- Product Details
- {{item.text}}
Quick Details
-
Product name:
-
Investment Casting Parts
-
Material:
-
Stainless steel
-
Keyword:
-
Investment Casting
-
Process:
-
Precision Lost Wax Investment Casting
-
Surface Treatment:
-
Sand Blasting
-
Application:
-
Machinery Parts
-
Certification:
-
ISO 9001:2015
-
Standard:
-
GB ASTM AISI DIN BS
-
Service:
-
OEM ODM Customized
-
Dimensions:
-
152*75*95mm
Quick Details
-
Place of Origin:
-
Guangdong, China
-
Brand Name:
-
Zeren
-
Model Number:
-
CB034
-
Product name:
-
Investment Casting Parts
-
Material:
-
Stainless steel
-
Keyword:
-
Investment Casting
-
Process:
-
Precision Lost Wax Investment Casting
-
Surface Treatment:
-
Sand Blasting
-
Application:
-
Machinery Parts
-
Certification:
-
ISO 9001:2015
-
Standard:
-
GB ASTM AISI DIN BS
-
Service:
-
OEM ODM Customized
-
Dimensions:
-
152*75*95mm
Metal Casting Service 304 316 Stainless Steel Precision Investment Casting Aluminum Parts Die Casting Zinc Die Casting
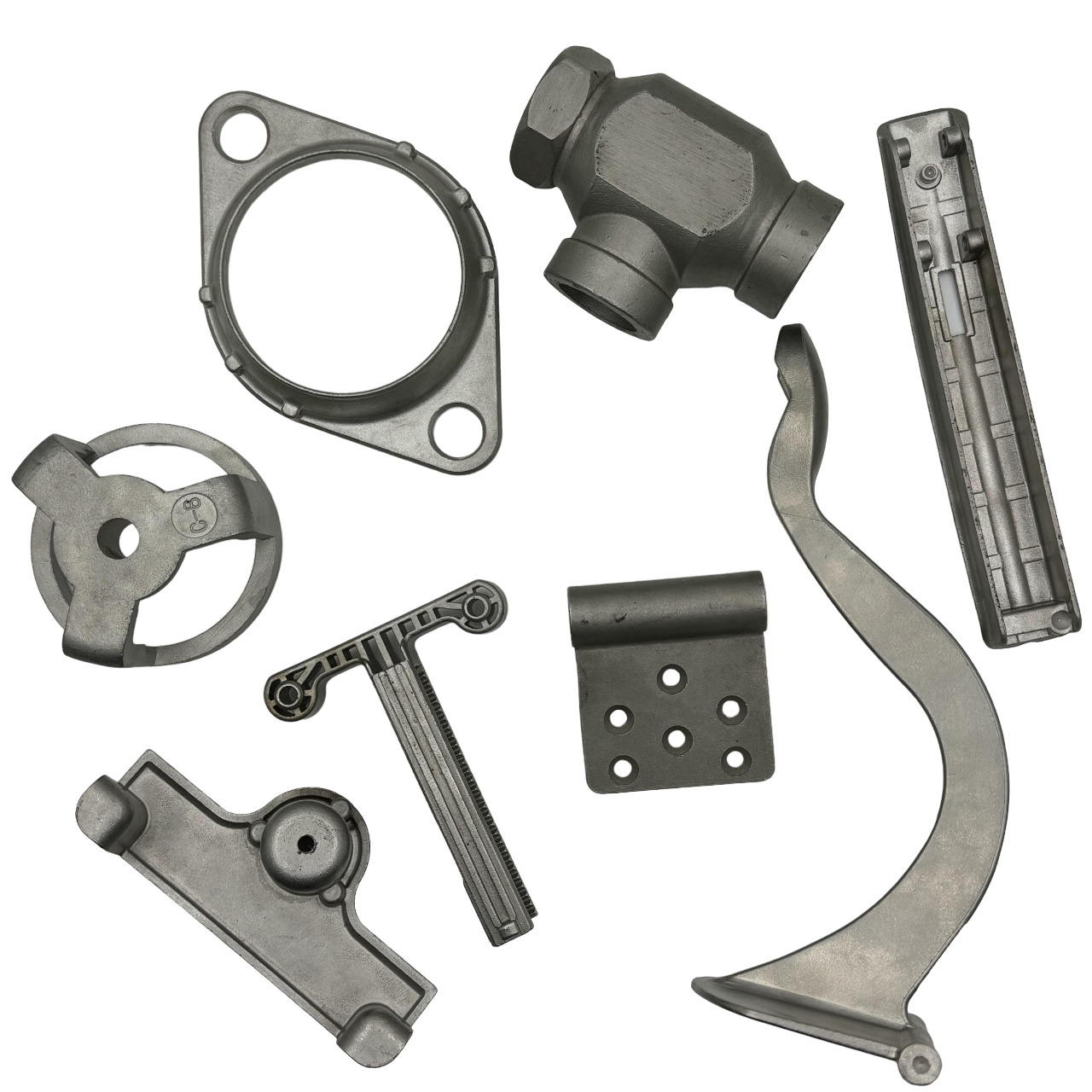
|
|
|
|
|
|
|
|
|
Investment Casting+CNC machining
|
|
|
Customized support
|
|
Product General Specs
|
|
|
Material
|
Austenitic stainless steel: 201, 303, 304, 316, 316L, 1.4581, scs14, scs16
|
|
|
Hardened stainless steel:17-4PH, 410, 420, 440C
|
|
|
Alloy cast steel: 4140, 4150, 4340, 8620, GS-25CrMo4
|
|
|
Casting alloy tool steel: CS-2, CS-7, CrWMn
|
|
|
Carbon steel: 1020, 1025(WCB), 1030, 1040, 1045, 1050
|
|
Weight
|
1g-30kg
|
|
Casting tolerance
|
CT4-CT7/GBT6414-1999; VDG Merkblad P690
|
|
Surface Roughness
|
Ra1.6-Ra6.3
|
|
Thickness
|
Min 2mm (1mm in Micro-region)
|
|
Casting Radius
|
Round radius ≥0.3mm, Internal fillet radius≥0.5mm
|
|
Blind Hole Depth
|
Max 30mm (Diamter 10mm)
|
|
Machining
|
Turning,Milling,Drilling,Boring,Threading, Grinding,CNC Machining & test equipment
|
|
Heat Treatment
|
Annealing,Hardening, Normalizing,Carburizing, Aging
|
|
Surface Finishing
|
Black Oxide,Black Coating,Anti-Pollution Flashover Coating,Mirror Polish
|
|
Industry Standards
|
ASTM, ICI, BS, DIN, JIS, ISO
|
|
Design Software
|
Pro-E, UG,Solidworks, AutoCAD
|
|
File Format
|
IGS, STP, XT, PDF, JPEG, JPG
|
|
Quality control
|
100% inspection before packing
|
Our Case1 & Solutions:
During the production process, we found the following problems: because the casting is easy to deform, subsequent shaping is difficult. , and after the surface is polished, it needs to be plated with copper and then chrome-plated.
At the same time, electroplating will have a magnifying effect on surface defects, and sand holes are prone to occur, resulting in rework or even scrapping after final polishing. Therefore, we recommend only casting the head of the product.
The rear plane part is processed by steel plate and then butted together, which does not affect the performance of the product, and overcomes the above defects, and reduces the cost by about 50%.
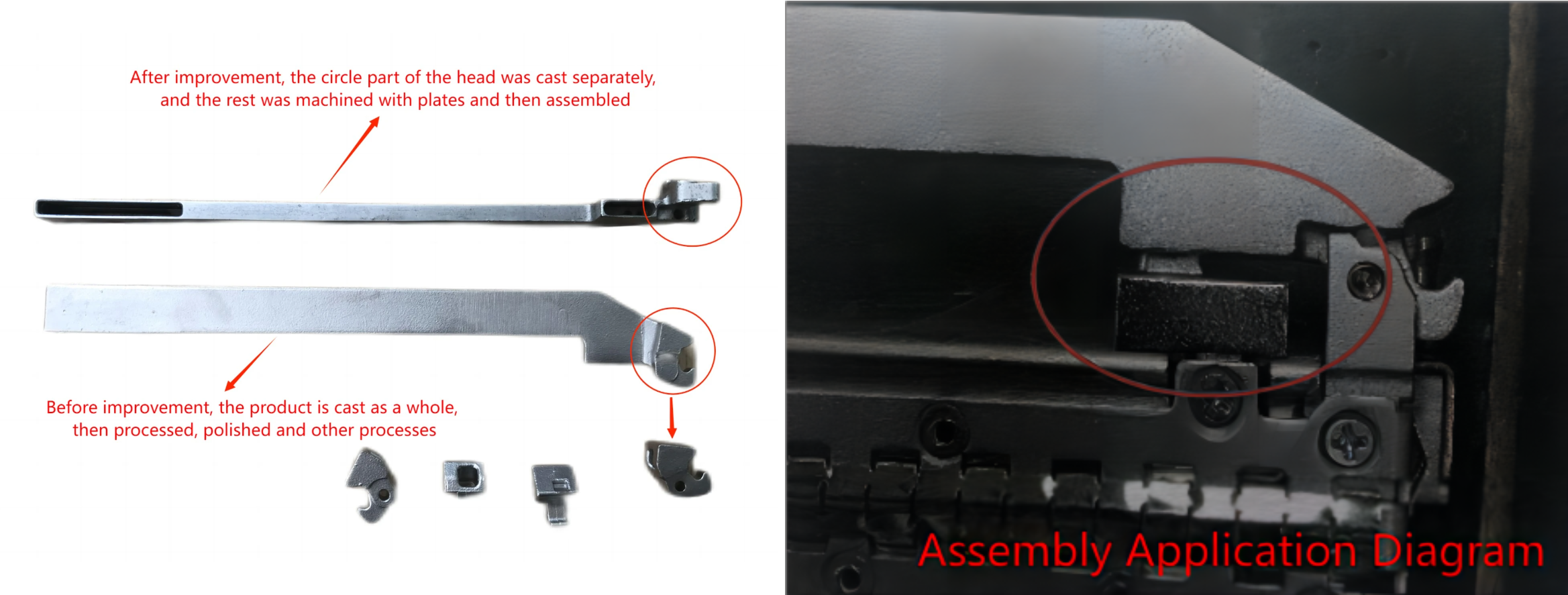
Our Case2 & Solutions:
In 2016, our company produced diffuser impellers (impeller accessories) according to the drawings provided by customers (As shown below), the material is 304 stainless steel.
This product contains five curved air-dissipating holes. It is very difficult to open the mold, make the shell and remove the sand, resulting in a high scrap rate.
In this regard, after research and discussion, our engineers decided to use a sand core material that not only has high temperature strength but also is easy to remove sand after high temperature, and finally perfectly solved the problem of curved hole casting.
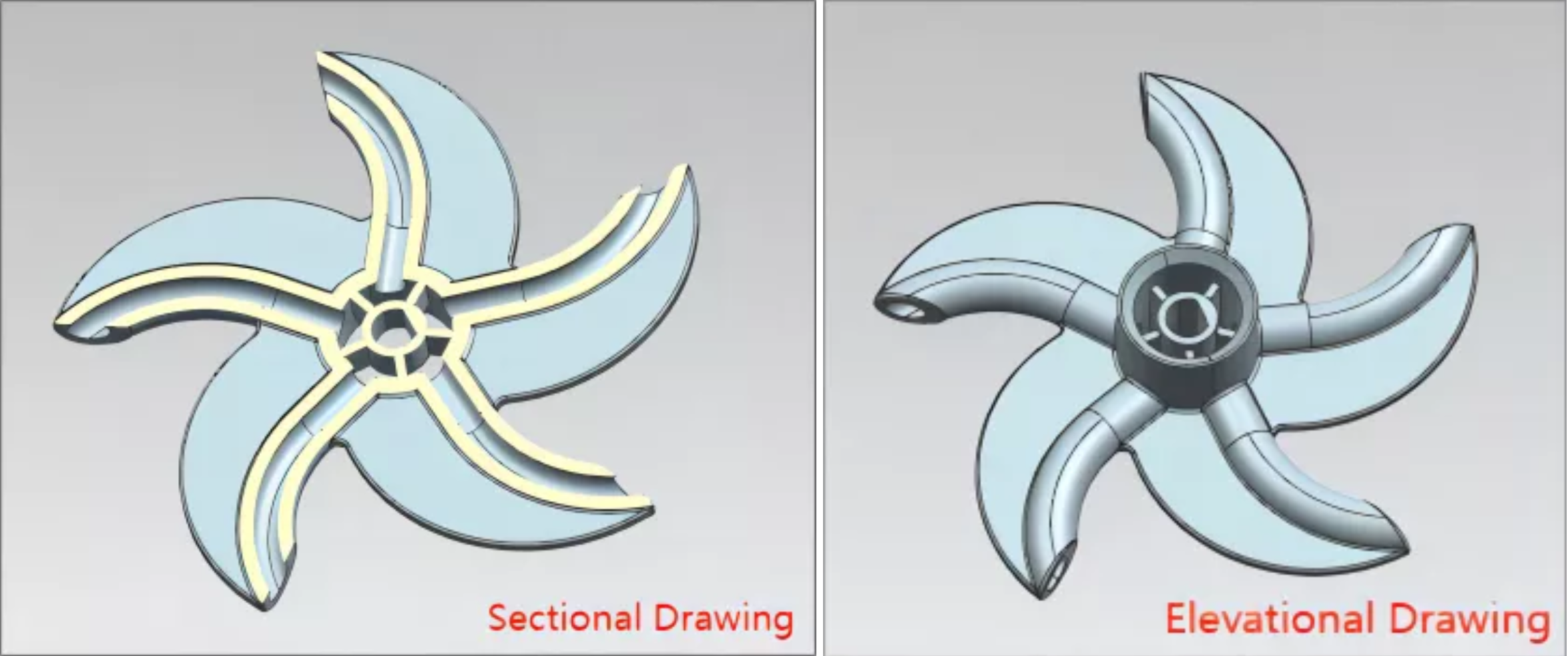
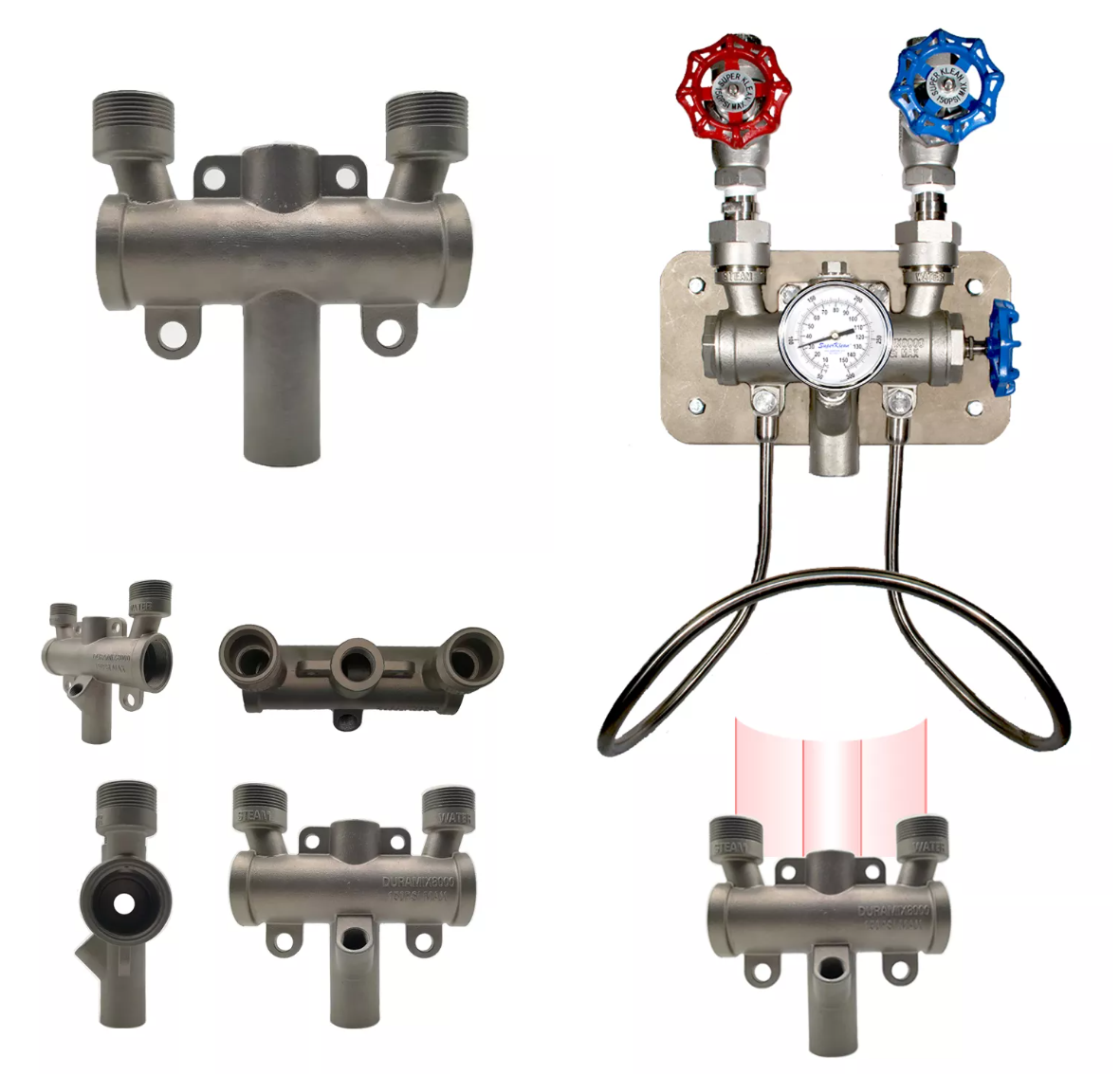
Our Case3 & Solutions:
Because the opening is too small, the inner cavity is small and complicated, and it is almost impossible to clean the internal sand core. Clean, so we opened a square hole on the back of the product, welded it with a stainless steel square plate, and opened a dovetail groove at the weld, which is conducive to a strong weld.
We also used a sand core that has both high-temperature strength and is easy to remove sand after high-temperature action to make this product. After the casting was processed, the air-tightness test was carried out, and was successful, so the product was mass-produced , and finally met the customer's requirements and won the trust of the customer.
Our Case4 & Solutions:
Therefore, we divided the wax mold of the part into upper and lower parts and made them separately, and then assembled the wax molds of the upper and lower parts into a whole.
The combined wax mold successfully passed the verticality tooling inspection procedure. , and finally all aspects of performance have met the customer's requirements, so the customer is very satisfied with our professional technical level and perfect product quality.