- Product Details
- {{item.text}}
Quick Details
-
Production Speed(Cycles/min):
-
35
-
Air Pressure(MPa):
-
0.7 MPa
-
Sheet Thickness(mm):
-
0.15 - 2 mm
-
Heating Power (kW):
-
35 kW
-
Air Comsumption(L/min):
-
2000 L/min
-
Water Comsumption(L/min):
-
35 L/min
-
Place of Origin:
-
Guangdong, China
-
Brand Name:
-
DONGXING
-
Voltage:
-
380V 50HZ
-
Dimension(L*W*H):
-
1200*280*300cm
-
Weight (T):
-
16 T
-
Power(KW):
-
120
-
Product name:
-
Automatic Plastic Thermoforming Machine
-
Application:
-
Disposable Plastic box
-
Suitable material:
-
PP PS PET PVC CPET OPS PLA
-
Color:
-
Customized Color
-
Max forming area:
-
760*800
-
After-sales Service Provided:
-
Field maintenance and repair service, Engineers available to service
-
Sheet width:
-
450-800
-
Travel depth:
-
165mm
-
Max Roll diameter:
-
1000mm
-
Cycle period:
-
40/min
Quick Details
-
Max.Forming Height(mm):
-
150 mm
-
Forming Width (mm):
-
760 mm
-
Forming Length (mm):
-
800 mm
-
Production Speed(Cycles/min):
-
35
-
Air Pressure(MPa):
-
0.7 MPa
-
Sheet Thickness(mm):
-
0.15 - 2 mm
-
Heating Power (kW):
-
35 kW
-
Air Comsumption(L/min):
-
2000 L/min
-
Water Comsumption(L/min):
-
35 L/min
-
Place of Origin:
-
Guangdong, China
-
Brand Name:
-
DONGXING
-
Voltage:
-
380V 50HZ
-
Dimension(L*W*H):
-
1200*280*300cm
-
Weight (T):
-
16 T
-
Power(KW):
-
120
-
Product name:
-
Automatic Plastic Thermoforming Machine
-
Application:
-
Disposable Plastic box
-
Suitable material:
-
PP PS PET PVC CPET OPS PLA
-
Color:
-
Customized Color
-
Max forming area:
-
760*800
-
After-sales Service Provided:
-
Field maintenance and repair service, Engineers available to service
-
Sheet width:
-
450-800
-
Travel depth:
-
165mm
-
Max Roll diameter:
-
1000mm
-
Cycle period:
-
40/min
Products Description
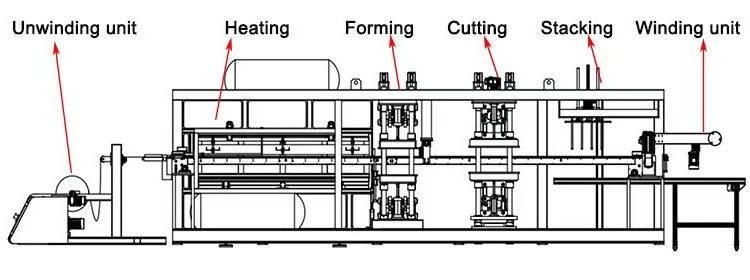
Main Configuration Instructions
|
|
|
|
|
||||
Control System
|
Germany Beckhoff System
|
|
|
|
||||
Programmable Controller (PLC)
|
Germany Beckhoff System
|
|
|
|
||||
Touch display
|
Taiwan Delta (15-inch color touch display)
|
|
|
|
||||
Pull tab servo system
|
Taiwan Delta 5.5KW
|
|
|
|
||||
Rail (beam) cooling system
|
The whole beam is cooled by water (circulating water)
|
|
|
|
||||
Forming Servo System
|
Taiwan Delta (with brake) 5.5KW 2 units
|
|
|
|
||||
Cutting servo system
|
Taiwan Delta (with brake) up 7.5KW, down 5.5KW
|
|
|
|
||||
Stack Servo System
|
Taiwan Delta (with brake) 1.5KW
|
|
|
|
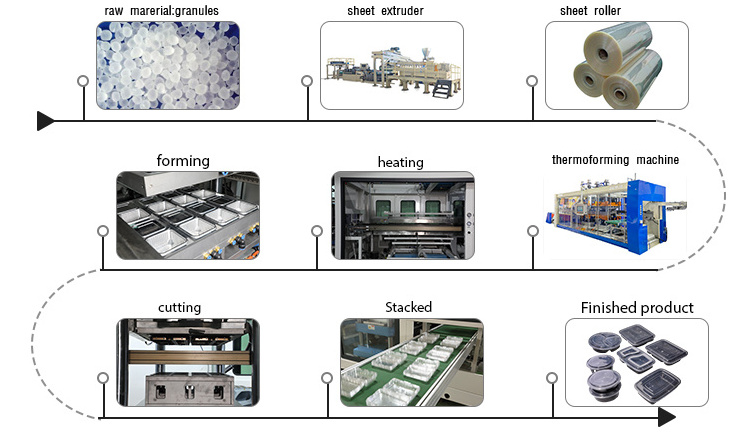
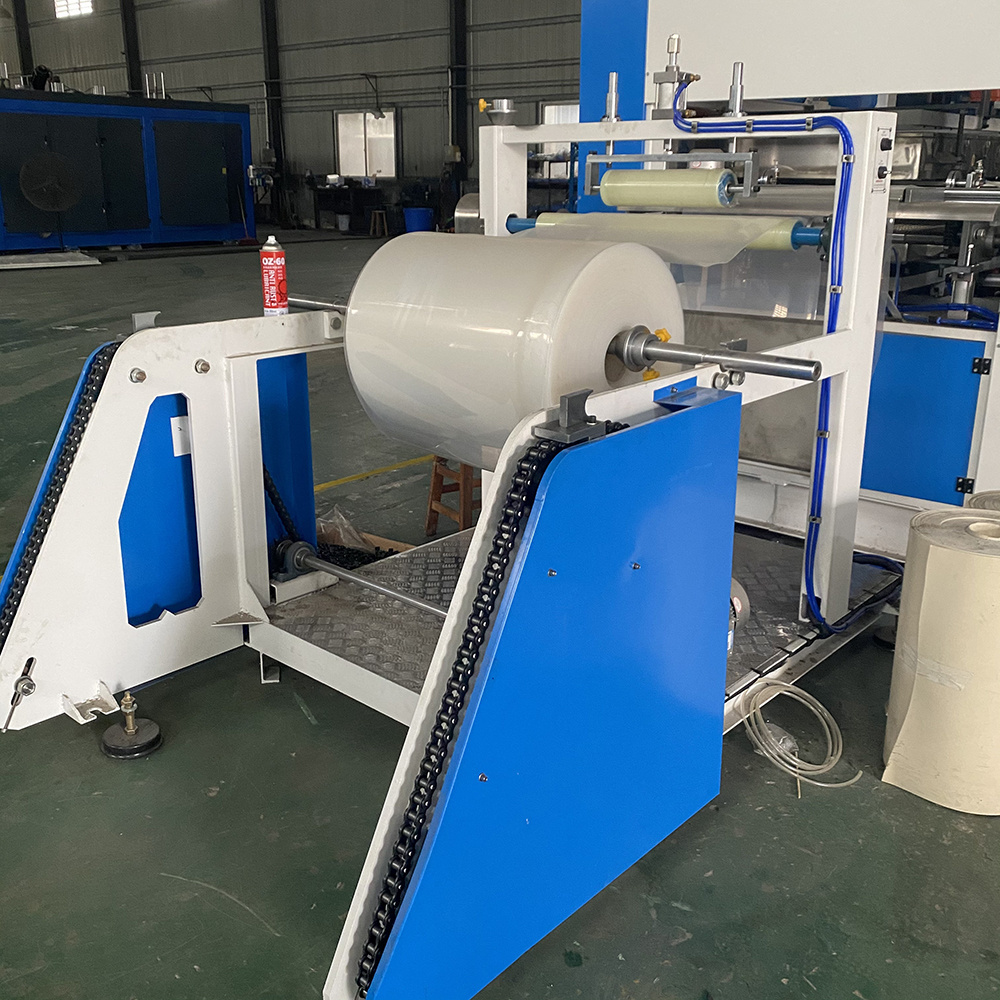
Feeding Part
1.Double material rod automatic mechanical loading roll device, roll diameter 1100mm, can bear 500kg.
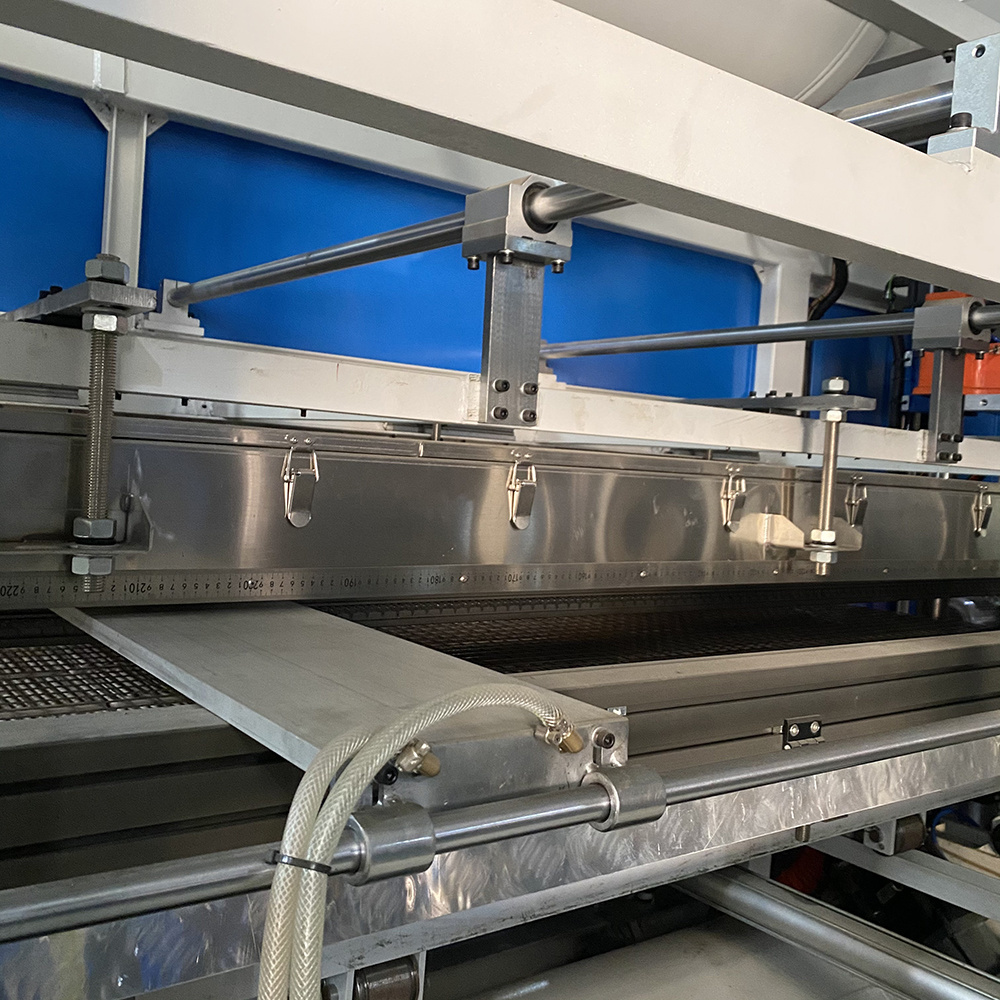
Heating Part
1.Hot oven length is 3 times the forming length,upper oven and lower oven heating ,lower oven with protective steel mesh,high temperature resistant wire,with current overload protection.
2.
Ceramic heating tile.
Details of the machine
Technical Parameters
|
|
|
|
|
|
|
|||||
Station
|
Four Station
|
Three station
|
Four stations
|
Three station
|
Three station
|
Three station
|
|||||
Model
|
DM-060
|
|
Dm-80
|
|
DX-7260
|
DX-FY7190
|
|||||
Forming Area
|
W780*L600mm
|
|
W720*L800mm
|
|
W720*L600mm
|
W710*L900mm
|
|||||
Forming Depth (Max.)
|
150mm
|
|
150mm
|
|
150mm
|
150mm
|
|||||
Sheet thickness
|
0.15-0.2mm
|
|
|
|
0.15-0.2mm
|
0.15-2.0mm
|
|||||
cycle period
|
40/min
|
|
|
|
30/min
|
30/min
|
|||||
Air pressure
|
7Bar
|
|
|
|
7Bar
|
7Bar
|
|||||
Min.Forming Area
|
420*300mm
|
|
420*300mm
|
|
420*300mm
|
|
|||||
Sheet width
|
450-810mm
|
|
450-780mm
|
|
450-810mm
|
450-760mm
|
|||||
Suitable Sheet
|
PP,PS,PET,CPET,PVC,OPS,PLA,etc.
|
|
|
|
|
|
|||||
Power supply
|
AC 380V, 50Hz, Three-phase, Four-wire
|
|
|
|
|
|
|||||
Rated power
|
|
100kw
|
|
120kw
|
100kw
|
80kw
|
|||||
Heating power
|
20-55kw
|
|
20-55kw
|
|
20-55kw
|
20-55kw
|
|||||
Procedure
|
Forming-punching-cutting-stacking
|
Forming-cutting-stacking
|
Forming-punching-cutting-stacking
|
Forming-cutting-stacking
|
Forming-cutting-stacking
|
Forming-cutting-stacking
|
|||||
Dimension
|
L11m*W2.8m*H3m
|
L13m*W2.8m*H3m
|
L12m*W2.8m*H3m
|
L14m*W2.8m*H3m
|
L11m*W2.8m*H3m
|
L8m*W2.
6m*H2.8m
|
|||||
Weight
|
16T
|
14T
|
18T
|
16T
|
13T
|
10T
|
and Germany Beckhoff Controller.
1. Full workstation casting.
2. Servo control of forming upper mold core .
3. Automatic mold locking device.
4. The connecting mechanism adopts wear-resistant steel sleeve, which can bear more weight and rotate more precisely. And the symmetrical swing ensures the parallelism of machine operation and avoids the lateral wear of the four pillars, which makes the life of the machine longer.
6. Adopt high power servo motor drive, high precision, high efficiency and low noise.
7. . The working principle is the combination of positive and negative pressure, through some nylon plugs in the mold to assist in stretching, so that it has a stronger production capacity.
8. Cooling water in the mold cavity speeds up the cooling speed and makes it easy to take off the mold.
9. The upper and lower working positions can be adjusted automatically, which is fast and convenient.
10. Each working position is locked by nuts to ensure the stability of machine operation.
1. High power servo motor directly punching and cutting, with strong cutting force, i.e. the cutting line can reach 12 meters to ensure perfect cutting.
2. Automatic mold locking device, the work station can be moved up and down, left and right by automatic adjustment, with anti-collision function, which makes the debugging of the mold more convenient and fast.
Forming upper mold table height adjustable 50mm
3. Overheating alarm function of heating guide plate (90℃) , safe and reliable.
4. The movable blade has the function of positioning guide, which makes the product cutting more accurate.
5. Intelligent lubrication system can be lubricated according to certain amount and time, which can make the machine long life and continuous.
8. Even the symmetrical swing ensures the parallelism of machine operation and avoids the lateral wear of four pillars, which makes the machine's service life longer.
Stacking Station
1. Stacking is driven by servo motor, higher precision and efficiency.
2. Automatic counting, automatic stacking.
3. Equipped with detachable and replaceable conveyor belt, which is efficient and convenient.
4. Equipped with several noise elimination devices to reduce stacking noise.
Rewinding System
1.
Inverter automatic winding function, adjustable torque function.
Features and Advantages:
1. Full servo-driven machine, no noise, no vibration, good molding and fast speed.
2. Servo-controlled molding of the upper mold core .
3. Work station casting .
4. Four-stage hot stove heating to improve PP speed.
5. Chain rail eight functions (for PP, full degradation material high sagging material.
The automatic removal device of the furnace can be turned off at any time during the production process without destroying the sheet. Achieve the purpose of not wasting materials.
6. Zhuanggu temperature control (computer digital temperature control, one-to-one precise temperature control temperature difference plus or minus 0.5 degrees, intelligent temperature control energy saving 20%).
7. Equipped with automatic mold locking device, forming and cutting mold servo drive. The height position of the upper and lower die can be easily and quickly adjusted in the closed state; the lower die can be buffered at any time in the closed direction to improve the closing speed and avoid impact.
8. Automatic cutting, automatic counting, automatic transmission by PLC.
9. Save manpower, only 1-2 workers are needed when packing.
Certifications
Our Factory
Dongguan Dongxing Machinery Equipment Co., Ltd.
is a professional production enterprise specializing in the R & D, innovation and manufacture of various plastic molding machines. The company is located in Qiaotou town, Dongguan, adjacent to the airport, bus station and freight station. The traffic is very convenient.
Combined with more than 20 years' experience of plastic suction machine manufacturing, we developed a positive and negative pressure forming punching and stacking integrated machine with independent intellectual property rights. From a series of production processes such as charging, positive and negative pressure
molding, punching, trimming, stacking, counting, conveying, automatic recovery of materials,etc., a series of production processes are completed at once. The company specializes in producing positive and negative pressure thermoforming machine, cup making machine, servo driven high-speed molding machine and ordinary high-speed molding machine.
Customer visits to our factory and our exhibitions
Application
This machine is suitable for the production of highly demanding food packaging products:
cup lids, freshness trays, moon cake trays, disposable fast food boxes, disposable food boxes, instant noodle bowl lids, milk tea lids, coffee cup lids, beverage cups, ice cream cups, jelly cups, packaging boxes, plastic packaging containers for daily necessities, medical plastic packaging, wine packaging and plastic packaging for electrical appliances.
Applicable materials: PP, PS, PET, CPET, PVA, OPS, PLA,
Biodegradable,
etc.
Packing Details
Plastic Thermoforming Machine packaging
1,Standard export wooden case with plastci film.
2,as customer's request.
FAQ
Q1: Are you a factory or trading company?
We are a factory, and we are a professional plastic thermoforming machinery and equipment manufacturer dedicated to the research and development。
Q2. why should you buy from us not from other suppliers?
Combined with more than 20 years' experience of plastic suction machine manufacturing, we developed apositive and negative pressure forming punching and stacking integrated machine with independentintellectual property rights.
Combined with more than 20 years' experience of plastic suction machine manufacturing, we developed apositive and negative pressure forming punching and stacking integrated machine with independentintellectual property rights.
Q3: How long is the warranty period?
13months calculated from the date of shipment from our factory.During warranty period, except the artificial factor, the spares are free to maintenance, beyond the warranty time, the buyer needs to pay the spare charge and shipping cost.
Q4: How to install the machine?
We will send technician to your factory to install the machine, and teach your workers to use it. You pay all related costs, including visa charge, double-way tickets, hotel, meals, and technician salary.
Q5:How can we guarantee quality?
W
e will test repeatedly before shipment until we achieve customer satisfaction.
Hot Searches