- Product Details
- {{item.text}}
Quick Details
-
Machinery Capacity:
-
30-800KG/H
-
Machinery Function:
-
colloid mill
-
Product name:
-
colloid mill
-
Material:
-
SS304/SS316L
-
Usage:
-
Food Industry Equipment
-
Capacity:
-
10-5000KGS
-
Frequency:
-
0-60HZ
-
Voltage:
-
120V-480V
-
Application:
-
Food Industry
-
Function:
-
Grinding Material
-
Weight:
-
50-300kgs
-
processing micron:
-
300micron
Quick Details
-
Weight (KG):
-
60
-
Place of Origin:
-
Zhejiang, China
-
Brand Name:
-
LENO
-
Machinery Capacity:
-
30-800KG/H
-
Machinery Function:
-
colloid mill
-
Product name:
-
colloid mill
-
Material:
-
SS304/SS316L
-
Usage:
-
Food Industry Equipment
-
Capacity:
-
10-5000KGS
-
Frequency:
-
0-60HZ
-
Voltage:
-
120V-480V
-
Application:
-
Food Industry
-
Function:
-
Grinding Material
-
Weight:
-
50-300kgs
-
processing micron:
-
300micron
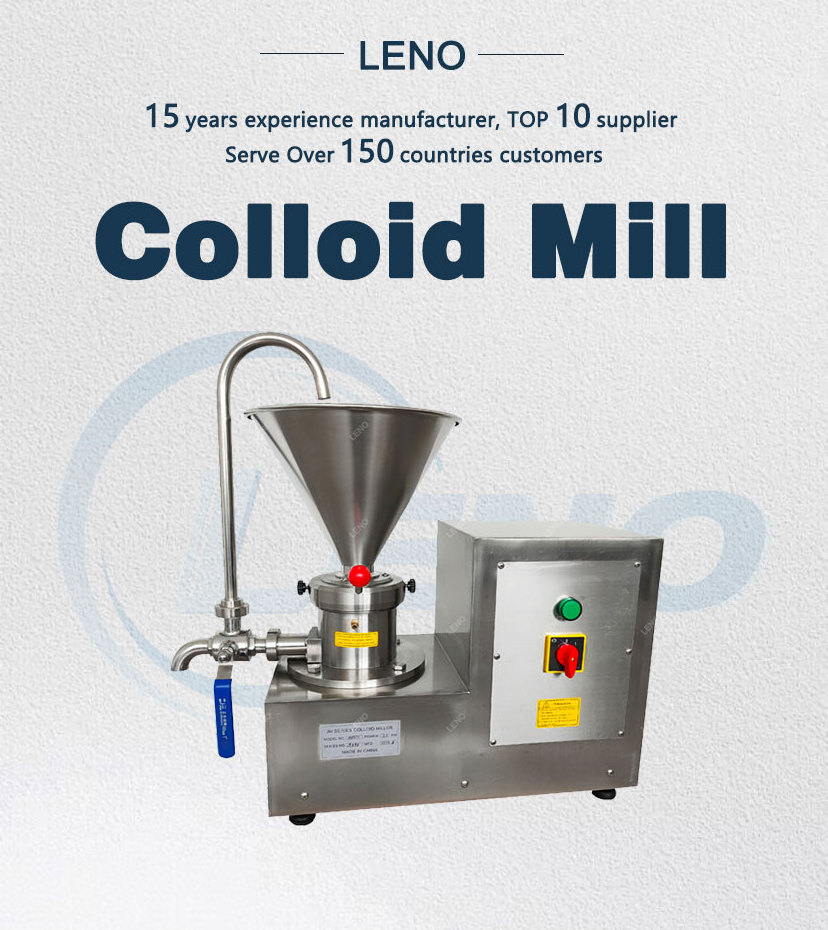
LENO colloid mill is a type of milling machine used in various industries to reduce the particle size of a solid or liquid
suspension. It is commonly used in the food, pharmaceutical, cosmetic, and chemical industries for the production of emulsions, suspensions, and dispersions.
The working process of a colloid mill involves the following steps:
1. Feed Material: The material to be processed is fed into the mill's hopper or inlet. This can be a solid or liquid substance or a mixture of both.
2. Rotor-Stator Assembly: Inside the colloid mill, there is a rotor and a stator. The rotor is a rotating component that contains a series of concentric teeth or grooves, while the stator is a stationary component that surrounds the rotor. The rotor and stator are designed to have a very small gap between them, typically in the range of 0.05 to 1.5 mm.
3. Shearing and Grinding: As the material passes through the small gap between the rotor and stator, it undergoes intense
Shearing, grinding, and turbulence. The high-speed rotation of the rotor generates a strong hydraulic shear force, causing the particles or droplets to be repeatedly broken down into smaller sizes. This process is known as homogenization or
micronization.
4.Circulation and Recirculation: The processed material continuously circulates within the colloid mill. It flows from the center of the rotor-stator assembly to the periphery, and then back to the center, creating a recirculation loop. This
circulation helps to ensure that all particles or droplets are subjected to the grinding action, resulting in a uniform and
consistent product.
5. Discharge: Once the desired particle size or consistency is achieved, the processed material is discharged from the colloid mill. It can be collected in a container or directed to further processing equipment.
LENO Colloid mills can have variations in design and configuration depending on the specific application
and industry requirements. Some mills may have additional features such as adjustable gap settings, temperature control, or multiple stages of grinding for finer particle size reduction.
Products Description
Material
|
SS304
|
|
|
Capacity
|
30KG-800KG/H
|
|
|
Viscosity
|
1-1000000pas
|
|
|
Temperature
|
0-100 celsius degree
|
|
|
Installation
|
Movebale or Fixed
|
|
|
Connection
|
Clamp/Union
|
|
|
Motor type
|
Normal
|
inverter
|
|
Griding precision
|
Normally Griding precision 60-100 microns (Emulsifying precision 50um)
|
|
|
RTS Default Specification
|
LNS60 with circulating pipe
(If you need other specifications, please contact us first. Thank you.) |
|
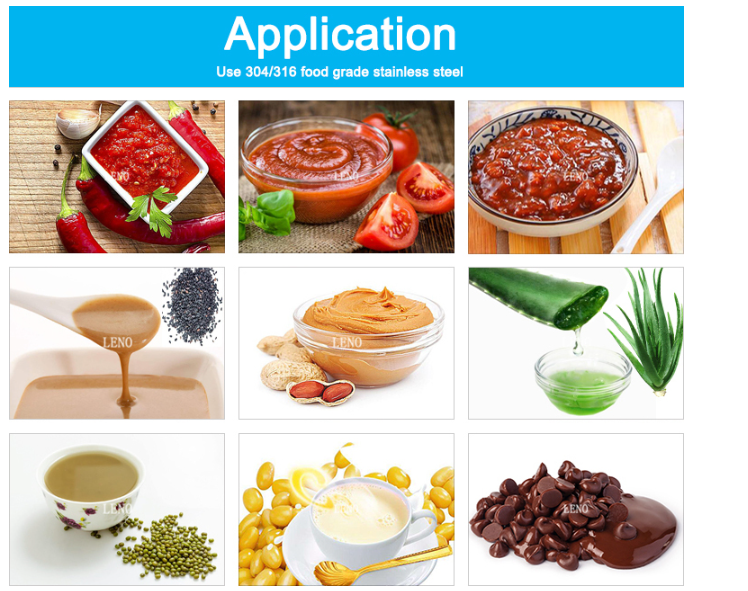
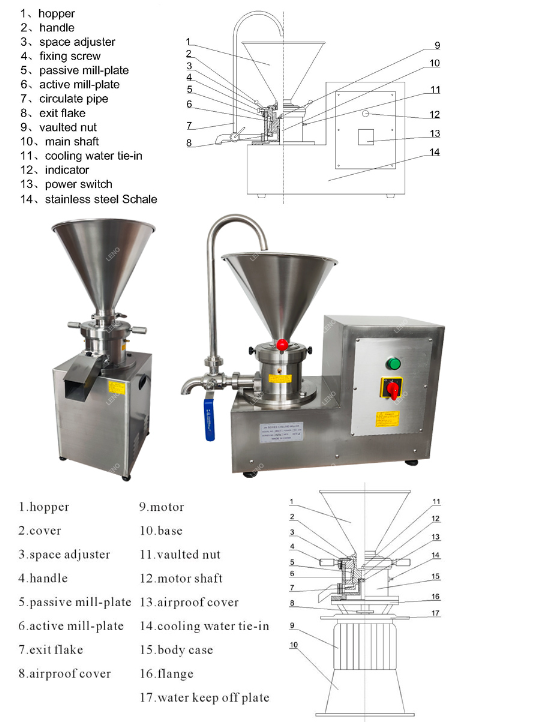
How to choose Our colloid mill
Check model no: The model no. of a colloid mill shows its structure type and diameter (mm) of grinding disc, which determines capacity.
Check capacity:
the capacity of a colloid mill varies greatly according to materials of different density and viscosity.
Circulation Tube:
suitable for low-viscosity materials that need recycling and reflux for grinding, such as soy milk, mung bean drinks, etc.
Rectangle Inlet:
suitable for high and medium viscosity materials that don’t need reflux or grinding, such as peanut butter, chili sauce, etc.
Check model no: The model no. of a colloid mill shows its structure type and diameter (mm) of grinding disc, which determines capacity.
Check capacity:
the capacity of a colloid mill varies greatly according to materials of different density and viscosity.
Circulation Tube:
suitable for low-viscosity materials that need recycling and reflux for grinding, such as soy milk, mung bean drinks, etc.
Rectangle Inlet:
suitable for high and medium viscosity materials that don’t need reflux or grinding, such as peanut butter, chili sauce, etc.
Product Paramenters
Model
|
Type
|
Power(Kw)
|
Funnel(L)
|
Capacity(Kg/h)
|
Cooling water pipe
|
Weight
|
LN60
|
Vertical
|
1.5kw
|
4.1L
|
30-50Kg/h
|
3/8"
|
42KGS
|
LNS60
|
Split
|
2.2kw
|
4.1L
|
30-50Kg/h
|
3/8"
|
65KGS
|
LN80
|
Vertical
|
4.0kw
|
8.4L
|
50-150Kg/h
|
3/8"
|
100KGS
|
LNS80
|
Spilt
|
4.0kw
|
8.4L
|
50-150Kg/h
|
3/8"
|
140KGS
|
LN120
|
Vertical
|
7.5kw
|
14.8L
|
60-150Kg/h
|
3/8"
|
160KGS
|
LNS120
|
Split
|
7.5kw
|
14.8L
|
60-150Kg/h
|
3/8"
|
215KGS
|
LNS130
|
Split
|
11kw
|
14.8L
|
300-500Kg/h
|
3/8"
|
315KGS
|
LNS150
|
Split
|
15kw
|
22L
|
400-700Kg/h
|
3/8"
|
335KGS
|
Product Image
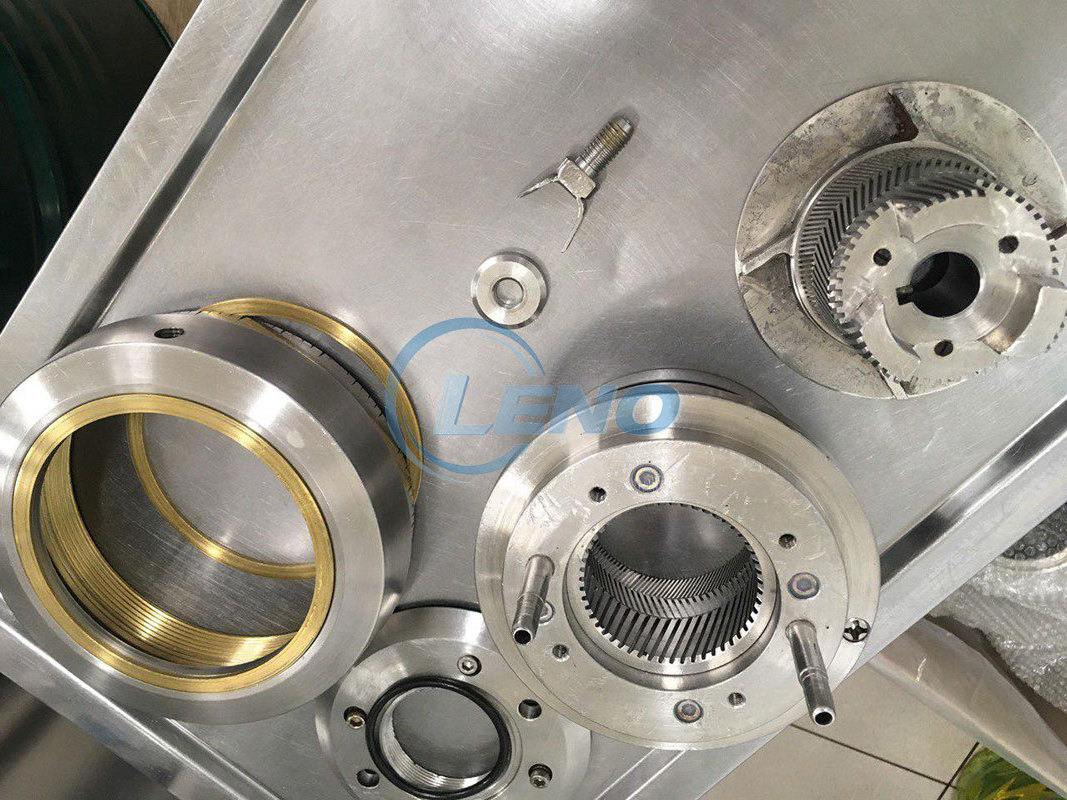
WHY CHOOSE LENO Colloid Mill
LENO colloid mill can provide the customized Hopper or Inlet: This is the entry point where the material to be processed is fed into the colloid mill. It can be a solid or liquid substance or a mixture of both.
LENO colloid mill comes with cooling water that can cool down the production temperature when it is being grinding.
LENO colloid mill can provide the circle piper that can clean by itself.
LENO coloid mill can provide the production with testing video for customer.
There are some advantages as below:
1:Rotor: The rotor is a rotating component within the colloid mill. It is typically driven by an electric motor or another power source. The rotor is designed with a series of concentric teeth, grooves, or other patterns that create intense shearing and grinding action when in contact with the stator.
2:Stator: The stator is a stationary component that surrounds the rotor. It is typically made of a hard material such as stainless steel and has a carefully engineered shape to form a small and uniform gap with the rotor. The stator provides support and stability to the rotor and contributes to the shearing and grinding process.
3:Gap Adjustment Mechanism: LENO colloid mills have a mechanism to adjust the gap between the rotor and stator. This allows for fine-tuning of the grinding intensity and particle size reduction. The gap can usually be adjusted by either manual or mechanical means.
4:Motor and Drive System: LENO colloid mill is powered by an electric motor or another power source, which drives the rotation of the rotor. The motor is connected to the rotor through a drive system such as belts, gears, or direct coupling.
5:Discharge Outlet: After the material has undergone the grinding process, it is discharged from the colloid mill through a separate outlet. The outlet can be connected to a collection container or directed to further processing equipment.
6:Frame and Housing: LENO colloid mill is housed within a sturdy frame or housing, which provides support, protection, and stability to the internal components. The housing is typically made of stainless steel or other suitable materials for hygienic and corrosion-resistant purposes.
Recommend Related Products
Hot Searches