- Product Details
- {{item.text}}
Quick Details
-
H Content (%):
-
0.01%
-
Ash Content (%):
-
0.01%
-
Place of Origin:
-
Shandong, China
-
Brand Name:
-
sportpro
-
Model Number:
-
CF4
-
Dimensions:
-
custom tube
-
Working Temperature:
-
200 degree
-
Volatile:
-
0.01%
-
Product name:
-
3K Carbon Fiber Tube
-
Material:
-
100% Carbon Fiber
-
Color:
-
Customer Request
-
Surface:
-
Glossy/ Matte/ 50% Glossy
-
Feature:
-
Light Weight High Strength
-
Weave:
-
3K Twill Weave/Plain Weave
-
Function:
-
outdoor industry
-
Tolerance:
-
+/-0.1mm
-
Process:
-
Roll-wrapped Technology
-
OEM:
-
OEM Accepted
Quick Details
-
C Content (%):
-
100% carbon
-
S Content (%):
-
0.01%
-
N Content (%):
-
0.01%
-
H Content (%):
-
0.01%
-
Ash Content (%):
-
0.01%
-
Place of Origin:
-
Shandong, China
-
Brand Name:
-
sportpro
-
Model Number:
-
CF4
-
Dimensions:
-
custom tube
-
Working Temperature:
-
200 degree
-
Volatile:
-
0.01%
-
Product name:
-
3K Carbon Fiber Tube
-
Material:
-
100% Carbon Fiber
-
Color:
-
Customer Request
-
Surface:
-
Glossy/ Matte/ 50% Glossy
-
Feature:
-
Light Weight High Strength
-
Weave:
-
3K Twill Weave/Plain Weave
-
Function:
-
outdoor industry
-
Tolerance:
-
+/-0.1mm
-
Process:
-
Roll-wrapped Technology
-
OEM:
-
OEM Accepted
Recommend Products
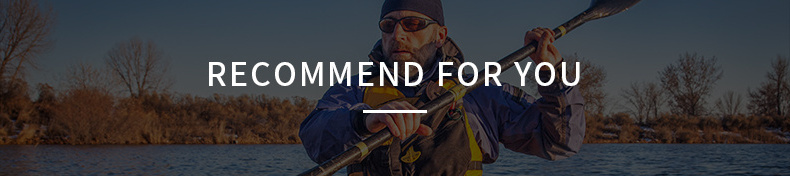
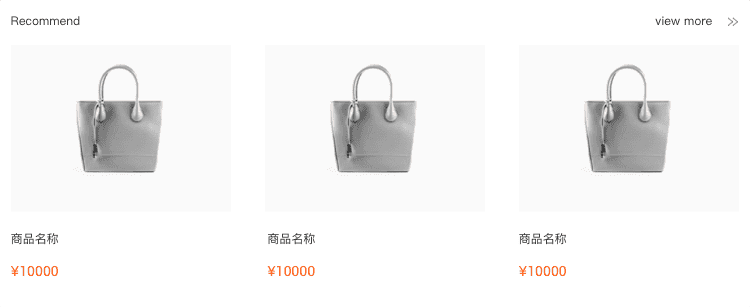
Products Description
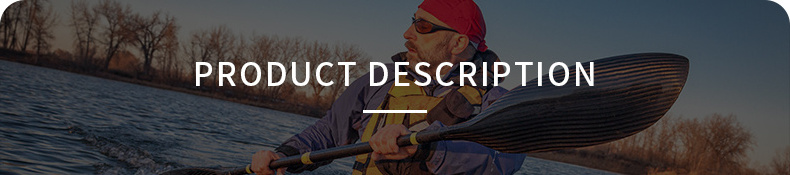
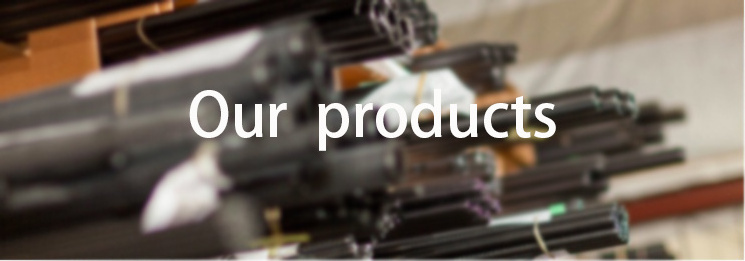
Due to their unique properties, carbon fiber tubes are used in numerous applications over traditional materials such as aluminum,
steel and titanium.
* High strength and stiffness with low weight
* Excellent fatigue resistance
* Dimensional stability: Low to Zero CTE (Coefficient of Thermal Expansion)
steel and titanium.
* High strength and stiffness with low weight
* Excellent fatigue resistance
* Dimensional stability: Low to Zero CTE (Coefficient of Thermal Expansion)
We manufacture carbon fiber parts and composite products using a variety of process methods. Or, when the need arises, we will develop a new process altogether to meet your needs and requirements. Our engineers thrive when solving problems and creating innovative solutions for your needs. Count on Clearwater Composites as a valuable carbon fiber manufacturing partner.
Composite Process Methods
* Roll Wrapping
* Resin Transfer Molding (RTM)
* Vacuum Bagging
* Compression Molding
* Trapped Rubber Molding
* Other Proprietary Composite Processes
* Resin Transfer Molding (RTM)
* Vacuum Bagging
* Compression Molding
* Trapped Rubber Molding
* Other Proprietary Composite Processes
Secondary Operations
* CNC Machining
* Centerless Grinding
* Complex Bonded Assemblies
* Finishing and Painting
* Centerless Grinding
* Complex Bonded Assemblies
* Finishing and Painting
Materials
* Carbon fiber
* Fiberglass – E-glass and S-glass
* Aramid
* Other fibers
* Thermoset composite
* Thermoplastic composites
* Fiberglass – E-glass and S-glass
* Aramid
* Other fibers
* Thermoset composite
* Thermoplastic composites
Talk with an Engineer
Contact our team of carbon fiber and composites experts to design a solution for your specific application. You will receive a prompt response. If you have your design or drawing pls also share with us!
Contact our team of carbon fiber and composites experts to design a solution for your specific application. You will receive a prompt response. If you have your design or drawing pls also share with us!
Roll wrapping tech
Roll wrapping is an excellent process to produce high quality carbon fiber tubing and fiberglass tubing. The roll wrapping process
utilizes pre-impregnated (prepreg) carbon fiber or fiberglass materials. The prepreg is cut into patterns with specific fiber
orientations. The patterns are rolled onto a mandrel and then wrapped with a thin plastic film. The plastic film applies pressure
and contains the resin during the curing cycle. After the part has cured, the mandrel is extracted and the plastic film is
removed.
Advantages of Roll Wrapping
* Maximum Strength and Stiffness – the use of prepreg materials and the ability to precisely control fiber orientation results in
maximizing the performance of carbon fiber and fiberglass products
* Customization – prepreg plies can readily be added or subracted allowing the tube to be customized with different wall
thicknesses
* No Minimum Quantities – Because each tube is made one at a time, small production runs are available.
utilizes pre-impregnated (prepreg) carbon fiber or fiberglass materials. The prepreg is cut into patterns with specific fiber
orientations. The patterns are rolled onto a mandrel and then wrapped with a thin plastic film. The plastic film applies pressure
and contains the resin during the curing cycle. After the part has cured, the mandrel is extracted and the plastic film is
removed.
Advantages of Roll Wrapping
* Maximum Strength and Stiffness – the use of prepreg materials and the ability to precisely control fiber orientation results in
maximizing the performance of carbon fiber and fiberglass products
* Customization – prepreg plies can readily be added or subracted allowing the tube to be customized with different wall
thicknesses
* No Minimum Quantities – Because each tube is made one at a time, small production runs are available.
Hot Searches