- Product Details
- {{item.text}}
Quick Details
-
Marketing Type:
-
Hot Product 2023
-
Place of Origin:
-
Anhui, China
-
Brand Name:
-
GENUO
-
Year:
-
2023
-
Weight (KG):
-
6800 KG
-
Motor Power (kw):
-
15 kw
-
Plate yield limit:
-
245MPa
-
Crimp speed:
-
6(m/min)
-
Loaded with minimum diameter:
-
550mm
-
The upper roller diameter:
-
220mm
-
Roll diameter:
-
180mm
-
The two lower rollers center distance:
-
320mm
-
power:
-
15KW
-
Dimension:
-
4550*1400*1700
-
Weight:
-
6800KG
Quick Details
-
Max. Working Length (mm):
-
2000 mm
-
Max. Plate Thickness (mm):
-
12 mm
-
No. of Roller:
-
4
-
Marketing Type:
-
Hot Product 2023
-
Place of Origin:
-
Anhui, China
-
Brand Name:
-
GENUO
-
Year:
-
2023
-
Weight (KG):
-
6800 KG
-
Motor Power (kw):
-
15 kw
-
Plate yield limit:
-
245MPa
-
Crimp speed:
-
6(m/min)
-
Loaded with minimum diameter:
-
550mm
-
The upper roller diameter:
-
220mm
-
Roll diameter:
-
180mm
-
The two lower rollers center distance:
-
320mm
-
power:
-
15KW
-
Dimension:
-
4550*1400*1700
-
Weight:
-
6800KG
Products Description
Machine Feature
GENUO hydraulic CNC HC4R Series 4 roller plate rolling machine has the pre-bending function of the plate end and the CNC rolling function.It can feed the metal plate at a time, and can complete the pre-bending and the roll forming of the workpiece without turning the head.
The upper working roll of the machine is the main drive roll, and the lower roll and
both sides of the roll are hydraulically driven. The lift displacement is controlled by the computer and is automatically leveled. The screen display shows the synchronization accuracy of ±0.1mm. The tilting and resetting of the rollover bearing body is hydraulic transmission, the balance of the upper roll is equipped with a balance mechanism, which can easily take out the rolled workpiece. It has a mobile stand-alone console that can be moved at any time; the machine is equipped with a safety interlocking device and is safe.
Due to its full-featured, high-precision, and easy-to-use operation, this device is the ideal contemporary CNC coiling device. It is the ideal model for rolling circular and arc-shaped workpieces in energy, transportation, petroleum, chemical, boiler, shipbuilding,
hydropower, and metal structure industries.
Standard Equipment
|
|
|
Optional Equipment
|
|
|
||||
SIEMENS PLC controller, Touch display
|
|
|
SIEMENS CNC control system
|
|
|
||||
42CrMo solid forging roller
|
|
|
Central and side supports
|
|
|
||||
Schneider & Omron electrical components
|
|
|
Automatic loading and unloading systems
|
|
|
||||
YUKEN hydraulic valves, NOK seal ring
|
|
|
Motorised feeding and squaring tables
|
|
|
||||
NSK double-row spherical roller bearing
|
|
|
Side motorised rolls
|
|
|
||||
Tamagawa precision rotary encoder
|
|
|
Provision for hot rolling
|
|
|
||||
SIEMENS main motor,Sunny pump
|
|
|
Integrated welding system
|
|
|
||||
iNi hydraulic motor, Peika planetary reducer
|
|
|
Automatic lubrication system
|
|
|
||||
Mobile wheel mounted control console
|
|
|
Automatic ejector
|
|
|
||||
Centralised manual lubrication
|
|
|
Customized colors
|
|
|
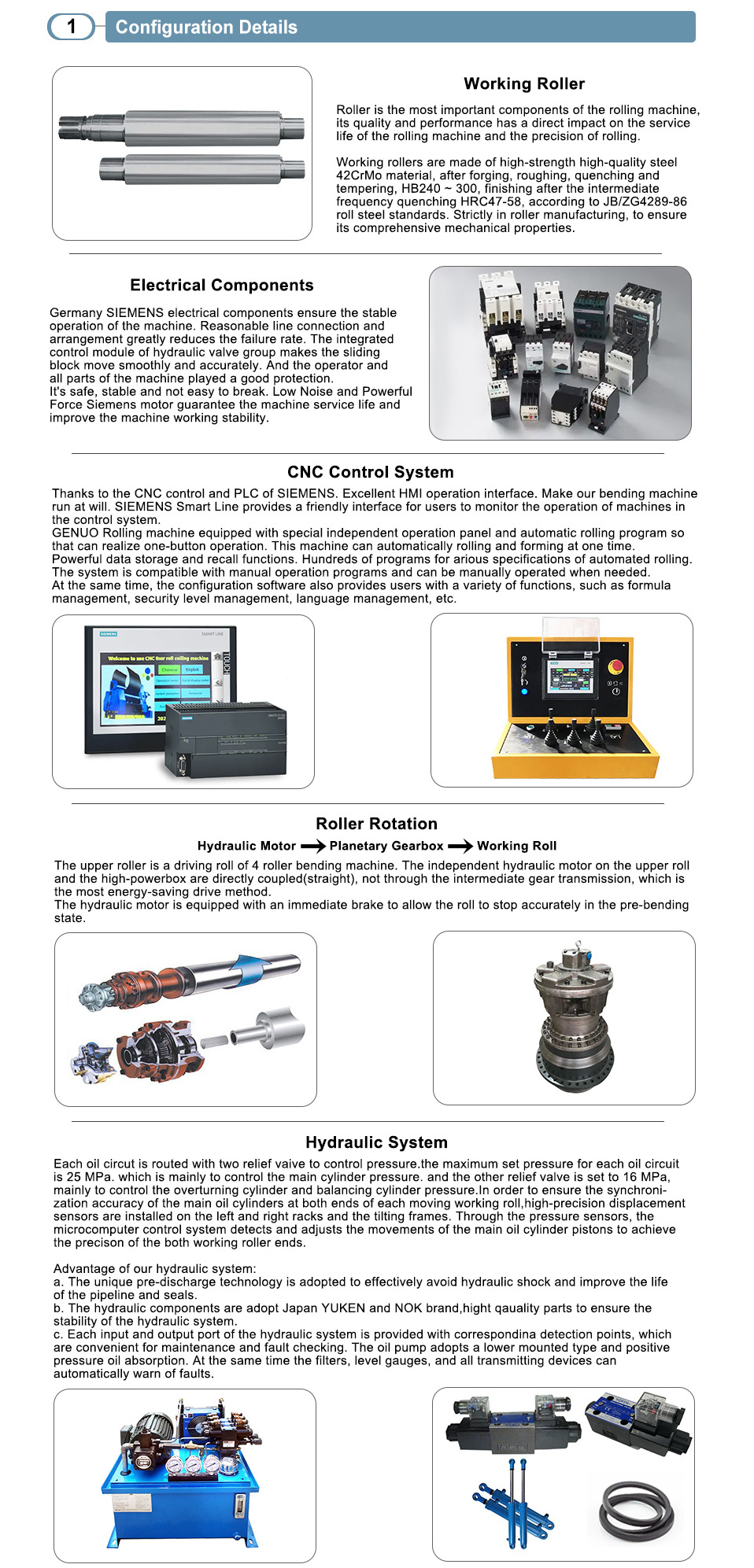
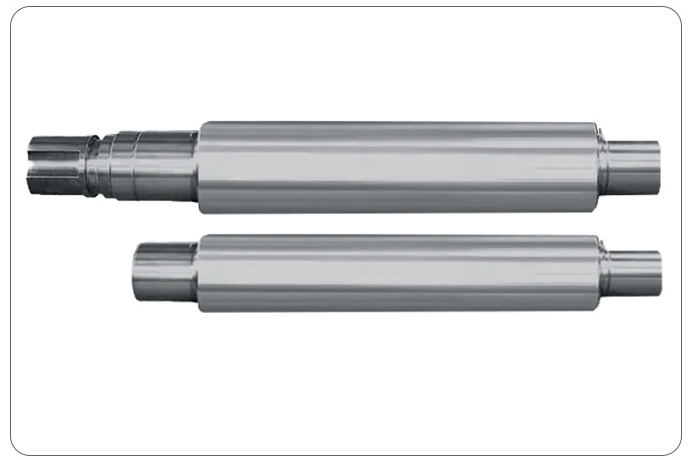
Working Roller
Roller is the most important components
of the rolling machine, its quality and performance has a direct impact on the service life of the rolling machine and the precision of rolling.
Working rollers are made of high-strength high-quality steel 42CrMo material, after forging, roughing, quenching and tempering, HB240 ~ 300, finishing after the intermediate frequency quenching
HRC47-58, according
to JB/ZG4289-86 roll steel standards.
Strictly in roller manufacturing, to ensure its comprehensive mechanical properties.
Electrical Components
Germany SIEMENS electrical components
Reasonable line connection and arrange-
ment greatly reduces the failure rate.
The integrated control module of
hydraulic
valve group
makes the sliding
block move
smoothly
and accurately.
And the operator
and all parts of the
machine played a good
protection.
Low Noise and Powerful Force
Siemens
motor guarantee the machine
service life
and improve the machine
working stability.
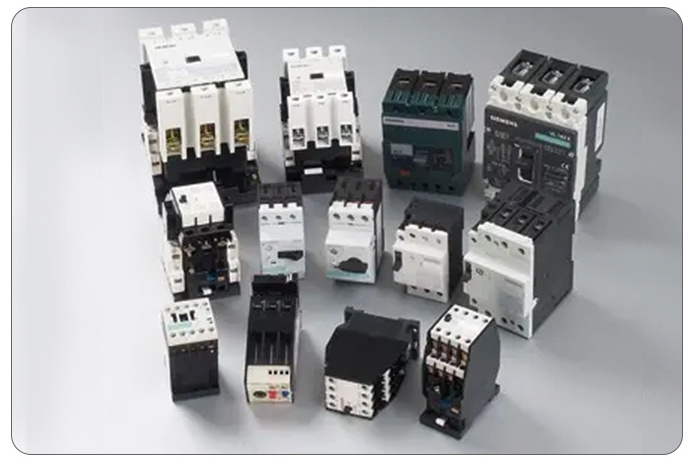
CNC Control System
Thanks to the CNC control and PLC of SIEMENS. Excellent HMI operation interface. Make our bending machine run
at will. SIEMENS Smart Line provides a friendly interface for users to monitor the operation of machines in the
control system.
GENUO Rolling machine equipped with special independent operation panel and automatic rolling program so that
can realize one-button operation. This machine can automatically rolling and forming at one time.
Powerful data storage and recall functions. Hundreds of programs for arious specifications of automated rolling.
The system is compatible with manual operation programs and can be manually operated when needed.
At the same time, the configuration software also provides users with a variety of functions, such as formula
management, security level management, language management, etc.
Roller Rotation
Hydraulic Motor
⇨
Planetary Gearbox
⇨
Working Roll
The upper roller is a driving roll of 4 roller bending machine. The independent hydraulic motor on the upper roll and
the high-powerbox are directly coupled(straight), not through the intermediate gear transmission, which is the
most
energy-saving drive method.
The hydraulic motor is equipped with an immediate brake to allow the roll to stop accurately in the pre-bending
s
tate.
Hydraulic System
Each oil circut is routed with two relief vaive to control pressure.the maximum set pressure for each oil circuit is 25
MPa. which is mainly to control the main cylinder pressure. and the other relief valve is set to 16 MPa, mainly to
control the overturning cylinder and balancing cylinder pressure.In order to ensure the synchronization accuracy of
the main oil cylinders at both ends of each moving working roll,high-precision displacement sensors are installed
on
the left and right racks and the tilting frames. Through the pressure sensors, the microcomputer control system
detects and adjusts the movements of the main oil cylinder pistons to achieve the precison of the both working
roller ends.
Advantage of our hydraulic system:
a. The unique pre-discharge technology is adopted to effectively avoid hydraulic shock and improve the life of the
pipeline and seals.
b. The hydraulic components are adopt Japan YUKEN and NOK brand,hight qauality parts to ensure the stability of
the hydraulic system.
c. Each input and output port of the hydraulic system is provided with correspondina detection points, which are
convenient for maintenance and fault checking. The oil pump adopts a lower mounted type and positive pressure
oil absorption.
At the same time the filters, level gauges, and all transmitting devices can automatically warn of faults.
The machine is four roller plate bending machine, its structure shown as drawing, upper roller as
initiative roller, down roller and side rollers as driven rollers; upper roller is fixed, down roller does
up and down movement; upper roller is mechanical initiative, while down roller and side rollers are
driven by friction from plate and rollers. Down roller and side rollers are driven by hydraulic oil tank
to do lifting movement.
Upper roller’s ventro-bearing overturn and reset are also driven by hydraulic oil tank.
Rollers’ bearing and
oil tank are installed on left and right side of machine frame.
1.Overturn Cylinder 7. Right Frame 13. Bottom Frame
2.Overturn Head 8. Balancing System 14. Side Support System【Optional】
3.Left Frame 9. Upper Roller Driven Device 15. Top Support System【Optional】
4.Upper Roller 10. Lower Roller Driven Device【Opt.】 16. Electric Feeding Electric Roll【Opt.】
5.Side Roller 11. Side Roller Cylinder 17. Hydraulic System
6.Lower Roller 12. Lower Roller Cylinder 18. Electronic Control System
2.Overturn Head 8. Balancing System 14. Side Support System【Optional】
3.Left Frame 9. Upper Roller Driven Device 15. Top Support System【Optional】
4.Upper Roller 10. Lower Roller Driven Device【Opt.】 16. Electric Feeding Electric Roll【Opt.】
5.Side Roller 11. Side Roller Cylinder 17. Hydraulic System
6.Lower Roller 12. Lower Roller Cylinder 18. Electronic Control System
Techical Specification
HC4R
|
Max
Pre-bending
Thickness
(mm)
|
Max
Rolling
Thickness
(mm)
|
Max
Rolling
Width
(mm)
|
Plate
Yield
Limit
(MPA)
|
Rolling
Speed
(m/min)
|
Upper
Roller
Dia
(mm)
|
Lower
Roller
Dia
(mm)
|
Side
Roller
Dia
(mm) |
Motor
Power
(KW)
|
|||||||||
6x2000
|
6
|
6
|
2000
|
265
|
5.5
|
180
|
180
|
145
|
5.5
|
|||||||||
6x2500
|
6
|
6
|
2500
|
265
|
5
|
210
|
210
|
165
|
7.5
|
|||||||||
8x2000
|
6
|
8
|
2000
|
265
|
5
|
215
|
215
|
165
|
11
|
|||||||||
8x2500
|
6
|
8
|
2500
|
265
|
5
|
230
|
230
|
180
|
11
|
|||||||||
12x2000
|
10
|
12
|
2000
|
265
|
5
|
260
|
260
|
200
|
18.5
|
|||||||||
12x2500
|
10
|
12
|
2500
|
265
|
5
|
280
|
280
|
220
|
18.5
|
|||||||||
16x2000
|
12
|
16
|
2000
|
265
|
5
|
280
|
280
|
220
|
18.5
|
|||||||||
16x2500
|
12
|
16
|
2500
|
265
|
5
|
330
|
330
|
260
|
22
|
|||||||||
16x3200
|
12
|
16
|
3200
|
265
|
5
|
360
|
360
|
280
|
30
|
|||||||||
20x2000
|
16
|
20
|
2000
|
265
|
5
|
330
|
330
|
260
|
22
|
|||||||||
20x2500
|
16
|
20
|
2500
|
265
|
5
|
360
|
360
|
280
|
30
|
|||||||||
25x2000
|
20
|
25
|
2000
|
265
|
5
|
360
|
360
|
280
|
30
|
|||||||||
25x2500
|
20
|
25
|
2500
|
265
|
4.5
|
410
|
400
|
320
|
37
|
|||||||||
30x2000
|
25
|
30
|
2000
|
265
|
4.5
|
410
|
400
|
320
|
37
|
|||||||||
30x2500
|
25
|
30
|
2500
|
265
|
4.5
|
470
|
470
|
390
|
37
|
|||||||||
30x3000
|
25
|
30
|
3000
|
265
|
4.5
|
560
|
520
|
420
|
45
|
|||||||||
40x2500
|
35
|
40
|
2500
|
265
|
4.5
|
560
|
520
|
420
|
45
|
|||||||||
40x3000
|
35
|
40
|
3000
|
265
|
4.5
|
650
|
580
|
480
|
55
|
|||||||||
50x2500
|
40
|
50
|
2500
|
265
|
4
|
650
|
620
|
500
|
55
|
|||||||||
50x3000
|
40
|
50
|
3000
|
265
|
3.5
|
720
|
650
|
520
|
55
|
|||||||||
60x3000
|
50
|
60
|
3000
|
265
|
3.5
|
750
|
710
|
560
|
75
|
|||||||||
70x3000
|
60
|
70
|
3000
|
265
|
3
|
750
|
720
|
600
|
75
|
|||||||||
80x3000
|
70
|
80
|
3000
|
265
|
3
|
800
|
780
|
620
|
75
|
|||||||||
90x3000
|
80
|
90
|
3000
|
265
|
3
|
840
|
820
|
660
|
90
|
|||||||||
The above data is only for reference only,to prevail in kind. More specifications available.
Please
click here!
|
|
|
|
|
|
|
|
|
|
Recommend Products
Hot Searches