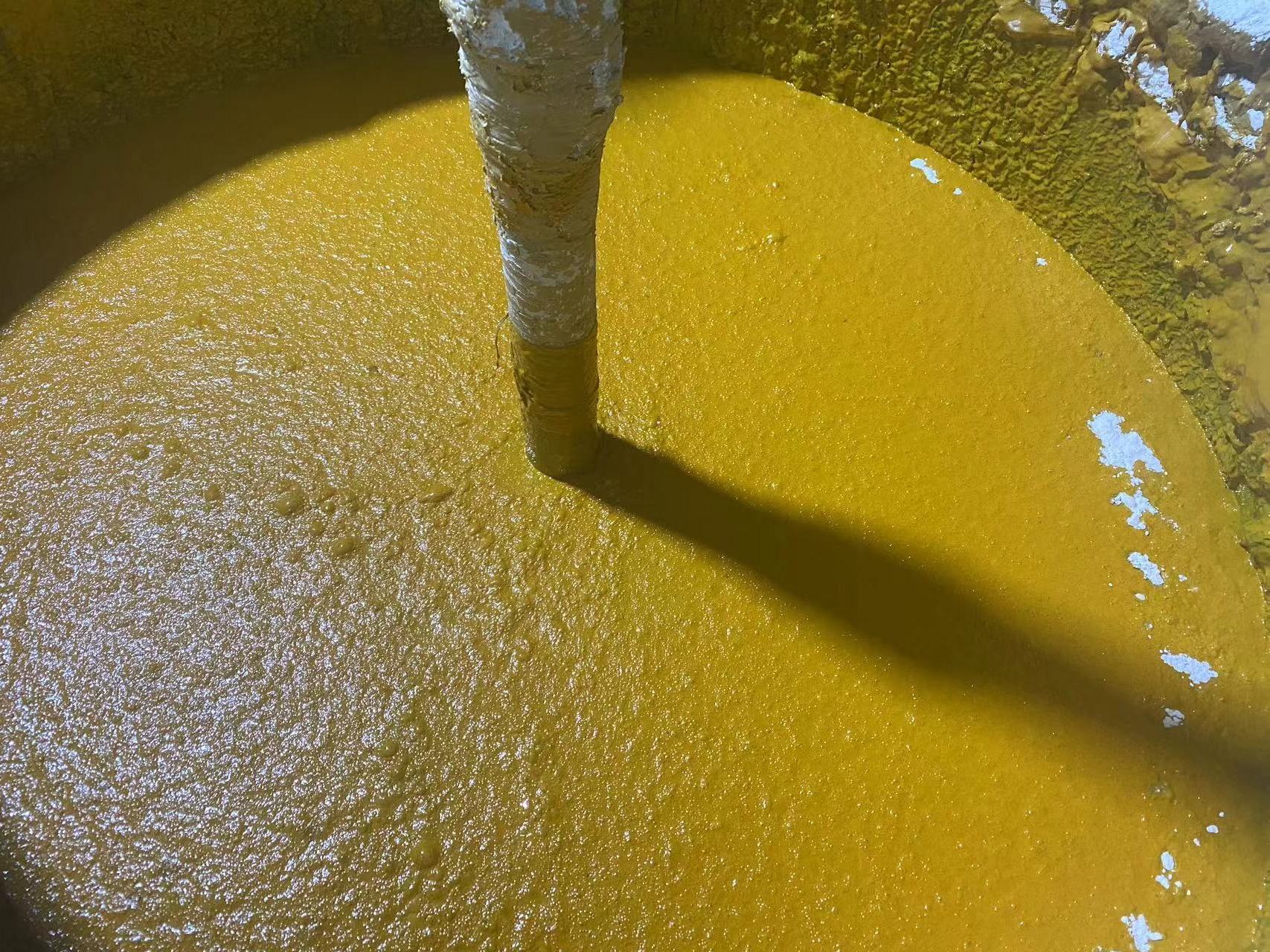
Details Images
Product packaging
Application
Fiber Glass Reinforced Plastic Grating, Plastic Floor Grid, Fiberglass Mini Mesh Grating
FRP grating is usually found in hazardous or harsh environments where it may be subject to the elements or come into contact with dangerous and corrosive chemicals. Here are some examples of situations where FRP grating is used:
1. On ships and offshore installations: the tough, durable nature of FRP grating makes it ideal for ships and oil rigs or other
offshore installations. It can be exposed to wind, rain and extremes of temperature and it can be submerged in water. It is also lightweight and relatively easy to transport.
2. Working with flammable materials: FRP grating doesn't give off any sparks, so it is often seen as a safer alternative to steel or other metals around flammable materials. For example, dropping metal objects on it would not create sparks, potentially causing atmospheric gases around it to ignite.
3. In electrically hazardous environments: FRP grating is often used in electrically hazardous environments because it is
non-conductive. It therefore reduces the risk of electric shock or other injuries in the event of an accident involving
electricity.
4. In chemical plants: FRP grating is non-corrosive. This can make it the ideal material for walkways, platforms and othersurfaces in chemical plants where there is a risk of corrosive materials leaking or being spilled.
5. On complex construction sites: the ease of transporting, storing and cutting FRP grating makes it a flexible and cost-effective solution for site work. Construction firms are able to use standard cutting tools to make FRP grating fit complicated and fluid site layouts.
FRP grating is usually found in hazardous or harsh environments where it may be subject to the elements or come into contact with dangerous and corrosive chemicals. Here are some examples of situations where FRP grating is used:
1. On ships and offshore installations: the tough, durable nature of FRP grating makes it ideal for ships and oil rigs or other
offshore installations. It can be exposed to wind, rain and extremes of temperature and it can be submerged in water. It is also lightweight and relatively easy to transport.
2. Working with flammable materials: FRP grating doesn't give off any sparks, so it is often seen as a safer alternative to steel or other metals around flammable materials. For example, dropping metal objects on it would not create sparks, potentially causing atmospheric gases around it to ignite.
3. In electrically hazardous environments: FRP grating is often used in electrically hazardous environments because it is
non-conductive. It therefore reduces the risk of electric shock or other injuries in the event of an accident involving
electricity.
4. In chemical plants: FRP grating is non-corrosive. This can make it the ideal material for walkways, platforms and othersurfaces in chemical plants where there is a risk of corrosive materials leaking or being spilled.
5. On complex construction sites: the ease of transporting, storing and cutting FRP grating makes it a flexible and cost-effective solution for site work. Construction firms are able to use standard cutting tools to make FRP grating fit complicated and fluid site layouts.
Hot Searches