- Product Details
- {{item.text}}
Quick Details
-
Brick size:
-
400*100*200 mm, 400*120*200 mm, 200*100*60 mm, 300*150*100 mm, 400*150*200 mm, 240*115*90 mm, 200*200*60 mm, 150*150*100 mm, 400*200*200 mm, 230*220*115 mm
-
Place of Origin:
-
China
-
Brand Name:
-
MINGGONG
-
Weight (KG):
-
12000 kg
-
Product Name:
-
AAC Plant
-
Advantage:
-
High Efficiency
-
Application:
-
Buliding Construction
-
After-sales Service:
-
Enigneer Available
-
Keywords:
-
AAC Block Autoclave
Quick Details
-
Type:
-
Autoclaved aerated concrete block (AAC)
-
Brick Raw Material:
-
Sand
-
Production Capacity (Pieces/8 hours):
-
50000-300000m3 per year
-
Brick size:
-
400*100*200 mm, 400*120*200 mm, 200*100*60 mm, 300*150*100 mm, 400*150*200 mm, 240*115*90 mm, 200*200*60 mm, 150*150*100 mm, 400*200*200 mm, 230*220*115 mm
-
Place of Origin:
-
China
-
Brand Name:
-
MINGGONG
-
Weight (KG):
-
12000 kg
-
Product Name:
-
AAC Plant
-
Advantage:
-
High Efficiency
-
Application:
-
Buliding Construction
-
After-sales Service:
-
Enigneer Available
-
Keywords:
-
AAC Block Autoclave
Product Showcase
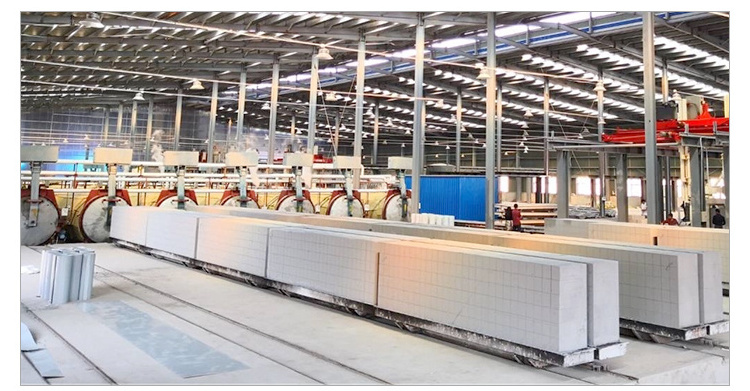
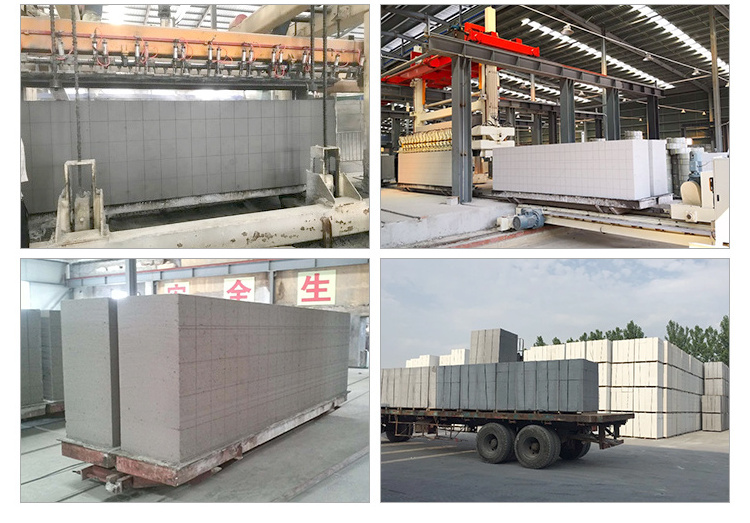
Aerated Autoclaved Concrete block machine (AAC) line
Shanghai minggong is the most professional manufacturer of autoclaved aerated concrete (AAC) plants for many years, and we can supply complete set of autoclaved aerated concrete plant with 50 000m3, 100 000m3, 150 000m3, 200 000m3, 250 000m3, 300 000m3 capacity annually, including plant design, equipments installation, technical instruction, personal training, etc, and also can design and manufacture as per clients' requirement.
(1) Material hopper (2) Ball Mill machine (3)Slurry store area (4) Pouring system structure (5)Material silo (6) weighing hopper (7) Pouring mixer (8)Frequency conversion pouring ferry car (9)Mould (10)Reversal hydraulic system (11)Cuttingmachines (12) Waste material mixer silo(13)Transport block system (14)Autoclave (15) Pallet reuse system (16) Packing system (usually no need this parts)
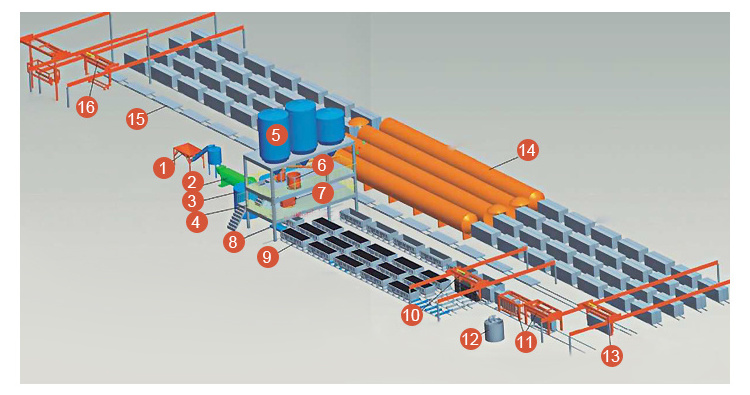
What is AAC
AAC is a kind of light cellular silicate products. Main material based on Silicon materials (sand, fly ash,gangue contains silicon) and Calcium(cement and lime),mix with foaming agent(Aluminium powder), a fter batching, mixing, pouring,pre-curing,cutting,steam(autoclaved),and other process,finally, get this light weight concrete products.
Introduction of AAC Block Production Line
2.Processing of raw materials:
Fly ash, sand or limestone is sent into ball mills by vibration feeders and belt conveyor.Then fine powders of flyash,sand or lime are pumped into slurry tank.
Quick lime is sent by vibrating feeder and belt conveyor into jaw crushers to crush. Crushed lime is sent into lime silo by bucket elevator and then is transported into ball mills by screw conveyor. Fined materials are sent into proportion bin by screw conveyor and bucket elevator.
1.Storing and supplying of raw materials of AAC blocks:
All raw materials are carried into factory by trucks, such as Fly ash, sand or lime are gathered in specified raw materials field waiting for use. Sacks of cement and bulk cements stored in cement warehouse. Chemicals and aluminium powder are separately keept in chemical warehouse and aluminium warehours.When used, these raw materials are carried into workshop respectively.
3.Aerated block ingredients,stiring and casting
Flyash (or sand or stone powder )and waste slurrry are measured in measuring tank.After the measuring and mould in their place,slurry stirring begins. Slurry temperature should reach about 40°c.
Cement ,lime,fly ash type aerated block raw material proportion:
Name
|
Unit
|
Proportion
|
Fly ash
|
%
|
65-70
|
Cement
|
%
|
6-15
|
Lime
|
%
|
18-25
|
Gypsum
|
%
|
3-5
|
Aluminum powder paste(600kg/m³)
|
1/10000
|
8
|
Water&material rate
|
|
0.60-0.65
|
Curing temperature
|
℃
|
36-40
|
Aluminum mixing time
|
S
|
30-40
|
Cement ,lime,sand type aerated block raw material proportion:
Name
|
Unit
|
Proportion
|
|
|
Sand
|
%
|
55-65
|
|
|
Cement
|
%
|
10-20
|
|
|
Lime
|
%
|
20-30
|
|
|
Gypsum
|
%
|
2-3
|
|
|
Aluminum powder paste(600kg/m³)
|
1/10000
|
8
|
|
|
Water&material rate
|
|
0.65-0.75
|
|
|
Casting system
|
℃
|
35-38
|
|
|
Aluminum mixing time
|
S
|
30-40
|
|
Raw material processing
1). The cement is bulk cement, which is pneumatically transported to the cement storage bin by a bulk cement truck. The cement storage capacity considered in this design is 90t.
2). After the lime and gypsum are crushed by the jaw crusher by calculation, the elevatorenters the storage bin, is fed by electromagnetic vibration, enters the mill, and the finely mixed ash is transported by the elevator to the ash storage bin for backup.
3). The sand is transported into the slurry storage tank through ball milling and water wet milling into a slurry storage tank, and after the slurry specific gravity required for production is reached, it is pumped to a stirring pouring machine through a slurry pump.
4.Aerated block’s precuring and cutting
1). Ingredients pouring
After the materials are ready, measure them separately, mix and stir with a stirring pouring machine,
add the metered and stirred aluminum powder suspension, stir for 30-45 seconds, and then pour into the mold.
2). Cutting Section
After pouring and foaming, the green body is statically stopped to a certain hardness (about 1.2-2h), that is, cutting is performed, and the green body is lifted to a steaming cart by a marshalling spreader, and then marled into a kettle
3). Autoclave
After cutting the green bodies, they can be marshalled to a certain number by driving and then enter
the autoclave for autoclaving.
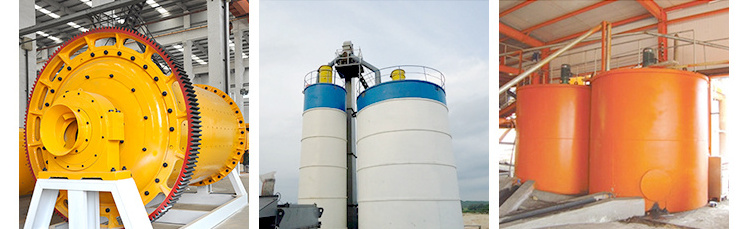
1.Ball mill 2.raw material silo 3.slurry storage tank
4.material scale 5.casting mixer 6.pouring system
7.Mould 8.Cutting Machine 9.prepare to enter the autoclave
10.Autoclave 11.boiler 12.Finished product
Advantages of AAC Block
1. Lightweight:
The aerated concrete dry bulk density generally is 400-800kg/m3, equivalently to clay brick 1/3, normal concrete 1/5, lower than normal light-weight aggregate concrete and hollow brick, hollow clay brick. so, using aerated concrete as wall material can lighten the building self weight, and then reduce the size of building foundation, girder and pillar etc. Structure, save building material and project cost, improve the building shock resistance.
2. Good heat preservation performance:
The aerated concrete inside have abundance tiny air hole, so it have good heat preservation performance, its coefficient of heat conductivity generally is 0.09-0.02W/(m.k), only 1/4-1/5 for clay brick, normal concrete 1/51/10. Usually 20cm thick aerated concrete wall heat preservation performance is correspond to 49cm normal clay brick wall, thus not only save heating and cooling energy, but also improve greatly building plane using coefficient.
3. Processability:
The aerated concrete don't use coarse aggregate, has good processability, can be sawed, digged, drilling and pinning, also can be cohered by suitable binding material, which give favorable condition to building operations.
4. Wide raw material source, high production efficient, low energy consumption
The aerated concrete can be produced by sand, ore slag, fly ash, tailing ore, coal gange and quick lime, cement etc. According to local actual condition to determine variety and process, and can using industrial waste residue greatly. The aerated concrete have high production efficiency, a medium scale AAC plant, annual per capita labor efficiency can reach to 600m3, some high degree automation can reach 900-1000m3, higher than clay brick (180m3) and concrete brick (500-800m3). Its production energy consumption is low, unit product energy consumption is only 50% for same volume clay brick.
Although the industrial production history of aerated concrete in China only has 40 years, its classification already developed non weight bearing block, weight bearing block, heating preservation block, wall and roof boarding, widely used in industrial and civil building, has become a new type rich vitality building material.
Main Raw Material for AAC BlockMain Raw Material for AAC Block
1). Sand (fly ash, slag): meet standard JC/T622-1996, technical requirements: SiO2s >65%, 0.08mm residue on sieve <20%, CaCO3<10%, So3<2%, clay<8%, no impurity.
2). Lump quick lime: meet standard JC/T621-1996, technical requirements: A-CaO>65%, slacking time 8-15min, slacking temperature >65°C, burnt lime content <8%, ash content <10%, MgO <5%.
3). Gypsum: technical requirement: Dihydrate gypsum or phosphogypsum, SO2 content >35%.
4). Aluminium powder or aluminum paste: solids content >65%,
5). Cement: meet standard GB175-92, 32.5R bulk cement.
Material-milling Equipments
1).Crusher: Lime, gypsum, and such kind of bulk material need to be crushed as the first step in AAC Plant.
2). Ball mill: The AAC material must be fully grinded in order to make better reaction. Ball Mill is used widely, it has two types: dry and wet, can be chosen upon requirement.
3). Material Metering Equipments: Computer Control Automatic Metering System is commonly used as measurement of raw materials.
4). Material mixing and casting equipments: Mixer, it’s the slurry mixing machine, also is slurry casting machine.
5). Cutting Machine: the AAC blank is formed after casting and precuring, as the size is too large, it must be cut to achieve the required product size.
6). Autoclave: Autoclave is a device for silicate hydration products to get physical and mechanical properties.
7). Boiler: the boiler supports for the autoclave and preheat furnace and other facilities with heat.
AAC brick use
Our Project
Packaging & Shipping
Packaging Details:
We will make different packaging according to different machine sizes .standard international export packing, container, wooden box.
Delivery Time:
We will customize according to the actual needs of customers. Senior designers start to design the plan. After receiving the deposit, we will complete the delivery within 20 to 30 working days.
Our factory is capable of shipping large machine even more than 100 tons
Hot Searches