- Product Details
- {{item.text}}
Quick Details
-
Voltage:
-
380V
-
Dimension(L*W*H):
-
Customization
-
Weight:
-
1600 KG
-
Product name:
-
Automatic Oil Refinery Machine
-
Raw material:
-
Soybean
-
Function:
-
Making Edible Oil
-
After-sales Service Provided:
-
Online Support
-
Capacity:
-
300~500kg/h
-
Feature:
-
High Efficiency Low Cost
-
Advantage:
-
Energy Saving Low Residual
-
Used for:
-
Oil Making Expeller
-
Keyword:
-
Mini Oil Expeller
-
Material:
-
Stainess Steel
Quick Details
-
Production Capacity:
-
2t-15t/day
-
Place of Origin:
-
Liaoning, China
-
Brand Name:
-
CONOVAL
-
Voltage:
-
380V
-
Dimension(L*W*H):
-
Customization
-
Weight:
-
1600 KG
-
Product name:
-
Automatic Oil Refinery Machine
-
Raw material:
-
Soybean
-
Function:
-
Making Edible Oil
-
After-sales Service Provided:
-
Online Support
-
Capacity:
-
300~500kg/h
-
Feature:
-
High Efficiency Low Cost
-
Advantage:
-
Energy Saving Low Residual
-
Used for:
-
Oil Making Expeller
-
Keyword:
-
Mini Oil Expeller
-
Material:
-
Stainess Steel
Product Description
Edible oil refining equipment
The edible oil refining machine is a small refining equipment specially used for refiningedible oil and crude oil,
which can also be called edible oil refining equipment. It is composedof refining tanks, bleaching tanks, filters,
oil pumps, and electric motor control systems. It canremove impurities in the edible oil and crude oil through
processes such as crude oildegumming, deacidification, drying, and decolorization, reaching advanced edible standardsallowing theedible oil to have a longer storage life, better color, and odor More green andhealthy.
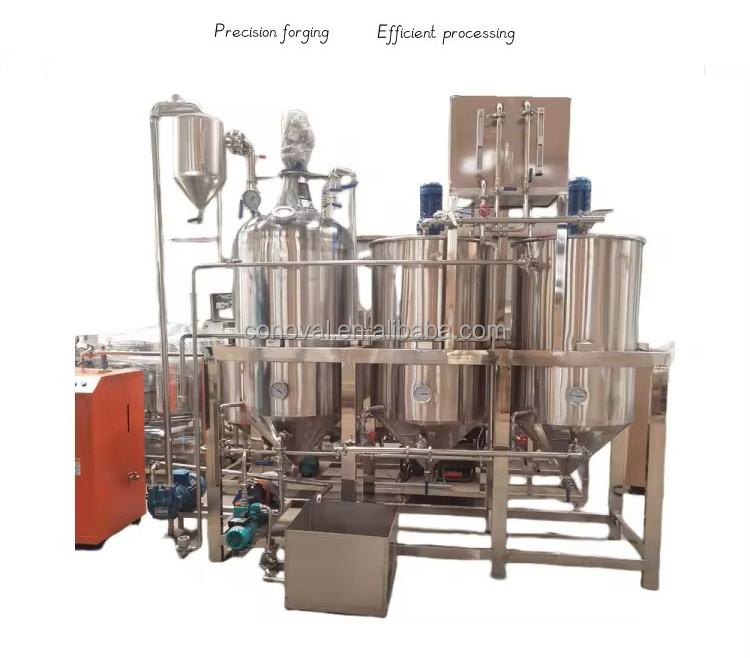
Suitable for large, medium, and small enterprises, capable of extracting 40-60 types of oil crops.
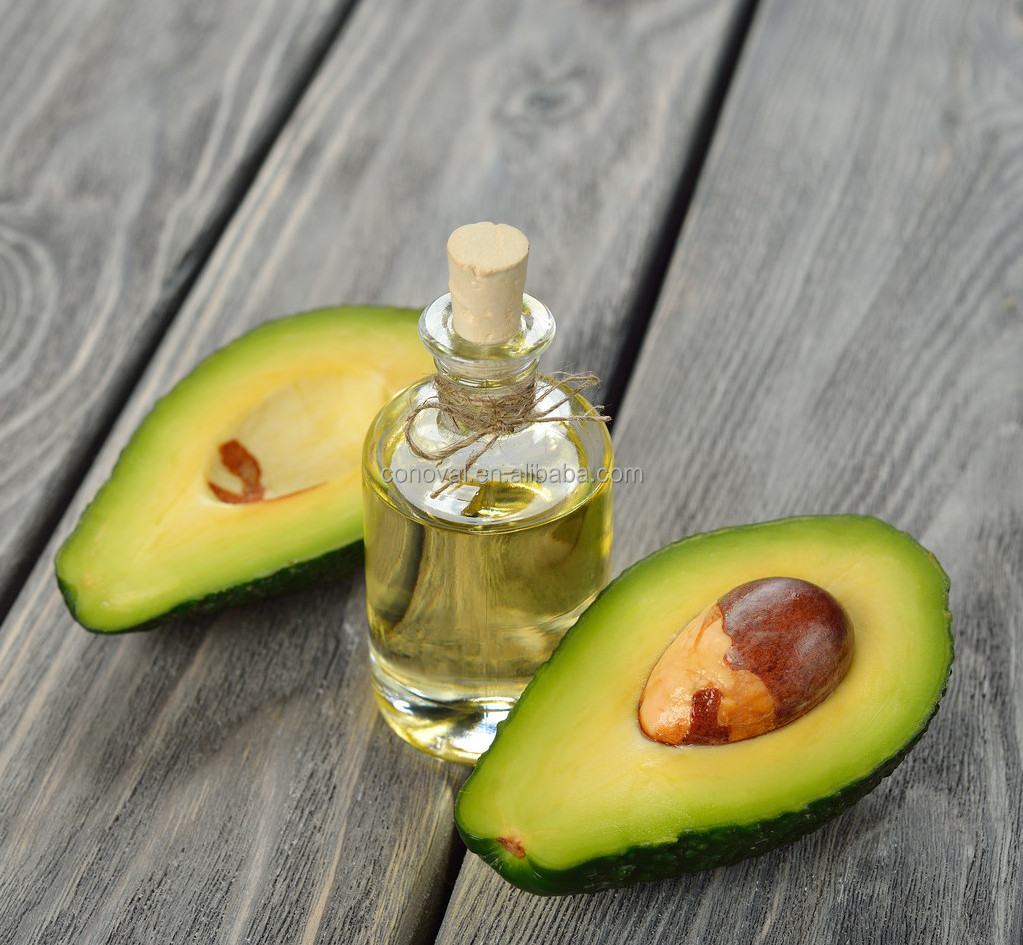
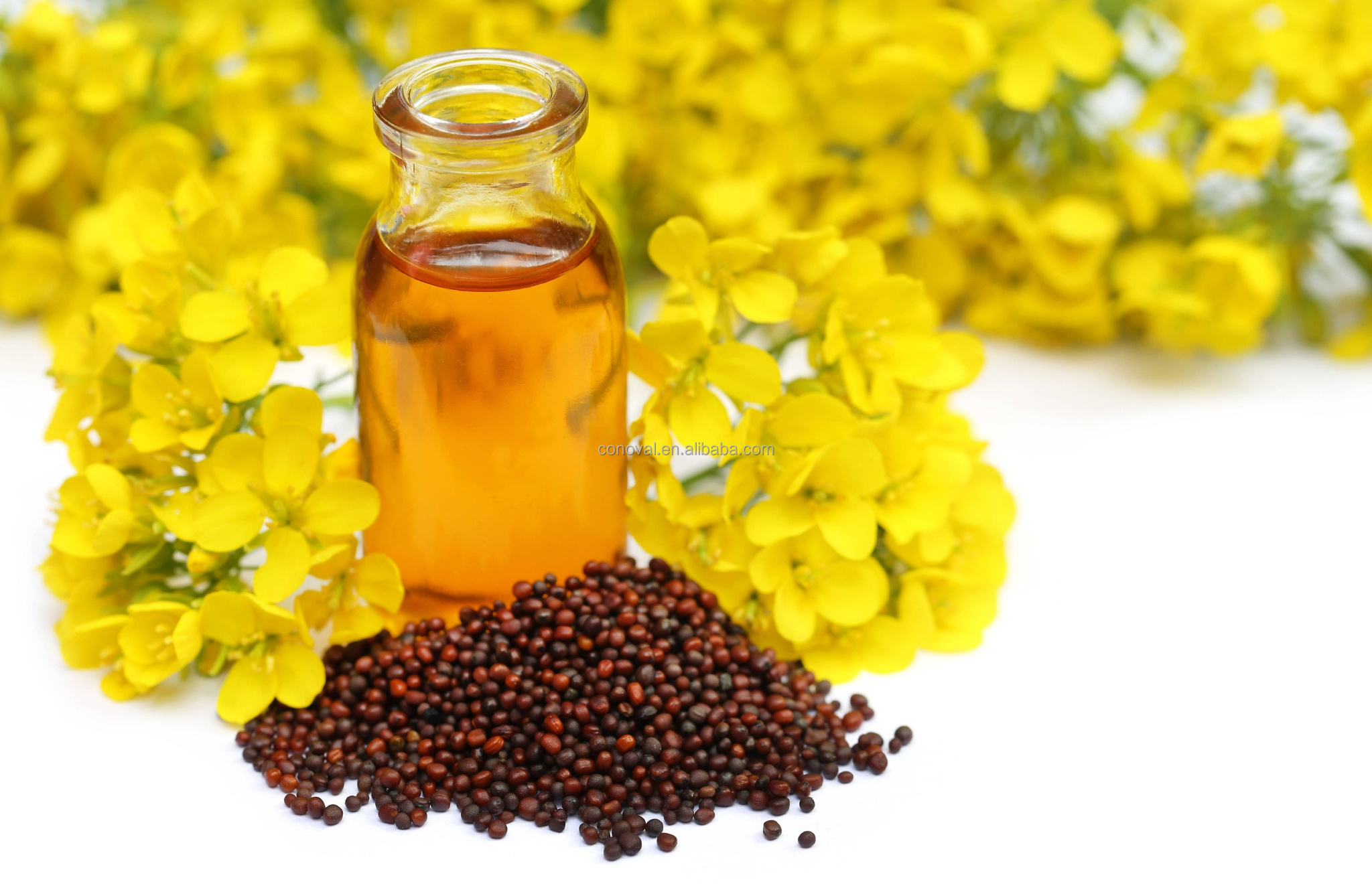
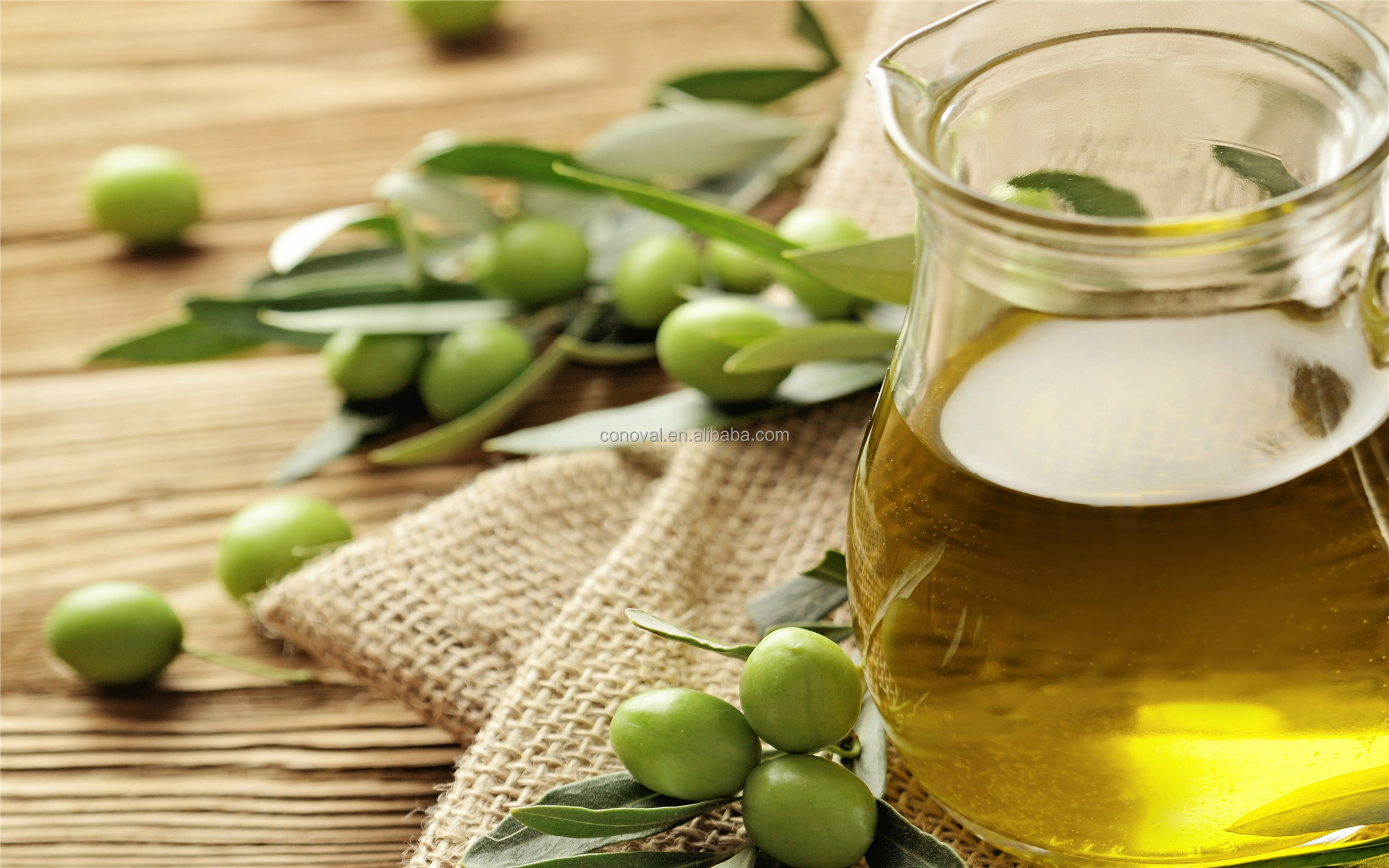
1.
Hydration degumming: Hydration degumming is a degumming method that uses the hydrophilic
properties of
colloidal impurities such as phospholipids to add a certain amount of water or electrolyte dilute solution to the
crude oil under stirring, allowing the colloidal impurities in the crude oil to absorb water and expand,
agglomerate,
and separate to remove.
During the hydration degumming process, the substances that can be
condensed and precipitated are mainly phospholipids, in addition to proteins, mucus, and trace metal ions that
bind to phospholipids.
2.
Alkali refining and deacidification: Various unrefined crude oils contain a certain amount of free fatty acids.
The process of removing free fatty acids from oils is called deacidification. The methods of deacidification
include alkali refining, distillation, solvent extraction, and esterification. The most widely used methods in
industrial production are alkali refining and steam distillation (i.e. physical refining)
3.
Oil decolorization: Oil adsorption decolorization refers to the use of certain substances that have a strong
selective adsorption effect on pigments (such as bleached earth, activated clay, activated carbon, etc.) to
adsorb pigments and other impurities in oil under certain conditions, thereby achieving the purpose of
decolorization. The oil treated with adsorbent not only achieves the goal of improving the oil color and
removing colloid, but also effectively removes some trace metal ions and some substances that can cause
hydrogenation catalyst poisoning in the oil, thereby providing good conditions for further refining
(hydrogenation and deodorization) of the oil.
4.
Oil deodorization: Oil deodorization is a process that utilizes the difference between the volatilization of
odorous substances in oil and triglycerides, and uses steam distillation to deodorize odorous substances under
high temperature and high vacuum conditions. The principle of water vapor distillation (also known as stripping)
for deodorization is that water vapor passes through grease containing odor components, contacts the vapor
liquid surface, and is saturated by the volatile odor components and escapes at a ratio of their partial pressure,
thereby achieving the purpose of deodorizing the odor components.
Effect after refining
After being processed by a refining machine, the oil has a transparent color, no precipitation after long-term
storage, no foaming after cooking, and no oil smoke. It meets the national edible oil standards, and can be
directly filled and sold. It is suitable for processing with supplied materials and small-scale oil processing plants.
Can refine 40-60 kinds of crude oil
Rice bran oil
Avocado oil
Camellia seed oil
Almond oil
Flax seed oil
Coconut oil
Other oils
Palm oil, cottonseed oil, corn germ oil, rapeseed oil, sunflower seed oil, peanut oil, soybean oil, xanthoceras oil, perilla seed oil, maple seed oil, evening primrose oil, cocoa butter oil, seaweed oil, sesame oil, mustard oil, safflower seed oil, peony seed oil, chili seed oil, gardenia oil, tung seed oil, millet oil, castor seed oil, walnut oil, olive oil, apple seed oil. sour jujube seed oil, wheat germ oil, Pumpkin seed oil, pomegranate seed oil, seabuckthorn seed oil, and various animal oils, fish oil, insect oil, butter. vegetable hydrogenated oil, etc.
There are many oils, so I won't list them all.
Specification
Model
|
ZY-112
|
ZY-113
|
ZY-115
|
Heating Power
|
3*2
|
6*3
|
9*3
|
Air pump power
|
1.1Kw
|
1.1Kw
|
1.1Kw
|
Capacity
|
1t/day
|
2t-5t/day
|
|
Mixing tanker
|
1unit
|
2unit
|
3unit
|
Voltage
|
380V 3 phase
|
380V 3 phase
|
380V 3 phase
|
Weight
|
500kg
|
800kg
|
1600kg
|
Size
|
3100*850*2500mm
|
4500*900*2500mm
|
6000*2000*2500mm
|
Notes:If any change of data, we will not notify further
Details Images
Operating methods of edible oil refining equipment
1.
Before rapeseed oil is sent to the crude oil pump and enters the refining tank, it is necessary to check
whether
the pipeline valves are normal. After each tank of rapeseed oil is delivered, the oil inlet valve should be
immediately closed. The crude rapeseed oil to be refined in the oil tank must first have foam on the oil surface
to make the oil surface smooth, and stand for a proper time so that there is no foam in the oil. Adjust the crude
oil temperature to 25-35 ℃
2.
Preparation of alkali liquor Weigh out a specified amount of alkali liquor (it must be identified first), mix with
appropriate amount of water, start the alkali pump, and circulate the alkali liquor to completely dissolve it.
Reduce the alkali liquor temperature to 25-30 ℃, measure the alkali liquor wave temperature with a Baume
meter, and adjust it to 10-12 °.
3.
When the crude oil surface is smooth and the temperature stabilizes at 25-35 ℃, start the agitator to start
mixing. First, slowly rotate (20 r/min) for stirring for 1 min, then quickly rotate (40 r/min). At the same time,
open the valve of the alkali tank and add the alkali liquor. The time for adding lye is generally about 15min.
After the lye is discharged, continue to quickly rotate and stir until the oil and soap particles are clearly
separated. The stirring time is about 3-3.5h. When the oil and soap feet are clearly separated, change to slow
stirring, open the heating steam valve (vapor pressure 1.4kgf/m*2), raise the temperature of the oil to 60 ℃
(the oil temperature should be maintained at 1 ℃/min, and the high temperature should not exceed 65 ℃),
immediately stop stirring, and close the steam valve to allow it to cool and precipitate by itself (sedimentation
time is about 8 hours). After checking that the pipeline of the oil delivery valve is normal, pump the oil into the
water washing tank. When the pump reaches the interface between the oil and the precipitated soap feet, be
careful not to pump the soap feet out while simultaneously pumping them out.
4.
Water washing heats up the oil pumped into the washing tank, while starting the mixer to add 75 to 80 ℃
hot
water to maintain the oil temperature at 80 to 85 ℃ (the temperature should not exceed 85 ℃). When the water
has been added (the amount of water added is 15% - 20% of the oil amount, and the time for adding water is
38 to 40 minutes), stop heating and continue stirring for 15 minutes, that is, stop stirring and precipitate for 2
hours (once). Open the drain valve at the bottom of the water washing tank to drain about 3/4 of the washing
water (before draining the washing water, first lift the remaining oil in the pipeline into the oil water separation
tank to recover it). Then close the drain valve, open the valve leading to the oil water separation tank, and
slowly add the remaining oil water mixture. During the second water washing, put all the viscous substances
in the oil-water intermediate layer into the separation tank until the oil is seen, and then close the valve.
Oil-water separation must be controlled by a dedicated person. When separating in the separation tank, the
heating coil in the tank must be opened to raise the temperature (not exceeding 80 ℃). After separation, the
water should be drained and the residual oil recovered.Follow the above method to continue washing the oil
machine with water until the washing water is completely clear. The sedimentation time for the second
washing is 1.5 hours.
5.
Before dehydration and transportation, first check whether the relevant pipeline valves are normal, and then
pump the water washing bin into the vacuum dehydration tank. At the same time, open the steam valve, start
the vacuum pump and agitator, adjust the cooling water of the condenser, and start the circulating oil pump to
accelerate the circulation of oil in the vacuum dehydration tank. The vacuum degree of the vacuum
dehydration tank is maintained above 0.0867MPa. The dehydration time is about 3h, calculated from the
delivery of oil from the dehydration tank, and the dehydrated oil should be sampled and inspected by the
quality inspector. If insufficient dehydration is found, dehydration must continue. The dehydration temperature
is maintained at about 70 ℃. After dehydration, stop the vacuum pump, open the air valve, and slowly add air.
Check whether the pipeline valve is normal, and then the transfer oil is cooled to 25-30 ℃ through the cooling
pipe and flows into the sedimentation tank for pressure filtration.
6.
Check whether the pipeline valve of the filter press is normal. Check that the oil temperature is below 30 ℃.
After the oil is filtered, stop the oil filter pump and close the valve. Gently open the filter plate to allow the
internal oil to flow into the oil pan, and then filter the filter residue on the cloth. Check the usage of the filter
cloth and prepare for replacement or washing. The residual oil from the filter cloth shall be separated and
recovered by a centrifuge.
Packing & Delivery
Hot Searches