- Product Details
- {{item.text}}
Quick Details
-
Power:
-
Customer's Requirement
-
Dimension(L*W*H):
-
Customer's Requirement
-
After-sales Service Provided:
-
Engineers available to service machinery overseas
-
Spraying area:
-
6 m2/h
-
Sand blasting room:
-
for Large castings
-
Size of jobs:
-
Customer's Requirement
-
Spray gun quatity:
-
2
-
Spray nozzle caliber:
-
Diameter 6mm
-
Compressed air consumption:
-
Customer's Requirement
-
Sand consumption:
-
Customer's Requirement
-
Certification:
-
CE
Quick Details
-
Place of Origin:
-
Shandong, China
-
Brand Name:
-
ATHI
-
Weight (KG):
-
4000 KG
-
Power:
-
Customer's Requirement
-
Dimension(L*W*H):
-
Customer's Requirement
-
After-sales Service Provided:
-
Engineers available to service machinery overseas
-
Spraying area:
-
6 m2/h
-
Sand blasting room:
-
for Large castings
-
Size of jobs:
-
Customer's Requirement
-
Spray gun quatity:
-
2
-
Spray nozzle caliber:
-
Diameter 6mm
-
Compressed air consumption:
-
Customer's Requirement
-
Sand consumption:
-
Customer's Requirement
-
Certification:
-
CE
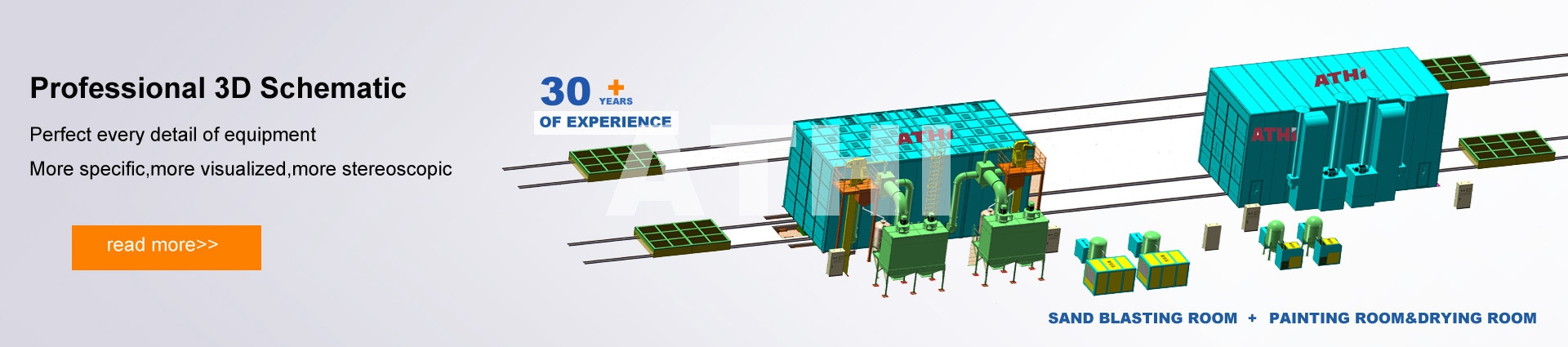
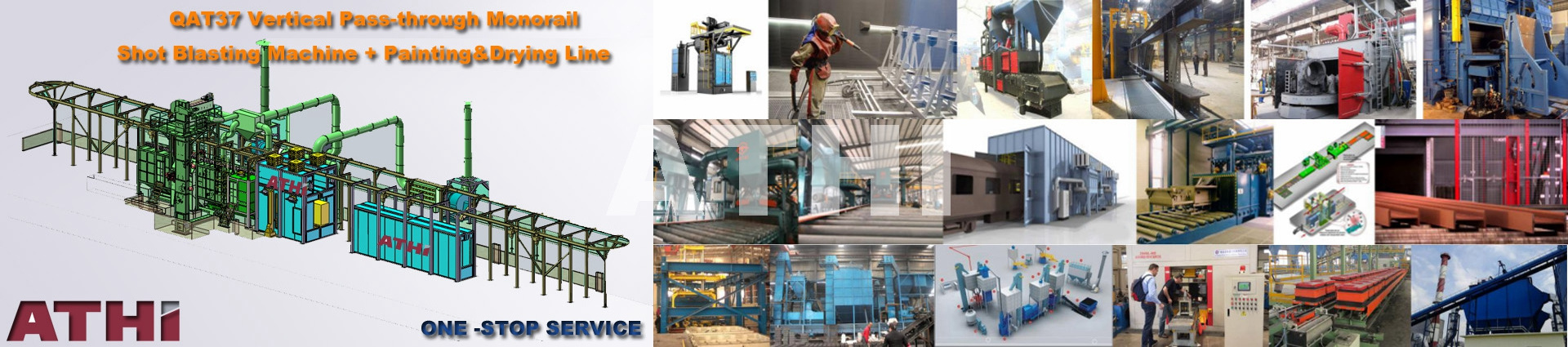
Sand blasting chamber:
This machine is a special reciprocating sand blasting machine, which consists of shot-p
eening chamber, shot-peening device, Screw Conveyor, elevator, separator, Shot distributing system, flat car system, flat car guide and support, lighting system, the bottom funnel, grid plate, dust- removing system, electric control system and so on.
This abrasive material reclaim system requires extremely reduced foundations, and can optionally be built without the need of foundations, or still on container type mobile rooms.
Optionally, ANTAI can supply room kits with the components that are necessary for the client, such as, for example, and automatic or semi-automatic abrasive material reclaim system, exhaust systems, etc., which will always fully meet the safety and environmental standards.
1) Doors:
The service door is built in welded profiles and has a closing in steel plates, and is internally coated with abrasion resistant rubber. An exclusive sealing system prevents the loss of abrasive materials and makes the closing of the doors possible, without effort. Optionally, two doors can be supplied (tunnel type room) and one door for the operator. Sensors connected to the doors automatically interrupt the blasti
ng operation when one of them is opened.
2) Luminaries:
Each LED lamps construction and positioning enable maximum utilization of the luminosity. The fastening system allows easy removal, for maintenance.
3) Working chambers:
Built in color steel tile, they are modulated in order to satisfy any dimension in height, width and length. Inside (except on the ceiling) there is a rubber coating that protects them against abrasion and helps in the acoustic insulation.
4) Horizontal transportation of abrasive material:
This system combines the drive of scraper carts that conduct the abrasive material to the center of the working chamber, where it is collected by a screw conveyor (in some cases by a belt conveyor) which conducts the abrasive material up to the foot of the bucket elevator (abrasive materials purifier). On the whole floor surface, there is a grid that is covered with a perforated plate, which retains larger impurities or even small parts which may drop accidentally on the floor. This unique system used by CMV requires a much smaller installed power that the other systems, thanks to the friction coefficient (wear), which is much smaller in this system.
5) Control panel:
Mounted on a shielded cabinet, it has thermal protection and interlocking for the motors, which makes it impossible to connect them in the incorrect order. Optionally, it is supplied with a PLC for the automatic control of the equipment. It meets the most important international standards, among which the 60204-1 of the EEC.
6) Blasting machine:
It has a pressure vessel built in accordance with the EU standard, which is hydrostatically tested to operate at a pressure of 8 Bar (116PSI), with and outlet for one or more operators, with a remote pneumatic command and a full kit for the protection of the operator(s), and an air filter that is appropriate for human breathing. The machine also has a high-efficiency pneumatic system and high-performance nozzle(s). Optionally, it can be equipped with a level sensor for automatic feeding of abrasive material.
7) Abrasive materials purifier / Bucket elevator:
The bucket elevator receives the abrasive in its hopper and lifts it to the purifier. The elevator features buckets in nodular cast iron that are highly resistant to abrasion and is driven by one gear motor. The abrasive materials purifier receives the abrasive material from the bucket elevator and, with a system that is adjustable through counterweights, forms a curtain with the abrasive material, through which an air stream passes, which is also adjustable, and which takes the dust and other residues that may be contaminating the abrasive material, to the exhaust system. The abrasive material, now free from impurities, drops into the silo that is located on the blasting machine. Optionally, the abrasive materials purifier can be supplied with a revolving screen.
8) Exhaust system:
The combination of deflectors for air intake / outlet ensures an excellent operational visibility, and, due to their construction, eliminates the waste of abrasive material. Our model BMF-H dust collectors have cartridge filters with elements in Viledon(r), which, besides ensuring an extremely low volume of residual dust (approximately 2mg/m3), have a considerably long useful life (approximately 15,000 h of work). The cleaning of the filter system is done automatically by an electronically controlled pulse-jet system. Optionally, among other items, it is possible to supply the equipment with a noise damper / rear HEPA type filter, thus obtaining a volume of residual dust of about
Model Size of room (mm) Size of jobs (mm) Spray gun quantity
Model
|
Size of room (mm)
|
Size of jobs (mm)
|
Spray gun quantity
|
ATSR665
|
6000×6000×5000
|
3000×3000×2500
|
2
|
ATSR666
|
6000×6000×6000
|
3000×3000×3500
|
2
|
ATSR865
|
8000×6000×5000
|
5000×3000×2500
|
2
|
ATSR866
|
8000×6000×6000
|
5000×3000×3500
|
2
|
ATSR1066
|
10000×6000×6000
|
7000×3000×3500
|
2
|
ATSR1566
|
15000×6000×6000
|
12000×3000×3500
|
2
|
ATSR1586
|
15000×8000×6000
|
12000×5000×3500
|
2
|
ATSR1886
|
18000×8000×6000
|
15000×5000×3500
|
4
|
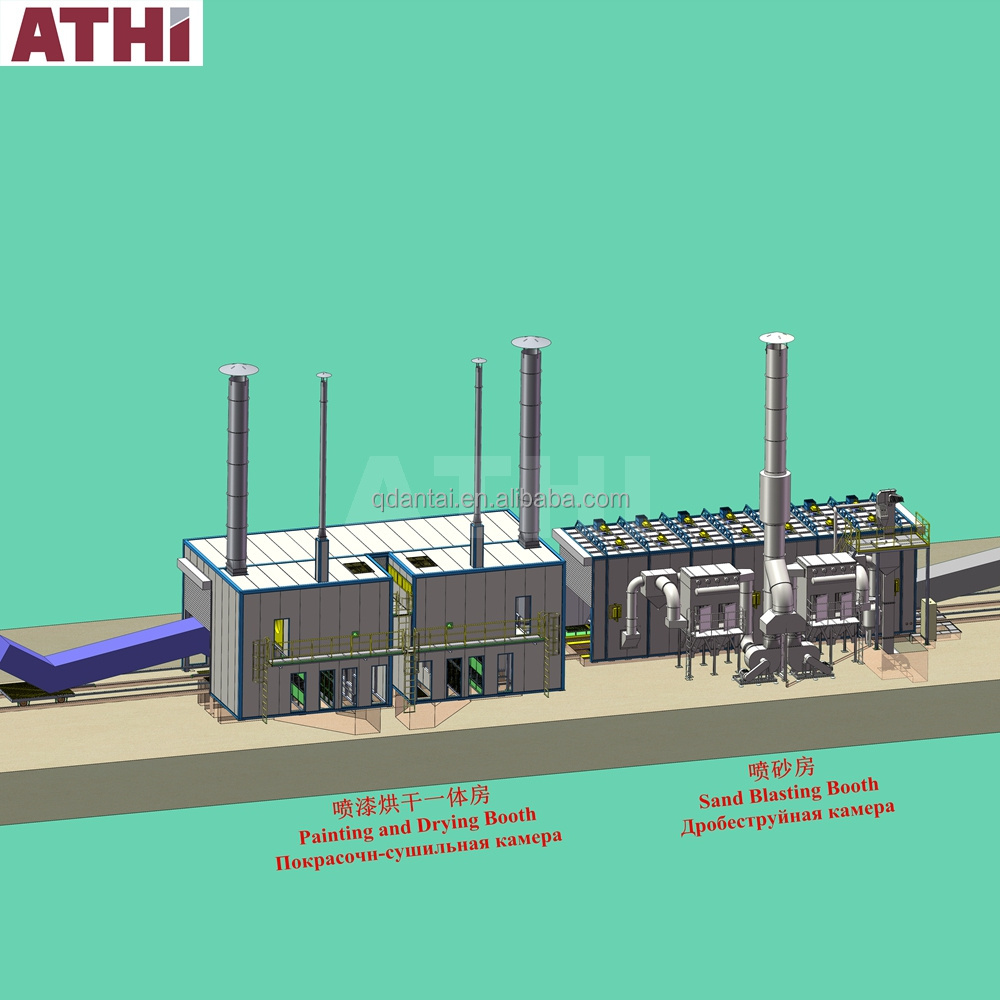
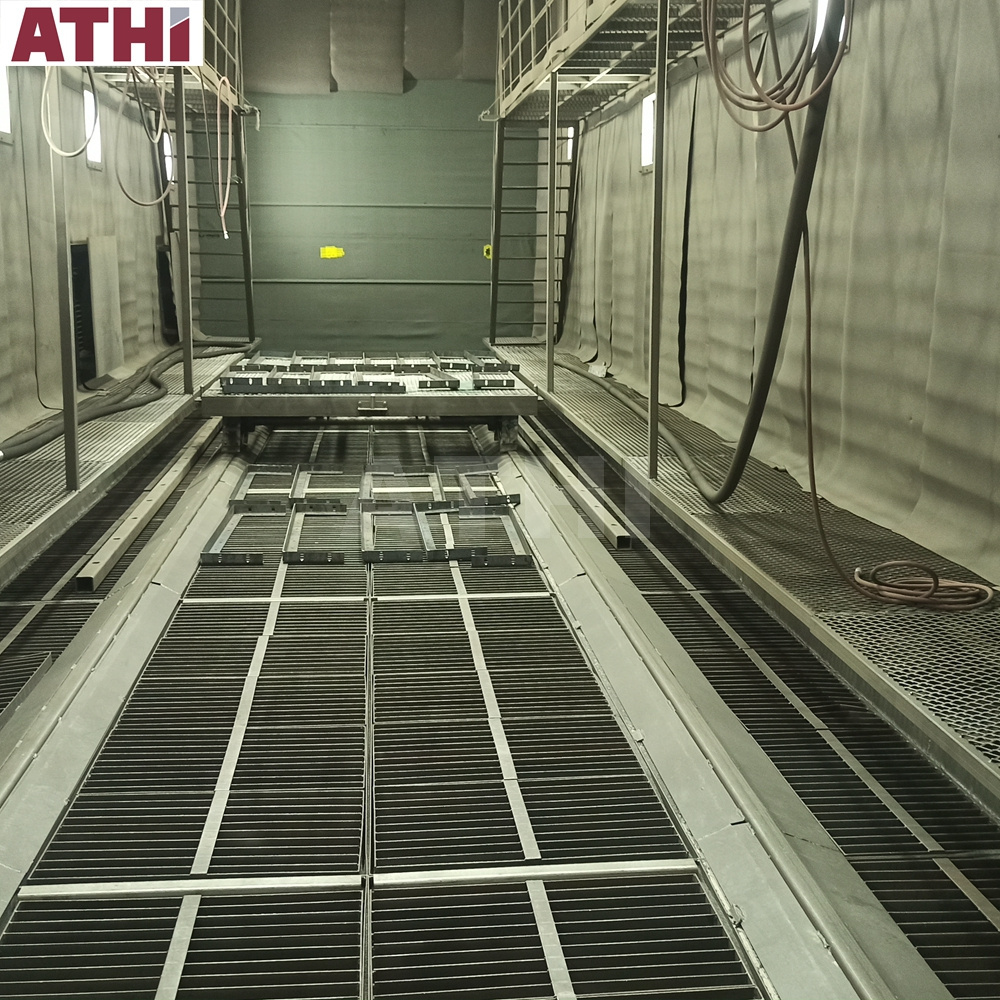