- Product Details
- {{item.text}}
Quick Details
-
Main coating methods:
-
Direct scraping coating
-
Working wheel face:
-
350 mm
-
Maximum operating line speed:
-
10m/min
-
After Warranty Service:
-
Video technical support, Online support
-
Local Service Location:
-
None
-
After-sales Service Provided:
-
Free spare parts, Online support, Video technical support
Quick Details
-
Place of Origin:
-
Fujian, China
-
Brand Name:
-
LN
-
Weight:
-
100 KG
-
Main coating methods:
-
Direct scraping coating
-
Working wheel face:
-
350 mm
-
Maximum operating line speed:
-
10m/min
-
After Warranty Service:
-
Video technical support, Online support
-
Local Service Location:
-
None
-
After-sales Service Provided:
-
Free spare parts, Online support, Video technical support
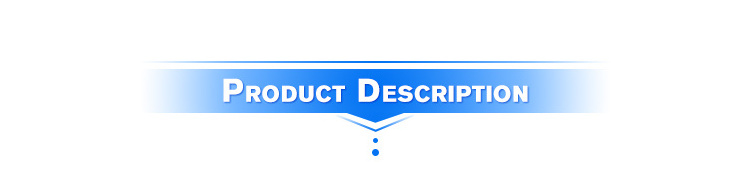
Laboratory Adhesive Solvent Coater Machine for Producing Coating of PET BOPP PP Paper Oily and Water-based Glue
Specification
1. Technical specification for laboratory coating
Applicable product
|
This production line is suitable for producing coating of PET, BOPP, PP, paper, etc. (suitable for scraping, etc.)
|
Mainly use raw materials
|
Substrate: PET, BOPP, PP, paper, etc
Glue: oily and water-based glue, etc
|
Main coating methods
|
Direct scraping coating
|
Mechanical specification
|
About L3000*W1000*H2150 mm
|
Working wheel face
|
350 mm
|
Maximum operating line speed
|
10m/min
|
Total power
|
Heating (electric heating mode) + power ≈20KW
|
2. Coating machine production line performance and technical parameters
Coating machine substrate width
|
250mm
|
Maximum external diameter of winding
|
¢200mm
|
Maximum external diameter of winding
|
¢200mm
|
Diameter of unwinding mandrel
|
¢3"
|
Coil mandrel size
|
¢3"
|
Coating uniformity dry adhesive
|
≤ 0.0025mm
|
Coiling edge uniformity end face alignment error
|
≤3mm
|
Production speed
|
0.5-10m/min
|
Machine speed
|
10m/min
|
Heating and drying mode
|
Electric heating (tunnel type hot air drying) ladder heating mode (low-high-low distribution)
|
Maximum adjustment temperature
|
180℃
|
Power
|
3 ¢2.11, 380 v, 50 hz
|
Compressed air source
|
6-8kg/cm2
|
Power suply
|
Three-phase alternating current of heat source.
|
Layout
|
Flat and straight layout of oven
|
3. Details of main equipment
No.
|
Item
|
1
|
The production line supports the body and accessories type 1
|
2
|
Single working position feeding machine 1
|
3
|
One straight scraping coating head
|
4
|
Oven (0.7m/section) 3 sections
|
5
|
Compound mechanism 1
|
6
|
One laminating feeding machine
|
7
|
One single shaft winding machine
|
8
|
Electronic control system type 1
|
9
|
Piping project type 1
|
10
|
Wiring engineering type 1
|
11
|
Piping engineering type 1
|
12
|
Transmission system type 1
|
4. Specification of 250mm multifunctional coating machine production line
Please refer to the attached drawing: "schematic diagram of 250mm coating machine"
Please refer to the attached drawing: "schematic diagram of 250mm coating machine"
The production line supports the body and accessories
|
The frame columns and girders are 50*50 square, and the beam is 50*50 square +10mm steel plate
|
Simplex unwinding machine
|
The maximum external diameter of the coil unloading is ¢200mm
Unwinding width 250mm Remove reel 1 piece Tension adjustment mode (using tension control) formula 1 One magnetic powder brake (2.5Kgm) |
Straight scraping coating head
|
Frame (&40 steel plate welding processing, symmetrical processing) 2 pieces
Scraper (diameter 100 scraper, hard chrome plating fine grinding) 1 piece Viscose wheel (diameter 180, hard chrome plating grinding) 1 piece Power (1KW servo motor + reducer) 1 set Bearing (imported from Switzerland) Hard chrome plating and fine grinding treatment for rubber plate 2 sets of scraper pneumatic mechanism 1 set of scraper positioning device Glue thickness adjustment mechanism pneumatic slider regulator Glue slot (stainless steel material) 1 piece (for discharging glue) 2 pieces of rubber plate (nylon material) |
Heat oven
|
The length of the oven unit 0.5 meters/day, a total of 3 day,
Oven skeleton with Angle, & 2 + 5 steel plate welding The inner wall of oven is made of stainless steel The wind tsui and bladder using 2 mm stainless steel plate production of the wind The wind tsui distance distance guide roller surface effective distance of 60 mm Temperature up to 180 ℃ (low, high and low trapezoid distribution) Thickness of insulation board is 50mm Guide roller diameter 60 aluminum alloy roller 2 pieces / 1 section (a total of 10 pieces, hard oxidation surface treatment) Black hair, oven outside the roller bearing structure, each wheel are driving force Power (0.75kw three-phase gear reducer motor) 1 set Frequency converter (1KW one tow two frequency converter) 1 set Transmission mode (belt type, high temperature resistant PU belt) 3 circulating fans (0.25kw, 4 poles) Frequency converter (1KW frequency converter) 3 sets Air inlet pipe (made of 0.75mm galvanized sheet) Three-phase alternating current at the heat source 3 exhaust fans (0.15kw 4-pole centrifugal fan) Vents with manual adjustment of air volume air valve Heat exchanger insulation board thickness of 50mm, internal stainless steel Heating wire domestic heating wire Pneumatic opening mechanism type 2 (type 1 contains a group of pneumatic mechanisms) |
Composite mechanism
|
The frame is made of &25 steel plate
Heating wheel (diameter 180, hard chrome plating on surface, heat conducting oil heating mode) 1 piece Rubber pressure wheel (surface covered with rubber, pneumatic drive, adjustable gap), ¢100mm 1 Pneumatic cylinder (50 * 75 cylinder bore) 2 Power (1) 0.75 KW three-phase ac motor type Inverter (0.75 KW inverter) 1 |
Simplex unwinding machine
|
Discharge volume ¢maximum diameter 200 mm
Unwinding width 250mm Remove reel 1 piece Tension adjustment mode (using tension control) formula 1 One magnetic powder brake (2.5Kgm) |
Single-shaft winding machine
|
Ejecting machine body 25 mm steel plate production, left and right sides is symmetrical processing
Discharge volume ¢maximum diameter 200 mm Unwinding width 250mm Remove reel 1 piece One winding motor (0.75kw gear reduction motor) Transmission mode gear type |
Electrical control system
|
Type of centralized control cabinet, a coating a head
Machine proportional linkage, sub - coating head, laminating, main power box three - point control mode 1 meter counter (electronic) 5 sets of temperature control devices, individual temperature control for each oven (domestic SCR throttling controller) Coating head, console, cooling mechanism, can automatically start, stop and speed adjustment, with emergency stop button, the whole machine adopts protective explosion-proof circuit design.Drive part of the inverter, fan speed converter.Tension control system adopts Taiwan and Japanese brands, main bearing adopts SKF brand imported from Switzerland and nissan line bearing, and the whole power system adopts gear reducer motor. Heating system Type electric heating mode |
Duct works
|
Exhaust fan adopts three 0.15 KWW centrifugal fan convulsions
Circulating fan three centrifugal fans Fan control mode starts and stops separately |
Driveline
|
Type AC motor with frequency converter control, feeding using automatic, semi-automatic tension control, winding for automatic
tension control Operation mode linkage of the whole machine 1. Coating head (with electric box) 2. Put volume 3. Cooling and recombination 4. Separate tension control for coiling (the tension control forms an action linkage with the host) |
5. Demander's own projects
Power supply
|
The power three-phase, 50 hz, 380 v
|
Air compressor
|
Air compressor or air compressor station, gas supply 2-6 kg/cm2 per hour
|
Exhaust fans
|
Construction of draft pipe between exhaust fans of coating machine body and installation of exhaust fans
|
Heat preservation
|
Heat preservation materials and construction of heating pipelines
|
Structure
|
Material and construction of coating machine body and heating source
|
On-site
|
The grounding resistance of the whole machine is less than 4 ohms and cannot be in common with the grounding wire of the lightning
protection system |
Self-provided1
|
The buyer shall provide test materials and corresponding glue
|
Self-provided2
|
Water supply system and installation of pipelines
|
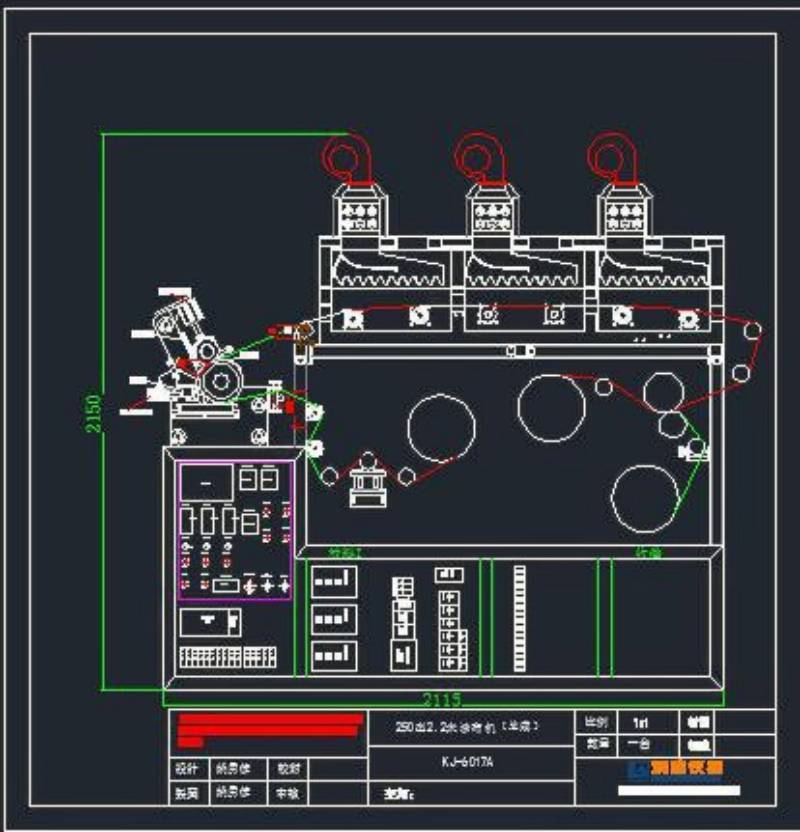
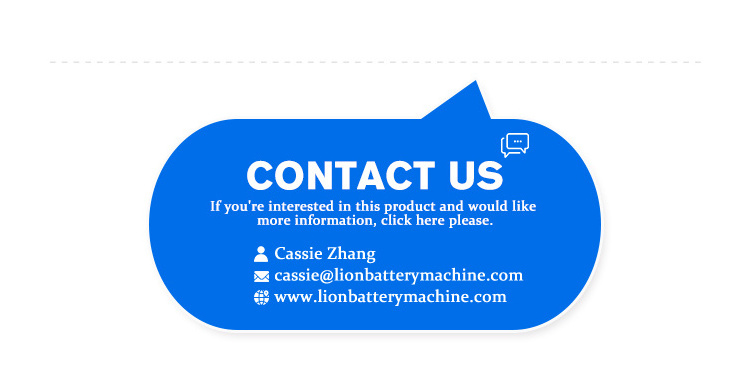
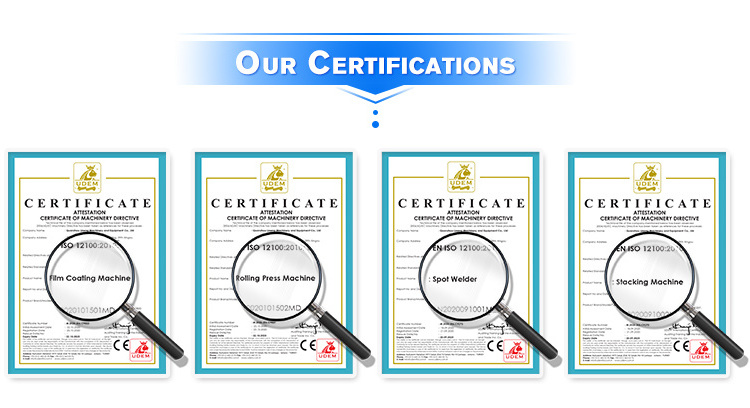
Hot Searches