1. Material Selection: Choose the appropriate material for the roller shaft based on the specific application requirements, such as steel, stainless steel, or aluminum.
2. Cutting: Cut the raw material into the desired length using a saw or other cutting tools.
3. Turning: Mount the cut piece onto a lathe and use cutting tools to remove excess material and shape the roller shaft to the
required dimensions. This process involves precision turning and may include operations such as facing, chamfering, and grooving.
4. Drilling: Drill holes or bores into the roller shaft to accommodate bearings, gears, or other components if necessary. This step is done using drilling machines or CNC equipment.
- Product Details
- {{item.text}}
Quick Details
-
Torque Capacity:
-
Customer-Making
-
Model Number:
-
NON-STANDARD, According to drawing
-
Place of Origin:
-
Henan, China
-
Brand Name:
-
YOGIE
-
Name:
-
steel rolling mill transmission propeller pto drive shaft
-
Process:
-
Lathing, milling,grinding,drilling
-
Standard:
-
ISO,DIN,JIS
-
Packaging Details:
-
Package adapting to transport
-
Delivery Time:
-
15-30 days
-
Certification:
-
ISO9001
-
Size:
-
Clients Drawings
-
Tolerance:
-
0.05mm
Quick Details
-
Weight (KG):
-
20000
-
Core Components:
-
shaft
-
Material:
-
Steel, 42CrMo, 40Cr , C45, Alloy steel
-
Torque Capacity:
-
Customer-Making
-
Model Number:
-
NON-STANDARD, According to drawing
-
Place of Origin:
-
Henan, China
-
Brand Name:
-
YOGIE
-
Name:
-
steel rolling mill transmission propeller pto drive shaft
-
Process:
-
Lathing, milling,grinding,drilling
-
Standard:
-
ISO,DIN,JIS
-
Packaging Details:
-
Package adapting to transport
-
Delivery Time:
-
15-30 days
-
Certification:
-
ISO9001
-
Size:
-
Clients Drawings
-
Tolerance:
-
0.05mm
Why Choose Us
Product Description
long mild steel rolling mill transmission propeller pto drive shaft
The drive shaft and the passive shaft shall be a pair of directly adjacent shafts connected by transmission pairs (gears, pulleys, sprockets, etc.). driving shaft is closer to the power source .on the contrary, the passive shaft is similar to the working shaft, it is mainly used in lathes, milling machines, fans, conveyors, injection molding machines, processing centers, steam turbines, drilling machines, hydraulic turbines, machinery industry, etc.
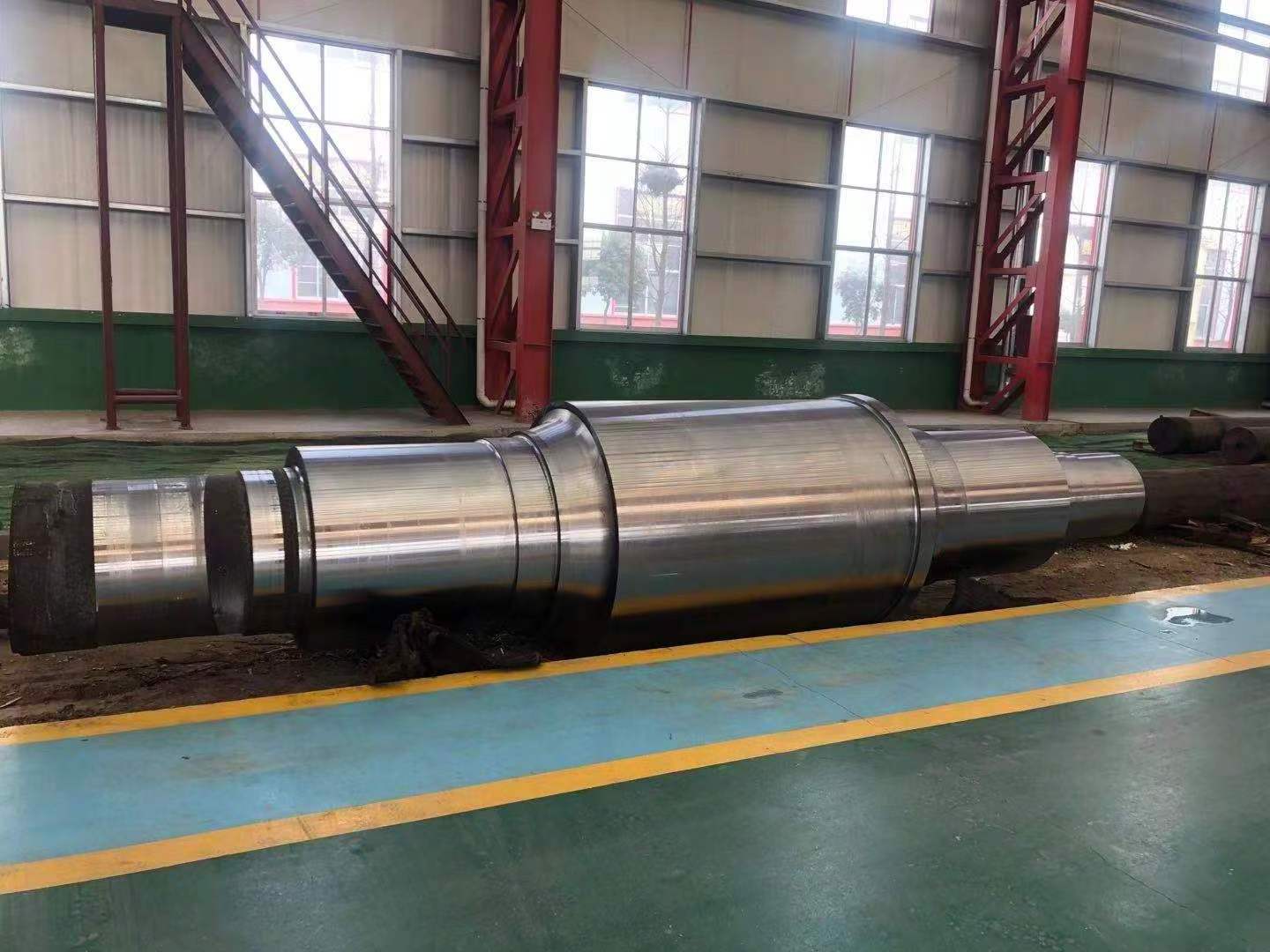
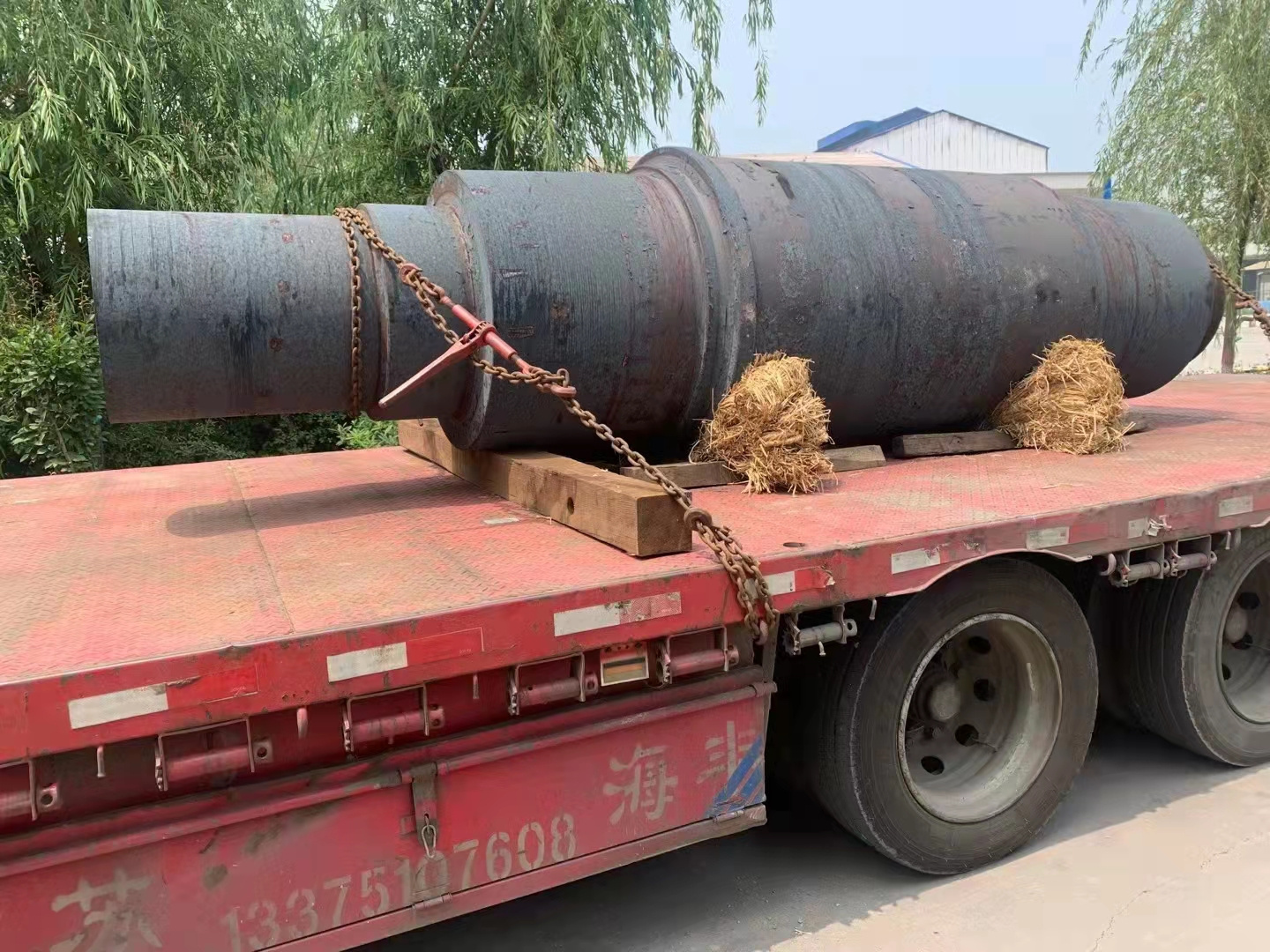
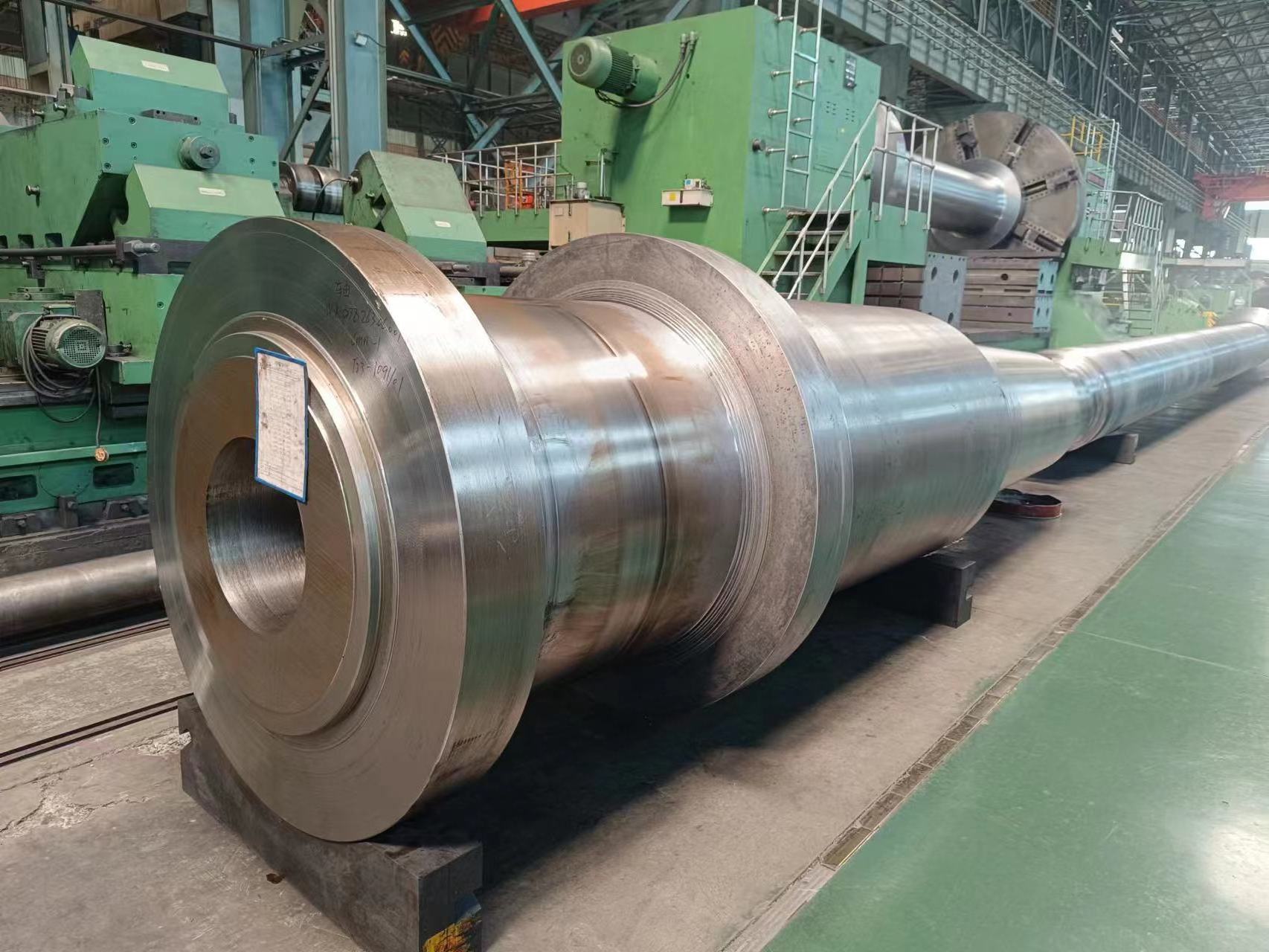
Product name
|
custom forged steel hot rolling mill support back up roller
|
Material
|
Alloy steel
|
Structure
|
Forging
|
Process
|
Lathing, milling,grinding,drilling
|
Heat treatment
|
Quenched and Tempered Hardness: 170-217HBS
|
Diam eter of Forged
Mill Roller Shaft
|
According to drawing
|
Weight
|
Max 55T
|
Torque Capacity
|
According to drawings
|
Chemical Control
|
Spectrograph
|
Defect Control
|
UT,MT
|
Standard
|
ISO
|
Model Number
|
According to drawing
|
Packaging Details
|
Package adapting to ocean transport
|
Delivery Time
|
30-90 days
|
Certificate
|
ISO9001-2008
|
Technological Process
Large shaft processing
Shaft Packing
1. Grinding: Use grinding machines to achieve precise surface finishes and ensure the roller shaft's dimensional accuracy.
2. Heat Treatment: Apply heat treatment techniques such as annealing, quenching, or tempering to enhance the mechanical properties of the roller shaft
3. Surface Treatment: Apply surface coatings or treatments
4. Inspection: Conduct thorough inspections to check the quality and dimensional accuracy of the roller shaft.
2. Heat Treatment: Apply heat treatment techniques such as annealing, quenching, or tempering to enhance the mechanical properties of the roller shaft
3. Surface Treatment: Apply surface coatings or treatments
4. Inspection: Conduct thorough inspections to check the quality and dimensional accuracy of the roller shaft.
About us
Quality Control
Our Equipment
Customer Comments
Customer Visit
Certifications
Exhibition
Contact Us
Hot Searches