Usually log length is more than 6 meters. Cutting according to the technology required length and quality. The cutting length should be product length add remains. For example, product is 1220mm*2440mm, cutting length usually be 2600mm or 1300mm. log length, camber and demerit affect plywood output directly. Remains are small wood pieces, truncations, sawdust, tec. Log cutting wastage ratio is 3%-10%.
- Product Details
- {{item.text}}
Quick Details
-
Voltage:
-
220V/380V
-
Dimension(L*W*H):
-
3550*1370*4200mm
-
Power (kW):
-
100kw
-
Weight (KG):
-
1000 kg
-
After-sales Service Provided:
-
Engineers available to service machinery overseas
-
Name:
-
Full automatic plywood production line
-
Capacity:
-
600 to 20000 pcs one day
-
Working time:
-
8hours/3shift
-
Raw material:
-
Logs
-
Board size:
-
1220x2440mm 1830x2750mm 1830x3660mm
-
Working methods:
-
Full automatic
Quick Details
-
Place of Origin:
-
Shandong, China
-
Type:
-
Plywood
-
Brand Name:
-
Xiangying
-
Voltage:
-
220V/380V
-
Dimension(L*W*H):
-
3550*1370*4200mm
-
Power (kW):
-
100kw
-
Weight (KG):
-
1000 kg
-
After-sales Service Provided:
-
Engineers available to service machinery overseas
-
Name:
-
Full automatic plywood production line
-
Capacity:
-
600 to 20000 pcs one day
-
Working time:
-
8hours/3shift
-
Raw material:
-
Logs
-
Board size:
-
1220x2440mm 1830x2750mm 1830x3660mm
-
Working methods:
-
Full automatic
Brief introduction of the plywood
Plywood is use the logs along the growth direction rotation cut into sheets of veneer, after drying, glue spreading then according to the adjacent veneer layer grain direction perpendicular principle assembly , glue paste. The layer number is an odd number, usually 3 to 13 layers, common has 3 layers plywood, 5layers plywood, 9 layers plywood, and 13 layers plywood. The outermost surface of the panel is called the surface veneer, the opposite is called the back veneer, and the inner layer is called the core veneer.
The first kind of plywood for weather resistance, boiling water resistance, one durability plywood, from here we can see this one plywood have advantages of high temperature resistance, can stand hot steam treatment;
The second kinds of plywood is waterproof plywood, can be immersed in cold water and short time hot water;
The third kind of plywood is damp proof plywood, can be immersed in cold water for a short time, it is suitable for indoor temperature. Used for furniture and general construction purposes;
The fourth types of plywood can not resistance the dump . used indoors and the fourth general plywood material usually have beech, basswood, ash, birch, elm, poplar, etc..
The first kind of plywood for weather resistance, boiling water resistance, one durability plywood, from here we can see this one plywood have advantages of high temperature resistance, can stand hot steam treatment;
The second kinds of plywood is waterproof plywood, can be immersed in cold water and short time hot water;
The third kind of plywood is damp proof plywood, can be immersed in cold water for a short time, it is suitable for indoor temperature. Used for furniture and general construction purposes;
The fourth types of plywood can not resistance the dump . used indoors and the fourth general plywood material usually have beech, basswood, ash, birch, elm, poplar, etc..
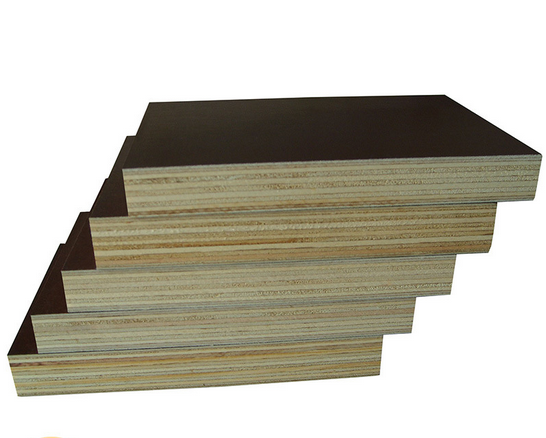
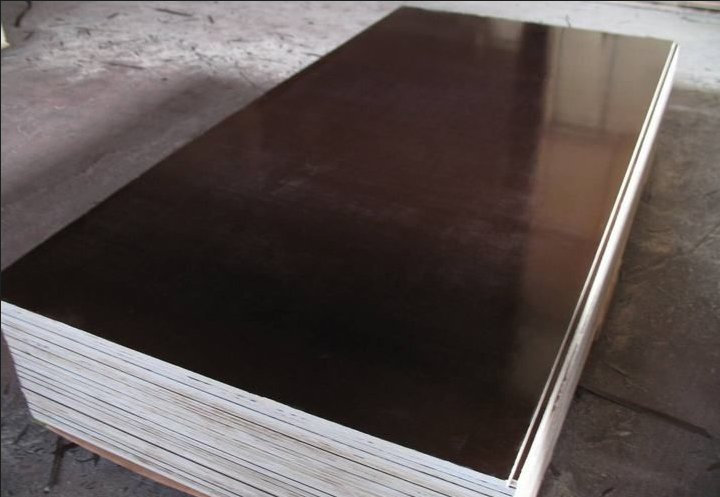
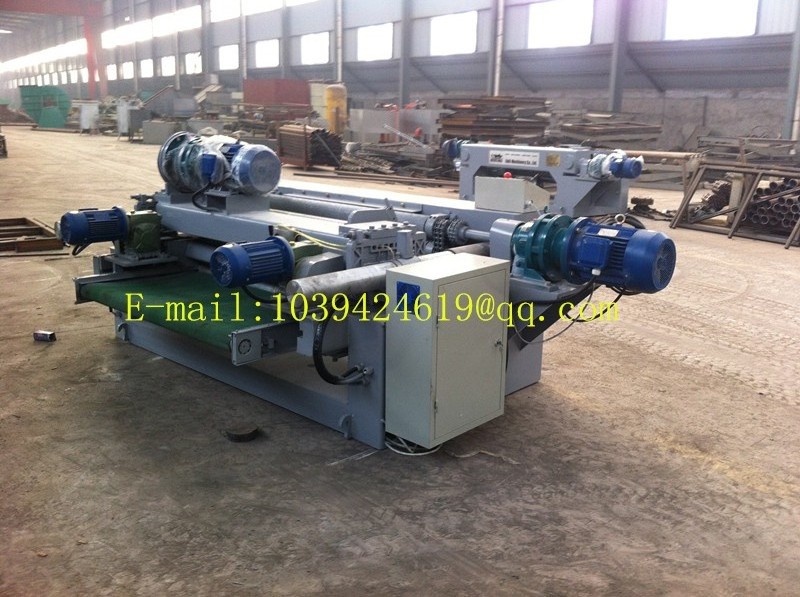
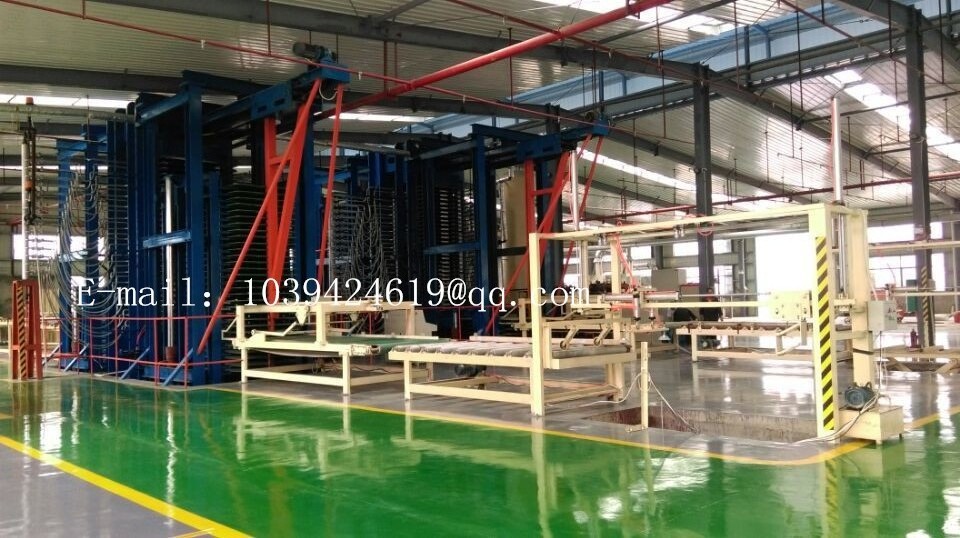
Machine name:Log cutting machine
Name:Peeling machine
Peeling is the most popular plywood producing process. Back veneer thickness is about 0.6mm, core veneer and centre veneer thickness is about 1.8mm.
Name:Drying machine
Veneer is moist. it should be dried according to the technology requirement. After drying, it will shrink. Dimension will become smaller. Veneer length, width, thickness will shrink. Shrink wastage is related to wood material, moisture containing, veneer thickness. Shrink wastage is 4%-10%.
Name:Handing machine
Handling include cutting, putting veneer together and mending. Cut zonal veneer into specification veneer or proper size which can be put together. Narrow zonal veneer can be put together into one veneer. Veneer with demerit can be mended to be qualified. Wastage in this part related to log material, peeled veneer quality, dried quality, and worker operation skill. Wastage ratio is 4%-16%. Import veneer processing plywood wastage ratio is 2%-11%.
Name:Hot press machine
Veneer be glued and stacked, then glue together under set temperature and pressure by hot press. As veneer temperature and moisture containing changes, veneer will shrink. Shrink wastage is related to temperature, pressure, hot press time, wood material, moisture containing, wastage ratio is 3%-8%
Name:Edge triming machine
Trimming the edge of the plywood flank from hot press to qualified plywood board. Remains related to process remains and product dimension. Production is bigger, wastage is smaller. Wastage ratio is 6%-9%
Name:Sanding machine
This is one abrasive belt sanding machine ,can make the board very smooth,and make the board in a very exact thickness size .Good quality board and melamine board all need this .
Pre-Sales Service
* Inquiry and consulting support.
* View our Factory.
After-Sales Service
*We suit for instal the machine, training how to use the machine.
* Engineers available to service machinery overseas in one year.