1.The main function of molding machine is to fill sand and press sand for molding.
2. It is mainly used for small-sized and mass-produced castings. It can be used on production lines or used alone to complete
compaction and mold functions.
3. It is the most ideal choice for producing small castings of handicrafts, lighting accessories, furniture hardware and plumbing
equipment.
4. This jolt squeeze molding machine is suitable for making sand mold by drag /cope flask in general foundry workshops and
mechanized/semi-mechanized foundry.
- Product Details
- {{item.text}}
Quick Details
-
Voltage:
-
380V 50HZ
-
Power:
-
7.5KW
-
Dimension(L*W*H):
-
1580 * 1300 * 1680 mm
-
Weight (KG):
-
4000
-
Product name:
-
Manual Jolt Squeeze Sand Casting Molding Machines
-
Technology:
-
Green sand casting machine
-
Foundry Machine:
-
Manual Jolt Squeeze Moulding Machine
-
Capacity:
-
40-60 Moulds/hour
-
The Size Of Sand Mold:
-
300 * 400 / 350 * 400 / 350 * 450 ( mm )
-
The Thickness Of Sand Mold:
-
( 80~150 ) * 2 ( mm )
-
The Speed Of Manufacturing Mold:
-
30 sec / mold
-
Air Comsumption ( Normal / Mold):
-
0.3 cubic meter
Quick Details
-
Place of Origin:
-
Shandong, China
-
Machine Type:
-
Manual Jolt Squeeze Moulding Machine
-
Brand Name:
-
TZZJ
-
Voltage:
-
380V 50HZ
-
Power:
-
7.5KW
-
Dimension(L*W*H):
-
1580 * 1300 * 1680 mm
-
Weight (KG):
-
4000
-
Product name:
-
Manual Jolt Squeeze Sand Casting Molding Machines
-
Technology:
-
Green sand casting machine
-
Foundry Machine:
-
Manual Jolt Squeeze Moulding Machine
-
Capacity:
-
40-60 Moulds/hour
-
The Size Of Sand Mold:
-
300 * 400 / 350 * 400 / 350 * 450 ( mm )
-
The Thickness Of Sand Mold:
-
( 80~150 ) * 2 ( mm )
-
The Speed Of Manufacturing Mold:
-
30 sec / mold
-
Air Comsumption ( Normal / Mold):
-
0.3 cubic meter
Products Description
The Jolt Squeeze Moulding Machine Work principle
The worktable fall and collide with floating shock-iron,and the sand was tighted slightly, and then to compaction,get the top and bottom of sand mould are tight. The slightly shock is high frequency (500-1000 times/min), small amplitude (5-25 mm) vibration instead of low frequency (60-120 times/min), the large amplitude vibration. This kind of moulding machine made of sand mold are good quality, the basic requirement is also lower.
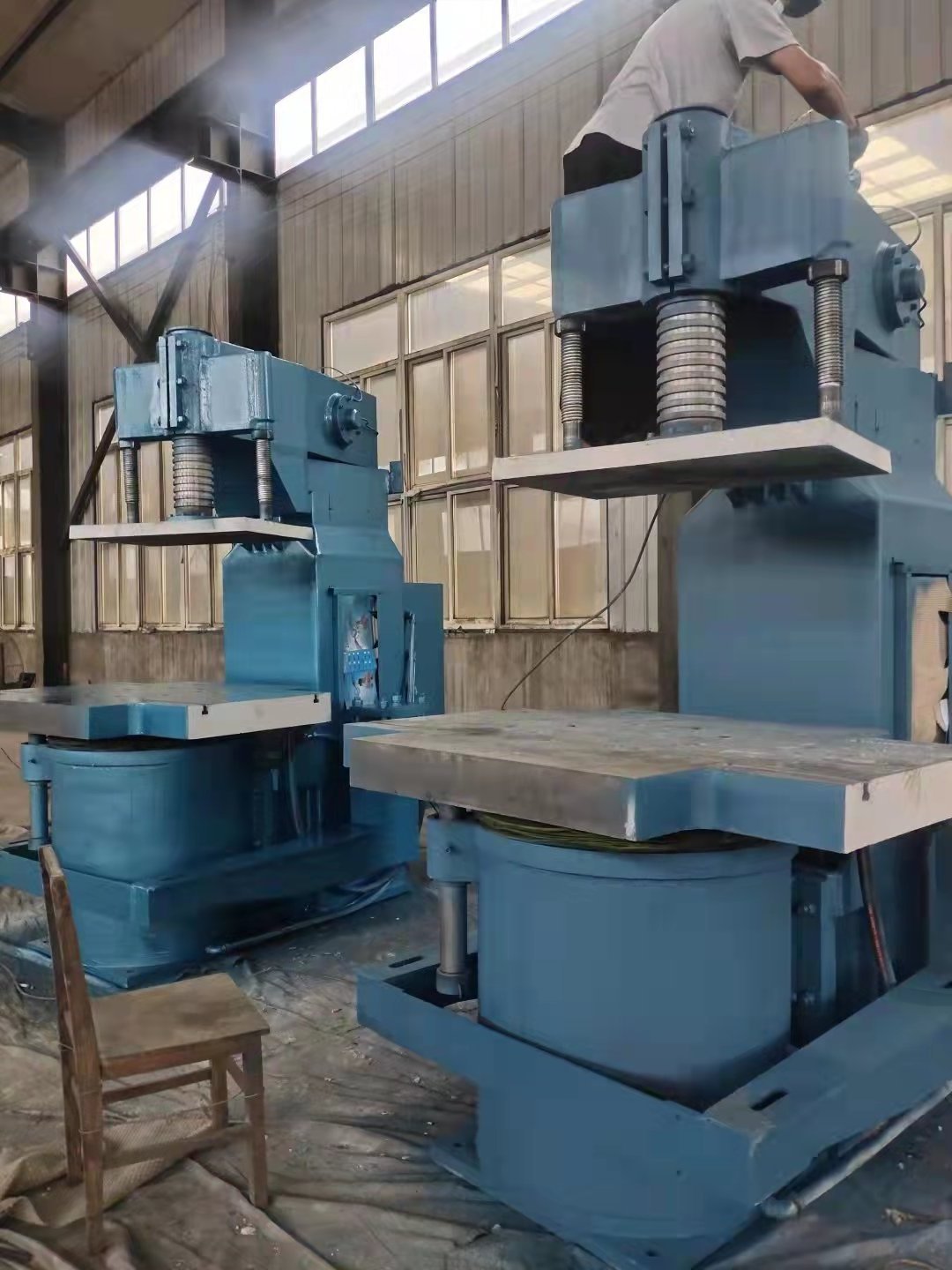
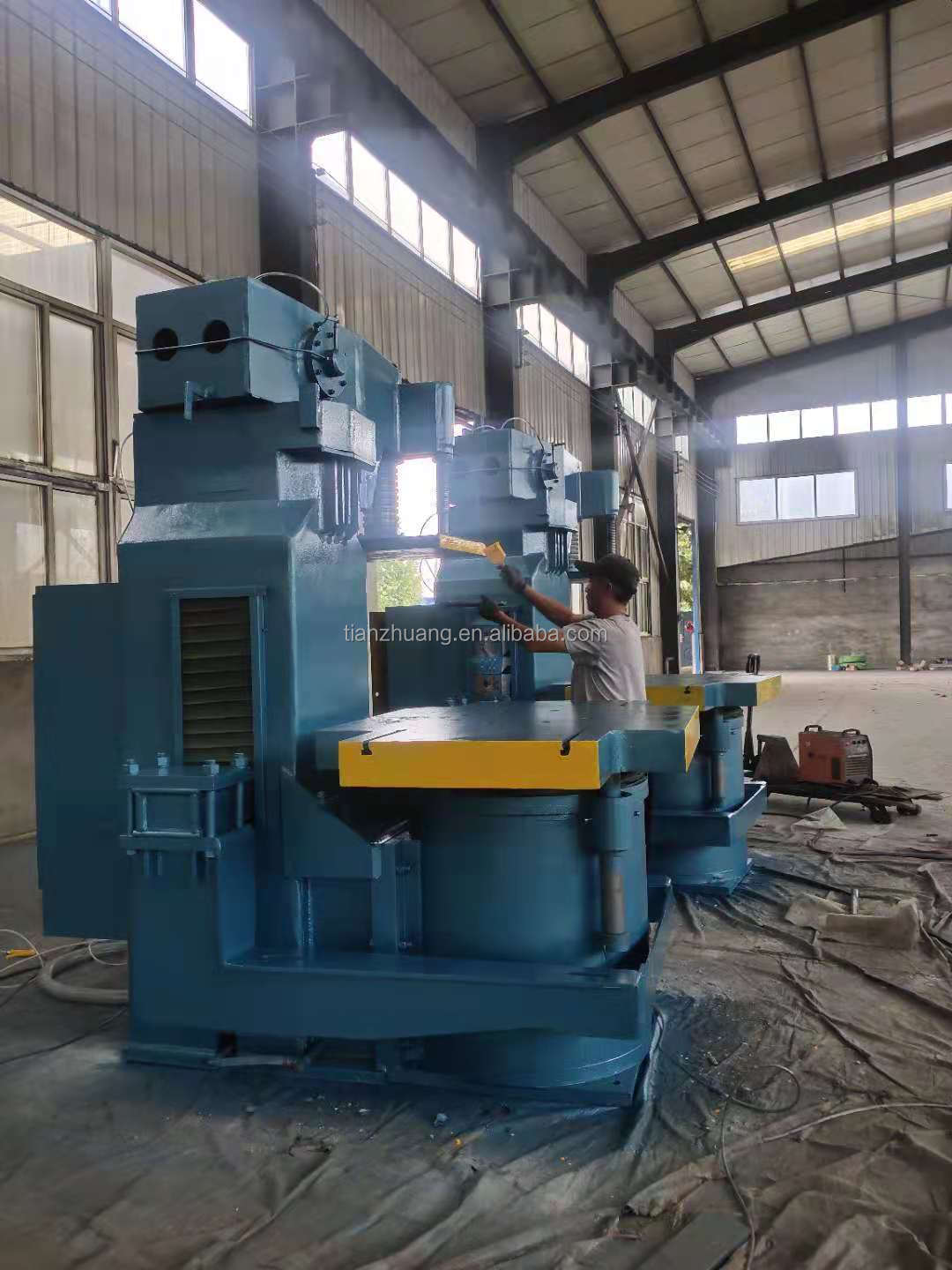
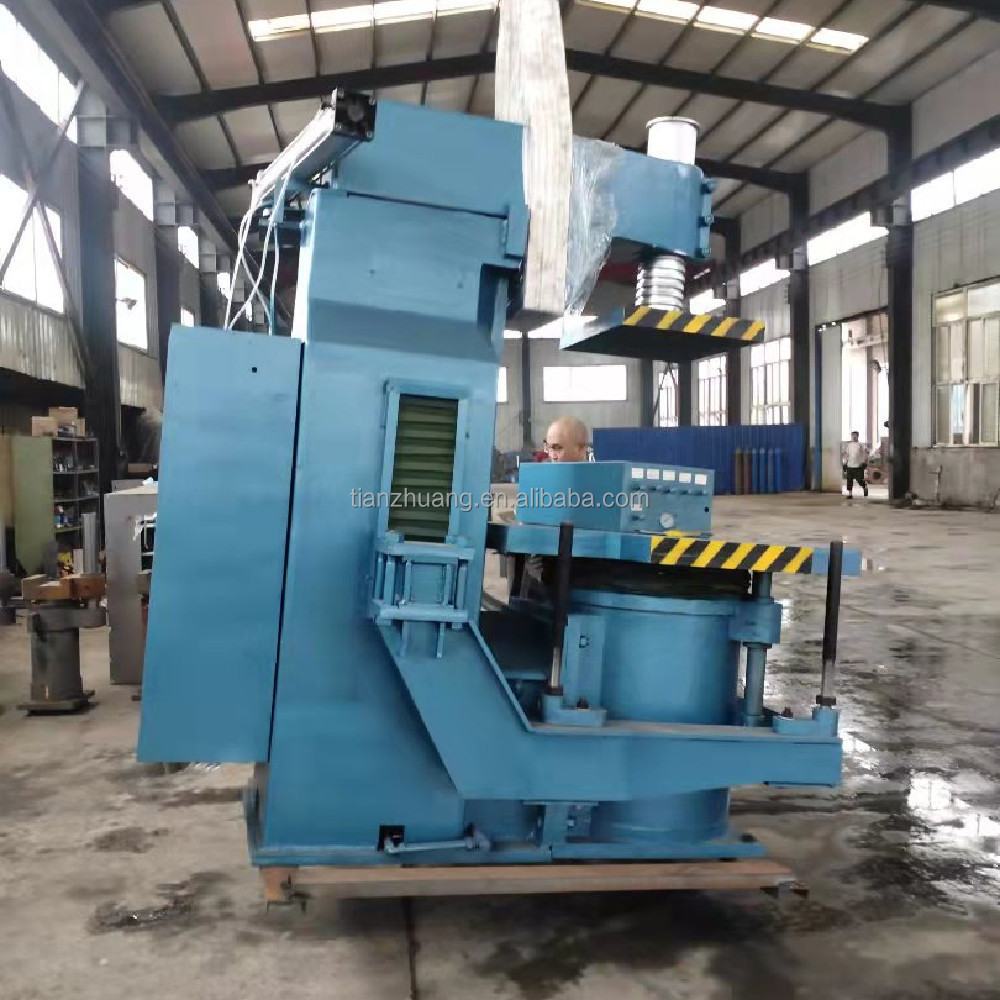
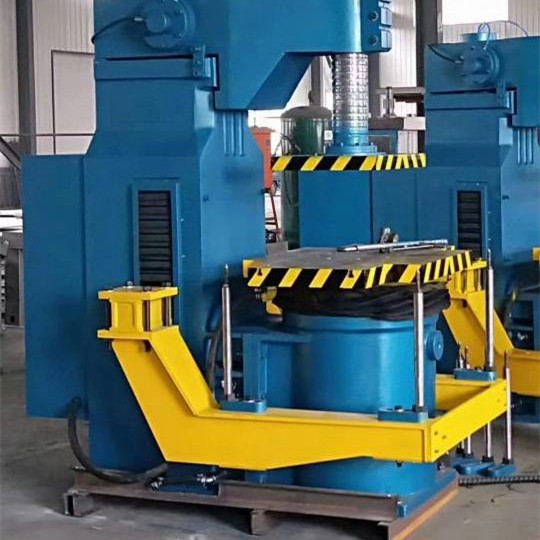
Usage
Foundry Green Sand Moulding Machine
is generally used for foundry casting workshop, mechanical production lines or semi-mechanical production lines.
Jolt Squeeze Microseism Molding Machine of
Characteristics:
A. Pneumatic multi-contact compaction is adopted to optimize the design of the machine, without oil leakage; moderate specific pressure, no special requirements for sand, more compaction contacts (48pcs), suitable for complex moulding.
B. High pressure compaction, the multi-contacts compacts sand molding,
and vibrate with working table(separated from machine frame, and frame without vibration). Therefore, good vibration effect, high hardness and uniform sand moulding(average hardness 85~90 , B type hardness tester),the sand consumption can be as small as 20~30mm, the compaction ratio is up to 4.2, and the vertical surface hardness of the mold cavity can still reach above HB80.
C. The machine adopts the spring micro-vibration compaction mechanism, large compaction cylinder diameter, high pressure strength,compacted and even sand moldings, it can guarantee quality of casting.The mold stripping structure adopts way of air oil pressure, the mold stripping adopts connecting rod, the synchronous shaft structure, the pressure oil speed regulation, good mold stripping synchronization, realizes the stable drawing by the two lifting cylinders, the
connecting rod, and the synchronous shaft. Simple pneumatic pipeline, easy and flexible operation, convenient operation, The machine adopts the spring fully cushioned pneumatic micro-vibration mechanism, no special foundation requirement.
D. The machine increases the stroke of the compaction cylinder, adopts multiple mechanisms to increase the pressure strength, and at the same time, it can pressurize and vibrate according to actual need, so that the elevation and plane hardness of the sand type (including type of complex sand moulding ) are compact and even. Convenient operation and high productivity.
A. Pneumatic multi-contact compaction is adopted to optimize the design of the machine, without oil leakage; moderate specific pressure, no special requirements for sand, more compaction contacts (48pcs), suitable for complex moulding.
B. High pressure compaction, the multi-contacts compacts sand molding,
and vibrate with working table(separated from machine frame, and frame without vibration). Therefore, good vibration effect, high hardness and uniform sand moulding(average hardness 85~90 , B type hardness tester),the sand consumption can be as small as 20~30mm, the compaction ratio is up to 4.2, and the vertical surface hardness of the mold cavity can still reach above HB80.
C. The machine adopts the spring micro-vibration compaction mechanism, large compaction cylinder diameter, high pressure strength,compacted and even sand moldings, it can guarantee quality of casting.The mold stripping structure adopts way of air oil pressure, the mold stripping adopts connecting rod, the synchronous shaft structure, the pressure oil speed regulation, good mold stripping synchronization, realizes the stable drawing by the two lifting cylinders, the
connecting rod, and the synchronous shaft. Simple pneumatic pipeline, easy and flexible operation, convenient operation, The machine adopts the spring fully cushioned pneumatic micro-vibration mechanism, no special foundation requirement.
D. The machine increases the stroke of the compaction cylinder, adopts multiple mechanisms to increase the pressure strength, and at the same time, it can pressurize and vibrate according to actual need, so that the elevation and plane hardness of the sand type (including type of complex sand moulding ) are compact and even. Convenient operation and high productivity.
The Jolt Squeeze Moulding Machine Work Technical Parameters
Advantages:
Improve sand compactness, reduce waste, reduce labor intensity, improve work efficiency, etc.
The air system is simple, easy to operate, flexible, easy to use, repair and maintenance.
Model
|
Z145
|
Z146
|
Z148
|
Z149
|
Z1410
|
Table Size(mm)
|
600×560
|
700×600
|
880×700
|
1100×900
|
1400×1100
|
Sand Flask(mm)
|
500×400
|
600×500
|
700×600
|
1000×800
|
1300×900
|
Sand Flask Height(mm)
|
<250
|
<250
|
<250
|
<400
|
<400
|
Capacity(molds/h)
|
25-35molds
|
25-36molds
|
25-37molds
|
25-38molds
|
25-40molds
|
Compaction cylinder diameter(mm)
|
380
|
420
|
470
|
630
|
650
|
Air pressure
|
0.6mpa
|
0.6mpa
|
0.6mpa
|
0.6mpa
|
0.6mpa
|
Squeeze Force
|
68,047
|
83,127
|
104,097
|
187,035
|
199,098
|
Air consumption
|
0.3m3/mold
|
0.4m3/mold
|
0.6m3/mold
|
0.9m3/mold
|
1.6m3/mold
|
Ram-jolt cylinder diameter
|
150mm
|
200mm
|
220mm
|
330mm
|
360mm
|
Stripping distance
|
200mm
|
250mm
|
250-300mm
|
350mm
|
350mm
|
Payload
|
560
|
720
|
1040
|
1600
|
2240
|
Weight
|
1.8T
|
2.3T
|
3.2T
|
6.5T
|
9.2T
|
Height Shorten
|
-150mm
|
-150mm
|
-150mm
|
-170mm
|
-300mm
|
Machine dimension mm
|
800x1300x1600
|
900x1350x1800
|
1100x1400x1850
|
1200x2100x2200
|
1400x2500x2550
|
|
|
|
|
|
|
Application of Sand Moulding machine
Description of proudction process
Description of proudction process
1. Most parts of the molding machine are ductile iron castings, and the quality of castings is very important
2. Our Huaxin Company has its own foundry and casting testing laboratory to ensure the quality of molding machines from the source.
3. After the casting comes out, it will go through a series of machining processes. The company has over 30 sets of machining equipment to ensure timely delivery.
4. After the casting is processed, polished, assembled and welded to the fuselage.
5. Connect the air source, debug and test run to ensure that the equipment delivered from the factory is qualified equipment.
1. Most parts of the molding machine are ductile iron castings, and the quality of castings is very important
2. Our Huaxin Company has its own foundry and casting testing laboratory to ensure the quality of molding machines from the source.
3. After the casting comes out, it will go through a series of machining processes. The company has over 30 sets of machining equipment to ensure timely delivery.
4. After the casting is processed, polished, assembled and welded to the fuselage.
5. Connect the air source, debug and test run to ensure that the equipment delivered from the factory is qualified equipment.
Hot Searches