- Product Details
- {{item.text}}
Quick Details
-
Weight (KG):
-
140
-
Machine Type:
-
Metal Polishing Machine
-
Capacity (L):
-
120
-
Size L*W*H(mm):
-
1700*1380*1410
-
Motor (kw):
-
4
-
Weight (kg):
-
1100
-
Speed (rpm):
-
0-60
-
Chamber dimension (mm):
-
640
-
PU thickness (mm):
-
26
-
Supplier by Area:
-
Asia
-
Suppliers by Country/Region:
-
China
Quick Details
-
Place of Origin:
-
Zhejiang, China
-
Brand Name:
-
HUMO
-
Power (kW):
-
0.75
-
Weight (KG):
-
140
-
Machine Type:
-
Metal Polishing Machine
-
Capacity (L):
-
120
-
Size L*W*H(mm):
-
1700*1380*1410
-
Motor (kw):
-
4
-
Weight (kg):
-
1100
-
Speed (rpm):
-
0-60
-
Chamber dimension (mm):
-
640
-
PU thickness (mm):
-
26
-
Supplier by Area:
-
Asia
-
Suppliers by Country/Region:
-
China
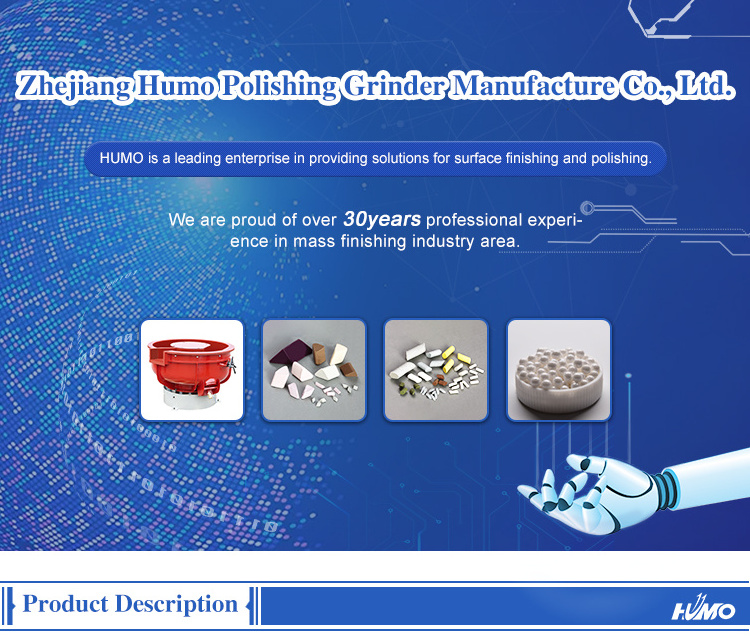
Specifications
1 Rotary Finishing Machine for metal deburring and finishing .
2 Good finishing machine with CE cert. at low price
3 Works fast
Rotary finishing machine consist of working barrel, motor, electrical box and base.
Barrel: It is consist of rotary disk in the bottom, and a good quality stainless steel plate welded barrel. The barrel is lined
with high quality wearable PU lining to avoid work-pieces hitting the side of the barrel.
Motor: It is under the rotary disk and drive the disk to rotate.
Electrical box: made of cold-roll steel plate. It is fixed on the side of the barrel. All CE certificated and good quality
components are in the box and the control panel is on the front side of electrical box.
Base: It is welded by high quality steel plate. And there is a sink to hold water coming from barrel in the middle of the base.
2. Function:
Tonzze rotary finishing machines are used for grinding, de-burring, chamfering and polishing all kinds of metal stamping parts,metal castings, rigid plastic, etc. And the grinding machines are applied into the industries of horologe, eyeglass, lock manufacturing, ornaments & jewellery, electronics, art ware, machinery and hardware, etc.
3. Working Principle.
When the rotating disk is rotating, an opposite force makes the mixed grinding stones and workpieces in the barrel stir all around and burnish each other. Thus the grinding machine finishes, grinds and polishes the surface of the workpieces in a very short time. The lining of the grinding tub is gear-teeth designed, and the bottom is uneven designed. These make the workpieces and the abrasives have a better proportioned grinding.
4. Packing details.
The whole machine will be packed in a firm plywood case for shipping.
1 Rotary Finishing Machine for metal deburring and finishing .
2 Good finishing machine with CE cert. at low price
3 Works fast
Centrifugal Disc Manual Discharging Finishing
Machine
1. Structure:
Rotary finishing machine consist of working barrel, motor, electrical box and base.
Barrel: It is consist of rotary disk in the bottom, and a good quality stainless steel plate welded barrel. The barrel is lined
with high quality wearable PU lining to avoid work-pieces hitting the side of the barrel.
Motor: It is under the rotary disk and drive the disk to rotate.
Electrical box: made of cold-roll steel plate. It is fixed on the side of the barrel. All CE certificated and good quality
components are in the box and the control panel is on the front side of electrical box.
Base: It is welded by high quality steel plate. And there is a sink to hold water coming from barrel in the middle of the base.
2. Function:
Tonzze rotary finishing machines are used for grinding, de-burring, chamfering and polishing all kinds of metal stamping parts,metal castings, rigid plastic, etc. And the grinding machines are applied into the industries of horologe, eyeglass, lock manufacturing, ornaments & jewellery, electronics, art ware, machinery and hardware, etc.
3. Working Principle.
When the rotating disk is rotating, an opposite force makes the mixed grinding stones and workpieces in the barrel stir all around and burnish each other. Thus the grinding machine finishes, grinds and polishes the surface of the workpieces in a very short time. The lining of the grinding tub is gear-teeth designed, and the bottom is uneven designed. These make the workpieces and the abrasives have a better proportioned grinding.
4. Packing details.
The whole machine will be packed in a firm plywood case for shipping.
Model
|
Capacity(L)
|
Size
L×W×H(mm) |
Motor (kw)
|
Weight (kg)
|
Speed (rpm)
|
Chamber dimension
(mm) |
PU thickness(mm)
|
LDG50A
|
50
|
1390×700×1240
|
1.5
|
400
|
50-180
|
460
|
22
|
LDG50
|
50
|
1000×660×1120
|
1.5
|
300
|
50-180
|
460
|
22
|
LDG120
|
120
|
1740×900×1470
|
4.0
|
600
|
50-160
|
640
|
26
|
LDG230
|
230
|
1620×1008×1135
|
7.5
|
1100
|
0-140
|
800
|
30
|
Model
|
Total volume(L)
|
Power of the motor(mm)
|
Rotary speed(kw)
|
Unload motor(kg)
|
Unloading tilt angle(rpm)
|
Size
L×W×H(mm) |
Weight of the machine(kg)
|
LDG50S
|
50
|
1.5
|
50-180
|
0.37
|
105°
|
1230×750×1730
|
300
|
Model
|
Capacity
(L) |
Size
L×W×H(mm) |
Motor (kw)
|
Weight (kg)
|
Speed (rpm)
|
Chamber dimension
(mm) |
PU thickness (mm)
|
LDG50AB
|
50
|
1565×660×1300
|
1.5
|
450
|
50-180
|
460
|
22
|
LDG50B
|
50
|
1010×660×1220
|
1.5
|
350
|
50-180
|
460
|
22
|
LDG120B
|
120
|
1700×1380×1410
|
4.0
|
1100
|
0-160
|
640
|
26
|
LDG230B
|
230
|
2450×1700×2000
|
7.5
|
2000
|
0-140
|
800
|
30
|
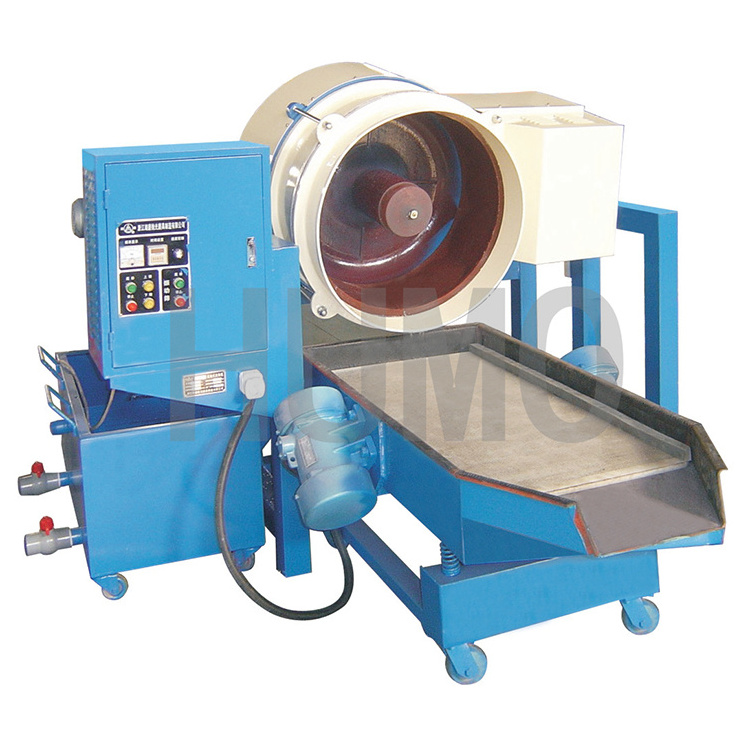
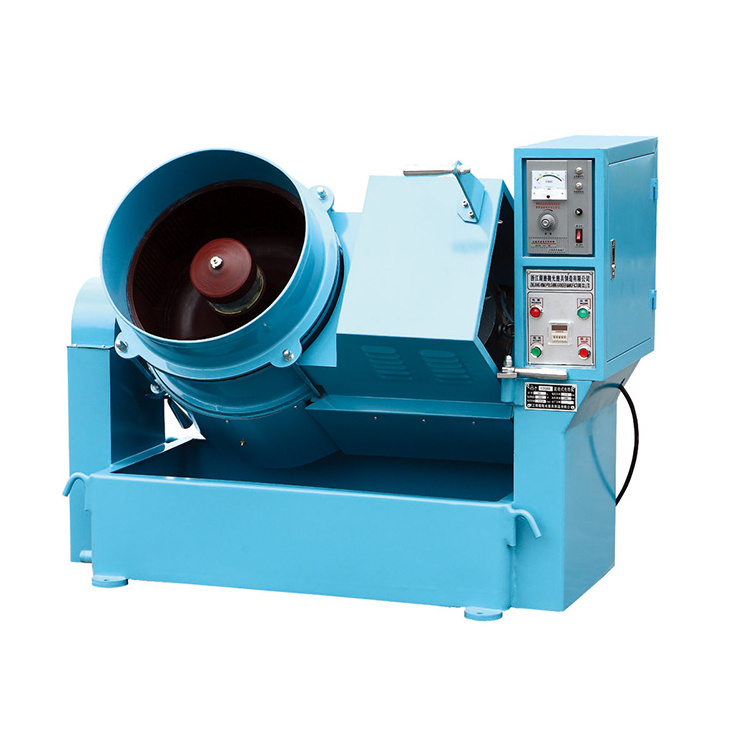
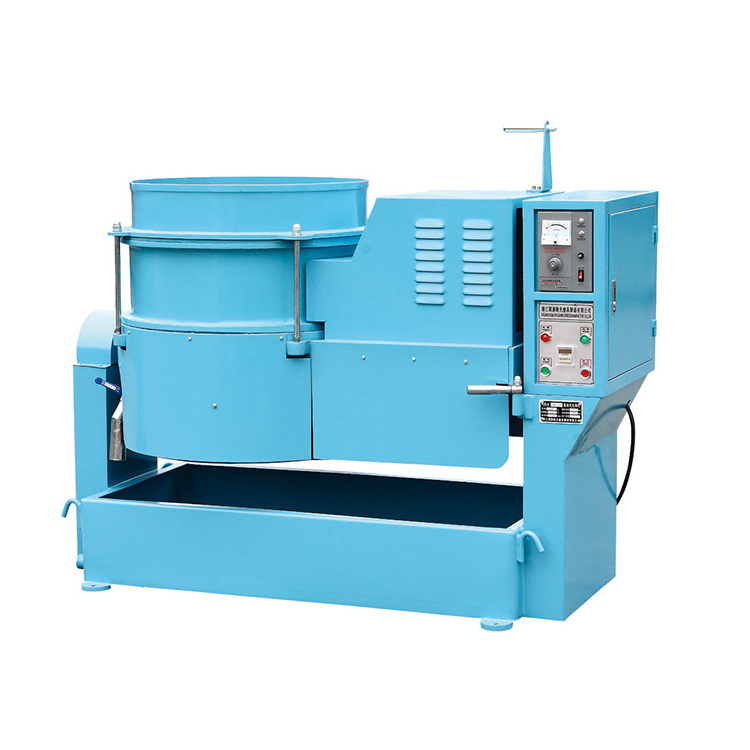
FAQ
Our laboratory services are available to you at no cost. Mass Finishing and determination of Process Capability allows you to use the right media to ensure consistent production capability and built-in reproducibility of your manufacturing processes. We will work with you to determine the best media and the best processes for your parts. This step can result in:
* Reduced Cycle Times
* Improved RMS Finishes
* Reduced Finishing Costs
* Access to Latest Technology
* R & D for Special Process Media
Mass Finishing describes a mechanical process where large amounts of parts are economically processed to achieve one or several surface improvement functions. These surface improvement functions include:
* Cleaning
* Deburring
* Surface refinement
* Inhibiting
* Drying
These functions are not independent of each other. It is common to have several or all of these functions take place in a single mass finishing process.
Process Capability is the measured, built-in reproducibility of the product turned out by the process. Such a determination is made using statistical data, not wishful thinking. Statistically determined limits are compared to specification limits to decide if a process can consistently produce acceptable product. Process capability is best established through closely monitored testing and recording of data over a set period of actually production.
* Reduced Cycle Times
* Improved RMS Finishes
* Reduced Finishing Costs
* Access to Latest Technology
* R & D for Special Process Media
Mass Finishing describes a mechanical process where large amounts of parts are economically processed to achieve one or several surface improvement functions. These surface improvement functions include:
* Cleaning
* Deburring
* Surface refinement
* Inhibiting
* Drying
These functions are not independent of each other. It is common to have several or all of these functions take place in a single mass finishing process.
Process Capability is the measured, built-in reproducibility of the product turned out by the process. Such a determination is made using statistical data, not wishful thinking. Statistically determined limits are compared to specification limits to decide if a process can consistently produce acceptable product. Process capability is best established through closely monitored testing and recording of data over a set period of actually production.
Hot Searches