- Product Details
- {{item.text}}
Quick Details
-
Dimension(L*W*H):
-
4300*4000*2000mm
-
Power (kW):
-
2200kw
-
Weight (KG):
-
390000 kg
-
Warranty:
-
One Year
-
Raw material:
-
Reed, wood, saw dust, rice husk
-
Capacity:
-
30000cbm per year
-
Pre press machine:
-
press roller 900mm*2
-
Forming machine:
-
Width 1285~1320mm
-
Dryer:
-
Cylinder dia 2200mm
-
Edge trim saw:
-
Blade dia 250mm*2
-
Hot press cylinder number:
-
6 pcs
-
Sanding:
-
With sanding section
-
After-sales Service Provided:
-
Field maintenance and repair service
-
Auto:
-
Auto running
Quick Details
-
Place of Origin:
-
Shandong, China
-
Brand Name:
-
Ruifeng particle board production line
-
Voltage:
-
220V/380V
-
Dimension(L*W*H):
-
4300*4000*2000mm
-
Power (kW):
-
2200kw
-
Weight (KG):
-
390000 kg
-
Warranty:
-
One Year
-
Raw material:
-
Reed, wood, saw dust, rice husk
-
Capacity:
-
30000cbm per year
-
Pre press machine:
-
press roller 900mm*2
-
Forming machine:
-
Width 1285~1320mm
-
Dryer:
-
Cylinder dia 2200mm
-
Edge trim saw:
-
Blade dia 250mm*2
-
Hot press cylinder number:
-
6 pcs
-
Sanding:
-
With sanding section
-
After-sales Service Provided:
-
Field maintenance and repair service
-
Auto:
-
Auto running

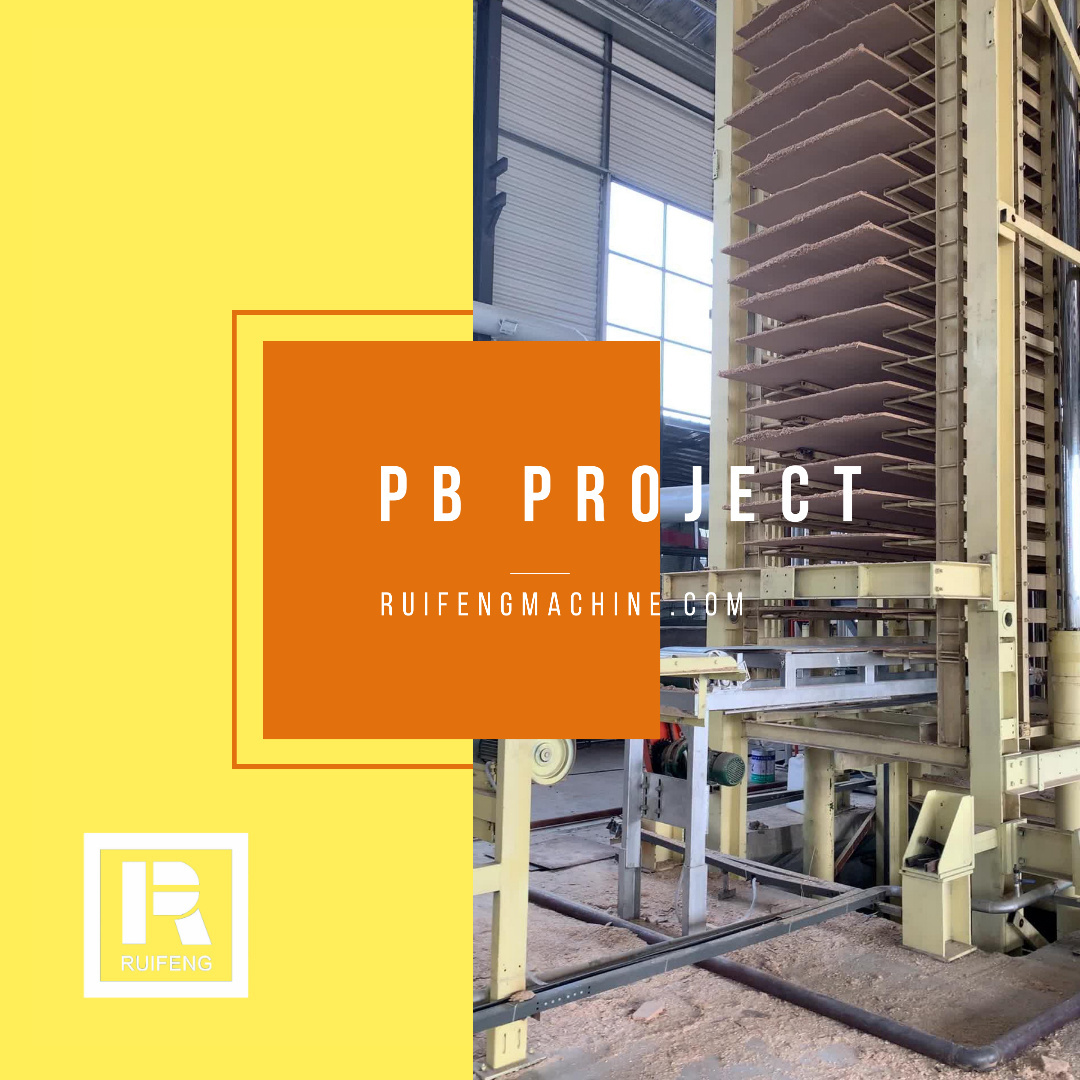
3 0,000 cbm Automatic Particle board production plant is the line to produce particle board with logs, branches, reeds, industrial wood waste as raw material. Applications include furniture, construction, pakaging, vehicles, ships and so on.
The main production process includes Flake prepareation, Drying and sifting section, Glue and forming section and Sanding section. Between each sections, there is electrical interlock, and when unlocked, single machines can be controlled individually.
This line is using wood as raw material to produce three layer structure particle boards. Besides, when facing the shortage of wood, other material like wood waste, bagasse, reed, cotton stem, and straws could be used as materials.
i Particle preparation
Wood are sent to the drum chipper feeding belt conveyor. The qualified chips cut by the chipper are sent to the bins for intermediate storage via the discharging belt conveyor.
Chips are conveyed to Pulverizer by a feeding conveyor, and are cut into qualified particles once and are delivered to the wet planer bin.
ii Drying and screening
Quantitatively output particles from wet bin are fed to a rotary dryer via a screw conveyor. The dried particles are then sent to a screen machine for screening by a screw conveyor. The selected rough particles are re-processed into a crushing machine, and together with the sieved core layer particles, are conveyed by a screw conveyor to air-separator. The screened qualified surface particles are wind delivered to the surface shavings silo. The qualified air-separated particles are sent to the core shavings store for intermediate storage.
iii Gluing
Core and surface layer is glued separately. The particles are quantitatively output from the silo, passed through a vibrating feeder, and continuously weighed by a
metering device and then evenly entered a ring-type mixer. The glue mixer fully mixes the incoming shavings with the atomized glue, uniformly applies the glue, and automatically adjusts the amount of glue according to the change of the amount of shavings, so as to keep the constant sizing rate.
iv Forming and Pressing
After sizing, the surface and core layer particles are sent via belt conveyor to the mobile airflow forming machine. Two groups of opposite airflow nozzles blow out the shavings to form the particleboard slab with a fine and uniform upper and bottom layers and size-grade structure. The formed chipboard is cut to the required length by a cross-cut saw, and the chips are fed back to the paving
machine via an air delivery system. After the single-layer hot press completes the hot pressing, the synchronously forming conveyor transports the blank board out of the press, meanwhile feed the slab into the press. Unqualified slabs will be returned to the wet silo via recycling devices for reuse.
v Post processing
The pressed slab enters the output roller conveyor with scales, is centered and weighed. And then the blank board is transmitted to the vertical and horizontal saws. Scraps will be returned to the wet silo. The board is transported via the roller conveyor to the forklift roller table and then forklift to the intermediate storage.
The stored board is sent to the sanding system. The sanding system consists of a hydraulic lifting platform, a roller conveyor, and a wide-belt sander. After sanding, the finished board is inspected and graded and sent to the finished product warehouse.
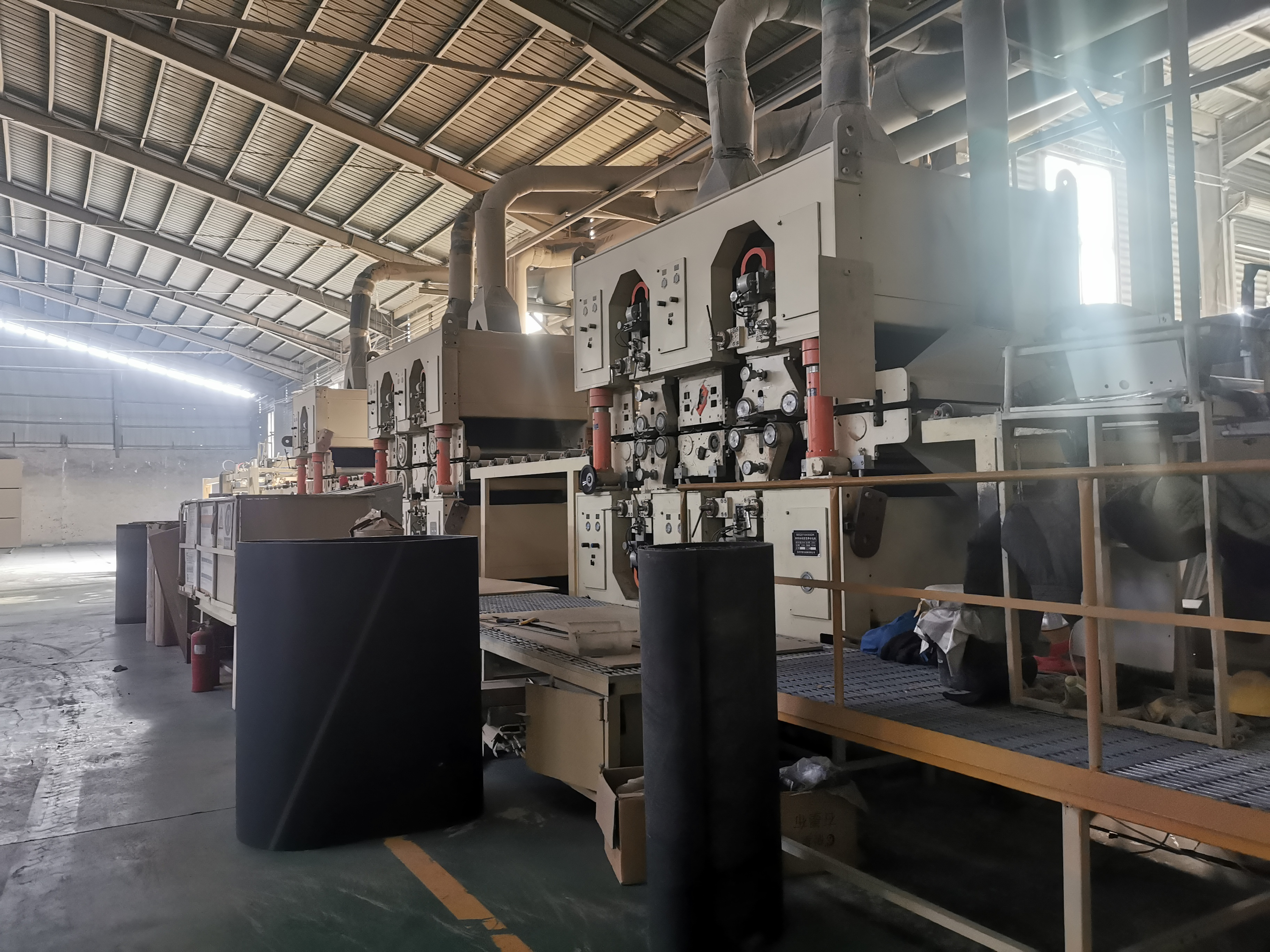
Product with different raw material:
(Reed particleboard sample)
Technical Data
Product name | 30,000cbm Automatic Particle board production plant |
Raw material | Wood, wood waste, rice straw, cotton stalk, reed, bagasse etc. |
Annual capacity | 30,000cbm (300 working days per year, 22 working hours per day) |
Board size | 1220*2440mm/1860*2700mm |
Board thickness | 8~25mm |
Main machines | Forming machine, Pre-press, Hot press, Sanding machine, Short cycle melamine lamination press |
Total power | 2200kw |
Overall size | As design |