- Product Details
- {{item.text}}
Quick Details
-
Formaldehyde Emission Standards:
-
E2
-
Place of Origin:
-
China
-
Model Number:
-
Red Film Faced Plywood
-
Core:
-
Poplar Hardwood Combi
-
Thickness:
-
12mm-24mm
-
Glue:
-
WBP Phenolic
-
Size:
-
1220x2440mm/1250x2550mm/as Request
-
Certification:
-
ISO9001:2000
-
Density:
-
530-700kg/m3
-
Packing:
-
Pallet Packing
-
Delivery time:
-
10-25days
-
Thickness tolerance:
-
0.2-0.5mm Depends
-
Color:
-
Black/Red/Brown
Quick Details
-
Warranty:
-
NONE
-
Project Solution Capability:
-
Others
-
Application:
-
Office Building
-
Formaldehyde Emission Standards:
-
E2
-
Place of Origin:
-
China
-
Model Number:
-
Red Film Faced Plywood
-
Core:
-
Poplar Hardwood Combi
-
Thickness:
-
12mm-24mm
-
Glue:
-
WBP Phenolic
-
Size:
-
1220x2440mm/1250x2550mm/as Request
-
Certification:
-
ISO9001:2000
-
Density:
-
530-700kg/m3
-
Packing:
-
Pallet Packing
-
Delivery time:
-
10-25days
-
Thickness tolerance:
-
0.2-0.5mm Depends
-
Color:
-
Black/Red/Brown

Product advantages
The superiority of high-end film-coated building formwork compared with steel formwork
Steel formwork is heavy and film-coated board is light, which facilitates the construction of high-rise buildings. Compared with steel formwork, it has a large area and reduces joints. It improves the quality and progress of the project, and can be cut into special specifications as required according to the needs of the project. The cast-in-place surface of the formwork using high-end film-coated buildings is smooth and beautiful. The secondary plastering process is omitted, which saves both labor and materials.
The superiority of high-end film-coated building formwork compared with bamboo plywood
Bamboo plywood is limited by its own material characteristics, and the thickness tolerance is not easy to grasp. The T performance of high-end wood formwork is higher than that of bamboo plywood. It is easy to nail, saw and drill holes, which facilitates construction. It has good water resistance and does not open after boiling for 20 hours. It is lighter than bamboo plywood. The cast-in-place surface is smooth and flat, while the cast-in-place surface of bamboo plywood is a big defect.
Advantages of clear water building formwork series board
1. Light weight: more suitable for high-rise building and bridge construction.
2. Large format: the maximum format is 2440X1220, which reduces the number of joints and improves the efficiency of formwork.
3. No warping, deformation, cracking, good water resistance, high turnover rate, long service life.
4. Easy demoulding, only 1/7 of steel mold.
5. Make plain concrete: the surface of the cast object is smooth and beautiful, minus the secondary plastering process of the wall, can be directly decorated, shortening the construction period.
6. Corrosion resistance: does not pollute the concrete surface.
7. Good thermal insulation performance, conducive to winter construction.
8. Can be used as a template for curved planes.
9. Good construction performance, nailing, sawing, drilling and other performance are better than bamboo plywood and small steel plates. Templates of various shapes can be processed according to construction needs.
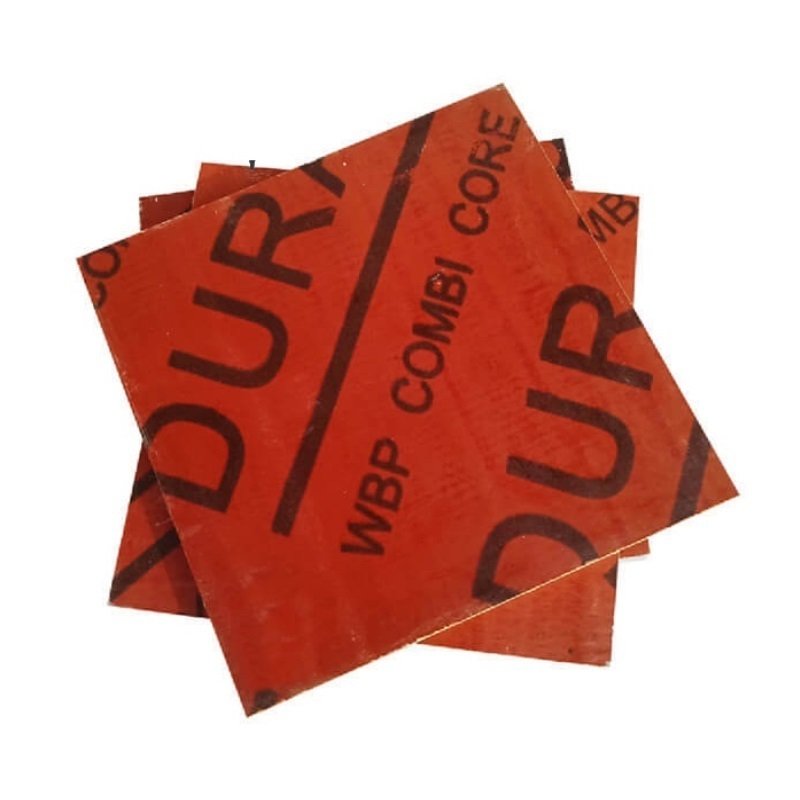
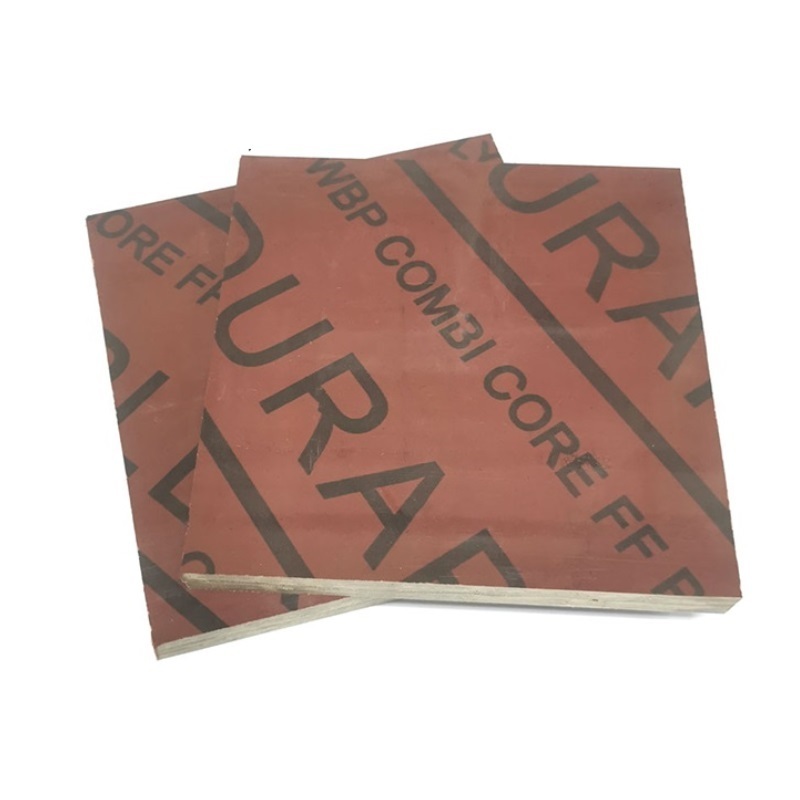
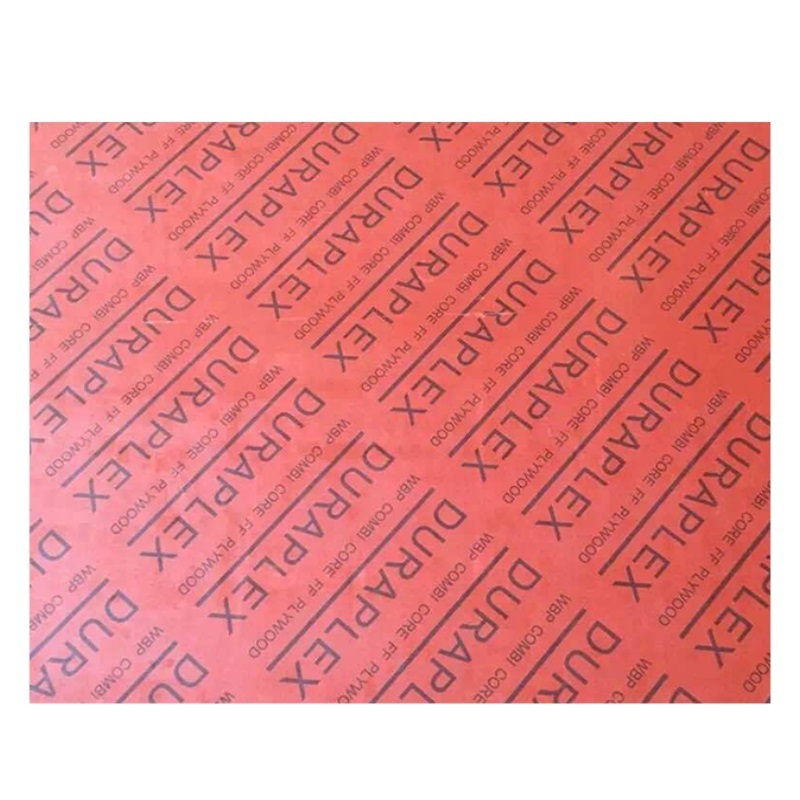
Product Characteristic
(I) Characteristics of clear water formwork:
1. Can be used repeatedly: The product uses high-quality waterproof glue, which is suitable for indoor and outdoor use. The phenolic resin film on the surface is wear-resistant, corrosion-resistant and high-strength.
2. Easy to use: The surface is smooth and flat, which is easy to demould, and the secondary plastering operation on the surface after pouring concrete is eliminated, shortening the decoration operation period.
3. Low thermal conductivity, which is conducive to winter construction insulation.
(II) Scope of use:
Clear water formwork is very suitable for horizontal formwork, shear wall, vertical wall panel, bridge, dam, tunnel and beam column formwork in high-rise buildings.
(III) Sawing formwork:
Please use an alloy saw blade with a diameter of 300 mm and 100 teeth, and use a sawing machine with a guide rail to keep the sawing edge as straight as possible. The speed is 4000 rpm. If irregular geometric shapes are required, high-speed portable electric saws can be used to saw the edges on site. To prevent burrs, pads should be placed under the board when sawing and drilling.
(IV) Edge sealing and repainting:
Clear water formwork is sealed before leaving the factory. When cutting boards and drilling holes, if you find scratches, bumps or other minor damage on the template surface, please paint the saw edge or drill hole three times with water-resistant phenolic paint. Phenolic paint should be applied again.
(V) Use of templates:
The wooden squares close to the template should be laid vertically. The board gaps should be minimized as much as possible, and the boards should be flat. The specifications of the wooden squares are 5 x 10 or 10x 10cm. The board gaps are filled with putty or sealed with adhesive tape to prevent leakage
Slurry and slurry from contaminating the board edges. It is strictly forbidden to collide with hard objects, hit with crowbars, and drag steel bars on the board surface.
1. The top formwork first lays the wooden squares horizontally on the scaffolding. The spacing is 1.2m. Then the wooden squares are vertically pressed with a spacing of 0.4-0.6m. When the thickness of the poured concrete exceeds 200mm; the spacing should be appropriately reduced.
2. Wall formwork: Lay three wooden squares longitudinally behind the formwork, and connect two wooden squares horizontally, leaving space for through-wall screws, and erect diagonal braces. If conditions permit, steel ribs can be used to connect horizontally to form a combined large wall formwork, which can be directly hoisted. Single formwork can be disassembled and replaced.
3. Cut the beam and column formwork according to size, leaving space for through-wall bolts on the top. The column formwork can be locked on all four sides with a short scaffold, and erect diagonal braces.
(VI) Surface treatment:
Before use, a layer of release agent should be evenly applied on the surface of the formwork to facilitate demoulding and surface cleaning, extend the service life of the formwork, and improve the surface quality of the concrete.
(VII) Storage and stacking:
After the formwork is disassembled, it should be cleaned immediately with non-metallic tools such as brushes, plastic wooden scrapers, etc., and then padded with wooden squares, with the edges and corners aligned and stacked on a flat ground. The board surface must not touch the ground. The formwork should be kept well ventilated, prevented from sun and rain, and checked regularly.
Hot Searches