- Product Details
- {{item.text}}
Quick Details
-
Application:
-
sc pesticides line
-
Name:
-
sc pesticides line
-
Function:
-
fertilizer production line
-
Capacity:
-
10~250000 TON/YEAR
-
Voltage:
-
220V/380V 50HZ Customized
-
Process:
-
Mannheim Furnace Process
-
Advantage:
-
Low Consumption
-
Certificate:
-
CE/ISO 9001
-
Feature:
-
High Effeciency
-
Machine:
-
fertilizer production mixing line
Quick Details
-
Place of Origin:
-
China
-
Brand Name:
-
Farfly
-
Weight (KG):
-
1000
-
Application:
-
sc pesticides line
-
Name:
-
sc pesticides line
-
Function:
-
fertilizer production line
-
Capacity:
-
10~250000 TON/YEAR
-
Voltage:
-
220V/380V 50HZ Customized
-
Process:
-
Mannheim Furnace Process
-
Advantage:
-
Low Consumption
-
Certificate:
-
CE/ISO 9001
-
Feature:
-
High Effeciency
-
Machine:
-
fertilizer production mixing line
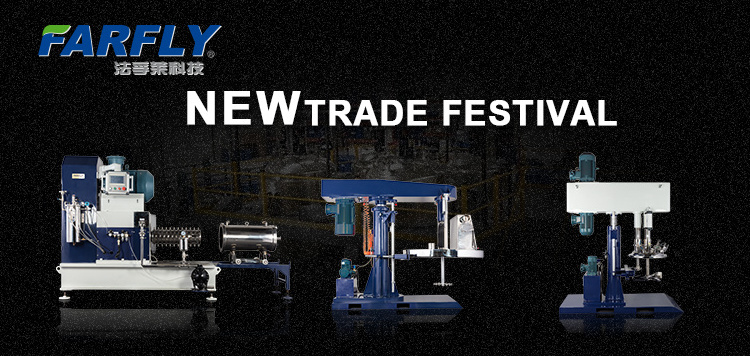

Product Introduction
1.This product is suitable for industrial mass production of complete sets of equipment.
2, The equipment can independently accomplish the vacuum feeding, dispersion, grinding, filtering and semi-automatic filling the
entire industrial process.
3, Design of products can be customized according to the scale of production, realize the automation process control the
equipment, saving space and staff, convenient management.
2, The equipment can independently accomplish the vacuum feeding, dispersion, grinding, filtering and semi-automatic filling the
entire industrial process.
3, Design of products can be customized according to the scale of production, realize the automation process control the
equipment, saving space and staff, convenient management.
Main Features
1) It applies to small, middle, large scale production, output from 1000-50,000 ton one year
2) The material which contact with the product is stainles steel, ss304 or 316L
3) The vessel is mirror plolished outside and inside, which make the vessle easy to clean and will
not have residual, with different thickness for different volume.
4) Configuration: according to different output and the particle size you need, we will equip with
high speed disperser, Bead Mill and paint color agitator, filter and automatic filling machine.
5) Installation: Our professional technician will come to your factory to instal the whole system.
6) Debug: After installation, we in charge of debug.
7) Training: Our engineer will train your workman about the operation and attention matters.
8) Maintenance: We have a strong service term, our engineer will solve your problem as earlier as possible
2) The material which contact with the product is stainles steel, ss304 or 316L
3) The vessel is mirror plolished outside and inside, which make the vessle easy to clean and will
not have residual, with different thickness for different volume.
4) Configuration: according to different output and the particle size you need, we will equip with
high speed disperser, Bead Mill and paint color agitator, filter and automatic filling machine.
5) Installation: Our professional technician will come to your factory to instal the whole system.
6) Debug: After installation, we in charge of debug.
7) Training: Our engineer will train your workman about the operation and attention matters.
8) Maintenance: We have a strong service term, our engineer will solve your problem as earlier as possible
Main Process
1). put the material to the 5000 L reactor kettle,start heating ,when the temperature reach about 100 degrees,it will product
gases,and the gas will into the separation column.
2). after part be cooled by the separation column, the rest gas into horizontal condenser,then condenser will cooling the gas
,after all the water and gas will into the catchment device.
3). the catchment device,will separate material back to reactor kettle,and exclude the water.(the process may be last about
fifteen to twenty hours)
4). during the reaction process,in order to improve the speed, can extracting vacuum,when reach the suitable time, sampling, assay
viscosity,if meet the requirement, then cooling.
5). when the temperature reach 130 degrees,put the raw materials to dilute kettle,and add Xylene (this kind of material) to dilute
kettle,
gases,and the gas will into the separation column.
2). after part be cooled by the separation column, the rest gas into horizontal condenser,then condenser will cooling the gas
,after all the water and gas will into the catchment device.
3). the catchment device,will separate material back to reactor kettle,and exclude the water.(the process may be last about
fifteen to twenty hours)
4). during the reaction process,in order to improve the speed, can extracting vacuum,when reach the suitable time, sampling, assay
viscosity,if meet the requirement, then cooling.
5). when the temperature reach 130 degrees,put the raw materials to dilute kettle,and add Xylene (this kind of material) to dilute
kettle,
Detailed
Equipment for paint making Features:
1. Sealessness , Eco-friendly
2. Highly Automatic, Easy operation;
3. Efficient and energy saving
4. Wide range of application: acrylic emulsion, primers, top finish painting, elastic flat paint, water proof coating, wall
painting inner and outer ,interior and exterior, high, medium and low end, etc
5. Annual production up to 2000~300 tons;
6. Painting fineness reaches 15 mm or less
7. Mirror surface polishing for all stainless steel parts makes them delightful and shining, vacuum operation
2. Highly Automatic, Easy operation;
3. Efficient and energy saving
4. Wide range of application: acrylic emulsion, primers, top finish painting, elastic flat paint, water proof coating, wall
painting inner and outer ,interior and exterior, high, medium and low end, etc
5. Annual production up to 2000~300 tons;
6. Painting fineness reaches 15 mm or less
7. Mirror surface polishing for all stainless steel parts makes them delightful and shining, vacuum operation
Noto:
The set includes 9 sub-systems:
1) Vacuum material adding system,
2) Pressure discharging and filtration system,
3) Slurry producing system,
4) Painting mixing system,
5) Cooling system,
6) Piping system,
7) Electrical control system,
8) Operation platform;
9) Packaging system
2) Pressure discharging and filtration system,
3) Slurry producing system,
4) Painting mixing system,
5) Cooling system,
6) Piping system,
7) Electrical control system,
8) Operation platform;
9) Packaging system
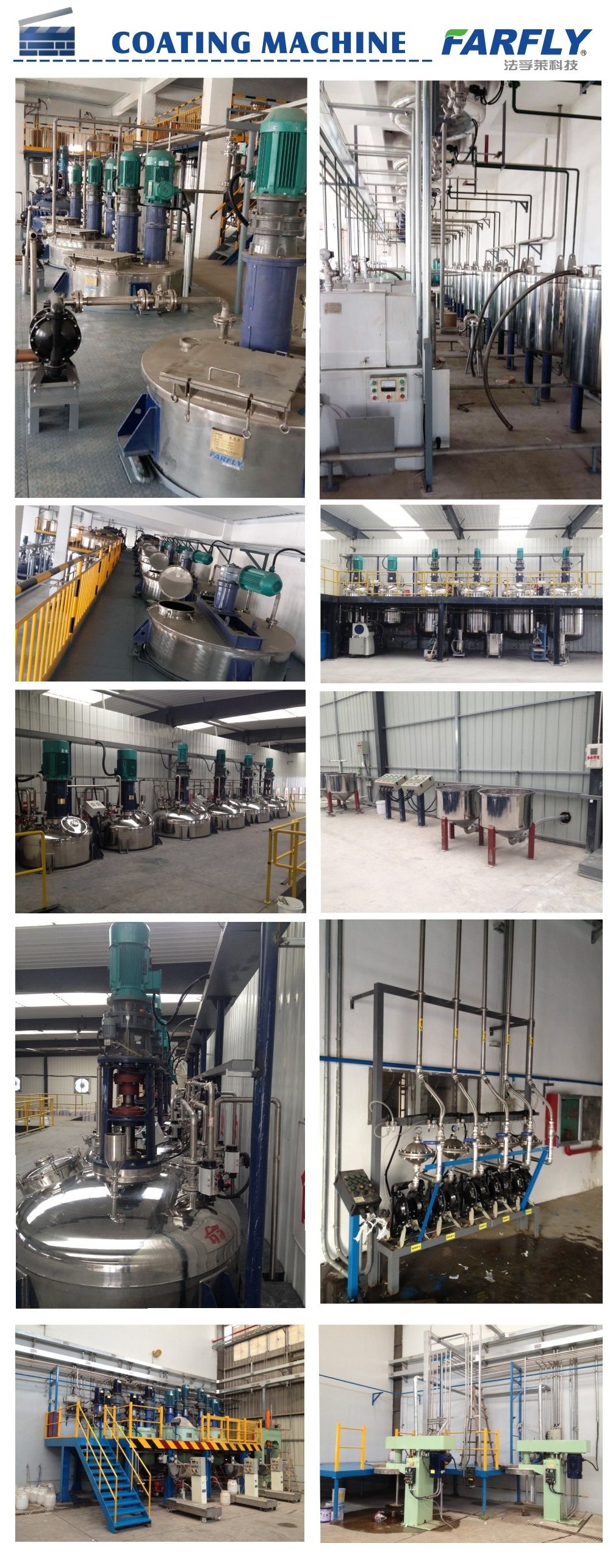
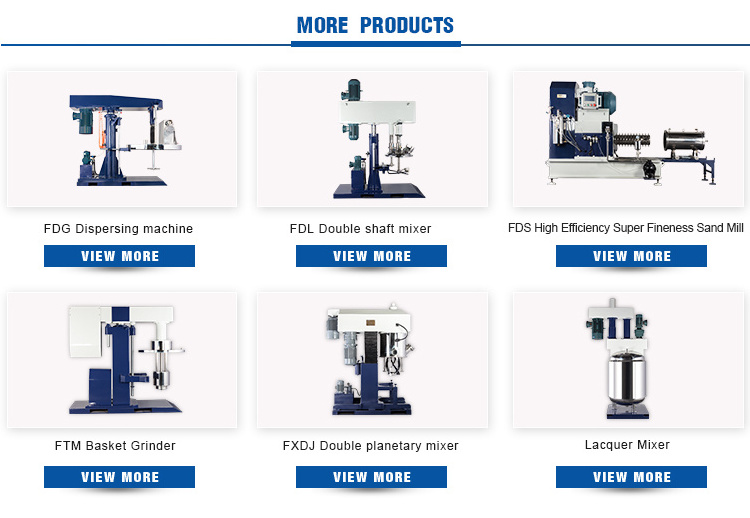
Hot Searches