- Product Details
- {{item.text}}
Quick Details
-
Weight:
-
100 KG
-
Product name:
-
Stainless Steel Falling Film Evaporator
-
Model:
-
YFE-50
-
Application:
-
Food Beverage Chemical Haramceutical Industry
-
Function:
-
Multifunction
-
Volume of Class I recovery tank:
-
25~150 L
-
Evaporation area:
-
3.5~15 ㎡
-
Ethanol handling capacity:
-
90~500 L/h
-
Condenser area:
-
6~33 ㎡
-
Volume of Class II recovery tank:
-
25~150 L
-
Evaporator design pressure:
-
-0.098 MPa
Quick Details
-
Place of Origin:
-
Qinghai, China
-
Brand Name:
-
YHCHEM
-
Power:
-
200W
-
Weight:
-
100 KG
-
Product name:
-
Stainless Steel Falling Film Evaporator
-
Model:
-
YFE-50
-
Application:
-
Food Beverage Chemical Haramceutical Industry
-
Function:
-
Multifunction
-
Volume of Class I recovery tank:
-
25~150 L
-
Evaporation area:
-
3.5~15 ㎡
-
Ethanol handling capacity:
-
90~500 L/h
-
Condenser area:
-
6~33 ㎡
-
Volume of Class II recovery tank:
-
25~150 L
-
Evaporator design pressure:
-
-0.098 MPa
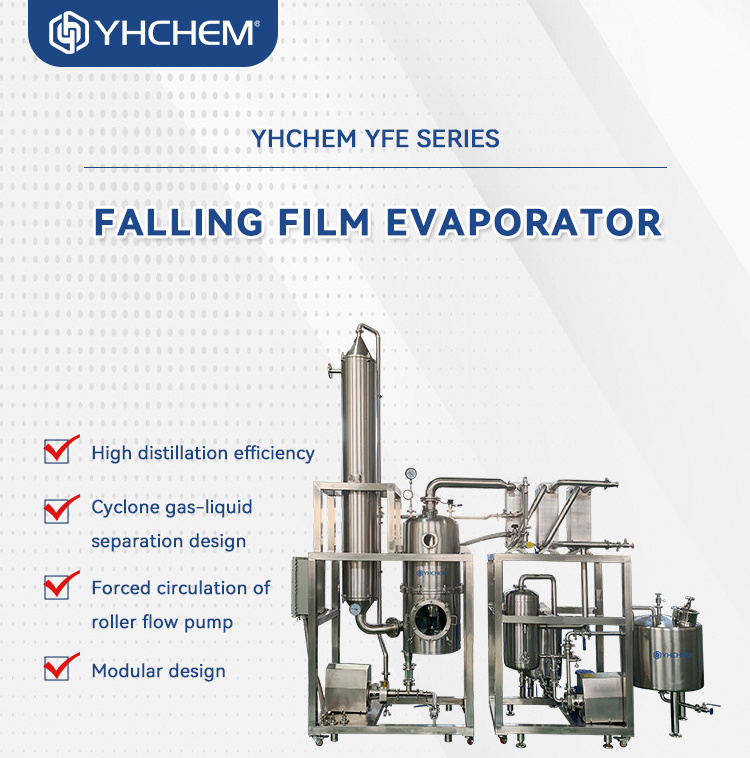
Product Parameter
Model
|
YFE-50
|
YFE-100
|
YFE-200
|
YFE-300
|
|||
Ethanol handling capacity (L/h)
|
90
|
180
|
350
|
500
|
|||
heat exchange area (m²)
|
3.5
|
6
|
11.5
|
15
|
|||
Condenser area (m²)
|
6
|
15
|
23
|
33
|
|||
Evaporator design pressure (MPa)
|
-0.098
|
|
|
|
|||
Volume of Class I recovery tank (L)
|
25
|
55
|
105
|
150
|
|||
Volume of Class II recovery tank (L)
|
25
|
55
|
105
|
150
|
Product Description
YFE Series Falling Film Evaporator is an evaporator that utilizes liquid film to flow and evaporate on the heating surface. lt is an efficient heat transfer device that is suitable for processing high-concentration organic compounds, high-salinity aqueous solutions, high-viscosity liquids, and so on. The falling film evaporator introduces the feed liquid into the heat exchanger of the falling film evaporator, and after the liquid distribution and film-forming device, it is evenly distributed into each heat exchange tube. Under the action of gravity, vacuum induction, and air flow, the liquid flows downward uniformly in a film shape.
During the flow, the heating medium in the shell side heats up and vaporizes, and the vapor and liquid phasesenter the separation chamber of the evaporator together. After sufficient separation, the vapor enters the condenser for condensation and collection. The falling film evaporator is mainly used in the solvent recovery of the biological, pharmaceutical, and chemical industries, and can be used in multiple stages to achieve higher energy efficiency ratio.
During the flow, the heating medium in the shell side heats up and vaporizes, and the vapor and liquid phasesenter the separation chamber of the evaporator together. After sufficient separation, the vapor enters the condenser for condensation and collection. The falling film evaporator is mainly used in the solvent recovery of the biological, pharmaceutical, and chemical industries, and can be used in multiple stages to achieve higher energy efficiency ratio.
Rroduct Advantage
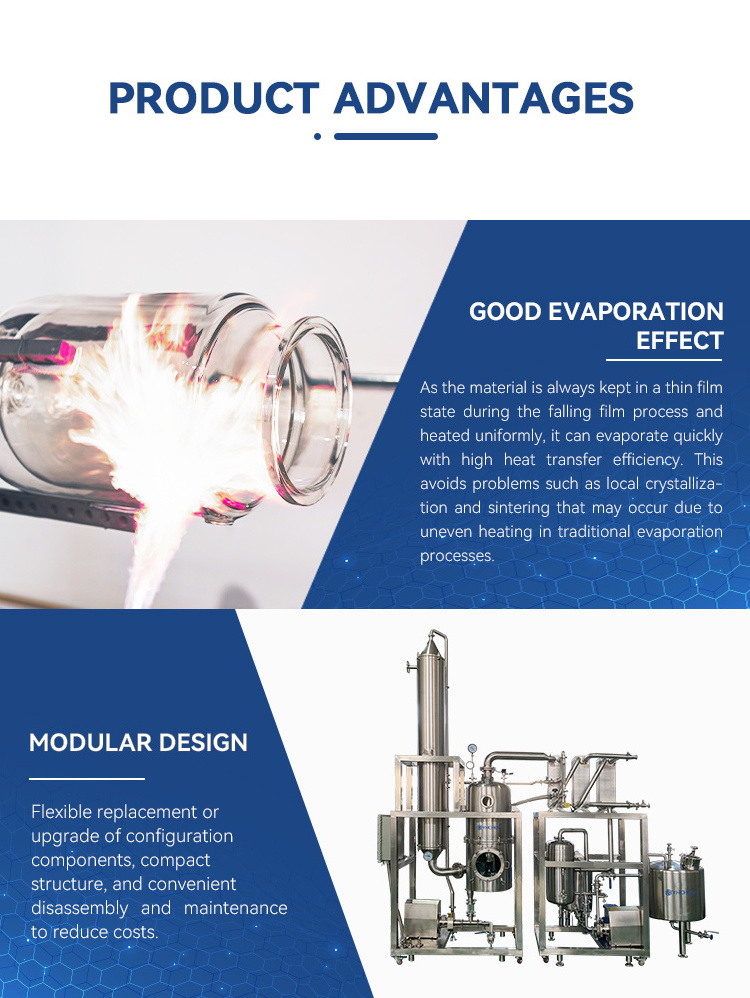
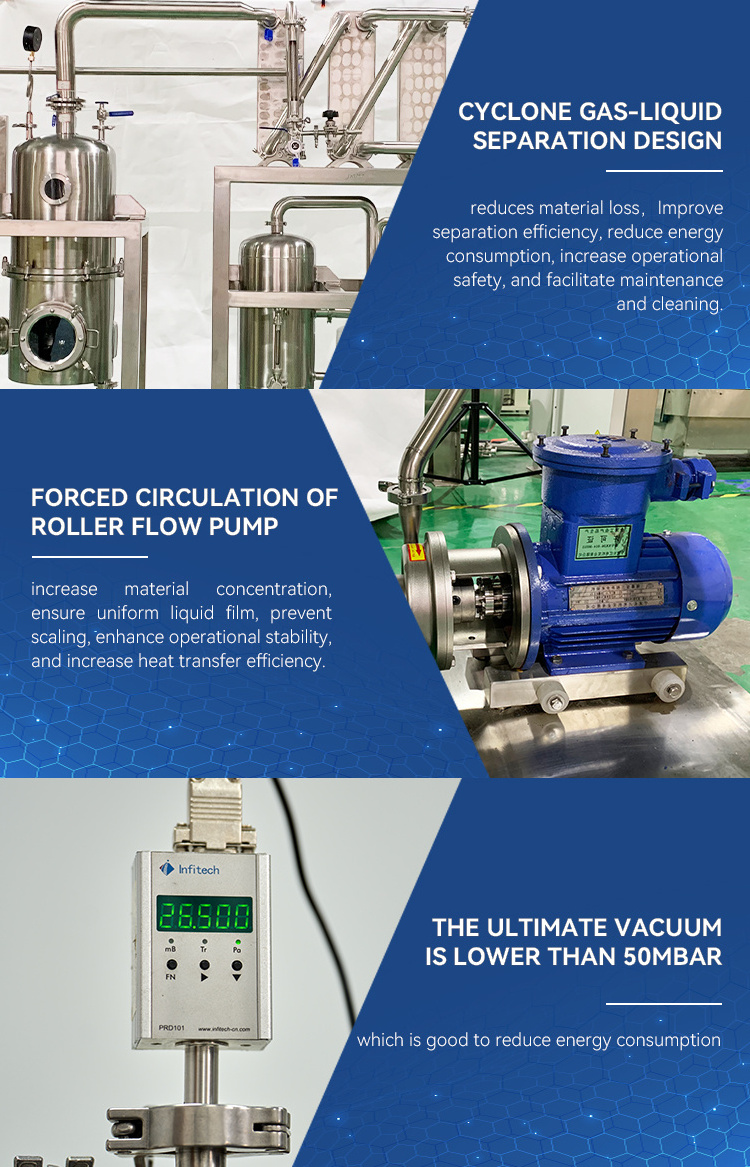
♣1.GOOD EVAPORATIONEFFECT
As the material is always kept in a thin film state during the falling film process and heated uniformly, it can evaporate quickly with high heat transfer efficiency. This avoids problems such as local crystallization and sintering that may occur due to uneven heating in traditional evaporation processes.
♣2.MODULAR DESIGN
Flexible replacement or upgrade of configuration components, compact structure, and convenient disassembly and maintenance to reduce costs.
♣3.CYCLONE GAS-LIQUIDSEPARATION DESIGN
reduces material loss, lmprove separation efficiency, reduce energy consumption, increase operational safety, and facilitate maintenance and cleaning
♣4.FORCED CIRCULATION OFROLLER FLOW PUMP
increase material concentration increase ensure uniform liquid film, prevent scaling, enhance operational stability and increase heat transfer efficiency
♣5.THE ULTIMATE VACUUM IS LOWER THAN 50MBAR
Which is good to reduce energy consumption
As the material is always kept in a thin film state during the falling film process and heated uniformly, it can evaporate quickly with high heat transfer efficiency. This avoids problems such as local crystallization and sintering that may occur due to uneven heating in traditional evaporation processes.
♣2.MODULAR DESIGN
Flexible replacement or upgrade of configuration components, compact structure, and convenient disassembly and maintenance to reduce costs.
♣3.CYCLONE GAS-LIQUIDSEPARATION DESIGN
reduces material loss, lmprove separation efficiency, reduce energy consumption, increase operational safety, and facilitate maintenance and cleaning
♣4.FORCED CIRCULATION OFROLLER FLOW PUMP
increase material concentration increase ensure uniform liquid film, prevent scaling, enhance operational stability and increase heat transfer efficiency
♣5.THE ULTIMATE VACUUM IS LOWER THAN 50MBAR
Which is good to reduce energy consumption
Application Fields
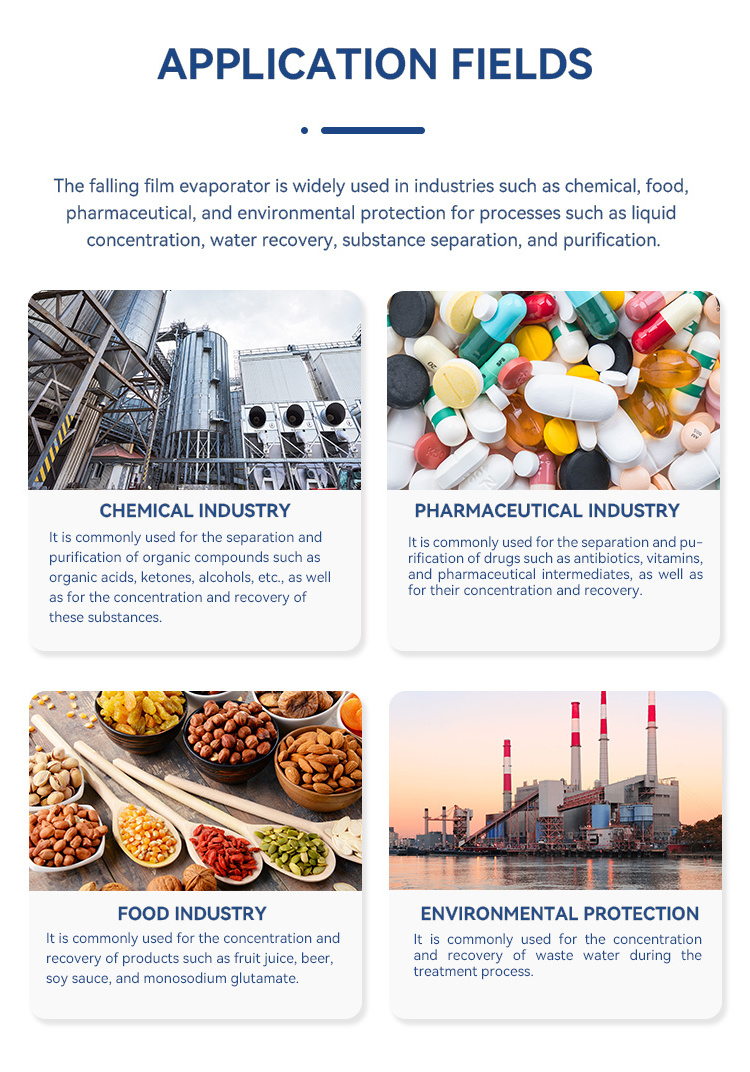
♣1.The falling film evaporator is widely used in industries such as chemical, food and environmental protection for processes such as liquid concentration, water recovery, substance separation, and purification.
♣2.CHEMICAL INDUSTRY
It is commonly used for the separation and purification of organic compounds such as organic acids, ketones, alcohols, etc, as well as for the concentration and recovery of these substances.
♣3.It is commonly used for the separation, purification, concentration and recovery of antibiotics, vitamins, etc.
♣4.FOOD INDUSTRY
lt is commonly used for the concentration and recovery of products such as fruit juice, beer, soy sauce and monosodium glutamate.
♣5.ENVIRONMENTAL PROTECTION
It is commonly used for the concentration and recovery of waste water during the treatment process.
♣2.CHEMICAL INDUSTRY
It is commonly used for the separation and purification of organic compounds such as organic acids, ketones, alcohols, etc, as well as for the concentration and recovery of these substances.
♣3.It is commonly used for the separation, purification, concentration and recovery of antibiotics, vitamins, etc.
♣4.FOOD INDUSTRY
lt is commonly used for the concentration and recovery of products such as fruit juice, beer, soy sauce and monosodium glutamate.
♣5.ENVIRONMENTAL PROTECTION
It is commonly used for the concentration and recovery of waste water during the treatment process.
Support Customisation
Can be customized according to customer's requirement.
♣1.GLASS FALLING FILM DESIGN
♣2.CUSTOMIZED DESIGN FOR HEAT TRANSFER AREA
♣2.CUSTOMIZED DESIGN FOR HEAT TRANSFER AREA
Product Structure
♣1.Evaporator
♣2.Oil-water separator
♣3.Plate heat exchanger (preheating)
♣4/5.plate heat exchanger (condensation)
♣6.Storage tank
♣7.Explosion-proof control cabinet
♣8.Centrifugal discharge pump
♣9.Centrifugal feed pump
♣2.Oil-water separator
♣3.Plate heat exchanger (preheating)
♣4/5.plate heat exchanger (condensation)
♣6.Storage tank
♣7.Explosion-proof control cabinet
♣8.Centrifugal discharge pump
♣9.Centrifugal feed pump
Supported Equipment
♣1.Cooling circulator
♣2.Heating circulator
♣3.The rotary vane vacuum pump
♣2.Heating circulator
♣3.The rotary vane vacuum pump
Product Series
♣1.WIPE FILM MOLECULAR DISTILLATION SYSTEM (STAINLESS STEEL)
♣2.WIPE FILM MOLECULAR DISTILLATION SYSTEM (BOROSILICATE GLASS)
♣3.THIN FILM EVAPORATION SYSTEM (STAINLESS STEEL)
♣4.THIN FILM EVAPORATION SYSTEM (BOROSILICATE GLASS)
♣2.WIPE FILM MOLECULAR DISTILLATION SYSTEM (BOROSILICATE GLASS)
♣3.THIN FILM EVAPORATION SYSTEM (STAINLESS STEEL)
♣4.THIN FILM EVAPORATION SYSTEM (BOROSILICATE GLASS)
Hot Searches