- Product Details
- {{item.text}}
Quick Details
-
Voltage:
-
220V
-
Power:
-
As your requirement
-
Dimension(L*W*H):
-
As your requirement
-
Weight:
-
1500 KG
-
After-sales Service Provided:
-
Overseas service center available
-
Plate Material:
-
AISI304/316/Ti
-
Gasket Material:
-
NBREPDM/FKM
-
Frame Material:
-
CS/SS
-
Color:
-
Blue
-
OEM:
-
Available
-
Application Industries:
-
Alcohol Plant,Fuel ethanol
-
Certification:
-
ISO9001/ce
-
Function:
-
Multifunction
Quick Details
-
Core Components:
-
evaporator
-
Place of Origin:
-
Jiangsu, China
-
Brand Name:
-
GOJE
-
Voltage:
-
220V
-
Power:
-
As your requirement
-
Dimension(L*W*H):
-
As your requirement
-
Weight:
-
1500 KG
-
After-sales Service Provided:
-
Overseas service center available
-
Plate Material:
-
AISI304/316/Ti
-
Gasket Material:
-
NBREPDM/FKM
-
Frame Material:
-
CS/SS
-
Color:
-
Blue
-
OEM:
-
Available
-
Application Industries:
-
Alcohol Plant,Fuel ethanol
-
Certification:
-
ISO9001/ce
-
Function:
-
Multifunction
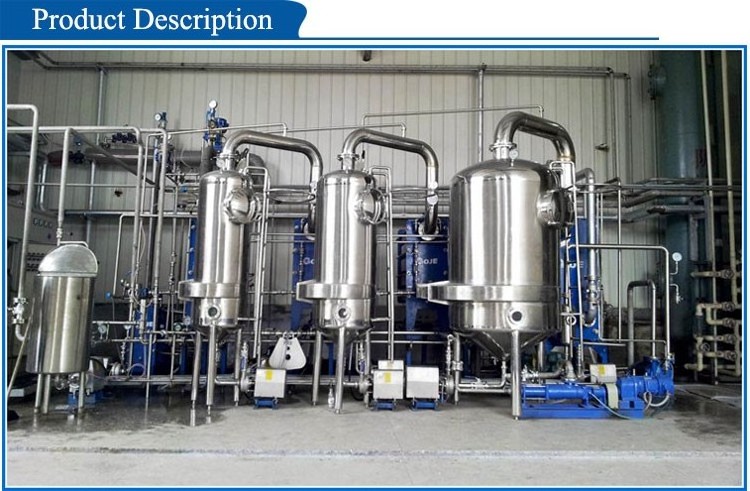
By analyzing material properties and process parameters, the system uses: four-effect plate-type downstream design, the process flow is as follows:
The material conveyed from the preceding stage is preheated by the feed preheating system to the boiling point temperature of the first effect evaporator ZF01, and enters the first effect evaporator ZF01, which is heated and vaporized by the heating steam on both sides in the evaporator, and then The mixture outlet of the evaporator is sprayed at a high speed in the form of a vapor-liquid mixture, and the tangential line enters the material inlet of the primary cyclone separator XFQ1. In the cyclone separator, due to the centrifugal force, the droplets are sucked to the wall of the cylinder and are collected by gravity. The bottom of the separator is then pumped out by the first material pump CB01 to the next stage evaporator ZF02, and the vapor phase is spirally raised. The small amount of droplets trapped by the top is captured by the top set of the juice trapping device and returned to the bottom of the tank. The heating chamber which is discharged into the lower stage evaporator ZF02 from the air outlet at the top of the separator serves as a heating heat source.
Similarly, the primary concentrated material sent from CB01 to the second-effect evaporator ZF02, the secondary steam generated by the first-effect evaporator ZF01 continues to be heated and vaporized and boiled, and enters the two-effect cyclone XFQ2 for centrifugal separation, and the liquid phase is pumped by the product. The CB02 is taken out to the next stage evaporator ZF03, and the vapor phase is passed to the heating chamber of the next stage evaporator ZF03 as a heating source.
Similarly, the secondary concentrated material sent from CB02 to the second-effect evaporator ZF03 is heated by the secondary steam generated by the two-effect evaporator ZF02 to vaporize and boil, and enters the three-effect cyclone XFQ3 for centrifugal separation. The pump CB03 is pumped out to the next stage evaporator ZF04, and the vapor phase is passed to the heating chamber of the next stage evaporator ZF04 as a heating source.
Similarly, the three concentrated materials sent from CB03 to the second-effect evaporator ZF04, the secondary steam generated by the three-effect evaporator ZF03 continues to be heated and vaporized and boiled, and enters the four-effect cyclone XFQ4 for centrifugal separation, and the liquid phase is pumped by the product. The CB04 is taken out, and the qualified material is sent to the product storage tank through the concentration or density detection, and the unqualified product is returned to the incoming material tank; the vapor phase enters the steam inlet of the condenser LNQ.
The secondary steam and non-condensable gas entering the condenser LNQ are cooled by the circulating cooling water of the process to be condensed and cooled, and then enter the condenser steam-water separation tank FLGL. The liquid phase is extracted by the condenser condensate pump NBL at the bottom of the separation tank, The condensate is withdrawn from the top of the separation tank by a vacuum system. The process circulating cooling water is provided by the user, and the user ensures that the water temperature and flow rate meet the requirements of use.
The establishment and maintenance of the system vacuum is completed by a set of water ring vacuum pumps. The working fluid of the vacuum pump is provided by the user, generally clean and non-corrosive 25 ° C normal temperature cold water.
In order to save energy and increase operating costs, the system is optimized as follows:
1. The feed preheating system adopts three-stage design: preheater A (end-effect waste steam preheating) → preheater B (mixed condensate preheating) → preheater C (fresh steam preheating)
Process flow diagram
Plate type advantage
For the multi-effect evaporation process, we adopt different types of evaporator types according to the material conditions: respectively: lifting film, rising film, falling film form:
Why Choose us?
1. More than 20 years of experience in the design and manufacture of evaporation systems, which can quickly determine the problems of the evaporation system during operation, and has a data database of practical operations of hundreds of materials.
2. The professional personnel and R&D team of the evaporation department have the most complete plate evaporation type in China, which is satisfied with the process needs of different industries.
3. Product series, rising film, lifting film, and falling film three series of evaporators, gathered in all the advantages of evaporation form, respectively, in different empirical data, is the most advanced and complete professional company in the field of evaporation.
4. The evaporation plate type has the largest single-plate area of the international model and the smallest model to meet different working conditions.
5. Semi-welded imported plate evaporator plate type, leading international technology, to solve the problem of expensive imported equipment and untimely service.
6. Ranked first in the market share of plate evaporation system in the starch sugar industry. China's first brand in the refined sugar market at home and abroad, has rich experience in overseas projects, and has served the project experience of evaporation systems for many countries.
7. The design process is
compact and the system energy saving effect is more significant than similar products. And each system has 3D drawings.
8. Experienced on-site commissioning and after-sales service personnel system, VIP quality customer system, 24-hour after-sales guarantee.
9. Provide quality transformation and technical support services for the evaporation system.
10. The susceptible gasket can be used for up to 10 years under normal use.