XPS extruded polystyrene board has significant advantages in the construction and engineering fields. Firstly, it boasts excellent insulation and compression resistance properties, effectively insulating heat and bearing heavy loads, thus improving building energy efficiency and structural stability. Secondly, XPS board demonstrates good moisture resistance and corrosion resistance, maintaining excellent performance over the long term without being affected by moisture or chemicals, thereby extending its service life. Additionally, it is lightweight, easy to process, and convenient for construction, reducing project costs and enhancing construction efficiency. With the construction industry's continuous pursuit of energy conservation and environmental protection, XPS extruded polystyrene board, as a high-quality insulation material, has vast application prospects and enormous
development potential in the future.
Explore More Products
- Product Details
- {{item.text}}
Quick Details
-
Screw Speed (rpm):
-
260 rpm
-
Place of Origin:
-
Shandong, China
-
Brand Name:
-
DE MENG
-
Voltage:
-
380v
-
Dimension(L*W*H):
-
100m*15m*8m
-
Power (kW):
-
500
-
Weight:
-
45000 KG
-
Raw material:
-
xps
-
Name:
-
Extrusion Machine
-
After-sales Service Provided:
-
Service Machinery Overseas
-
Marketing Type:
-
Hot Product 2024
-
Usage:
-
Plastic Extrusion
-
Keywords:
-
Foam Machiney
-
Final product:
-
XPS Foam Board
-
Processing Type:
-
Extrusion Process
-
Product Type:
-
Flat
-
Product name:
-
XPS Production Line
Quick Details
-
Screw Design:
-
Double-screw
-
Screw L/D Ratio:
-
40:1
-
Screw diameter (mm):
-
95
-
Screw Speed (rpm):
-
260 rpm
-
Place of Origin:
-
Shandong, China
-
Brand Name:
-
DE MENG
-
Voltage:
-
380v
-
Dimension(L*W*H):
-
100m*15m*8m
-
Power (kW):
-
500
-
Weight:
-
45000 KG
-
Raw material:
-
xps
-
Name:
-
Extrusion Machine
-
After-sales Service Provided:
-
Service Machinery Overseas
-
Marketing Type:
-
Hot Product 2024
-
Usage:
-
Plastic Extrusion
-
Keywords:
-
Foam Machiney
-
Final product:
-
XPS Foam Board
-
Processing Type:
-
Extrusion Process
-
Product Type:
-
Flat
-
Product name:
-
XPS Production Line
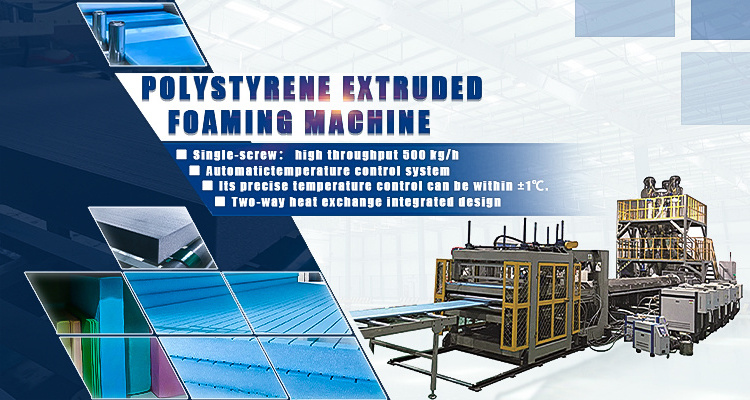
xps insulation board production line
In accordance with CO2 foaming process environment, we design and develop single-screw secondary extruder with 2-way and igh cooling efficiency. Single-screw design has good effect on large cooling area coverage. Its process multi-stage kneading low shear heating, melting temperature homogenizer, low-speed but high throughput 500 kg/h speed only 3.6 rpm. Automatic temperature control system with multiple points on integrated design of 2-ways heat exchange and with a special design of the secondary efficient cooling extruder screw, it is able to regional peer-to-peer rapid cooling heat exchange. According to the set process parameters PID self-tuning adjustment, its precise temperature control can be within±1℃
Product Applacation
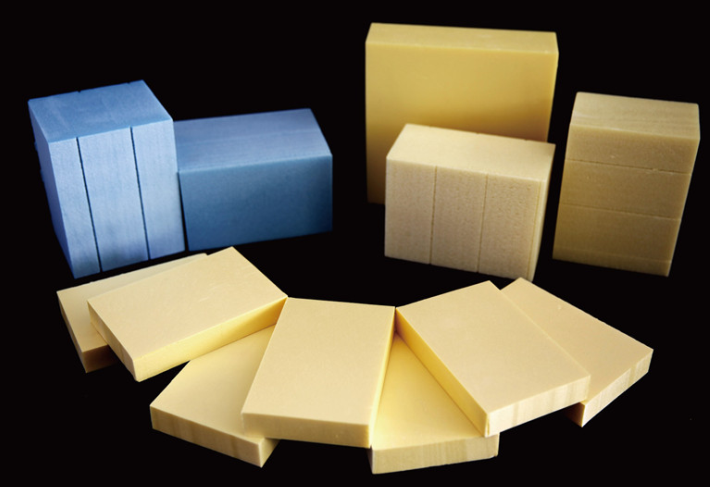
XPS extruded polystyrene board
Machine model
Model
|
Unit
|
XPS-75/200
|
|
XPS-85/250
|
|
XPS-95/300
|
|
|||||
Screw diameter
|
mm
|
Φp75/200
|
|
Φp85/250
|
|
Φp95/300
|
|
|||||
Heating power
|
kw
|
70
|
72
|
80
|
88
|
90
|
100
|
|||||
Driving motor power
|
kw
|
132
|
90
|
200
|
110
|
280
|
132
|
|||||
Thickness of board
|
mm
|
20-120
|
|
20-130
|
|
40-140
|
|
|||||
Width of board
|
mm
|
600 1200
|
|
600 900 1200
|
|
600 900 1200
|
|
|||||
Length of board
|
mm
|
1200 1250 2450 2500
|
|
|
|
|
|
|||||
Capacity
|
kg/h
|
550-600
|
|
750-800
|
|
850-1200
|
|
|||||
Total power
|
kw
|
520
|
|
620
|
|
720
|
|
|||||
Oversize(L*W*H)
|
m
|
60*10*5
|
|
62*11*5
|
|
64*12*5
|
|
|||||
Total weight
|
T
|
35
|
|
38
|
|
40
|
|
Machine introduction
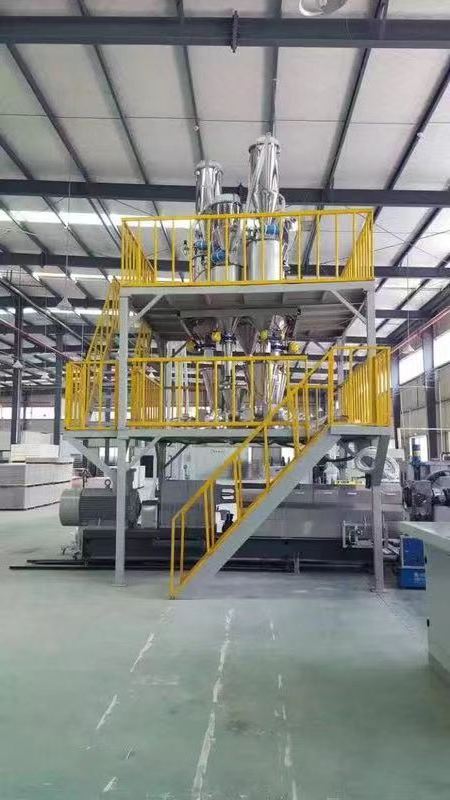
The five groups of automatic weight feeding system
1、Adopt multi component dynamic automatic continuous measurement, vacuum automatic feeding.
2、High accuracy can achieve 0.5% of the dynamic accuracy, stable state of up to 0.2%.
3、The average of each component power consumption is only 0.2KW/h.
4、Meter can handle the material from the state can be divided into pellets, powder
2、High accuracy can achieve 0.5% of the dynamic accuracy, stable state of up to 0.2%.
3、The average of each component power consumption is only 0.2KW/h.
4、Meter can handle the material from the state can be divided into pellets, powder
75 parallel and same direction twin screw extruder
1、Screw body processing by the horizontal machining center one-piece complete, to ensure the installation accuracy.
2、Screw design according to the required amount of CO2 foaming process tailored, adopt high carbon high alloy ledebrite
3、With a stainless steel protective cover with radiating holes, to prevent accidental contact scald.
4、High pressure four position leak proof high pressure switch
2、Screw design according to the required amount of CO2 foaming process tailored, adopt high carbon high alloy ledebrite
3、With a stainless steel protective cover with radiating holes, to prevent accidental contact scald.
4、High pressure four position leak proof high pressure switch
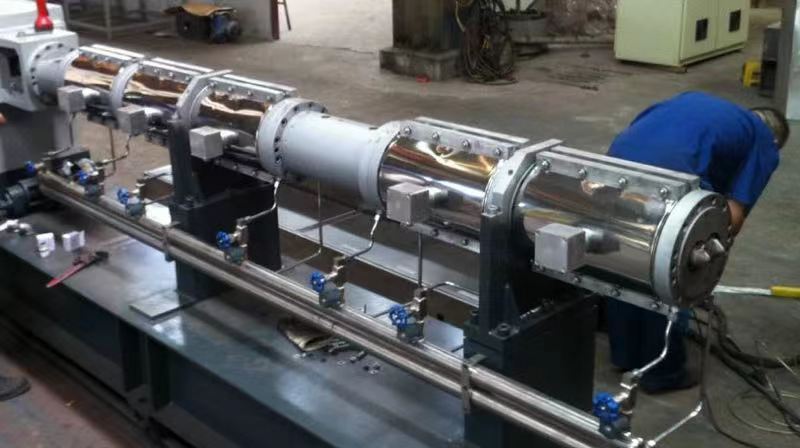
Horizontal cutting machine
1、Horizontal cutting knife, double knife double cut design.
2、Horizontal mobile motor with 1.5 *2 KW.
3、Longitudinal movement of the track drive.
4、The cutting length is controlled by a photoelectric or contact type switch.
5、Vacuum cleaner port PLC programming control
2、Horizontal mobile motor with 1.5 *2 KW.
3、Longitudinal movement of the track drive.
4、The cutting length is controlled by a photoelectric or contact type switch.
5、Vacuum cleaner port PLC programming control
CO2 foaming agent automatic injection system
1、High pressure and low temperature metering pump station
2、Mass flow calculation system
3、Automatic cycle constant liquefaction device
4、Liquid static mixing device
5、Stainless steel high pressure anti-corrosion connection, pipe fittings
6、Computer control system
7、Low temperature transport system
8、Buffer high-pressure and low temperature tank (with CO2/ethanol)
2、Mass flow calculation system
3、Automatic cycle constant liquefaction device
4、Liquid static mixing device
5、Stainless steel high pressure anti-corrosion connection, pipe fittings
6、Computer control system
7、Low temperature transport system
8、Buffer high-pressure and low temperature tank (with CO2/ethanol)
stacking unit
1、Stack size: 1200-2400mm*600mm*900mm
2、Lift motor power: 3kw
3、Transmission motor power: 0.37kw
4、Speed control mode: frequency conversion speed
2、Lift motor power: 3kw
3、Transmission motor power: 0.37kw
4、Speed control mode: frequency conversion speed
Mold temperature cotroller
The heat conduction medium with high heat conduction is used to control the temperature rise of the die in a very short time.
After setting the heat balance temperature, the mold temperature can automatically control its temperature within the minimum
error and maintain the fixed value.
After setting the heat balance temperature, the mold temperature can automatically control its temperature within the minimum
error and maintain the fixed value.
Details Images
Machine Advantages
Recommended Product
FAQ
Q: What is the production capacity of XPS extrusion panel production line?
A: The production capacity of the XPS extrusion board line varies by model and configuration, usually ranging from 500 to 1000kg/h.
Q: What are the main components of XPS extrusion board production line?
A: The main components of XPS extrusion board production line include raw material mixing system, extruder, mold, cooling system, cutting machine and conveying system.
Q: What is the control system of XPS extrusion board production line?
A: XPS extrusion board production line is equipped with advanced PLC control system, with touch screen interface, to achieve automatic control and parameter adjustment, improve production efficiency and quality stability.
Q: What are the main uses of XPS extrusion panel production line?
A: XPS extrusion board production line is used to produce various specifications and thickness of extrusion polystyrene board, widely used in building insulation, floor insulation, refrigerator materials and other fields.
Q: Do you provide installation and commissioning services for XPS extrusion panel production line?
A: Yes, we provide a full range of installation, commissioning and training services for the XPS extrusion board production line to ensure that the equipment is put into operation smoothly and meets customer needs.
Q: What is the after-sales service of XPS extrusion board production line?
A: We provide all-weather after-sales service support, including remote technical support, spare parts supply, regular maintenance, etc., to ensure the stable operation of customer equipment and smooth production.
Q: What type of screw is used in the extruder of XPS extrusion board production line?
A: The extruders in the XPS extrusion line usually use specially designed efficient twin screws to ensure uniform extrusion of raw materials and excellent extrusion performance.
Q: How does the cooling system of the XPS extrusion board production line ensure uniform cooling of the board?
A: The cooling system of the XPS extruded sheet production line uses advanced water circulation cooling technology to ensure that the sheet is cooled evenly and quickly during the production process.
Q: Can the mold of XPS extrusion board production line be customized?
A: Yes, we can customize molds of various specifications and thicknesses according to customers' requirements to meet the production needs of different customers.
Q: What is the energy consumption of XPS extrusion panel production line?
A: XPS extrusion board production line adopts advanced energy-saving technology and efficient equipment design, low energy consumption, while having high production efficiency and stability, saving energy and costs for customers.
Q: How long is the equipment life of XPS extrusion board production line?
A: The equipment life of XPS extrusion board production line depends on the manufacturing quality of the equipment, the use of the environment and maintenance and other factors, usually can reach more than 10 years. We provide a full range of after-sales services and regular maintenance to extend the service life of equipment and ensure stable production.
Hot Searches