The 2 in 1 can filler and sealer is developed on the basis of digesting and absorbing advanced technology introducing from abroad and is with international advanced level. It is mainly used for filling carbonated containing drink in tin cans, such as water, juice, soda water, soft drink,sparkling water and so on. The filling way is normal pressure. It adopts the automatic PLC touch screen control system, and the speed can be regulated forever as customer requirements within the scope. It is set with 24 filling heads and 6 sealing heads. The filling valves are adopted special for filling juice and pulp. It adopts the high quality of stainless steel 304 material, meets the requirements of food grade. It is full automatic and advanced in construction, steadily in performance, safe in operation, easy in maintenance, high in production efficiency. The filler is the ideal choice for drink factories of small and middle size.
- Product Details
- {{item.text}}
Quick Details
-
Filling Accuracy:
-
±2ml
-
Voltage:
-
0.3-0.7Mpa
-
Place of Origin:
-
Jiangsu, China
-
Brand Name:
-
Paima
-
Dimension(L*W*H):
-
2600*1965*2250mm
-
Weight:
-
5500 KG
-
Name:
-
canning machine
-
Bottle type:
-
aluminium can / metal can /
-
Capacity:
-
100-18000BPH
-
Feature:
-
High Precision Filling Level
-
Material:
-
SUS304/316
-
Control:
-
PLC+ Touch Screen
-
Operation:
-
Automatic Operation
-
Suitable for:
-
Can Filling Line
-
Filling volume:
-
150ml-750ml
-
Filling nozzles:
-
2/4/6/8/10/12(customized)
-
Marketing Type:
-
New Product 2021
Quick Details
-
Machinery Capacity:
-
Other, 400BPH, 500BPH, 100BPH, 200BPH
-
Packaging Material:
-
Plastic, Metal, Glass
-
Filling Material:
-
Beer, Milk, Water, Oil, Juice
-
Filling Accuracy:
-
±2ml
-
Voltage:
-
0.3-0.7Mpa
-
Place of Origin:
-
Jiangsu, China
-
Brand Name:
-
Paima
-
Dimension(L*W*H):
-
2600*1965*2250mm
-
Weight:
-
5500 KG
-
Name:
-
canning machine
-
Bottle type:
-
aluminium can / metal can /
-
Capacity:
-
100-18000BPH
-
Feature:
-
High Precision Filling Level
-
Material:
-
SUS304/316
-
Control:
-
PLC+ Touch Screen
-
Operation:
-
Automatic Operation
-
Suitable for:
-
Can Filling Line
-
Filling volume:
-
150ml-750ml
-
Filling nozzles:
-
2/4/6/8/10/12(customized)
-
Marketing Type:
-
New Product 2021
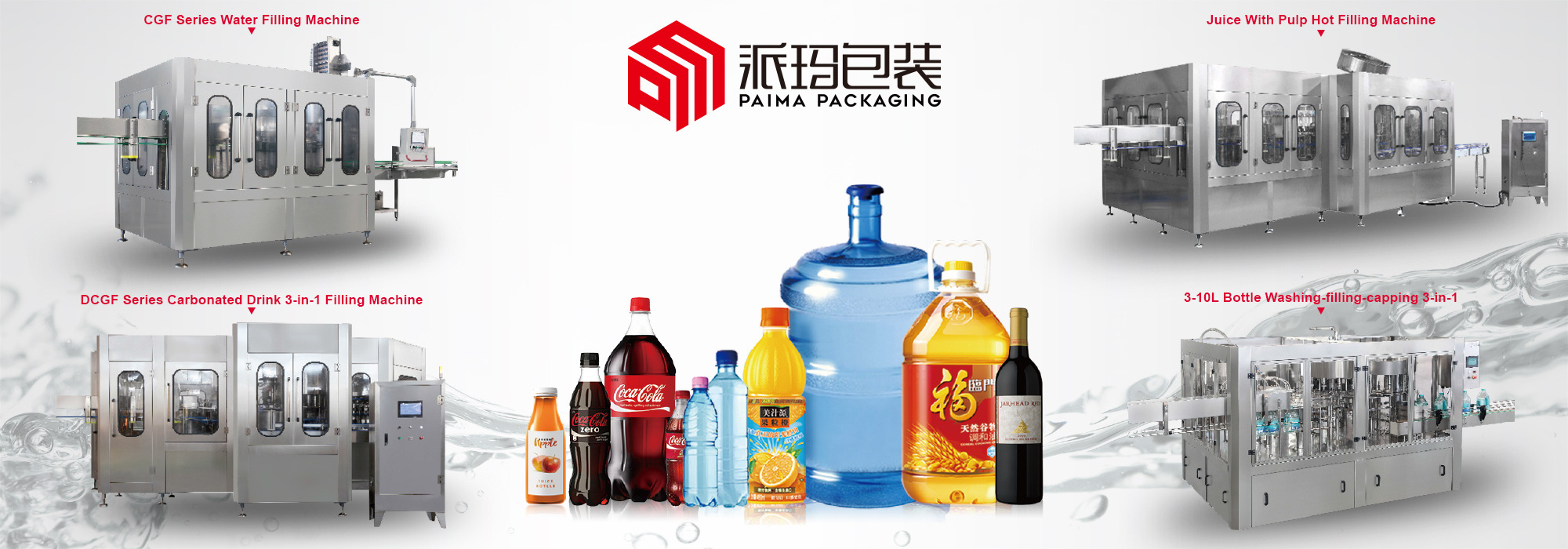
Product Description
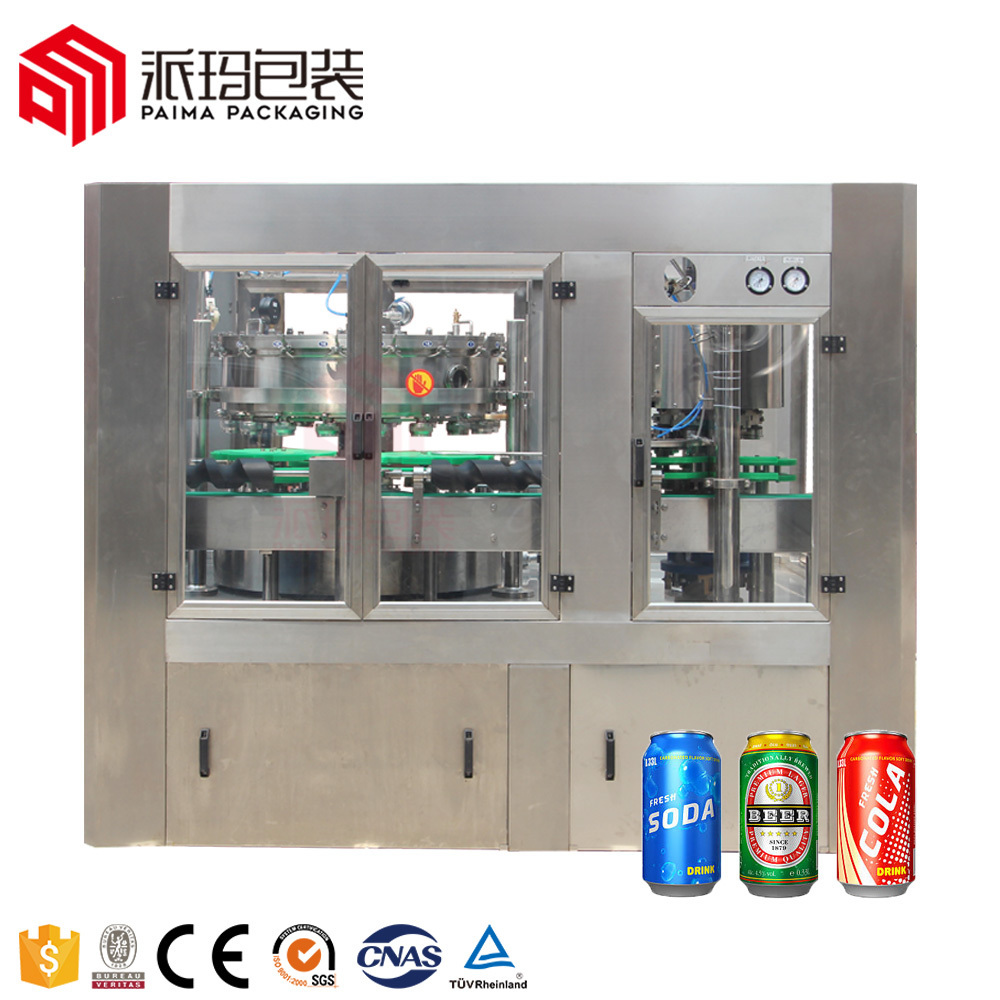
Brief introduction of can filling machine
Specification
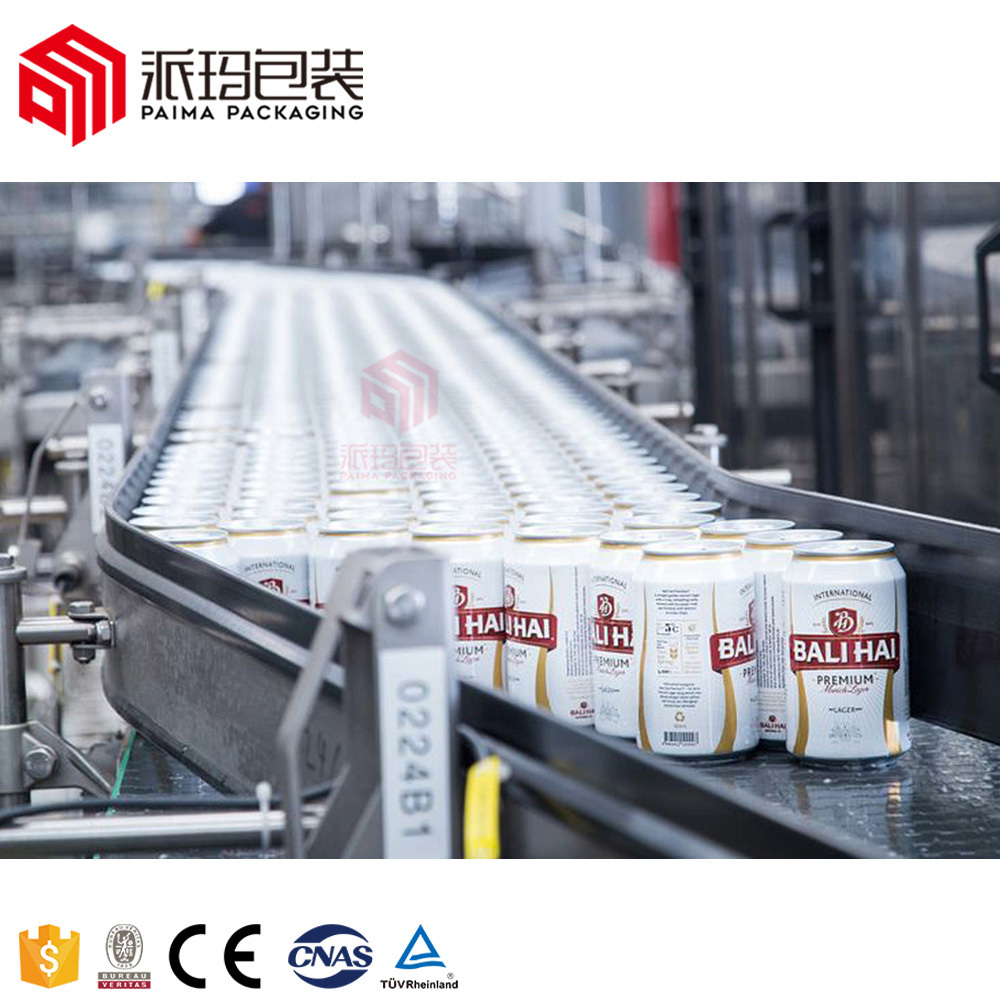
Soda drink / Sparkling beverage / Carbonated drink tin can filling machines
* Filling Temperature: 0~2°C
* CO2: 2~5 g/L
* Production Capacity: Up to 18000 cans/h (330ml/12oz)
Main Features of tin can filling machine
1、The machine adopts special filling valve, high power vacuum pump, low vacuum filling principle, filling against the bottle wall, no choking, no froth, to ensure the consistency of the liquid level after filling.
2、The bottle mouth is sealed when filling, the liquid flows down along the bottle wall, and the bottle with defective bottle is not filled automatically, which effectively controls the foam caused by the liquid impact when filling, prevents the liquid from overflowing, does not spill liquid, does not break the bottle, and the bottle height error is automatically adapted.
3、The machine frequency conversion speed regulation, filling speed, with overload protection device, card bottle stop, start soft start, the use of flexible bottle-holding device to reduce the breakage of bottles.
4、Filling system: The filling system includes filling valve (exhaust valve), filling cylinder, liquid level control device, cylinder for lifting the filling valve, filling cylinder height adjustment device, etc.
5、Transmission system: The power of this machine comes from the capping machine, and after changing the speed ratio by the first-level chain wheel transmission, it is passed to the reducer, and the gear on the output shaft of the reducer drives the filling cylinder and related parts.
6、Can feeding system: The inlet conveyor belt of this machine is self-assigned, and the outlet conveyor belt is assigned by the capping machine. The can feeding system includes can feeding screw, can stopping device, can feeding star wheel and various stopper parts.
7、Pipe control system: including liquid distributor, gas distributor, gas control cabinet and liquid inlet and CIP piping, etc.
8、Control system: The system is installed on the peripheral support of the filling machine circumference, and various devices to control the opening of the filling valve.
9、Rack and protective door: The rack is used to support and install the transmission system and other parts, and the machine is surrounded by protective cover.
Technical Parameters
Beer / soda can filling machine
|
|
|
|
|
||||
MODEL
|
PMCF-12-4
|
PMCF-20-4
|
PMCF-24-4
|
PMCF-30-6
|
||||
Capacity
(cans/min)
|
90
|
150
|
150
|
300
|
||||
Filling Heads
|
12
|
20
|
24
|
30
|
||||
Sealing Heads
|
4
|
4
|
4
|
6
|
||||
Power
|
3.5kw
|
5.5kw
|
5.5kw
|
7.5kw
|
||||
Overall Dimensions(L*W*H)
|
3350*2150*2100mm
|
3400*1950*1900mm
|
3350*2150*2100mm
|
3488*2288*2168mm
|
||||
Weight
|
3500kg
|
4000kg
|
5300kg
|
8000kg
|
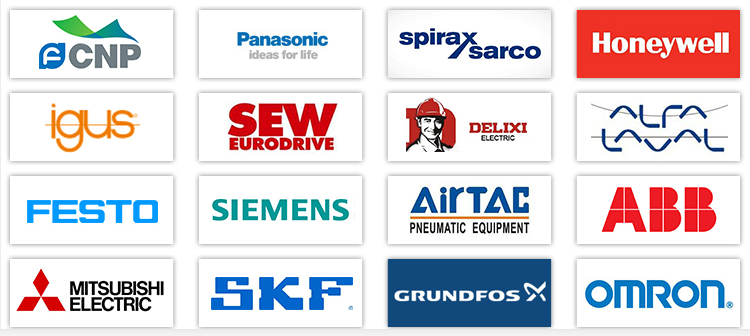
Devices
|
Brand
|
Origins
|
PLC
|
SIEMENS
|
Germany
|
Inverter
|
|
|
Touch Screen
|
|
|
Switch
|
|
|
Contactor
|
|
|
Relayer
|
|
|
Solenoid Valve
|
AIRTAC
|
Taiwan, China
|
Drive motor
|
FEITUO
|
Swiss
|
Reducer
|
CNP
|
China
|
Water Pump
|
SKF
|
China
|
Main Bearing
|
AUTONICS
|
Sweden
|
Sensor
|
AIRTAC
|
Korea
|
Air component
|
ABB
|
Taiwan, China
|
Details Images
Working Principles of can filling machines
The cans enter the filling machine through the inlet star wheel and reach the predetermined center behind the can table, then the
filling valve descends along the support cam to align and pre-pressure seal the cans, the sealing pressure is generated by a cylinder pressurized in addition to the weight of the centering cover itself, the air pressure in the cylinder can be adjusted by the pressure reducing valve on the gas control cabinet, the pressure is 0~40KPa (0~0.04MPa), the size of the pressure depends on the material of the cans. While opening the vacuum channel, the back pressure gas in the filling cylinder rushes into the tank and flows into the vacuum channel. Evacuation is used to implement the CO2 flushing procedure to remove the air from the cans. Through this procedure, the material is filled with minimum oxygenation and no negative pressure is generated in the cans, so even aluminum cans with very thin walls can go into the CO2 flushing.
For filling without vacuum, the filling machine can directly use the CO2 gas from the original vacuum channel to flush the cans directly. After the vacuum valve is closed, the can and the cylinder establish equal pressure, the liquid valve is opened by the spring and the filling starts. Through the three inlet slots, the material goes down the can wall, while the gas inside the can returns to the filling cylinder through the gas valve. By changing the length of the gas return pipe, the height of the filling liquid level is changed. When the liquid level of the material reaches the return tube, the return air is blocked and the filling stops, creating an overpressure in the upper gas part of the tank, thus preventing the material from continuing to flow down. Pull fork to close the gas valve and liquid valve, through the exhaust valve, the exhaust makes the pressure in the can balanced with the atmospheric pressure, the exhaust channel is far away from the liquid level, thus preventing the exhaust from bringing out the liquid. During venting, the gas at the top of the tank expands and the material in the return pipe falls back into the tank, emptying the return pipe. At the moment of discharging the can, the centering cover lifts up under the action of the cam, and the can leaves the can table under the action of the inner and outer guards and enters the capping machine delivery chain to the capping machine.
FILLING PARTS
1. The filling machine is designed and manufactured by our company by introducing German technology and applying the principle of
atmospheric pressure filling, which can realize the filling of liquid into the washed cans.
2. The filling adopts the gravity filling principle.
3. Filling valve adopts mechanical valve, with fast filling speed and high liquid level precision.
4. With perfect CIP cleaning function.
5. Adopt the combination of filling valve mouth with guiding device and bottle bottom lifting device to make the accurate sealing of bottle mouth and filling valve and reduce the phenomenon of material leakage from the can mouth.
6. According to the different heights of cans, manual lifting can be realized to meet the filling requirements.
7. Gear transmission is adopted for its high efficiency, low noise, long life, easy maintenance and sufficient lubrication.
8. Bottle guiding system, simple structure, can be changed quickly and easily according to the can type, the whole machine adopts can bottom structure conveying.
9. PLC automatic control of the whole machine, fault online display, such as blocked bottles, lack of lids, etc.
10. It has safety protection functions such as no cans, no valve opening, no lid adding and lid stopping.
11. Automatic control of material in the filling cylinder, the liquid level height is detected by liquid level sensor to make the liquid level stable.
SEAMING PARTS
a. The sealing part seals the lid on the filled cans and sends them to the later process by conveyor chain.
b. The sealing roller is hardened by high hardness alloy (HRC>62) and the sealing curve is precision machined by optical curve grinding to ensure the sealing quality and normal operation of the machine.
c. The machine has the control system of putting down the lid with cans and not putting down the lid without cans to ensure the normal operation of the machine and reduce the rate of lid loss.
d. Manually put the aluminum lid in the sliding groove and rely on the gravity of the lid and the thruster to lower the lid, and there is a detection switch in the sliding groove to stop the machine when the lid is missing.
e. According to the different height of cans, the capping machine can be lifted manually to meet the requirements.
Related Products
Complete soda can drink production line
1 / Preparing System (Aseptic water storage tank, Sugar melting tank & syrup filter, Flavour blending tank & syrup cooler, Flavour
blending tank & syrup cooler, Co2 drink mixer & Co2 filter, Water chiller )
2 / Water Treatment Syatem (quartz sand filter, active carbon filter, softner, RO system and so on)
3 / Empty can unloading machine
4 / Slide - type empty tank spray washer
5 / Can juice/csd drink filling sealing 2 in 1 monoblock
6 / Spray sterilizing chiller (including local control cabinet and electrical control device)
7 / Shrink labeling machine
8 / Wrapping machine
Water treatment system includes silica sand filter, active carbon filter, sodium ion exchanger, Ozone generator and UV Sterilizer,
RO machine (If mineral water, use hollow fiber filter). All these machines made by stainless steel food stage
Wide range of uses - The system can handle a wide range of products such as carbonated drinks, juice drinks, etc. Easy power adjustment - easy adjustment of mixing ratio without having to replace parts. Structural Hygiene - All parts in contact with fluids are of high-quality stainless steel, all tanks are equipped with a CIP ball for easy cleaning. Accurate mixing accuracy - product mixing accuracy G ≤ 2%.
Temperature control, control precision ±2℃
A flow meter make flow rate can be verified by observing the value; Manual valve on the operating surface, easy to control; Perfect control of cleaning time, improve cleaning efficiency; Reasonable layout, save space, improve cleaning efficiency.
Bottle Cooling Tunnel
Mainly for cooling and sterilization.
The main parts of the machine are made of stainless steel, the top is designed to be openable for easy maintenance and observation. Nozzles are manufactured using U.S. technology and spray water evenly. Conveyor belt adopts Reznor technology, flat surface with small wear. Smooth and reliable operation with low energy consumption.
Shrink Labeling Machine
This Shrink Sleeve Labeling Machine adopts international advanced technology, covers the circle label on the PET bottle, and then hot shrinking to fix the position which bottle body designated.
The shrink wrapping machine is specially designed for packing production line of beverage, drinking water, fruit juice, dairy products, etc .with full automatic functions of bottle transfer and arrange, membrane packing, sealing and cut, shrinkage, cooling and shaping, etc
Customer cases
We have a customer from Ethiopia who ordered a complete water line from water treatment to the back-end packaging equipment. And last year, when we went to Ethiopia to participate in the exhibition, we specially visited them. These are the real pictures we took from the our customer's factory.
Packing & Delivery
To better ensure the safety of your goods, professional, environmentally friendly, convenient and efficient packaging services will be provided.
Hot Searches