- Product Details
- {{item.text}}
Quick Details
-
Power:
-
420KW-3000KW
-
Dimension(L*W*H):
-
Customizable
-
Weight:
-
100000 kg
-
Product Name:
-
Cement Manufacturing Process
-
Color:
-
Customers' Requirements
-
Application:
-
Cement Clinker, Limestone
-
After Sale Service:
-
Engineer Overseas Service
-
Motor:
-
Chinese Brand
-
Factory:
-
50,000 Square Meters Closed Workshops
-
Installation and Trial:
-
We Can Send Engineer for Guidance
-
Fuel:
-
Coal, Mazut, Gas etc.
-
Certification:
-
ISO9001 CE, ISO9001:14000
-
Advantage:
-
Timely Delivery and Installation, Fast Technical Support
Quick Details
-
Place of Origin:
-
Henan, China
-
Brand Name:
-
ZOOMJO
-
Voltage:
-
220v, 380v, 440v
-
Power:
-
420KW-3000KW
-
Dimension(L*W*H):
-
Customizable
-
Weight:
-
100000 kg
-
Product Name:
-
Cement Manufacturing Process
-
Color:
-
Customers' Requirements
-
Application:
-
Cement Clinker, Limestone
-
After Sale Service:
-
Engineer Overseas Service
-
Motor:
-
Chinese Brand
-
Factory:
-
50,000 Square Meters Closed Workshops
-
Installation and Trial:
-
We Can Send Engineer for Guidance
-
Fuel:
-
Coal, Mazut, Gas etc.
-
Certification:
-
ISO9001 CE, ISO9001:14000
-
Advantage:
-
Timely Delivery and Installation, Fast Technical Support
Product Description
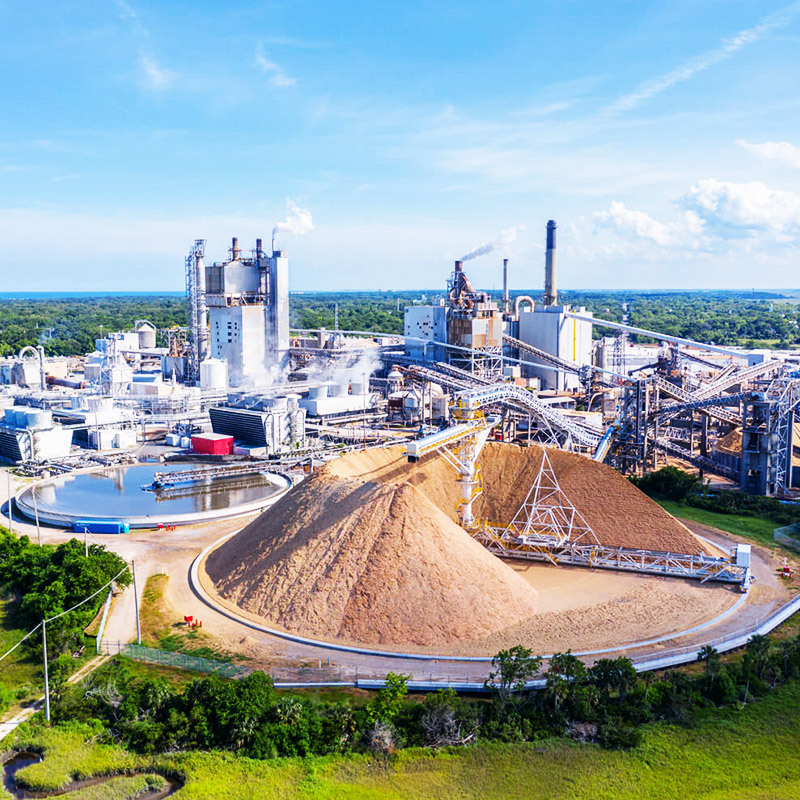
Cement is an important and indispensable material for modern building and infrastructure construction. The cement production line is the key process for transforming raw materials into cement products.
Cement production line usually includes the following main stages:
a. Raw material collection and processing:
The main raw materials for cement are limestone, clay and gypsum. First, miners collect limestone and clay from the mines and use blasting or drilling to obtain large pieces of ore. These raw materials are then transported to the production plant and fed into a crusher for initial crushing. Next, the raw materials enter a preheater, where they are preheated at high temperatures to minimize fuel consumption and promote chemical reactions.
b. Clinker production:
The preheated raw material enters the rotary kiln, which is one of the most important pieces of equipment in a cement production line. The rotary kiln is a long, sloping rotating cylinder with an internal temperature of up to about 1400°C. The kiln is designed to produce clinker at a temperature of about 1,000°C. In the rotary kiln, the raw material undergoes a series of complex chemical reactions and is converted into clinker, the main components of which are slaked lime, silica, alumina and iron oxide. This process is called clinker firing.
c. Cement Grinding:
After clinker is discharged from the rotary kiln, it needs to be processed by cement grinding. The clinker is mixed in the cement grinder along with an appropriate amount of gypsum, the addition of which regulates the setting time of the cement, and then the mixture is ground into a cement powder of suitable fineness. The cement grinding process is an energy consuming process, but its fineness control directly affects the performance of cement.
d. Cement packaging and shipment:
After grinding, the cement is transported to the storage silo and then packed or bulked by automatic packing machine or bulk device.
The specific cement production line equipment composition may vary depending on factors such as production scale, process flow, raw material type and technology level.
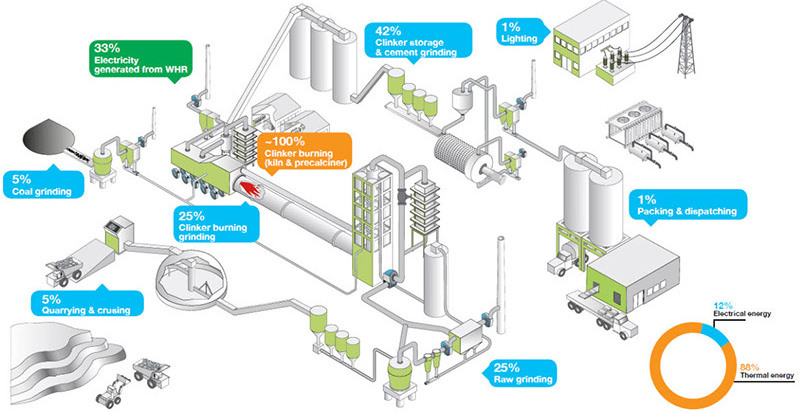
These are two different processes of manufacturing cement. wet process minerals are wet ground (by adding water) to form a slurry and then dried, dry process minerals are dry ground to form a powder like substance.Both the processes are in use and have their own advantages and disadvantages.While in wet process grinding is easier,in dry process there is a saving in fuel costs involved in drying up the slurry.
Cement by Dry Process Features
1. Mixing of raw material in dry state in blenders.
2. The dry materials exiting the mill are called “kiln feed”.
3. Size of the kiln needed for manufacturing of cement is smaller.
4. Difficult to control mixing of Raw materials, so it is difficult to obtain a better homogeneous material.
5. Fuel consumption is low i.e., 100 kg of coal per tonne of cement produced.
6. Cost of production is less.
7. Capital cost is high due to blenders.
1. Mixing of raw material in dry state in blenders.
2. The dry materials exiting the mill are called “kiln feed”.
3. Size of the kiln needed for manufacturing of cement is smaller.
4. Difficult to control mixing of Raw materials, so it is difficult to obtain a better homogeneous material.
5. Fuel consumption is low i.e., 100 kg of coal per tonne of cement produced.
6. Cost of production is less.
7. Capital cost is high due to blenders.
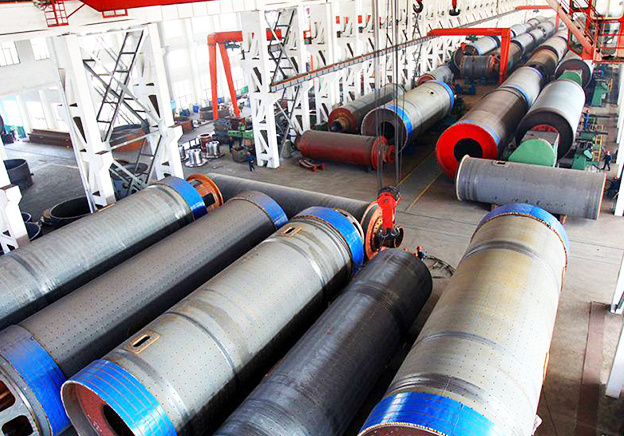
In dry process all the materials in powder form are ground separated in the absence of water and then mixed in the desired proportion and the resultant product is fed into kiln for burning. This process results less consumption of energy. And low quality of product is achieved in this method. while, In wet process, The raw materials(clay silica alumina) is purified by washing with water and then mixed with crushed limestone to get raw slurry liquid which is then fed to kiln for burning. Energy comsumption is high in this process. Produce good quality product. Dust emission is low.
Working Flow
Which process is better?
If we consider the quality and rate then wet process is better and if we consider fuel consumption and time of process then dry process is better. Difference between dry and wet process in table form:
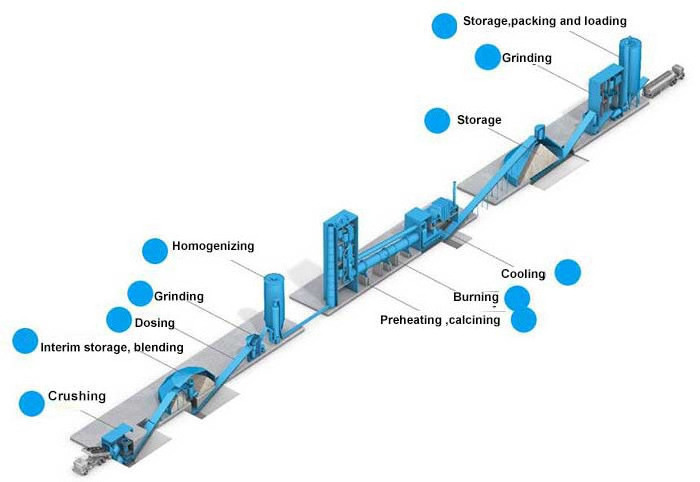
Dry Process
|
Wet Process
|
1. Mixing of raw material in dry state in blenders.
|
1. Mixing of Raw materials in wash mill with 35 to 50% water.
|
2. The dry materials exiting the mill are called “kiln feed”.
|
2. Materials exiting the mill are called “slurry” and have flowability characteristics.
|
3. Fuel consumption is low i.e., 100 kg of coal per tonne of cement produced
|
3. Fuel consumption is high i.e., 350 kg of coal per tonne of cement produced
|
4. Cost of production is less.
|
4. Cost of production is high
|
5. Capital cost is high due to blenders.
|
5. Capital cost (Cost of establishment) is comparatively less
|
6. Size of the kiln needed for manufacturing of cement is smaller.
|
6. Size of the kiln needed for manufacturing of cement is bigger.
|
7. Difficult to control mixing of Raw materials, so it is difficult to obtain a better homogeneous material.
|
7. Raw material can be mixed easily, so a better homogeneous material can be obtained
|
Main Equipment
Cement m
aking machinery
mainly includes crushing equipment, grinding equipment, calcination equipment, dust removal equipment, packaging equipment and preheater, coal mill, cooler, steel silo.
1. Crushing & Proportioning
Primary crushing involves limestone rock fed through large capacity crushers. This reduces the rock to a maximum size of approximately 150 mm. Secondary crushing further reduces this to 75mm or under. Residule material is stacked and reclaimed with a bridge reclaimer in a cross section so that the homogeneous limestone is fed further in the process. This averages the limestone quality.
Primary crushing involves limestone rock fed through large capacity crushers. This reduces the rock to a maximum size of approximately 150 mm. Secondary crushing further reduces this to 75mm or under. Residule material is stacked and reclaimed with a bridge reclaimer in a cross section so that the homogeneous limestone is fed further in the process. This averages the limestone quality.
2. Raw milling & Blending
Crushed particles are ground to 90 microns or less in a closed circuit ball mill with high efficiency separator. The raw meal is transferred to continuous blending silos (CFC) for homogenization ,extracted by load cell hopper for feeding to the kiln preheaters.
Crushed particles are ground to 90 microns or less in a closed circuit ball mill with high efficiency separator. The raw meal is transferred to continuous blending silos (CFC) for homogenization ,extracted by load cell hopper for feeding to the kiln preheaters.
3. Pyro processing
Raw material is heated to over 1,450 °C in a pre-heater tower,then through a pre-calciner and finally to the rotary kiln.
Raw material is heated to over 1,450 °C in a pre-heater tower,then through a pre-calciner and finally to the rotary kiln.
4. Burning
As the material progresses through the kiln, certain elements areremoved in the form of gases. The remaining elements unite to form a new substance (clinker) with new physical and chemical characteristics. Clinker is formed in small marble sized pieces
As the material progresses through the kiln, certain elements areremoved in the form of gases. The remaining elements unite to form a new substance (clinker) with new physical and chemical characteristics. Clinker is formed in small marble sized pieces
5. Cooling,
Milling, Storage & Packing
Clinker is discharged from the kiln and the temperature is reduced in grate coolers. The hot air from the coolers is redirected back to the kiln, this saves fuel and increases burning efficiency.
Portland cement, the basic ingredient of concrete, is a combination of calcium, silicon, aluminum, iron and small amounts of other ingredients to which gypsum is added in the final grinding process to regulate the setting time of the concrete.
Our Advantages
Since the establishment of the company in 1949, it has developed into a large-scale enterprise integrating scientific research, production and sales. Our factory can produce cement production line equipment with various outputs, ensuring quality, timely delivery, and timely and efficient after-sales service.
Our senior technical engineers can provide solutions to the problems you encounter through online or quickly arrive at your production site at any time, and our experienced installation team can quickly and efficiently build and install your cement line factory, allowing you Produce cement products that meet the requirements in the shortest time, allowing you to see benefits in the shortest time.
Packing & Delivery
Customer Cases
500TPD Cement Production Line in
Philippines
1000TPD Cement Production Line in
Peru
2000TPD Cement Production Line in Oman
800TPD
Cement Production Line
in
Uzbekistan
Hot Searches