- Product Details
- {{item.text}}
Quick Details
-
Brand Name:
-
ZW
-
Voltage:
-
220V / 380V / As client's demand
-
Dimension(L*W*H):
-
900*900*750mm
-
Weight:
-
200 KG
-
Product name:
-
Tumbler swing sieve vibrating screen for powder food industry
-
Keyword:
-
Large Capacity Swing Vibration Sieve
-
Diameter(mm):
-
800-2600mm
-
Layer(s):
-
1-5 Layers
-
Motor:
-
China Standard Brand
-
Usage:
-
removing impurities
-
Material:
-
Carbon Steel/ Stainless Steel
-
Function:
-
Screening\separation\sorting\sieving
-
Customized:
-
Support
-
Cleaning:
-
Automaitic Self-cleaning
Quick Details
-
Type:
-
Circular
-
Marketing Type:
-
New Product 2023
-
Place of Origin:
-
Henan, China
-
Brand Name:
-
ZW
-
Voltage:
-
220V / 380V / As client's demand
-
Dimension(L*W*H):
-
900*900*750mm
-
Weight:
-
200 KG
-
Product name:
-
Tumbler swing sieve vibrating screen for powder food industry
-
Keyword:
-
Large Capacity Swing Vibration Sieve
-
Diameter(mm):
-
800-2600mm
-
Layer(s):
-
1-5 Layers
-
Motor:
-
China Standard Brand
-
Usage:
-
removing impurities
-
Material:
-
Carbon Steel/ Stainless Steel
-
Function:
-
Screening\separation\sorting\sieving
-
Customized:
-
Support
-
Cleaning:
-
Automaitic Self-cleaning
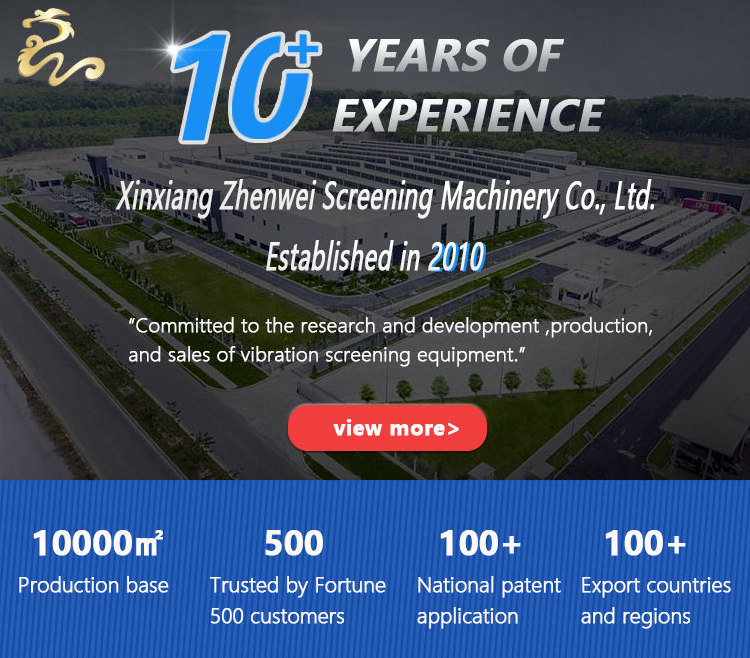

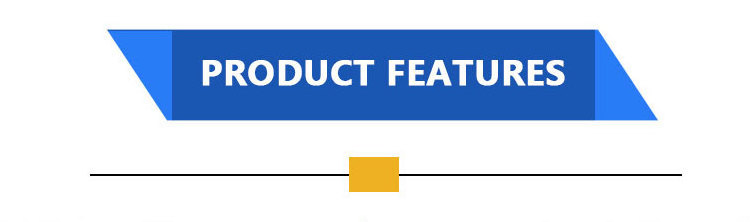
Swing sieve is designed to meet the large output, high-precision screening manufacturers and special design of a high-efficiency screening machine, the simplest screening is the two eyes watching hands screening. Swing sifter is the mechanical simulation of this, it is currently the most effective simulation of the effective principle of artificial sieving movement (screening accuracy,efficiency, screen life are 5-10 times the conventional circular sieve), in line with all the fine and ultra-fine range of powder and particulate materials, especially suitable for difficult to deal with the material.
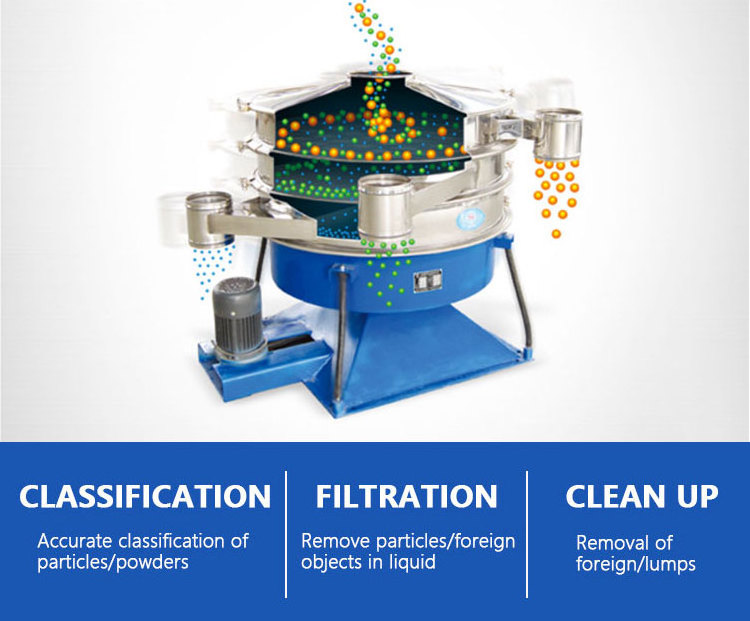
Structural principle
-The basic rotary motion is similar to manual screening. The eccentricity is adjustable from 25 to 40 mm and the low speed V-belt drive is adjustable from 120 to 360 rpm.
-The residence time of each product can be adjusted by the radial and tangential angle of the tumbler screen towards the drive axis.
-The material forms a horizontal and throwing three-dimensional tumbling motion on the screen surface, dispersing uniformly over the entire screen surface from the center to the outer edges and thus propagating axially in a spiral motion. The fine particles are thus completed by the entire screening process.
-The horizontal and vertical acceleration increases with the movement of the particles, and particles close to the screen aperture size are successfully separated; larger particles are transported to the outlet, where the flow rate is controlled by an adjustable guide, which is another factor in controlling the residence time of the material.
-This process is repeated between each screen deck.
-The basic rotary motion is similar to manual screening. The eccentricity is adjustable from 25 to 40 mm and the low speed V-belt drive is adjustable from 120 to 360 rpm.
-The residence time of each product can be adjusted by the radial and tangential angle of the tumbler screen towards the drive axis.
-The material forms a horizontal and throwing three-dimensional tumbling motion on the screen surface, dispersing uniformly over the entire screen surface from the center to the outer edges and thus propagating axially in a spiral motion. The fine particles are thus completed by the entire screening process.
-The horizontal and vertical acceleration increases with the movement of the particles, and particles close to the screen aperture size are successfully separated; larger particles are transported to the outlet, where the flow rate is controlled by an adjustable guide, which is another factor in controlling the residence time of the material.
-This process is repeated between each screen deck.
Features
Up to 5 times the output per unit area; Precise separation up to 6 levels, screening efficiency up to 90%-99%; Use of silicone rubber ball, ultrasonic and other efficient screen cleaning device system, the screen holes will not be clogged. Closed dust removal, safe operation; acceleration is 4.5 times lower than vibrating screen, screening parts life is improved and maintenance is reduced; noise <75 dB. Optimized weight balance, low foundation dynamic load.
Up to 5 times the output per unit area; Precise separation up to 6 levels, screening efficiency up to 90%-99%; Use of silicone rubber ball, ultrasonic and other efficient screen cleaning device system, the screen holes will not be clogged. Closed dust removal, safe operation; acceleration is 4.5 times lower than vibrating screen, screening parts life is improved and maintenance is reduced; noise <75 dB. Optimized weight balance, low foundation dynamic load.
Modular design and process optimization
Each swing screen through our more subtle combination of transformation, a short period of time can make the throughput capacity and screening precision doubled, our professional sales engineers will be for your material professional design more suitable screening modularization.
Bouncing Ball Cleaning System
This form of screen clearing is through the high performance bouncing ball laid under the screen, above the ball plate irregularly strikes the screen, by the second vibration to complete the screen clearing and anti-blocking, this structure is simple and effective, suitable for most of the screen operation of the screen and anti-blocking clearing.
This form of screen clearing is through the high performance bouncing ball laid under the screen, above the ball plate irregularly strikes the screen, by the second vibration to complete the screen clearing and anti-blocking, this structure is simple and effective, suitable for most of the screen operation of the screen and anti-blocking clearing.
Brush Cleaning System
The rotary brush screen clearing system relies on the rotation of the brush arranged under the screen to clear the screen, which is suitable for spherical, crystallized and brittle materials. The supporting arm of the rotary brush is driven by a speed reducer mounted on the chassis.
The rotary brush screen clearing system relies on the rotation of the brush arranged under the screen to clear the screen, which is suitable for spherical, crystallized and brittle materials. The supporting arm of the rotary brush is driven by a speed reducer mounted on the chassis.
Ultrasonic Cleaning System
Ultrasonic screen cleaning is suitable for the treatment of very fine materials. The system is through the ultrasonic generator generated by the high-frequency vibration transmitted to the screen mesh to achieve the purpose of clearing the mesh, the device can not only be effective in clearing the mesh to prevent clogging, but also significantly improve the production capacity, in addition, its style can be updated to meet the needs of different screening processes.
Ultrasonic screen cleaning is suitable for the treatment of very fine materials. The system is through the ultrasonic generator generated by the high-frequency vibration transmitted to the screen mesh to achieve the purpose of clearing the mesh, the device can not only be effective in clearing the mesh to prevent clogging, but also significantly improve the production capacity, in addition, its style can be updated to meet the needs of different screening processes.
(1)Double-deck secondary screening
The product is pre-screened at the top into two parts, the fine part is taken over by an empty plate, the larger material and the fine material not separated into the side channel and into the center of the lower screen surface. The lower deck of this model has the same holes as the upper deck, and the larger sizes are screened twice, thus further improving the accuracy of the screened material.
The product is pre-screened at the top into two parts, the fine part is taken over by an empty plate, the larger material and the fine material not separated into the side channel and into the center of the lower screen surface. The lower deck of this model has the same holes as the upper deck, and the larger sizes are screened twice, thus further improving the accuracy of the screened material.
(2) Double-deck screening with pre-screening
This type of double-deck screening model can be fitted with one or two pre-screening surfaces with coarser holes to handle the coarse fraction, which can be separated into up to four different fractions at a time.
This type of double-deck screening model can be fitted with one or two pre-screening surfaces with coarser holes to handle the coarse fraction, which can be separated into up to four different fractions at a time.
(3) Reverse double deck screening
This type is suitable for the treatment of materials with a high percentage of sub-screen material. The upper deck of the screen is for fine screening, and with the help of the coarser particles, the fine material can easily pass through the screen and be taken up by an empty plate, while the larger portion of the material enters the side channels and continues to be processed on the lower deck, which separates up to four different portions at a time.
This type is suitable for the treatment of materials with a high percentage of sub-screen material. The upper deck of the screen is for fine screening, and with the help of the coarser particles, the fine material can easily pass through the screen and be taken up by an empty plate, while the larger portion of the material enters the side channels and continues to be processed on the lower deck, which separates up to four different portions at a time.
(4) Three-deck screening
The highest screening efficiency can be achieved with this model, which is equivalent to double-deck screening with the same screen aperture installed on the third deck.
The highest screening efficiency can be achieved with this model, which is equivalent to double-deck screening with the same screen aperture installed on the third deck.
(5) Double throughput screening
This style is suitable for operations with special output requirements. It can be used if two parts are to be processed at high throughput. This is accomplished by equalizing the product through a distributor installed between the upper and lower decks. With this model, the output of a single-deck screen can be increased to about 180%. Anti-clogging device effect.
This style is suitable for operations with special output requirements. It can be used if two parts are to be processed at high throughput. This is accomplished by equalizing the product through a distributor installed between the upper and lower decks. With this model, the output of a single-deck screen can be increased to about 180%. Anti-clogging device effect.
Equipment
type
|
YB-
600
|
YB-
1000
|
YB-
1200
|
YB-
1600
|
YB-
2000
|
YB-
2200
|
YB-
2400
|
YB-
2600
|
Diameter
(mm)
|
650
|
1040
|
1200
|
1580
|
1880
|
2150
|
2400
|
2650
|
Screening
area (㎡)
|
0.29
|
0.76
|
1.1
|
1.8
|
2.6
|
3.46
|
3.63
|
5.3
|
Space
requirements (㎡)
|
0.4
|
1.8
|
2.5
|
3.9
|
5.6
|
7.1
|
8.75
|
9.6
|
Maximum
screen layer
|
Five layers
|
Five layers
|
Five layers
|
Five layers
|
Five layers
|
Five layers
|
Five layers
|
Five layers
|
Power (kw)
|
0.25
|
1.5
|
2.2
|
3
|
4
|
4
|
5.5
|
5.5
|
Cleaning
device optional
|
|
|
|
|
|
|
|
|
Silicone
ball cleaning net
|
Five layers
|
Five layers
|
Five layers
|
Five layers
|
Five layers
|
Five layers
|
Five layers
|
Five layers
|
Swivel
brush clean net
|
Five layers
|
Five layers
|
Five layers
|
Five layers
|
Five layers
|
Five layers
|
Five layers
|
Five layers
|
Ultrasonic
cleaning
|
Five layers
|
Five layers
|
Five layers
|
Five layers
|
Five layers
|
Five layers
|
Five layers
|
Five layers
|
Filter
attachment
|
Two layers
|
Two layers
|
Two layers
|
Two layers
|
Two layers
|
Two layers
|
Two layers
|
Two layers
|
Base
width (mm)
|
630
|
900
|
1100
|
1340
|
1340
|
1540
|
1740
|
1940
|
Height of
one layer
(mm)
|
830
|
1155
|
1480
|
1480
|
1500
|
1520
|
1570
|
1580
|
Weight of
one layer (kg)
|
140
|
490
|
700
|
980
|
1050
|
1250
|
1690
|
1900
|
Height of
two layers
(mm)
|
960
|
1280
|
1640
|
1640
|
1660
|
1680
|
1700
|
1710
|
weight
of
two layers
(kg
)
|
155
|
535
|
770
|
1060
|
1140
|
1370
|
1780
|
2000
|
Height of
three layers
(mm)
|
1090
|
1400
|
1800
|
1800
|
1820
|
1840
|
1810
|
1840
|
Weight of
three layers (kg)
|
170
|
580
|
840
|
1140
|
1230
|
1490
|
1870
|
2100
|
Height of
four layers
(mm)
|
1220
|
1525
|
1960
|
1960
|
1980
|
2000
|
1930
|
1970
|
Weight of
four layers (kg)
|
185
|
625
|
910
|
1220
|
1320
|
1610
|
1960
|
2200
|
Height of
five
layers
(mm)
|
1350
|
1650
|
2120
|
2120
|
2140
|
2160
|
2050
|
2100
|
Weight of
five layers (kg)
|
200
|
670
|
980
|
1300
|
1410
|
1730
|
2050
|
2300
|
1.Our company can design and manufacture special type and specification sieve machine according to user's need.
2.The company reserves the right to modify all technical information and dimensions. If the physical object does not conform to the pattern in the text, the physical object should prevail, and the right of interpretation belongs to the company.
1. Chemical industry: resin pigment, calcium carbonate, decorative coatings, medicine, grease, paint, palette, etc.
2. Abrasive material and ceramic industry: building sand, mica, alumina, antimony ore, silica sand, abrasive, refractory material,slurry, etc.
3. Food industry: sugar, salt, alkali, flour powder, nut powder, farina, gourmet powder, starch, milk powder, yeast powder, pollen, food additive, bean milk, juice, etc.
4. Paper-making industry: coated slurry, exhaust liquid, paper making liquid and waste water reclamation, etc.
5. Metallurgy and mining industry: quartz sand, sand, ore, titanium oxide, zinc oxide, etc.
6. Mechanical industry: casting sand, charcoal, metallurgy powder, aluminum powder, electromagnetic material and metal powder,etc.
2. Abrasive material and ceramic industry: building sand, mica, alumina, antimony ore, silica sand, abrasive, refractory material,slurry, etc.
3. Food industry: sugar, salt, alkali, flour powder, nut powder, farina, gourmet powder, starch, milk powder, yeast powder, pollen, food additive, bean milk, juice, etc.
4. Paper-making industry: coated slurry, exhaust liquid, paper making liquid and waste water reclamation, etc.
5. Metallurgy and mining industry: quartz sand, sand, ore, titanium oxide, zinc oxide, etc.
6. Mechanical industry: casting sand, charcoal, metallurgy powder, aluminum powder, electromagnetic material and metal powder,etc.
Xinxiang Zhenwei Screening Machinery Co., Ltd.
is located in the east side of Qinglong Road in Xinxiang economic and technological industrial agglomeration zone, adjacent to 107 National Highway, with superior geographical location and convenient transportation. It is an enterprise committed to the research and development and production of fine screening machinery. It integrates design, production, sales and service, and is committed to solving various screening problems and meeting the requirements of modern construction standards. The introduction of scientific management methods, combined with strong technical force and perfect testing means, has gradually developed into a high-tech enterprise. The company's main products are
swing screen
,
rotary vibrating screen
,
ultrasonic screen
,
air flow screen
and
other fine screening equipment
.
Products are widely used in
food industry
,
chemical synthesis industry
,
plastic industry
,
resin industry
,
Chinese and Western medicine
,
metal powder
,
mining industry
and other industries that need to use screening equipment.
Q1: Industry application
A:Our vibrating screen machines are widely used in food, medicine,chemical industry, metallurgy,mining, ceramics, plastics,electro-magnetic materials, thermoelectricity, building materials and other industries.
A:Our vibrating screen machines are widely used in food, medicine,chemical industry, metallurgy,mining, ceramics, plastics,electro-magnetic materials, thermoelectricity, building materials and other industries.
Q2: Guaranteed
A:The whole machine is guaranteed for one year, and the core accessories are guaranteed for three months.After receiving the goods,if you have any quality problems, please contact us in time.
A:The whole machine is guaranteed for one year, and the core accessories are guaranteed for three months.After receiving the goods,if you have any quality problems, please contact us in time.
Q3: After-sale service
A: lf there is any installation or test machine problem,provide remote online guidance or on-site service.
A: lf there is any installation or test machine problem,provide remote online guidance or on-site service.
Q4: Shipping Method and Shipping Time
A:1.By air port to port: about 7days depends on port. 2.By sea port to port: about 20-35days.
A:1.By air port to port: about 7days depends on port. 2.By sea port to port: about 20-35days.
Q5: Where is Xinxiang Zhenwei Screening Machinery? ls it possible to visit your factory?
A: Our company is located in Xinxiang City, Henan province, a very famous vibrating screen city in China. The city is near by Zhengzhou Airport, it only take one and half hour from Zhengzhou Airport, welcome to visit our company!
A: Our company is located in Xinxiang City, Henan province, a very famous vibrating screen city in China. The city is near by Zhengzhou Airport, it only take one and half hour from Zhengzhou Airport, welcome to visit our company!
Hot Searches