layered cutting geometry design, ring cutting, reduce power consumption, high efficiency and energysaving.
- Product Details
- {{item.text}}
Quick Details
-
Warranty:
-
1 Year
-
Place of Origin:
-
China
-
Application:
-
Cutting
-
Material:
-
TCT tips+ Alloy Steel
-
Size:
-
25mm
-
MOQ:
-
50 PCS
-
Color:
-
Silver
-
OEM:
-
Customized
-
Brand:
-
LARIX
-
Package:
-
Plastic Tube
-
Shank Type:
-
Weldon Shank Cutter
-
Depth of cutting:
-
35mm
Quick Details
-
Type:
-
Core Drill Bit
-
Use:
-
Metal Drilling
-
Finish:
-
Plain
-
Warranty:
-
1 Year
-
Place of Origin:
-
China
-
Application:
-
Cutting
-
Material:
-
TCT tips+ Alloy Steel
-
Size:
-
25mm
-
MOQ:
-
50 PCS
-
Color:
-
Silver
-
OEM:
-
Customized
-
Brand:
-
LARIX
-
Package:
-
Plastic Tube
-
Shank Type:
-
Weldon Shank Cutter
-
Depth of cutting:
-
35mm
Product Description
Larix Hot Sale
TCT Annular Cutter Core Drill Hole Cutter with Weldon Shank
Carbide Tips
: Tungsten carbide tipped weldon shank annular cutter, the other part are alloy steel, sharper than HSS annular cutters.
Weldon Shank
: Applicable to hole cutting and process of annular groove on various magnetic drills and press,can also be used with machine tools such as mills and large drill presses with tool holders.
Better Performance
: Selected special-purpose carbide tip with multi-cut geometry for ply-cutting and lower friction,reduced damage of tips and improved performance of chips removal.
Widely Usage
: Applicable materials include various steel material, steel plate, stainless steel, aluminum, brass, cast iron, etc.
Material
|
Carbide Tips+Alloy Steel
|
Cutting Diameter
|
12--120MM
|
Cutting Deepth
|
35/50MM
|
Shank Style
|
Weldon
|
Finish
|
White Sand
|
MOQ
|
50 PCS
|
OEM
|
Acceptable
|
Packing
|
One Piece in One Plastic Tube
|
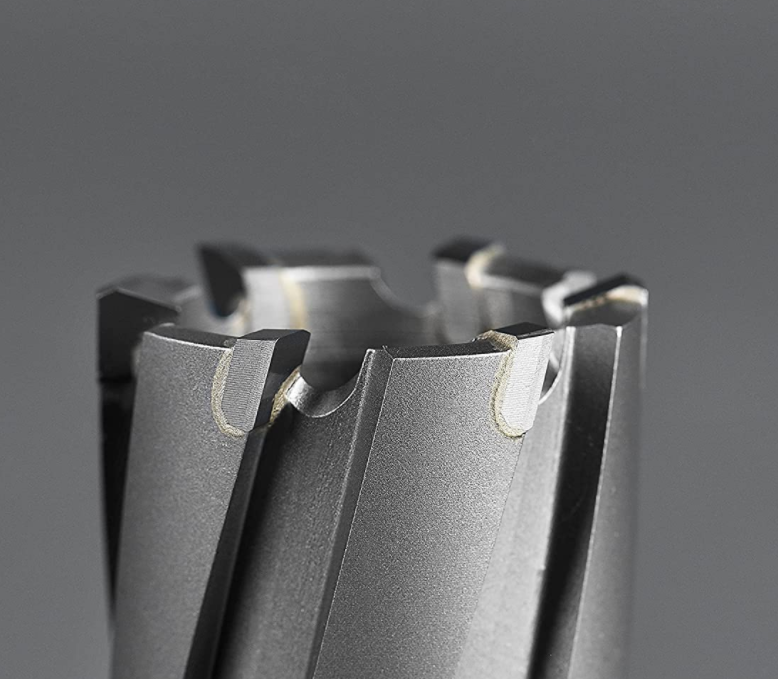
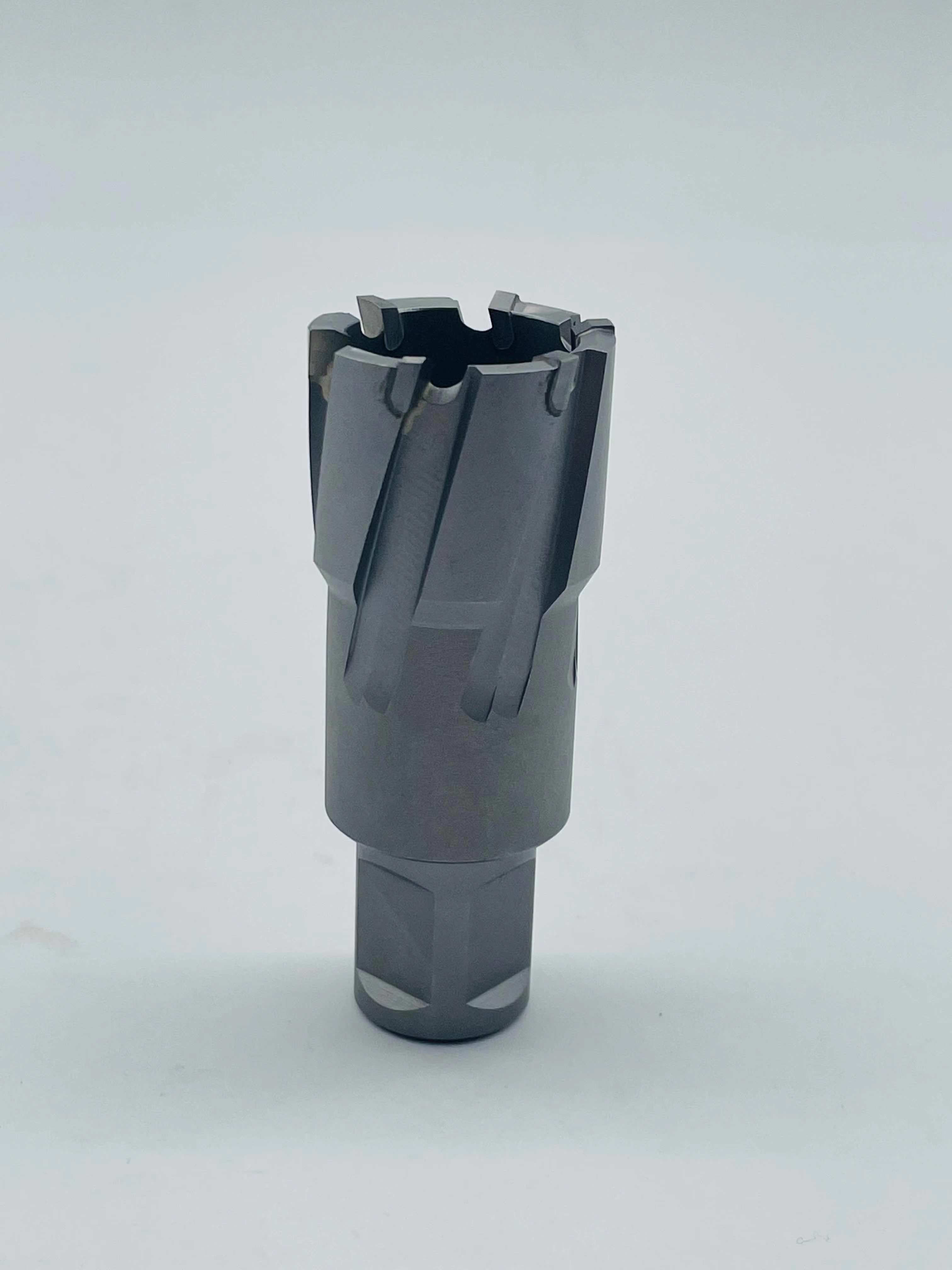
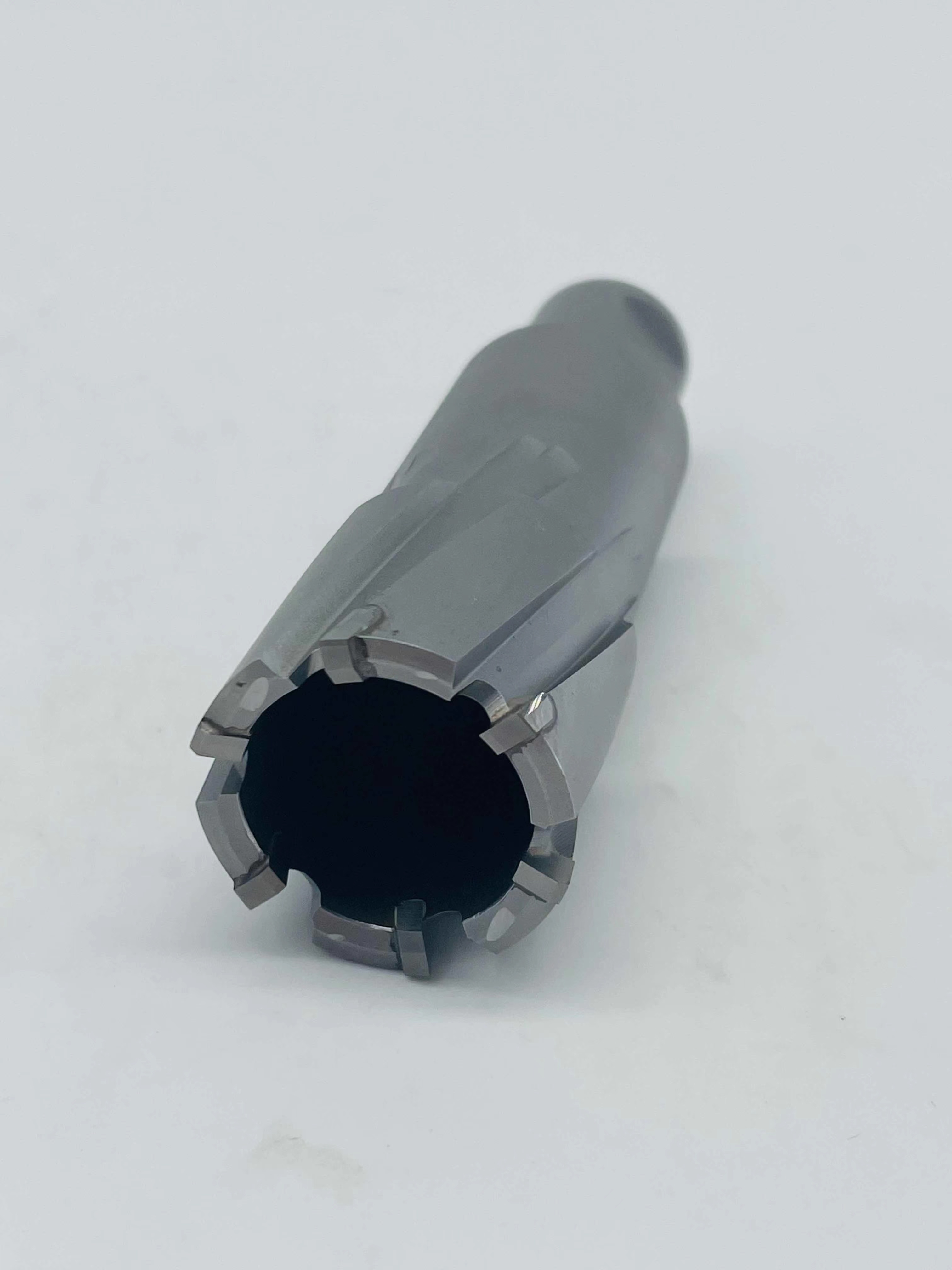
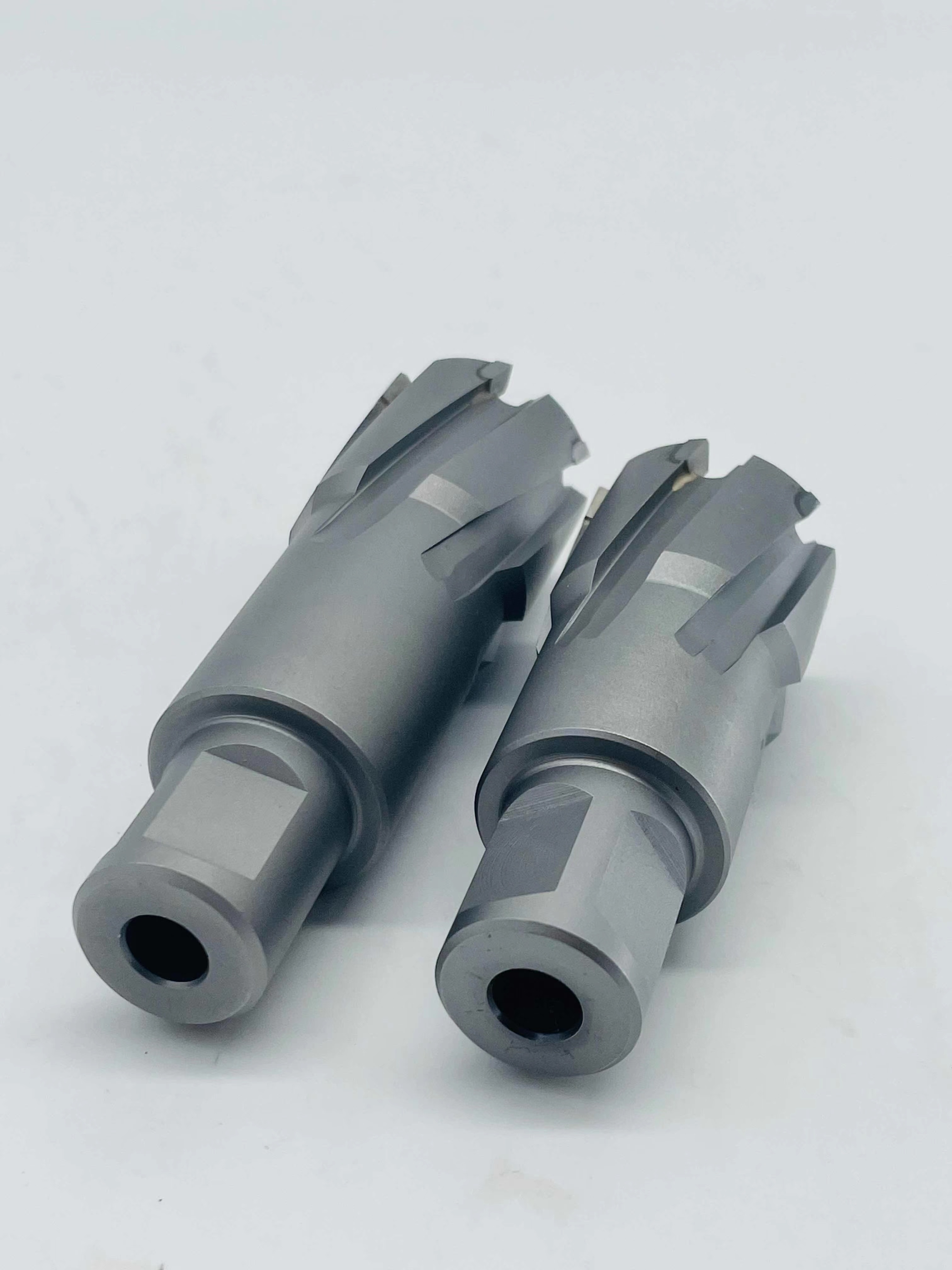
Highly Recommended
Specification
large capacity chute, unique spiral groove design, chipping is smooth, easy and quick.
weldon shank, with more stable clamping for stable cutting and finish of holes, shank diameter 3/4 inch(19.05mm), suitable for 120 degree, three points bolt, fastening for fast loading and unloading chuck bit clamp interface.
COMPARE WITH HSS ANNULAR CUTTER AND WHY YOU SHOULD CHOOSE TCT ANNULAR CUTTER?
1.The biggest advantage of TCT annular cutters is
speed and ease
in which it may cut harder materials, especially for boring larger diameter holes in hard materials, TCT cutters can be used to great success.
2.The linear
speed requirement
is higher than that of HSS.
3.The teeth on TCT annular cutters are
harder
than HSS, allowing them to cut more difficult materials.
* Wear protective equipment during operation
* Ensure the drill and metal sheet are secured
* Set appropriate RPM and feed rate
* Must use with coolant during drilling
1. What causes annular cutters to break or dull prematurely?
The primary cause of broken or prematurely dull cutters is a feed rate that is too slow. Slow feed rates will reduce the life of your cutter. Using a firm, steady feed pressure throughout the cut will maximize performance and extend tool life.
2. Why do I have to clear chips from the cutter before every cut?
As the cutter begins removing material, new chips flow out through the gullets and up the flutes. If these pathways are not cleared before cutting a new hole, packing or binding may result, causing the cutter to fill with chips and possibly break. Because annular cutters are hollow, there is no dead-zone resistance to overcome. All cutting edges are located near the
periphery of the tool, and surface speeds are consistent throughout the entire cut.
3. When do I use a magnetic drill?
It can be time-consuming and cumbersome to try to jockey a large pipe into position at a stationary drill press or work center. A portable magnetic drill allows you to take the drill to the work-piece, instead of trying to bring the work-piece to the drill. A portable magnetic drill press also may be used in any position—vertical, horizontal, or overhead. The work-piece must be at least 3/8 inch thick.
4. Is the magnet on my portable drill press strong enough to drill pipe?
When you're using a portable drill press, a support system is needed. A safety chain or strap is also recommended, in case the magnet slips from the support. When you are using a magnetic drill and pipe adapter accessory, mount the adapter securely to the pipe with a tightly wrapped chain (see lead image). Make sure the support system for the drill arbor is rigid and in good condition.
5. How do I keep my magnetic drill from slipping?
Make sure the drill's magnetic base is clear of chips and debris and is securely attached to a clean work-piece. Uneven surfaces or large debris buildup prevents the magnet from obtaining optimal holding power, which can cause the drill to shift or lift during operation. A safety chain or strap also helps to prevent injury if the drill shifts. If it does shift or lifts during the cut, and the motor is not stopped, the cutter will break. A good magnetic drill will have a built-in safety circuit that stops the motor immediately when the drill lifts from the material.
6. What is the purpose of coated cutters, or cutters made from premium steel?
Cutters made from M2 high-speed steel (HSS) are recommended for materials with a Brinell hardness number (BHN) of up to 275. A titanium nitride or similar coating may be applied to M2 to fortify wear resistance in materials up to 325 BHN. For materials up to 350 BHN (Brinell hardness number), cobalt steel (M35) is recommended with a titanium nitride or similar coating.
7. What makes the slug stick in the cutter?
Using lubricant or cutting fluid helps the slug to eject at the end of the cut. But when slug ejection becomes unreliable or the tube resists cutting, it probably means the cutter's cutting edges are becoming dull. Resharpen or replace your cutter.
8. Is coolant necessary?
Always use some form of coolant when drilling to maintain cutting performance and tool life. Any form of coolant or lubrication helps—even water works better than nothing at all.
9. What happens when my portable drill press becomes loose or parts wear out?
For the best performance, always maintain your drill as instructed in the operator's manual. Many magnetic drills feature a slide/gib/way system that requires periodic adjustments to maintain rigidity and optimal performance. Worn or damaged parts should be replaced to reduce the possibility of injury.
10.
Feed rate
Construction and stainless steel...............0.08-0.12 mm / rpm
Cast iron......................................................0.12-0.20 mm / rpm
Non-ferrous metals.....................................0.22-0.45 mm / rpm
Special alloys...............................................0.05-0.08 mm / rpm
* At the start of your drilling job, cut the feed from above mentioned recommendations in half.
* Remember that excessive pressure on the annular cutter will not increase performance!
* When drilling fragile material try to drill in one go, so without making stops
* When processing speed is important then use Tungsten Carbide Tipped (TCT) annular cutters and a magnetic drilling machine with increased rotational speed.
* If you have to apply significant effort, perhaps the annular cutter has become dull or the material being drilled is too hard for this type of annular cutter.
11. Maintenance recommendations
lean the annular cutter periodically. When drilling holes deeper than 30 mm repeat the following steps every 20 - 30 mm:
* Take out the annular cutter and clean it from chips;
* Lubricate the hole with cutting lubricant or paste;
* Continue drilling with lower feed.
Construction and stainless steel...............0.08-0.12 mm / rpm
Cast iron......................................................0.12-0.20 mm / rpm
Non-ferrous metals.....................................0.22-0.45 mm / rpm
Special alloys...............................................0.05-0.08 mm / rpm
* At the start of your drilling job, cut the feed from above mentioned recommendations in half.
* Remember that excessive pressure on the annular cutter will not increase performance!
* When drilling fragile material try to drill in one go, so without making stops
* When processing speed is important then use Tungsten Carbide Tipped (TCT) annular cutters and a magnetic drilling machine with increased rotational speed.
* If you have to apply significant effort, perhaps the annular cutter has become dull or the material being drilled is too hard for this type of annular cutter.
11. Maintenance recommendations
lean the annular cutter periodically. When drilling holes deeper than 30 mm repeat the following steps every 20 - 30 mm:
* Take out the annular cutter and clean it from chips;
* Lubricate the hole with cutting lubricant or paste;
* Continue drilling with lower feed.
❤All these factors directly affect the conditions and lifetime of the annular cutter. Therefore, if you want to expand the lifetime of your annular cutter and achieve maximum efficiency keep these factors in mind and never forget to check all other machine components. If you have any questions, please feel free to ask. I am here for you.
Packing & Delivery
Services
- Reply your inquiry within 12 hours.
- Experienced staffs answer all your questions in professional Manner, proficient in English.
- Customized design is available. OEM&ODM are warmly welcomed.
- Exclusive and unique solution can be provided to our customer by our well-trained and professional engineers and staffs.
Hot Searches