Perfectly suited for accepting and dispersing mica powder pigments, liquid pigments and alcohol inks and dyes! Liquid Glass is the
ideal epoxy for evenly distributing color and suspending inks and powders. *Paint, acrylic paint and oil based paint are not
recommended to use with epoxy, and can have negative results.
- Product Details
- {{item.text}}
Quick Details
-
EINECS No.:
-
230-391-5
-
Place of Origin:
-
Guangdong, China
-
Brand Name:
-
JHX
-
Model Number:
-
JHX-318AB
-
Type:
-
silicone sealant
-
Shelf life:
-
12months
-
Feature:
-
Non VOC
-
Color:
-
Transparent
-
Material:
-
Epoxy Resin+hardener
-
Mixing Ratio:
-
A:B=3:1
-
Viscosity:
-
Resin 1600cps Hardener 100cps
Quick Details
-
CAS No.:
-
7085-85-0
-
Other Names:
-
Deep Pour Epoxy Resin
-
MF:
-
C15H16O2C2H7ONC3H5OCl
-
EINECS No.:
-
230-391-5
-
Place of Origin:
-
Guangdong, China
-
Brand Name:
-
JHX
-
Model Number:
-
JHX-318AB
-
Type:
-
silicone sealant
-
Shelf life:
-
12months
-
Feature:
-
Non VOC
-
Color:
-
Transparent
-
Material:
-
Epoxy Resin+hardener
-
Mixing Ratio:
-
A:B=3:1
-
Viscosity:
-
Resin 1600cps Hardener 100cps
Product Description
Crystal Clear Floral Epoxy Resin is Perfect for Large Castings, Thick table pours and gives simulated water appearance for floral decor.
This product is a 3:1 mix. It is 100% polyamine based epoxy system that is designed for high gloss crystal clear casting applications. This epoxy system will cure rigid with a blush free, shiny high gloss finish. This product was specifically developed for large castings - low viscosity (150cps.) bubble free - 0% shrinkage - minimal yellowing - low exotherm.
This resin can also be used for embedding as well as castings where typically micro-bubbles and heat are an issue. Cured specimens will be free of bubbles and have the optically clear appearance.
This epoxy system will cure rigid with a blush free, shiny high gloss finish. This product was specifically developed for large castings - 3" in depth. This has low viscosity (150cps.) and can do what other epoxies can't.
Approved applications:
Large castings (riverbed pours)
Jewelry making
Hobbyist and craft making
Floral arrangements
Fake water applications
Waterproofing & sealing
Advantages:
Bubble-free
Slow cure (72 hours @ room temp.)
Very low yellowing
Minimal exotherm
Low viscosity at 150cps (close to water)
Pot life of 240 minutes (150 grams)
Acid, chemical, & moisture resistant
Rigid, blush-free, high gloss finish
Hardness shore - durometer scale d-88
Heat resistant to 130c.
This is not a polyester
Tensile Strength - 8750
You will receive part A epoxy and part B curing agent (measured by weight), full instructions, and outstanding customer support with every purchase.
Unmatched Qualities of Liquid Glass Deep Pour Epoxy Resin
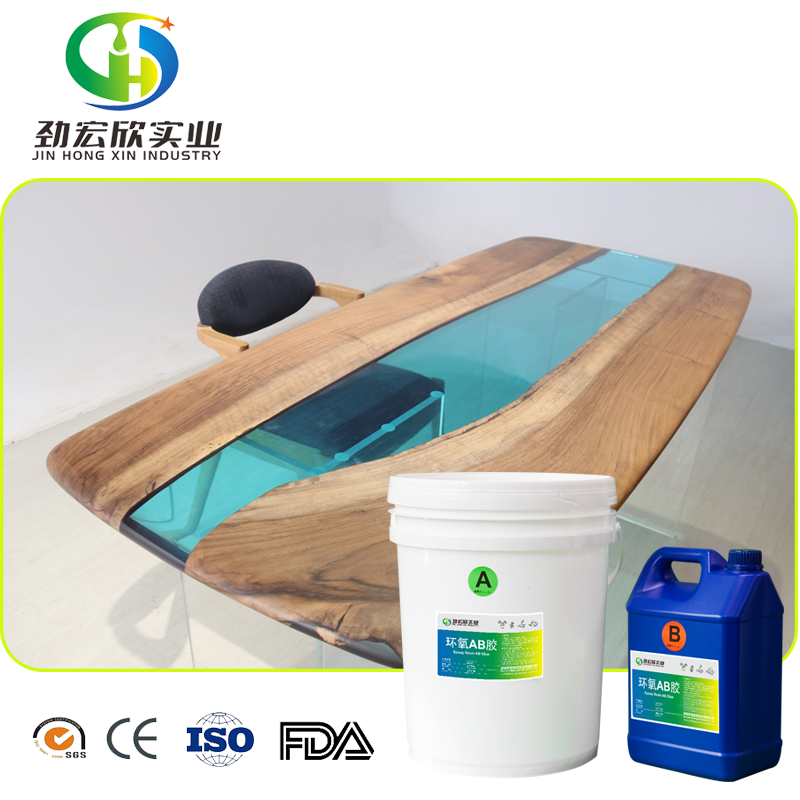
Deep Pour 2”- 4” Inches Plus!
Not only can you pour Liquid Glass Deep Pour Epoxy thicker at 2-4 inches and higher, but it is harder, to protect it from damage,
more heat resistant to prevent warping, and more stable, to provide a strong structure with no flexing.
These attributes are what differentiates Liquid Glass from the competition! You’ll find nothing more clear, harder or more
workable!
Not only can you pour Liquid Glass Deep Pour Epoxy thicker at 2-4 inches and higher, but it is harder, to protect it from damage,
more heat resistant to prevent warping, and more stable, to provide a strong structure with no flexing.
These attributes are what differentiates Liquid Glass from the competition! You’ll find nothing more clear, harder or more
workable!
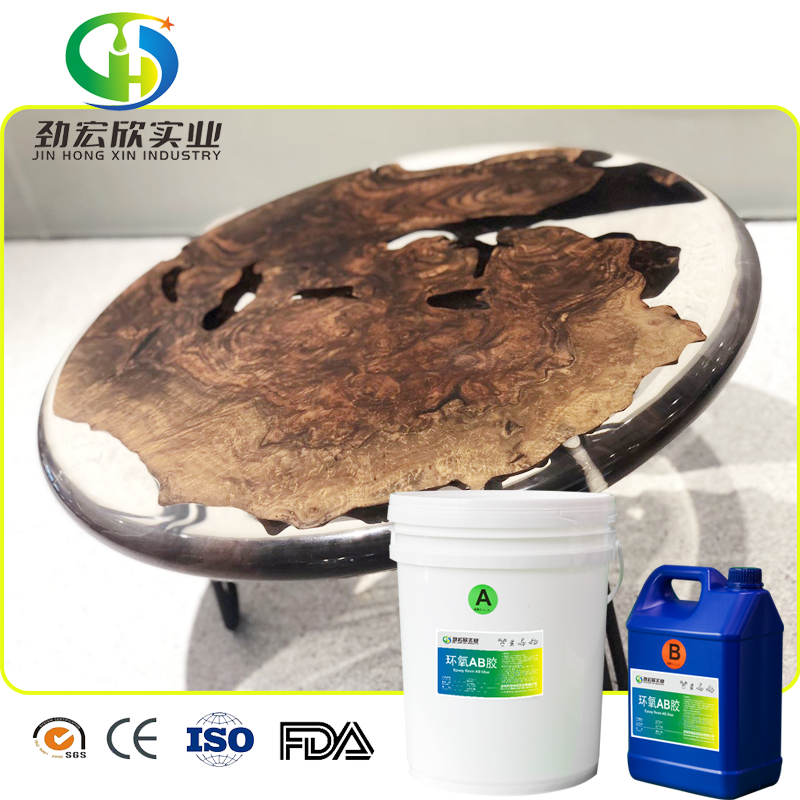
Practically Bubble-less Crystal Clear Finish
Our Liquid Glass Deep Pour Epoxy resin kit is a two part epoxy, and has a thinner viscosity with bubble releasing attributes that
assist in giving the finished product a practically bubble-less finish with unparalleled depth and clarity. Liquid Glass is
formulated to use within all casting applications such as: River Tables, Void Filling Live-Edge Tables, Casting Art, and Even
Small Jewelry Castings as Small as 4ml’s! If you have a small project like a ring mold or jewelry, make sure to mix up no less
than a pint at a time. If mixing less than a pint, it is much easier to mix the incorrect volumes, which is a common mistake,
leading to curing issues.
Our Liquid Glass Deep Pour Epoxy resin kit is a two part epoxy, and has a thinner viscosity with bubble releasing attributes that
assist in giving the finished product a practically bubble-less finish with unparalleled depth and clarity. Liquid Glass is
formulated to use within all casting applications such as: River Tables, Void Filling Live-Edge Tables, Casting Art, and Even
Small Jewelry Castings as Small as 4ml’s! If you have a small project like a ring mold or jewelry, make sure to mix up no less
than a pint at a time. If mixing less than a pint, it is much easier to mix the incorrect volumes, which is a common mistake,
leading to curing issues.
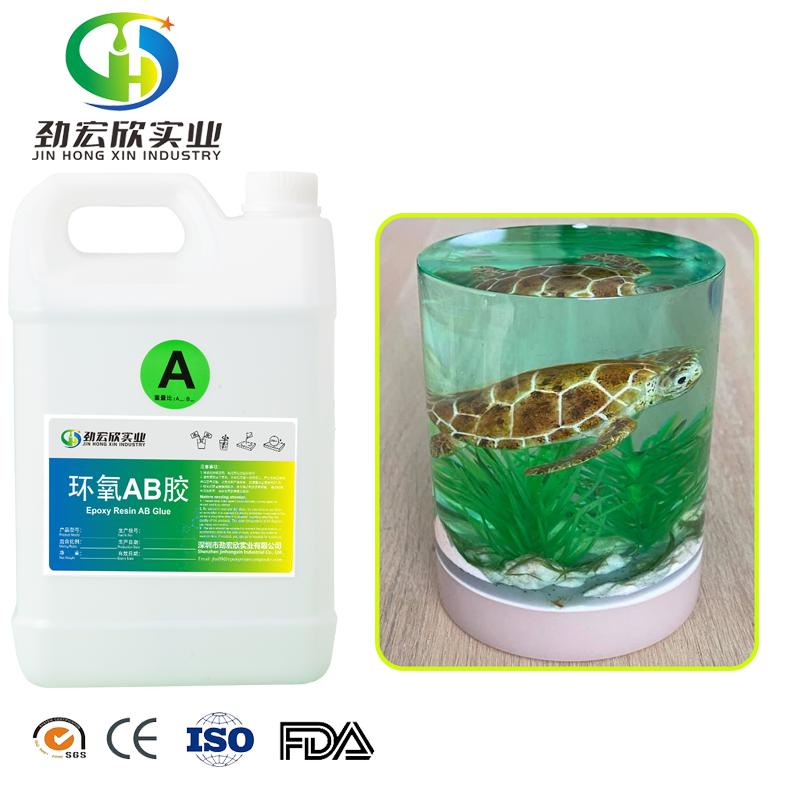
High-Grade UV Resistance
All epoxies will turn yellow overtime. What makes our Liquid Glass Deep Pour Epoxy different is our specific high-grade additive
formulations. Ours will yellow less and remain ultra-crystal-clear over a longer period of time than any of our competitors. Our
products are made for you, and made to last, bar none. .
All epoxies will turn yellow overtime. What makes our Liquid Glass Deep Pour Epoxy different is our specific high-grade additive
formulations. Ours will yellow less and remain ultra-crystal-clear over a longer period of time than any of our competitors. Our
products are made for you, and made to last, bar none. .
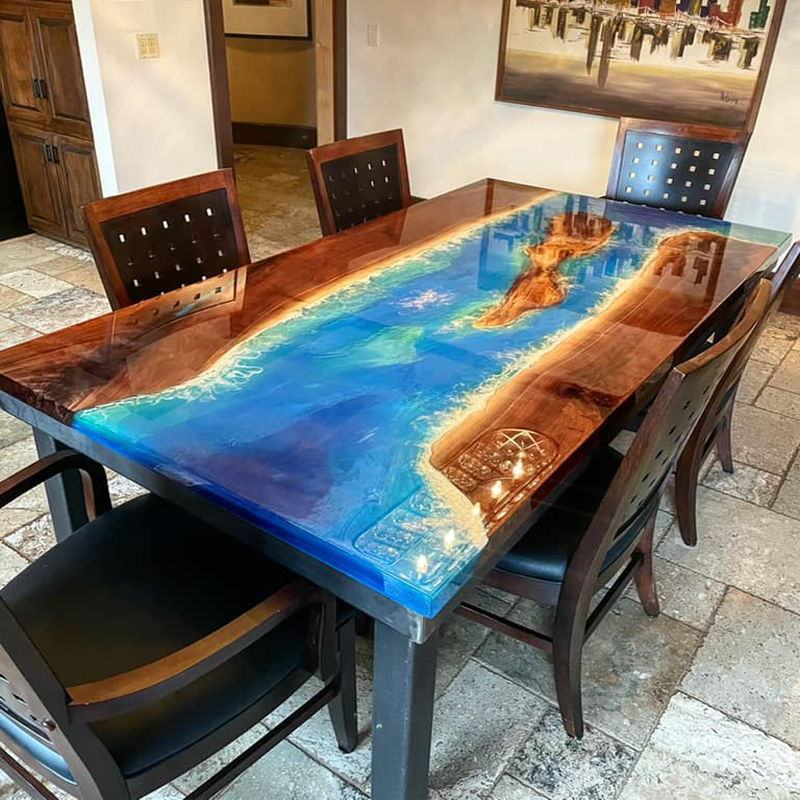
Integrate Color With Ease
Specification
OUR 3:1 FORMULA IS EASY TO MEASURE & EVEN EASIER TO POUR!
DIRECTIONS FOR USE:
Step 1: The ideal working temperature is around 77°F. Best results can be obtained at temperatures between 70°F and 85°F, in a
clean, dry, dust-free environment. Avoid working in high humidity. We recommend using this product on a leveled and flat work
surface.
Step 2: Measure product in accordance with your intended use. Prepare 2 parts Base Resin to 1 part Curing Agent by liquid volume.
Pour the Curing Agent first and then the Base Resin into a clean, smooth-sided container large enough to hold all the liquid and
allow room for mixing.
Step 3: The material must be mixed thoroughly for at least 6-8 minutes. Be sure to scrape the container sides, bottom, and corners
as you mix. Be careful not to whip excessive air into the mixture. If mixing a gallon, use a power mixer set to “hand speed.” For
smaller quantities, use stir sticks. Do not mix more than a gallon. Pour into a new, clean container and mix for an additional
minute.
Step 4: Pour the mixed resin onto the surface and distribute evenly with a squeegee or gloved hand. Continue to pour remaining
material to achieve the desired thickness, allowing the resin to flow evenly over the project’s sides. Resin can be poured up to
2” thick per pour, and up to 4” depending on the volume of the pour.
Step 5: Use a heat source such as a heat gun to remove any bubbles by adding a small amount of heat to the surrounding area. The
bubble will rise to the surface and pop.
Step 6: If you are going to make a second pour, the first pour should still be slightly sticky. Once the second pour is made,
bubbles may once again need to be removed. Material will feel hard after 48-72 hours, but full cure and maximum hardness can
require up to 7 days, depending upon the temperature.
PRO TIP: If you wish to apply paper decals or other objects under the JHX-318AB surface, those objects need to be bonded to
the surface either with JHX-318AB Epoxy or craft glue. Some wood may take the material well in a single coat; however, many types
of wood require a seal coat to prevent air bubbles from rising out of the wood and ruining the surface. Older, more porous pieces
of wood may contain both air and moisture that can contaminate the finish. In this case, the user may first paint on a very thin
coat of SuperClear Table Top Epoxy, allowing that to set before pouring the new layer.
DIRECTIONS FOR USE:
Step 1: The ideal working temperature is around 77°F. Best results can be obtained at temperatures between 70°F and 85°F, in a
clean, dry, dust-free environment. Avoid working in high humidity. We recommend using this product on a leveled and flat work
surface.
Step 2: Measure product in accordance with your intended use. Prepare 2 parts Base Resin to 1 part Curing Agent by liquid volume.
Pour the Curing Agent first and then the Base Resin into a clean, smooth-sided container large enough to hold all the liquid and
allow room for mixing.
Step 3: The material must be mixed thoroughly for at least 6-8 minutes. Be sure to scrape the container sides, bottom, and corners
as you mix. Be careful not to whip excessive air into the mixture. If mixing a gallon, use a power mixer set to “hand speed.” For
smaller quantities, use stir sticks. Do not mix more than a gallon. Pour into a new, clean container and mix for an additional
minute.
Step 4: Pour the mixed resin onto the surface and distribute evenly with a squeegee or gloved hand. Continue to pour remaining
material to achieve the desired thickness, allowing the resin to flow evenly over the project’s sides. Resin can be poured up to
2” thick per pour, and up to 4” depending on the volume of the pour.
Step 5: Use a heat source such as a heat gun to remove any bubbles by adding a small amount of heat to the surrounding area. The
bubble will rise to the surface and pop.
Step 6: If you are going to make a second pour, the first pour should still be slightly sticky. Once the second pour is made,
bubbles may once again need to be removed. Material will feel hard after 48-72 hours, but full cure and maximum hardness can
require up to 7 days, depending upon the temperature.
PRO TIP: If you wish to apply paper decals or other objects under the JHX-318AB surface, those objects need to be bonded to
the surface either with JHX-318AB Epoxy or craft glue. Some wood may take the material well in a single coat; however, many types
of wood require a seal coat to prevent air bubbles from rising out of the wood and ruining the surface. Older, more porous pieces
of wood may contain both air and moisture that can contaminate the finish. In this case, the user may first paint on a very thin
coat of SuperClear Table Top Epoxy, allowing that to set before pouring the new layer.
Primary Applications
|
Small Table/Bar Top Epoxy Coating, Jewelry, Epoxy Tumbler Art Projects
|
Large Table/Bar Top Epoxy Coating, Jewelry, Epoxy Tumbler Art Projects
|
Small Deep Pour, Void Filling, River Tables, Live Edge Tables,Casting Art, Jewelry, Serving Board Projects
|
Medium Deep Pour, Void Filling, River Tables, Live Edge Tables,Casting Art, Jewelry, Serving Board Projects
|
Large Deep Pour, Void Filling, River Tables, Live Edge Tables,Casting Art, Jewelry, Serving Board Projects
|
Max Pour Depth
|
1/4 inch
|
1/4 inch
|
2-4 inches
|
2-4 inches
|
2-4 inches
|
Premium UV Resistance
|
✓
|
✓
|
✓
|
✓
|
✓
|
Unparalleled Clarity & Depth
|
✓
|
✓
|
✓
|
✓
|
✓
|
Gel Time
|
20-30 Mins, Depending On Temp & Volume Mixed
|
20-30 Mins, Depending On Temp & Volume Mixed
|
8-12, Depending On Temp & Volume Mixed
|
8-12, Depending On Temp & Volume Mixed
|
8-12, Depending On Temp & Volume Mixed
|
Cure Time
|
24 Hours
|
24 Hours
|
36-72 Hours, Depending On Temp & Volume Mixed
|
36-72 Hours, Depending On Temp & Volume Mixed
|
36-72 Hours, Depending On Temp & Volume Mixed
|
Demould Time
|
12-14 Hours
|
12-14 Hours
|
36-48 Hours, Depending On Temp & Volume Mixed
|
36-48 Hours, Depending On Temp & Volume Mixed
|
36-48 Hours, Depending On Temp & Volume Mixed
|
Optimum Workability Time
|
Recommended After Fully Cured At 24 Hours
|
Recommended After Fully Cured At 24 Hours
|
Recommeded at 72 Hours After Fully Cured
|
Recommeded at 72 Hours After Fully Cured
|
Recommeded at 72 Hours After Fully Cured
|
Packing & Delivery
To better ensure the safety of your goods, professional, environmentally friendly, convenient and efficient packaging services will be provided.
Hot Searches