- Product Details
- {{item.text}}
Quick Details
-
Coil Weight (T):
-
15
-
Marketing Type:
-
New Product 2024
-
Leveling Precision(±mm/m):
-
1.5 ±mm/m
-
Place of Origin:
-
Hebei, China
-
Brand Name:
-
Liming
-
Voltage:
-
380 or on customer requirements
-
Rated Power:
-
on customer requirements
-
Dimension(L*W*H):
-
18000*6000*2000
-
Weight:
-
15000
-
Year:
-
2024
-
Name:
-
Length Line Machine
-
After-sales Service Provided:
-
Send Engineer
-
Machine Type:
-
Automatic Cutting Machine
-
Cutting accuracy:
-
Length: 0.5mm Based
-
Application:
-
Steel Shearing
-
Raw material:
-
Q235 or Q345
-
Control system:
-
PLC+touch Screen
-
Cutting mode:
-
Hydraulic Shear
-
Certificate:
-
CE ISO
-
Can be designed according to clients:
-
Customizable
Quick Details
-
Cutting Width (mm):
-
4000 - 12000 mm
-
Material Thickness(mm):
-
8 - 20 mm
-
Cutting Speed(m/min):
-
15 - 25 m/min
-
Coil Weight (T):
-
15
-
Marketing Type:
-
New Product 2024
-
Leveling Precision(±mm/m):
-
1.5 ±mm/m
-
Place of Origin:
-
Hebei, China
-
Brand Name:
-
Liming
-
Voltage:
-
380 or on customer requirements
-
Rated Power:
-
on customer requirements
-
Dimension(L*W*H):
-
18000*6000*2000
-
Weight:
-
15000
-
Year:
-
2024
-
Name:
-
Length Line Machine
-
After-sales Service Provided:
-
Send Engineer
-
Machine Type:
-
Automatic Cutting Machine
-
Cutting accuracy:
-
Length: 0.5mm Based
-
Application:
-
Steel Shearing
-
Raw material:
-
Q235 or Q345
-
Control system:
-
PLC+touch Screen
-
Cutting mode:
-
Hydraulic Shear
-
Certificate:
-
CE ISO
-
Can be designed according to clients:
-
Customizable
3x1300mm High precision Laser cutting uncoiling cut-to-length machine steel metal coil cut to length line machine manufacturer
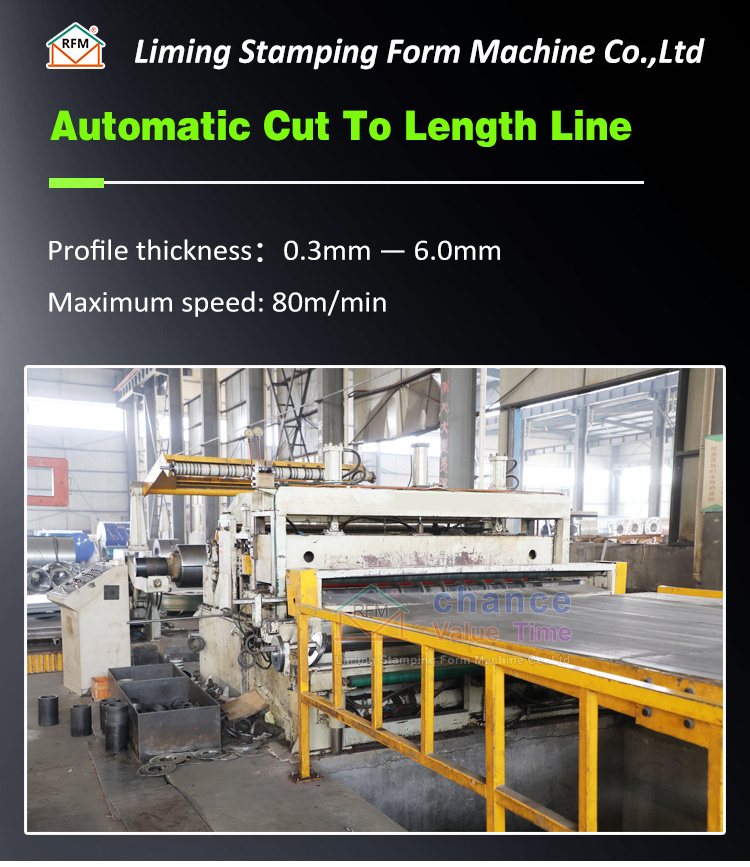
Manufacturing Technique
Open flat thickness:
|
8---25 mm
|
|
Cut length:
|
4—12m
|
|
Open flat width:
|
1000—2300mm
|
|
Cutting edge thickness:
|
8-- 20 mm(Q235)
|
|
Cut-to-length accuracy:
|
长度 ≤1.5mm (1000mm)
|
|
Diagonal
|
≤2mm (1000mm)
|
|
Cutting edge sickle bend
|
≤5mm (12000mm)
|
|
Production line speed:
|
15—25m/min
|
|
Levelling accuracy:
|
1.5mm/ m2
|
|
Continuous shearing times:
|
8次/min
|
|
Total length of automatic line:
|
92M
|
|
Total power load:
|
580KW
|
|
Stacking device:
|
|
|
1. Length adjustment range:
|
4000-12000mm
|
|
2. Width adjustment range:
|
1000-2300mm
|
|
3. Maximum stacking weight:
|
15T
|
|
4. Maximum stacking height:
|
300mm
|
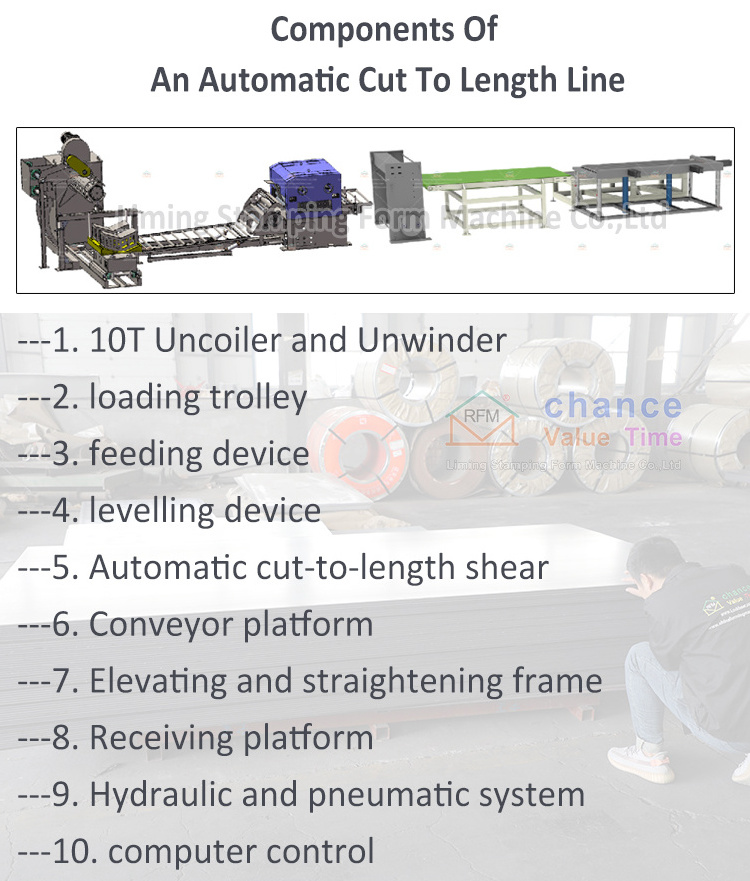
Cut to Length Line is a common metal sheet levelling and processing equipment, which is widely used in metal manufacturing industry.
Liming will introduce the process flow and precautions of the levelling line in detail.
I. Process flow of cross shear machine
1. loading: the metal plate to be processed placed in the flat line, the requirements of the plate clean and burr-free.
2. Loosening: the sheet will be received through the primary loosening rollers, using the loosening rollers to correct the cracks,
back bends and edge deviations on the sheet.
3. Flattening: The sheet is received through the flattener and flattened to make it flat.
4. Splitting rolls: The sheets are handed over to the roll splitting machine for splitting rolls, separating the sheets and
dealing with burrs exposed on the upper part of the sheets.
5. Spinning: The sheet is passed through the rotary tangent roller machine to spin the sheet to improve the flatness.
6. Water cooling: After the plate is rotated, it needs to be cooled by water cooling to shorten the time of plate temperature
rise.
7. Fine finishing roller pressing: the sheet is realised through the pressure releaser to achieve fine processing, flattening and
stretching at the end of the sheet to ensure the consistency of the flatness of the sheet.
8. Vertical warping correction: The purpose of warping roller correction is to balance the tension inside the plate and improve
the flatness of the plate.
9. Inspection: Inspection of the processed sheet to check whether it meets the specified standards.
10. Unloading: The processed plates are put on the conveyor belt for discharging, which is convenient for storage and subsequent
processing.
Liming will introduce the process flow and precautions of the levelling line in detail.
I. Process flow of cross shear machine
1. loading: the metal plate to be processed placed in the flat line, the requirements of the plate clean and burr-free.
2. Loosening: the sheet will be received through the primary loosening rollers, using the loosening rollers to correct the cracks,
back bends and edge deviations on the sheet.
3. Flattening: The sheet is received through the flattener and flattened to make it flat.
4. Splitting rolls: The sheets are handed over to the roll splitting machine for splitting rolls, separating the sheets and
dealing with burrs exposed on the upper part of the sheets.
5. Spinning: The sheet is passed through the rotary tangent roller machine to spin the sheet to improve the flatness.
6. Water cooling: After the plate is rotated, it needs to be cooled by water cooling to shorten the time of plate temperature
rise.
7. Fine finishing roller pressing: the sheet is realised through the pressure releaser to achieve fine processing, flattening and
stretching at the end of the sheet to ensure the consistency of the flatness of the sheet.
8. Vertical warping correction: The purpose of warping roller correction is to balance the tension inside the plate and improve
the flatness of the plate.
9. Inspection: Inspection of the processed sheet to check whether it meets the specified standards.
10. Unloading: The processed plates are put on the conveyor belt for discharging, which is convenient for storage and subsequent
processing.
Machine Details
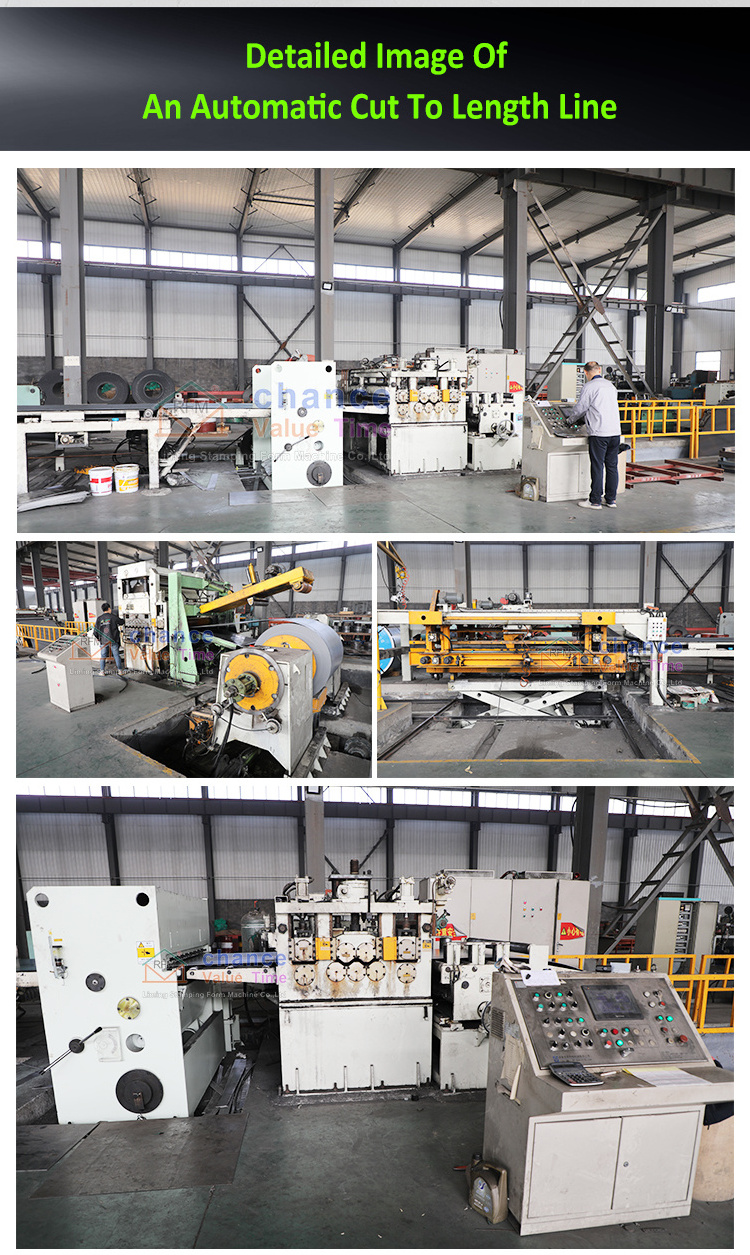
Hot Searches