- Product Details
- {{item.text}}
Quick Details
-
Brick size:
-
600*200*200mm, 600*300*200mm, 600*100*200mm
-
Place of Origin:
-
Guangxi, China
-
Brand Name:
-
HONGFA
-
Voltage:
-
220/380/440V
-
Dimension(L*W*H):
-
A Whole Production Line
-
Marketing Type:
-
Hot Product 2023
-
Weight (KG):
-
90000 kg
-
Brick type:
-
Autoclaved Aerated Concrete Brick
-
Weight:
-
400-800kq/CBM
-
Motor brand:
-
Siemens
-
Operate style:
-
Automatic
-
Worker:
-
8-10
-
Color:
-
Customer's Request
Quick Details
-
Type:
-
Autoclaved aerated concrete block (AAC)
-
Brick Raw Material:
-
Cement
-
Production Capacity (Pieces/8 hours):
-
50000-300000CBM/Year
-
Brick size:
-
600*200*200mm, 600*300*200mm, 600*100*200mm
-
Place of Origin:
-
Guangxi, China
-
Brand Name:
-
HONGFA
-
Voltage:
-
220/380/440V
-
Dimension(L*W*H):
-
A Whole Production Line
-
Marketing Type:
-
Hot Product 2023
-
Weight (KG):
-
90000 kg
-
Brick type:
-
Autoclaved Aerated Concrete Brick
-
Weight:
-
400-800kq/CBM
-
Motor brand:
-
Siemens
-
Operate style:
-
Automatic
-
Worker:
-
8-10
-
Color:
-
Customer's Request
Product Description
Autoclaved Aerated Concrete Block Production Line
What is the Autoclaved Aerated Concrete?
·Aerated concrete is a porous silicate product made of siliceous and calcareous materials as the main raw materials, mixed with aerating agent, stirred with water, formed pores by chemical reaction, and made through the process of casting and molding, pre-cultivation and cutting, autoclave maintenance, and so on.
What are the advantages of AAC bricks?
·Light weight: 400~700kg/m³
·Good thermal insulation performance: thermal conductivity 0.09~0.22W/(m.k)
·Good fire resistance without emission of harmful gases
·Machinability
·Wide source of raw materials, high production efficiency, low energy consumption
What are the advantages of AAC bricks?
·Light weight: 400~700kg/m³
·Good thermal insulation performance: thermal conductivity 0.09~0.22W/(m.k)
·Good fire resistance without emission of harmful gases
·Machinability
·Wide source of raw materials, high production efficiency, low energy consumption
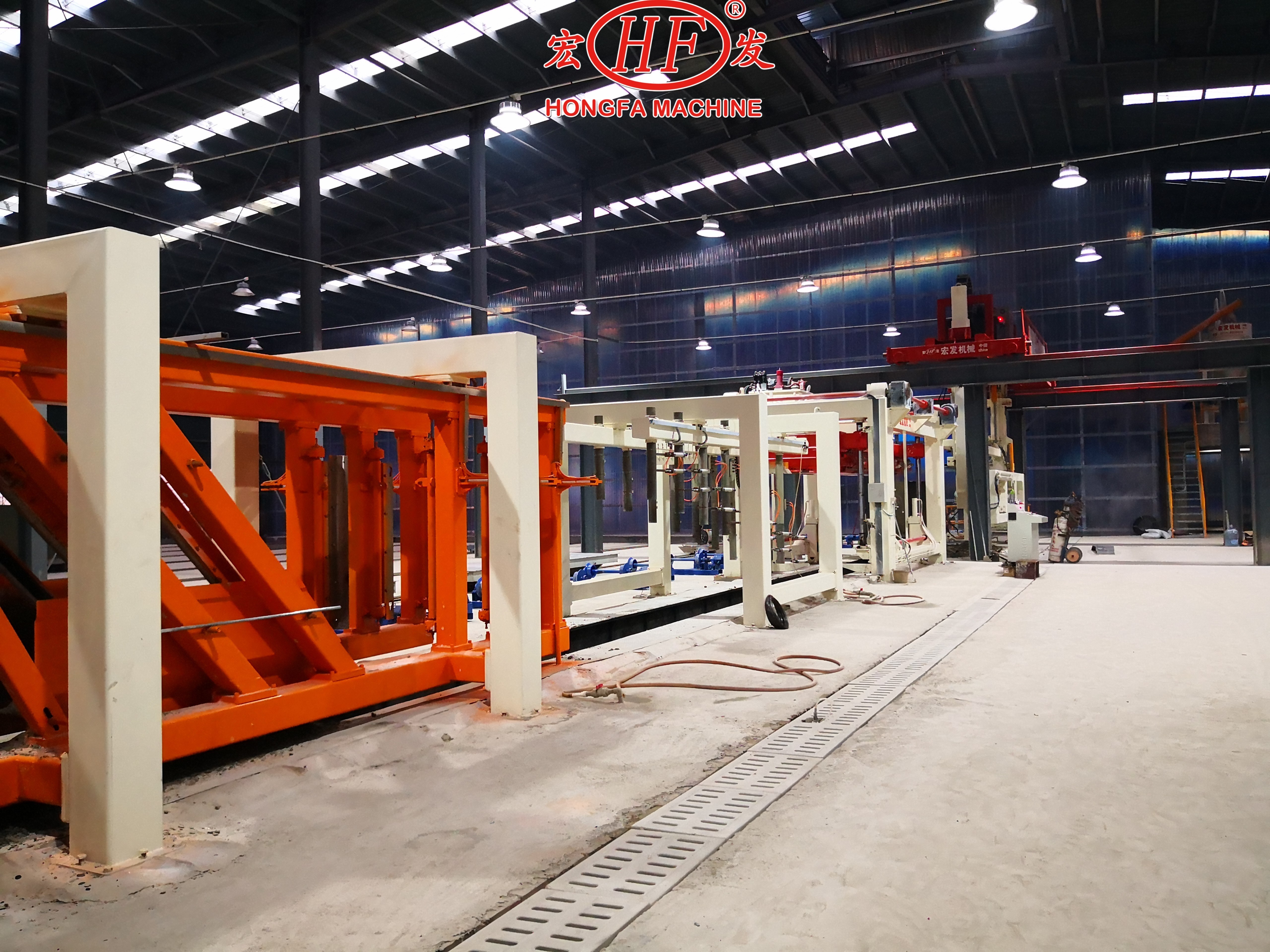
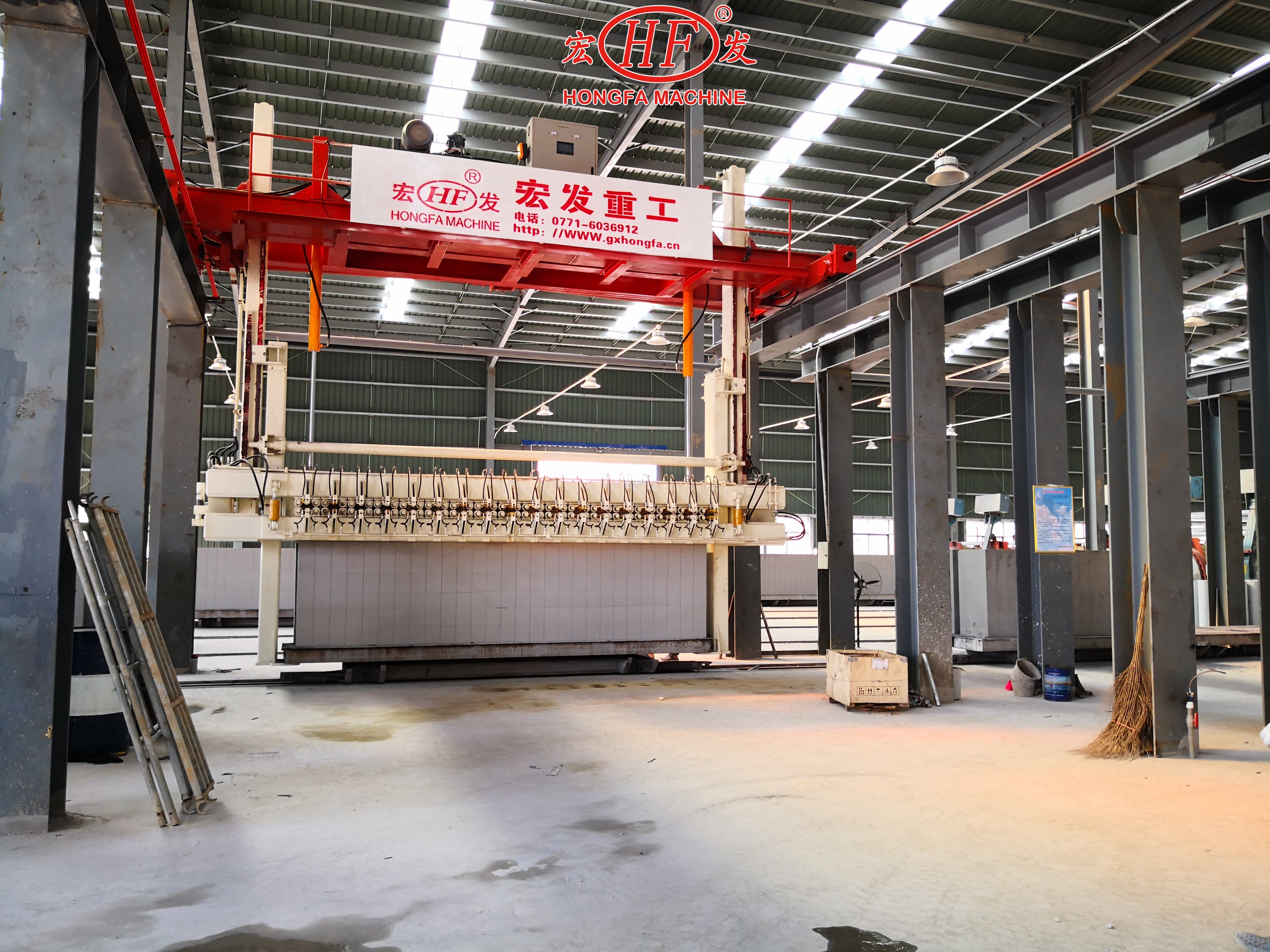
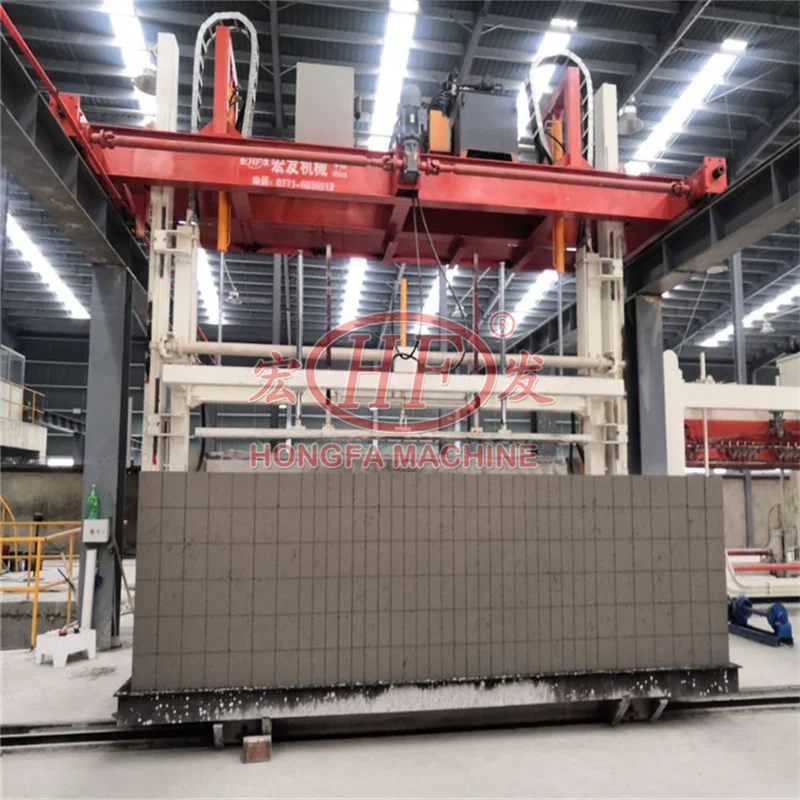
Our Advantages
·It can realize mixing and grinding to prepare cementitious materials, and effectively improve the stability of casting; infusion
cylinder casting mixing, so that the mixing time is shortened, and greatly improve the uniformity of mixing.
·Staggered dosage process, the dosage building is divided into two, staggered arrangement of high and low, to simplify the
arrangement of equipment and architectural structure, to meet the staff space and equipment layout requirements.
Full View Of The Production Line
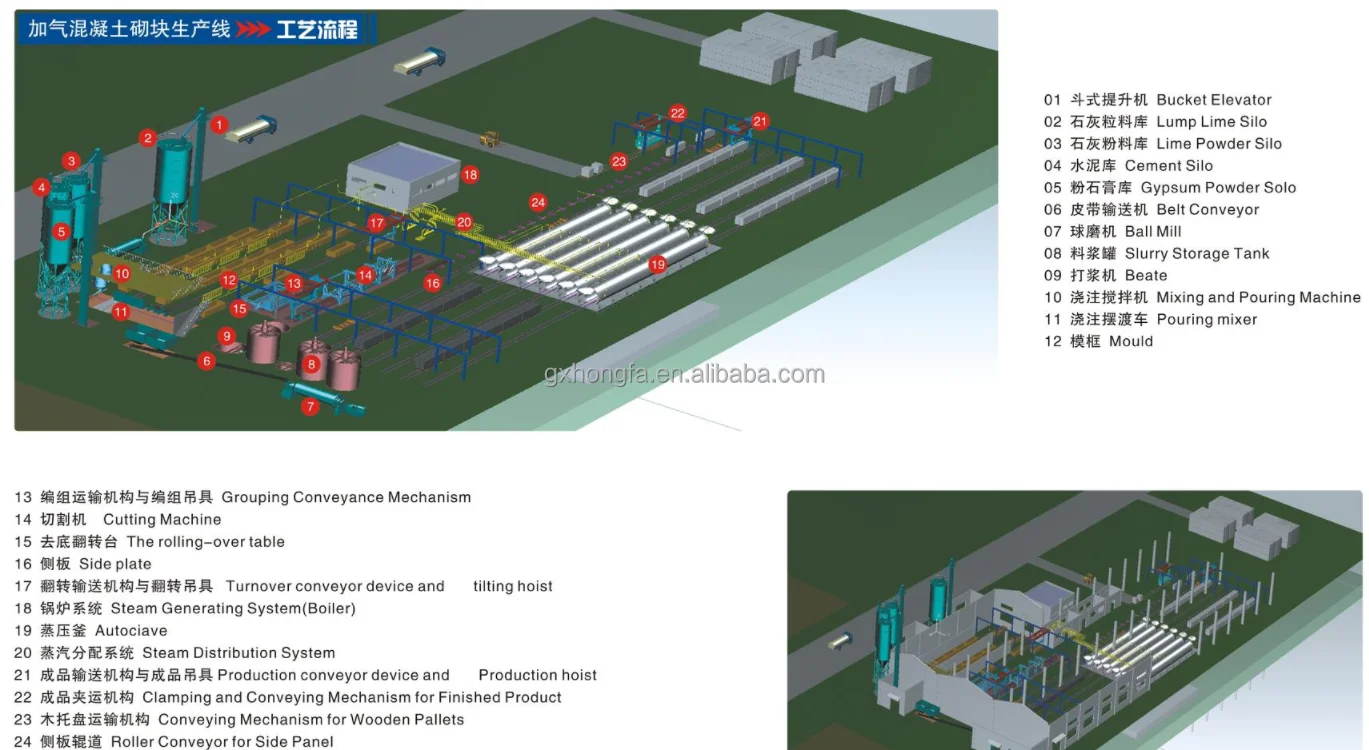
Products Details
Process Flow And Material
Sand (65-70%):
The core raw material of AAC product; the main resource of silica-aluminum components; correspond with JC409-91,the clay should less than 4%.
Lime(12-20%):
One of the main raw materials of fly ash AAC; the main effect is to provide efficient calcium oxide with cooperation of cement making calcium oxide react with SiO2, Al2O3 in hot water then to produce calcium silicate hydrate. Therefore, lime is also the main resource of strength. Effective calcium oxide of lime should not less than 65%, over 80% is perfect and should accord with JC/T621-1996.
Cement(8-10%): This Project aims to utilize OPC cement as main binder material. It will give faster strength to the bricks, besides giving improved consistent quality. It also ensures a better cost effectiveness for the same. Using OPC will be a standardized practice. The other prime advantages of using OPC (compared to other binders) is it’s easy availability locally through nationwide Retail Network of Cement Companies.
Gypsum(1-2%): Gypsum is the foaming regulator in AAC which dispels quicklime and postpones slurry’s densification.CaSO4 should be more than 70%.
Aluminum Podwer(0.074%): It is the forming agent type and recommendation for supply depend on raw materials and mix formula:A lot has been said about this raw material in this Project Profile itself. But this Raw material is freely available in Thermal Power plants. There are no taxes on this item whatsoever. Transportation charges are only to be attended by the entrepreneur.
Cement(8-10%): This Project aims to utilize OPC cement as main binder material. It will give faster strength to the bricks, besides giving improved consistent quality. It also ensures a better cost effectiveness for the same. Using OPC will be a standardized practice. The other prime advantages of using OPC (compared to other binders) is it’s easy availability locally through nationwide Retail Network of Cement Companies.
Gypsum(1-2%): Gypsum is the foaming regulator in AAC which dispels quicklime and postpones slurry’s densification.CaSO4 should be more than 70%.
Aluminum Podwer(0.074%): It is the forming agent type and recommendation for supply depend on raw materials and mix formula:A lot has been said about this raw material in this Project Profile itself. But this Raw material is freely available in Thermal Power plants. There are no taxes on this item whatsoever. Transportation charges are only to be attended by the entrepreneur.
Main Parts of Production Line
Raw material dealing
Put the fly ash or sand into the ball mill to mill via the conveyor belt, after milling, put the slurry into the slurry storage tank by slurry pump.
Batching, mixing and pouring process
The lime, cement will convey by conveyor to the dry powder measure scale to scale separately. The slurry convey by slurry pump then to the automatic scale;the power and slurry put into the mixer,pouring into the mould.
Curing process
After slurry pouring into the mould, put the mould box into the curing room with 50~70℃. After 2-3 hours curing, the blocks become soft solid and ready for cutting.
Cutting process
Cutting size can be adjusted flexibly, Crushing rate is almost 0.
Aerated autoclaved process
Finished cutting using semi-product crane carry to the front of autoclave grouped, hoisting machine or dragger will drag steam trolley into autoclave to steam,it need 6-10 hours.
Finished block dealing process
After 6-10 hours, finished products come out of autoclave, with separting machine to separate blocks layer by layer.
Product Application
Our Services
Pre-sales services
*
Price inquiry and technology consultancy.
* Provide you with professional and customised solutions according to your needs.
* Factory site visit. We are a real manufacturer and have our own factory, you can see the machines and production.
Services during sale
* Assist customers with factory layout planning.
* Inspection and commissioning of machines before delivery.
After-sales service
* Provide one-year warranty.
* Arranging for engineers to travel overseas to guide the installation of machines and train workers.
* Continued technical advice after sale.
* Provide you with professional and customised solutions according to your needs.
* Factory site visit. We are a real manufacturer and have our own factory, you can see the machines and production.
Services during sale
* Assist customers with factory layout planning.
* Inspection and commissioning of machines before delivery.
After-sales service
* Provide one-year warranty.
* Arranging for engineers to travel overseas to guide the installation of machines and train workers.
* Continued technical advice after sale.
Packaging and Shipping
Production Workshop
Hot Searches