- Product Details
- {{item.text}}
Quick Details
-
Model Number:
-
JC
-
Product materials:
-
PDCPD
-
Mould material:
-
Aluminium/Steel Mold
-
Mould Life:
-
5000-100000 shots
-
Mould type:
-
Reaction Injection Moulding(RIM)
-
Drawing Format:
-
2D/(PDF/CAD)3D(IGES/STEP)
-
Surface treatment:
-
Painting
-
Design:
-
3D CAD STP OEM ODM
-
Size:
-
Customized Size
-
Cavity:
-
Single Cavity\ Multiple Cavity
Quick Details
-
Shaping Mode:
-
Reaction Injection Moulding
-
Place of Origin:
-
Jiangsu, China
-
Brand Name:
-
Jingchuang
-
Model Number:
-
JC
-
Product materials:
-
PDCPD
-
Mould material:
-
Aluminium/Steel Mold
-
Mould Life:
-
5000-100000 shots
-
Mould type:
-
Reaction Injection Moulding(RIM)
-
Drawing Format:
-
2D/(PDF/CAD)3D(IGES/STEP)
-
Surface treatment:
-
Painting
-
Design:
-
3D CAD STP OEM ODM
-
Size:
-
Customized Size
-
Cavity:
-
Single Cavity\ Multiple Cavity
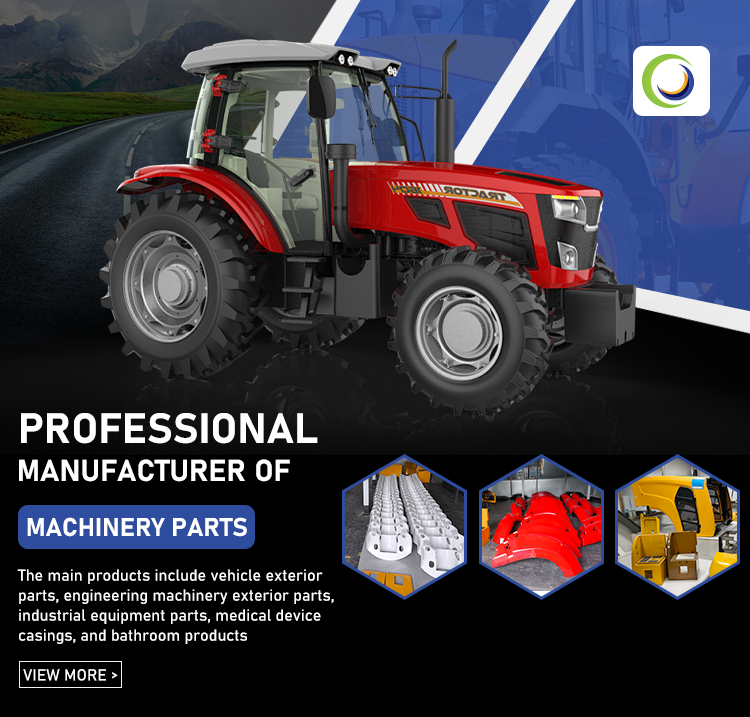

Shaping Mode
|
Reaction Injection Moulding
|
Product Material
|
PDCPD DCPD PDCP
|
Product
|
Vehicle Mould
|
Product materials
|
PDCPD
|
Mould material
|
Aluminium/Steel Mold
|
Mould Life
|
5000-100000 shots
|
Mould type
|
Reaction Injection Moulding(RIM)
|
Drawing Format
|
2D/(PDF/CAD)3D(IGES/STEP)
|
Surface treatment
|
Painting
|
Design
|
3D CAD STP OEM ODM
|
Size
|
Customized Size
|
Cavity
|
Single Cavity\ Multiple Cavity
|
Polydicyclopentadiene (PDCPD) is an "environmentally friendly material" widely used in chemical piping, sanitary ware,
kayaks,automotive interior and exterior parts, hoods, bumpers, medical equipment, etc. The density of 1.03g/cm³ realizes the goal of lightweighting, and the single size can be completed in 4m of product. It is characterized by high design freedom, high impact resistance and good rigidity, and is resistant to low temperatures up to minus 40 degrees Celsius, making it suitable for use in cold regions of the northern hemisphere. It can also well reflect the design intent; excellent mounting structure is easy to assemble and ensure high assembly quality; at the same time, the mold development cost of large products is greatly reduced than the traditional injection molding process, which is more suitable for small and medium-sized mass production, such as new energy and so on.
kayaks,automotive interior and exterior parts, hoods, bumpers, medical equipment, etc. The density of 1.03g/cm³ realizes the goal of lightweighting, and the single size can be completed in 4m of product. It is characterized by high design freedom, high impact resistance and good rigidity, and is resistant to low temperatures up to minus 40 degrees Celsius, making it suitable for use in cold regions of the northern hemisphere. It can also well reflect the design intent; excellent mounting structure is easy to assemble and ensure high assembly quality; at the same time, the mold development cost of large products is greatly reduced than the traditional injection molding process, which is more suitable for small and medium-sized mass production, such as new energy and so on.
Reaction injection molding (RIM) is used for TELENE1600/1700 series. RIM essentially involves a two-liquid system:liquid A is dicyclopentadiene (DCP) with a catalyst activator and additive, and liquid B is DCP with a catalyst, additive,
and polymerization initiator.
Liquids A and B are pumped through pipes into a mold. They are impingement-mixed at an even volume rate using a mixing head located at the bottom of the mold and then injected into the mold (3~5kgf/cm®2).Once liquids A and B
are impingement-mixed, the catalyst and catalyst activator initiate a chemical reaction that completes inside the mold
in only a few minutes. The reaction generates heat and the molded product is heated to nearly 200°C; therefore,it should
be allowed to cool to about 100°C before being removed. The entire process, from injecting liquids A and B to removing the molded product, is completed in only about five minutes.
and polymerization initiator.
Liquids A and B are pumped through pipes into a mold. They are impingement-mixed at an even volume rate using a mixing head located at the bottom of the mold and then injected into the mold (3~5kgf/cm®2).Once liquids A and B
are impingement-mixed, the catalyst and catalyst activator initiate a chemical reaction that completes inside the mold
in only a few minutes. The reaction generates heat and the molded product is heated to nearly 200°C; therefore,it should
be allowed to cool to about 100°C before being removed. The entire process, from injecting liquids A and B to removing the molded product, is completed in only about five minutes.
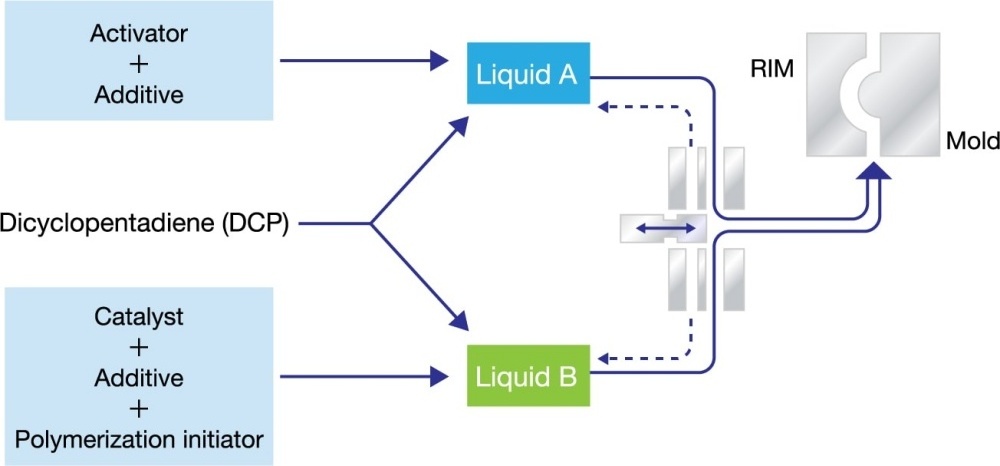
The DCP-RIM process is suitable for manufacturing large-scaled molded products with complex shapes in a very short period and offers remarkable energy saving advantages. TELENE is an environmentally sound olefin thermosetting resin with well-balanced properties that respond to today’s need. ®
TELENE1600/1700 series for large-scale molding is used for the body parts of trucks, buses, construction and agricultural
equipment, and other products because it is lightweight, resistant to impact, heat, water, and chemicals, and provides electrical insulation. And due to its excellent water and chemical resistance, it is also used for seawater pump casings, combined septic tanks, and other environment-related products.
TELENE1600/1700 series for large-scale molding is used for the body parts of trucks, buses, construction and agricultural
equipment, and other products because it is lightweight, resistant to impact, heat, water, and chemicals, and provides electrical insulation. And due to its excellent water and chemical resistance, it is also used for seawater pump casings, combined septic tanks, and other environment-related products.
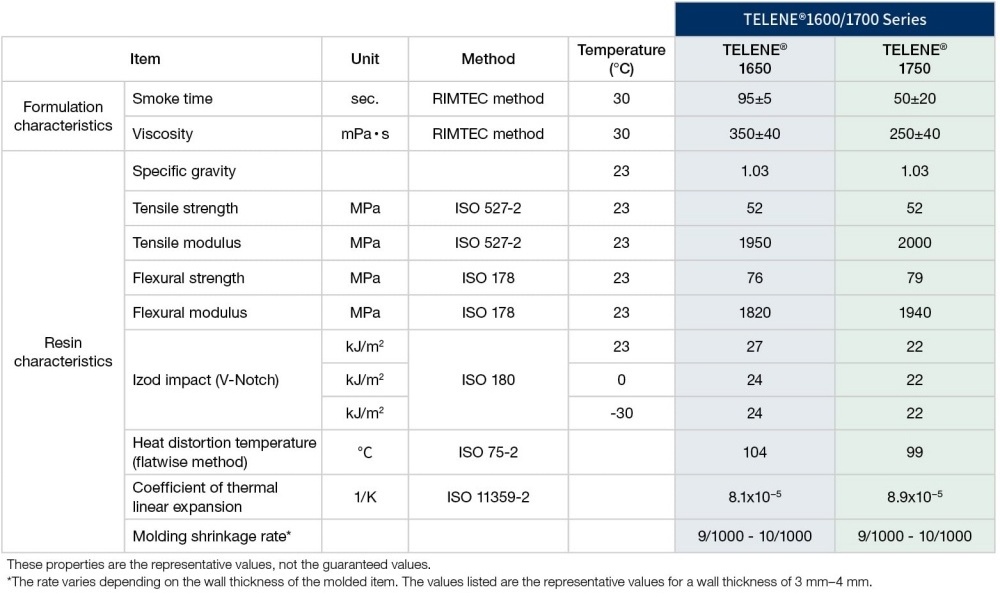
Hot Searches