- Product Details
- {{item.text}}
Quick Details
-
Filling Accuracy:
-
±1%
-
Voltage:
-
220 / 380 V
-
Place of Origin:
-
Zhejiang, China
-
Brand Name:
-
EVERHEAL
-
Dimension(L*W*H):
-
7.8*2.2*2
-
Weight:
-
3000 KG
-
Bag-making Film:
-
NON-PVC
-
Specification:
-
100ml,250ml, 500ml.1000ml
-
Bag-making Form:
-
Single port, Heat insulation sealing
-
Auxiliary Equipments:
-
Leak Detector,Lamp Checking Machine etc
Quick Details
-
Machinery Capacity:
-
4000BPH, 8000BPH, 6000BPH, 400BPH, 2000BPH, 1000BPH, 200BPH, Other
-
Packaging Material:
-
Wood
-
Filling Material:
-
Water, Powder, Other
-
Filling Accuracy:
-
±1%
-
Voltage:
-
220 / 380 V
-
Place of Origin:
-
Zhejiang, China
-
Brand Name:
-
EVERHEAL
-
Dimension(L*W*H):
-
7.8*2.2*2
-
Weight:
-
3000 KG
-
Bag-making Film:
-
NON-PVC
-
Specification:
-
100ml,250ml, 500ml.1000ml
-
Bag-making Form:
-
Single port, Heat insulation sealing
-
Auxiliary Equipments:
-
Leak Detector,Lamp Checking Machine etc
Product Description
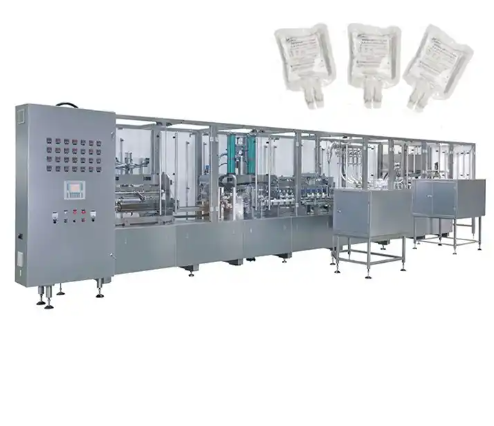
Specification
Condition
|
New
|
Type
|
Filling Machine
|
Machinery Capacity
|
4000BPH, 8000BPH, 6000BPH, 400BPH, 2000BPH, 1000BPH, 200BPH, Other
|
Applicable Industries
|
Manufacturing Plant, Medical
|
Showroom Location
|
Brazil, India, Russia, Nigeria, Uzbekistan
|
Application
|
Chemical, medical
|
Packaging Type
|
Cartons
|
Packaging Material
|
Wood
|
Automatic Grade
|
Automatic
|
Driven Type
|
Electric
|
Voltage
|
220 / 380 V
|
Place of Origin
|
China
|
|
Zhejiang
|
Brand Name
|
EVERHEAL
|
Dimension(L*W*H)
|
7.8*2.2*2
|
Weight
|
3000KG
|
Warranty
|
1 Year
|
Key Selling Points
|
Easy to Operate
|
Filling Material
|
Water, Powder, Other
|
Filling Accuracy
|
±1%
|
Machinery Test Report
|
Provided
|
Video outgoing-inspection
|
Provided
|
Warranty of core components
|
1 Year
|
Core Components
|
Motor, Pressure vessel, Pump, PLC, Gear, Bearing, Gearbox, Engine, Other
|
Bag-making Film
|
NON-PVC
|
Specification
|
100ml,250ml, 500ml.1000ml
|
Bag-making Form
|
Single port, Heat insulation sealing
|
Auxiliary Equipments
|
Leak Detector,Lamp Checking Machine etc
|
Model
|
Spec
|
Capacity
|
CS1
|
50-1000ml
|
800-1200BPH
|
CS2
|
50-1000ml
|
1800-2500BPH
|
CS4
|
50-1000ml
|
3200-4000BPH
|
CSD1
|
2000-4000ml
|
400-900BPH
|
CSD2
|
2000-4000ml
|
700-1600BPH
|
CSM
|
Multi-Chamber Bag
|
400-800BPH
|
Key Functions and Introduction:
Efficient Filling and Sealing:
Automatically completes the filling and sealing of non-PVC IV bags, enhancing production efficiency.
Filling Precision:
Ensures precise filling of medication or solution into each IV bag to guarantee product consistency and quality.
Sterile Operations:
Maintains a sterile environment throughout the filling and sealing process to ensure the prepared infusion fluid is sterile.
Customizability:
Can be adjusted and configured according to customer requirements to meet various specifications and demands of IV bags.
Data Tracking and Recording:
Collects and records production data for tracking and verifying process consistency and compliance.
Key Components
Film Roll Module:
Unwinds and supplies IV bag film material, providing the raw material for bag formation.
Bag Forming System:
Shapes the film material into individual IV bags, creating the structure for holding liquids.
Filling System:
Precisely injects liquid, ensuring accurate dosage of medication or solution.
Bag Cutting Module:
Cuts and separates filled bags from the continuous film material, forming sealed IV bags.
Sealing Mechanism:
Securely seals the filled bags, preventing leakage and maintaining content integrity.
Sterilization System:
Maintains a sterile environment throughout the process, ensuring the safety and quality of IV bags.
Control Panel:
Controls and monitors machine operations, allowing real-time parameter adjustments and performance monitoring.
Conveyor System:
Efficiently transports IV bags, facilitating continuous and seamless production.
4 Why Choose Us:
Pharmaceutical-Grade Purity:
Our line is manufactured using pharmaceutical grade stainless steel and high efficiency purification processes,ensuring it delivers high purity and meets the hygiene and quality standards essential for pharmaceutical and medical facilities
Strict Manufacturing Processes and Quality Control:
We follow strict manufacturing processes and quality checks. Every generator undergoes thorough testing and inspection before it'sshipped to ensure it provides a stable supply of steam during continuous operations. This reduces the risk of steam quality related issues in pharmaceutical production
Deployment of Experienced Engineers to Customer Facilities:
We dispatch experienced engineers to our customers' facilities. During the installation process, they supervise the equipment installation, ensuring that every component is correctly and accurately configured. Additionally, they provide detailed operating instructions to ensure customers can fully utilize the equipment's capabilities for efficient production.
Over 10 Years of Project Experience:
With over 10 years of successful project experience providing water purification solutions to the pharmaceutical industry,Our
expertise and experience serve as strong support for the success of your projects.
Efficient Filling and Sealing:
Automatically completes the filling and sealing of non-PVC IV bags, enhancing production efficiency.
Filling Precision:
Ensures precise filling of medication or solution into each IV bag to guarantee product consistency and quality.
Sterile Operations:
Maintains a sterile environment throughout the filling and sealing process to ensure the prepared infusion fluid is sterile.
Customizability:
Can be adjusted and configured according to customer requirements to meet various specifications and demands of IV bags.
Data Tracking and Recording:
Collects and records production data for tracking and verifying process consistency and compliance.
Key Components
Film Roll Module:
Unwinds and supplies IV bag film material, providing the raw material for bag formation.
Bag Forming System:
Shapes the film material into individual IV bags, creating the structure for holding liquids.
Filling System:
Precisely injects liquid, ensuring accurate dosage of medication or solution.
Bag Cutting Module:
Cuts and separates filled bags from the continuous film material, forming sealed IV bags.
Sealing Mechanism:
Securely seals the filled bags, preventing leakage and maintaining content integrity.
Sterilization System:
Maintains a sterile environment throughout the process, ensuring the safety and quality of IV bags.
Control Panel:
Controls and monitors machine operations, allowing real-time parameter adjustments and performance monitoring.
Conveyor System:
Efficiently transports IV bags, facilitating continuous and seamless production.
4 Why Choose Us:
Pharmaceutical-Grade Purity:
Our line is manufactured using pharmaceutical grade stainless steel and high efficiency purification processes,ensuring it delivers high purity and meets the hygiene and quality standards essential for pharmaceutical and medical facilities
Strict Manufacturing Processes and Quality Control:
We follow strict manufacturing processes and quality checks. Every generator undergoes thorough testing and inspection before it'sshipped to ensure it provides a stable supply of steam during continuous operations. This reduces the risk of steam quality related issues in pharmaceutical production
Deployment of Experienced Engineers to Customer Facilities:
We dispatch experienced engineers to our customers' facilities. During the installation process, they supervise the equipment installation, ensuring that every component is correctly and accurately configured. Additionally, they provide detailed operating instructions to ensure customers can fully utilize the equipment's capabilities for efficient production.
Over 10 Years of Project Experience:
With over 10 years of successful project experience providing water purification solutions to the pharmaceutical industry,Our
expertise and experience serve as strong support for the success of your projects.
Hot Searches