- Product Details
- {{item.text}}
Quick Details
-
Voltage:
-
110V - 440V
-
Power:
-
52Kw-180Kw
-
Weight:
-
6840 KG
-
Dimension(L*W*H):
-
customizable
-
Dryer Heating source:
-
oil, gas, electric, steam
-
Raw material:
-
Bone Meal,flour
-
Material:
-
Stainless Steel
-
Feature:
-
High Efficiency Low Cost
Quick Details
-
Marketing Type:
-
New Product 2023
-
Place of Origin:
-
Shandong, China
-
Brand Name:
-
Linyang
-
Voltage:
-
110V - 440V
-
Power:
-
52Kw-180Kw
-
Weight:
-
6840 KG
-
Dimension(L*W*H):
-
customizable
-
Dryer Heating source:
-
oil, gas, electric, steam
-
Raw material:
-
Bone Meal,flour
-
Material:
-
Stainless Steel
-
Feature:
-
High Efficiency Low Cost
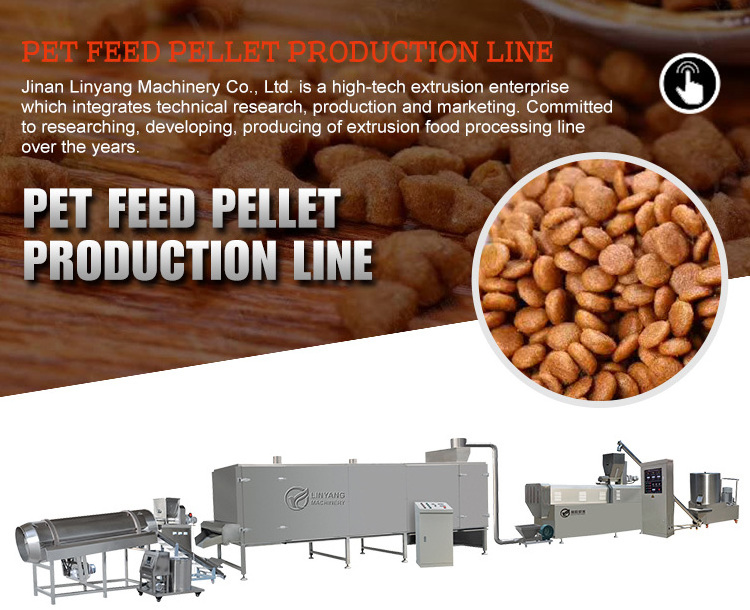
Pet Feed Pellet Making Equipment:
The dog food production line can divide into electrical type and steam type which according to the extruder heating method. The capacity can up to 100-5000kg/h. This production line can produce all kinds of products with different shapes by changing the mold as bone, heart, circular, triangle and others shapes. Also our customers can customized the mold to produce different shape and size dog feed.
Our company according to the pet food market demands to design and develop lots of models of pet food production line. According to the different capacity, we can provide all kinds of configuration production line for our customers.
This production line can produce the novel shape, unique taste, rich nutrition and delicate tissue pet feed according adjust the raw material, temperature, water and other technology parameter which can suitable for various pet taste.
The dog food production line can divide into electrical type and steam type which according to the extruder heating method. The capacity can up to 100-5000kg/h. This production line can produce all kinds of products with different shapes by changing the mold as bone, heart, circular, triangle and others shapes. Also our customers can customized the mold to produce different shape and size dog feed.
Our company according to the pet food market demands to design and develop lots of models of pet food production line. According to the different capacity, we can provide all kinds of configuration production line for our customers.
This production line can produce the novel shape, unique taste, rich nutrition and delicate tissue pet feed according adjust the raw material, temperature, water and other technology parameter which can suitable for various pet taste.
Raw Material: Fish meal, Soybean Meal, Wheat, Flour, Corn Powder, Rice Powder, Meat and others.
Voltage: 380V/50HZ We can customized according our customer's local voltage.
Machine Material: All the machine are made by stainless steel.
Product Name
|
Pet Feed Production Line
|
Style
|
Full Automatic
|
Brand
|
LINYANG
|
Colour
|
Sliver
|
Raw Material
|
Wheat, Flour, Soybean Meal, Meat and others
|
Place of Product
|
Shandong Province,China
|
Material
|
Stainless Steel
|
Modes of packing
|
Packed in wooden case
|
Size
|
17*1.3*2.2M
|
After sale service
|
Field installation, commissioning and training
|
Product Description
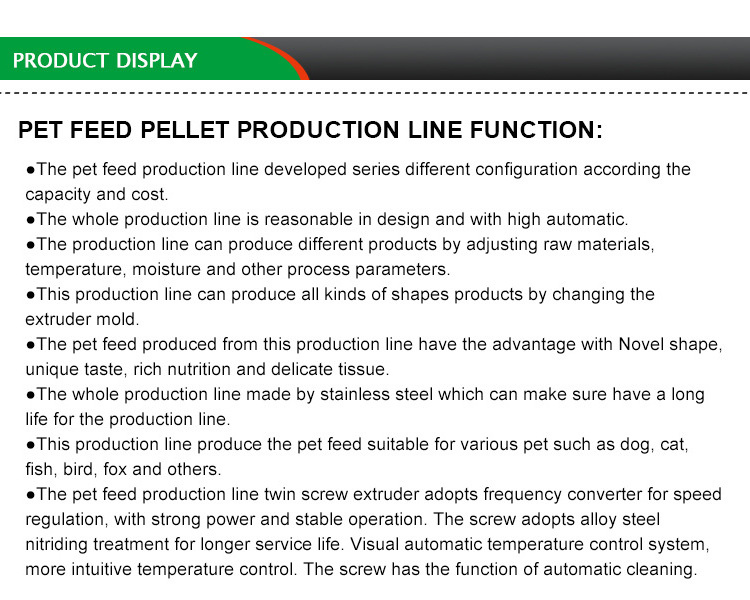
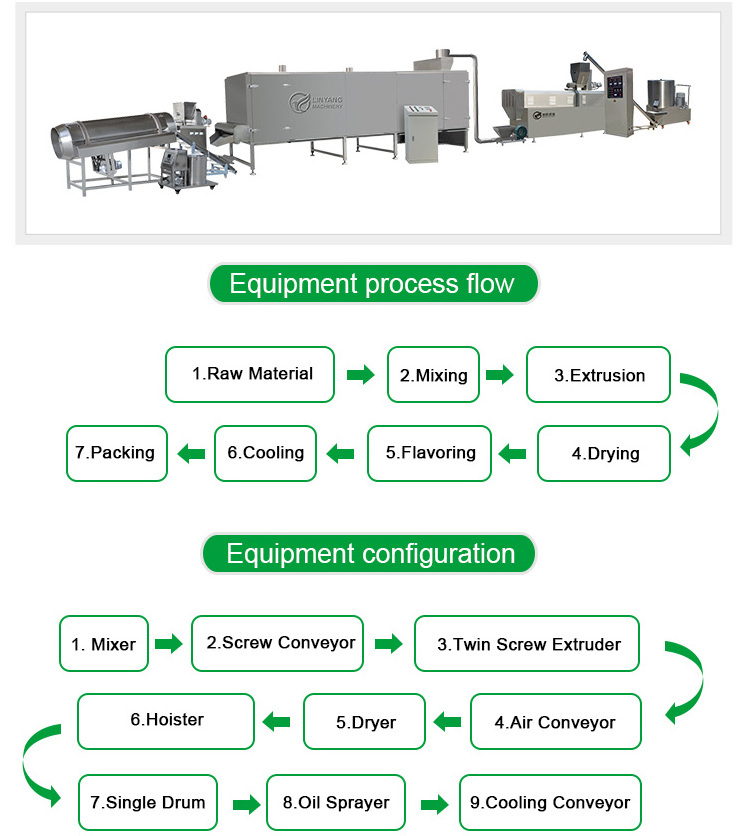
Model
|
LY65
|
LY70
|
LY85
|
LY95
|
Installed Power
|
74KW
|
105KW
|
205KW
|
255KW
|
Power Consunption
|
52KW
|
75KW
|
150KW
|
180KW
|
Production Capacity
|
100-150KG/H
|
200-260KG/H
|
400-500KG/H
|
800-1000KG/H
|
Dimension
|
17*1.3*2.2M
|
20*1.5*2.2M
|
30*1.5*2.6M
|
35*2.0*2.6M
|
Operation Process
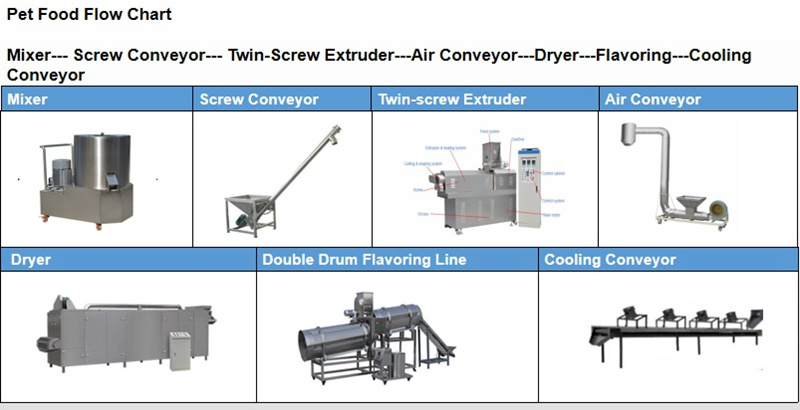
Operation
Actual shooting
Different Configuration
Model
|
LY65
|
LY70
|
LY85
|
LY95
|
Installed Power
|
74KW
|
105KW
|
205KW
|
255KW
|
Power Consumption
|
52KW
|
75KW
|
150KW
|
180KW
|
Production Capacity
|
100-150KG/H
|
200-260KG/H
|
400-500KG/H
|
800-1000KG/H
|
Dimension
|
17*1.3*2.2M
|
20*1.5*2.2M
|
30*1.5*2.6M
|
35*2.0*2.6M
|
If you need larger capacity, we can provide the customized services according our customer's demands with 100-10000kg/h.
Samples
Advantages of twin Screws extruder
1. The adaptability of raw materials is wider, and they can self regulate high viscosity, low viscosity, high fat content, high moisture or viscosity, oily, very wet and other raw material processing, which may slip in single screw .
2. The particle size limit of raw materials is relatively small, and the processing of raw materials with self adjustable particle sizes ranging from micro powder to coarse powder particles and single screw processing can be carried out.
3. Regardless of whether steam, water or other auxiliary production processes are added, the material flow inside the machine barrel can be more evenly distributed to obtain a more accurate proportion, achieving the actual required effect.
4. The product has good internal and external quality and can achieve a good homogeneous state, making the molecular structure of the material evenly distributed. During the extrusion process, the appearance is smooth, and the product particles have high uniformity and good uniform distribution.
5. The homogenization and maturation effect is good. Usually, the maturity of starch can reach over 95%, which keeps processed aquatic feed stable in water, prevents nutrient loss, and facilitates digestion and absorption.
6. Under the same power, the output is higher. Good mixing performance timely and evenly distributes the heat obtained by the material, accelerates the maturation of the material, reduces temperature fluctuations of the material, and improves the yield of extruded expansion products.
7. The product has a wider range of diversity and adaptability, and can be processed into aquatic feed, high oil formula, high moisture content, high viscosity, multi-color, sandwich, and special shaped products.
8. The process operation is relatively simple, and the spindle speed can be adjusted according to the needs of the processed product. Due to the characteristics of self-cleaning, cleaning is very convenient, and there is no need to disassemble the equipment after each processing.
9. The wear of vulnerable parts is relatively light, and the generally incorrect concept is that single screw wear is less. In fact, due to the stable material transportation and flow characteristics during twin-screw extrusion, the wear of screws and cylinder sleeves is less than that of single screws. Although there are more screws, the cost of accessories is still lower than that of single screws.
10. The production cost is relatively low. Due to the good operational stability of the twin-screw model, there are fewer starting materials, less water and gas waste, fewer working hours, high heat transfer efficiency, high yield, high power output indicators, and low accessory costs during feed processing. The final production cost is much lower than that of a single screw.
Packing And Delivery
Hot Searches