2.
Grinding can give full play to the activity of the material;The ground slurry has better water retention and higher viscosity due to the dissolution of some components , which can make the slurry have proper consistency and liquidity
- Product Details
- {{item.text}}
Quick Details
-
Brick size:
-
customizable
-
Processing:
-
Molding,cutting,steamed
-
Place of Origin:
-
Linyi Shandong
-
Voltage:
-
customizable
-
Marketing Type:
-
New Product
-
Warranty of core components:
-
1 years
-
Weight (KG):
-
100000 kg
Quick Details
-
Type:
-
Autoclaved aerated concrete block (AAC)
-
Brick Raw Material:
-
sand/ fly ash,lime, cement,Aluminum powder
-
Production Capacity (Pieces/8 hours):
-
Customize as your need
-
Brick size:
-
customizable
-
Processing:
-
Molding,cutting,steamed
-
Place of Origin:
-
Linyi Shandong
-
Voltage:
-
customizable
-
Marketing Type:
-
New Product
-
Warranty of core components:
-
1 years
-
Weight (KG):
-
100000 kg
Product Description
AAC Block & Panel Production Line
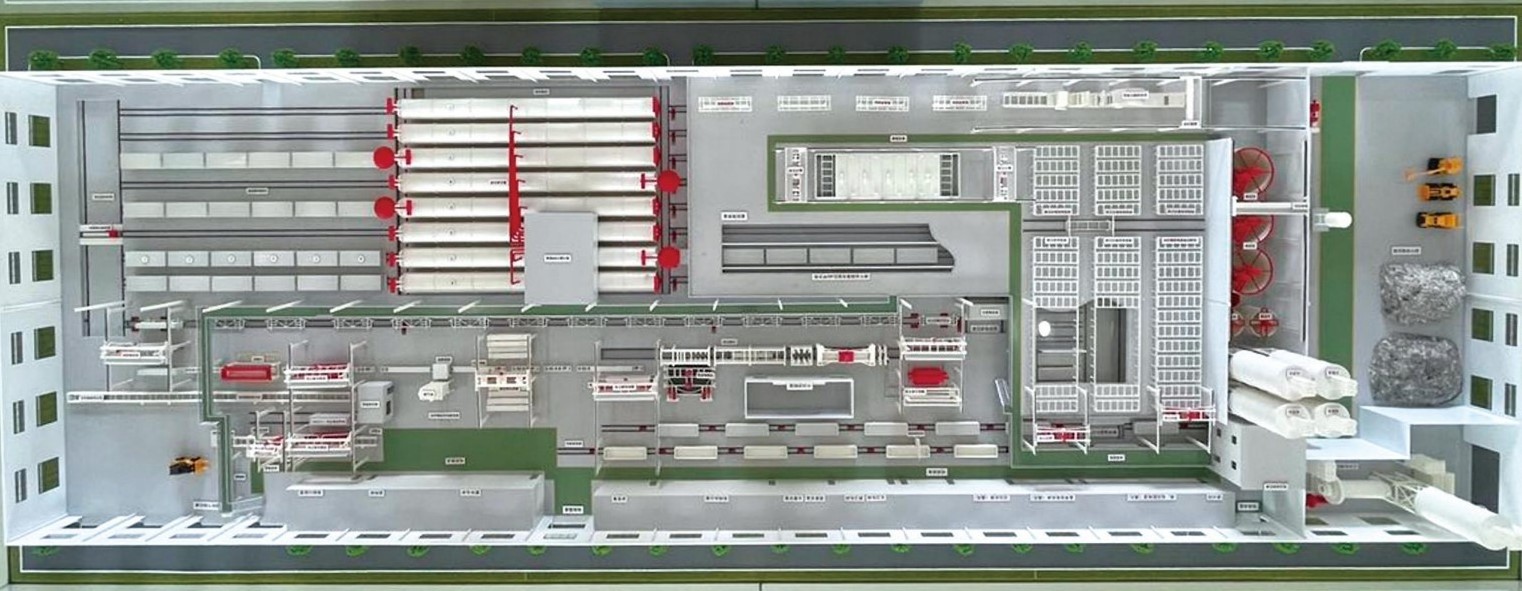
What is AAC ?
AAC
is the abbreviation of
Autoclaved aerated concrete,
It is a new type of light weight , thermal insulation building material .The raw material are siliceous materials (such as fly ash, sand) and calcareous materials (lime and cement) ,made by batching, pouring, expansion, cutting, curing and other processes.
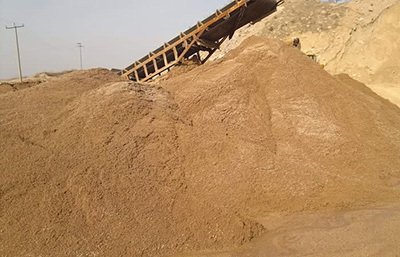
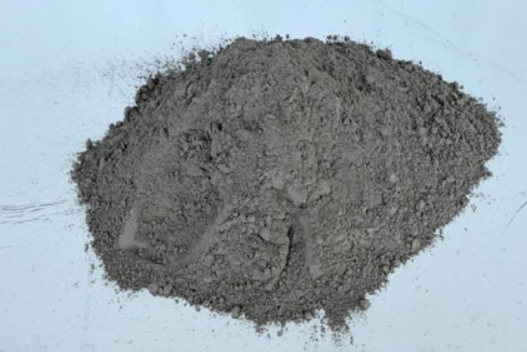
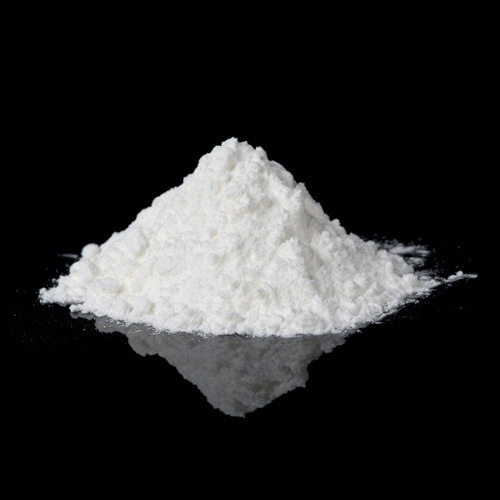
1.Sand is widely used siliceous material in aerated concrete industry . The main function of sand is to provide SiO2.
2.T
he role of fly ash in AAC is also to provide SiO2.And the Al2O3 in fly ash can give large effect during
static stop
after the casting process .
3.
Lime is the main calcareous material in the production process. Its main function is to provide calcium oxide, so that it can react with SiO2 and Al2O3 in the siliceous material under hydrothermal conditions to form calcium silicate hydrate, so that the product can gain strength.
Finely ground quicklime is used in the production process.
4.
Cement is a hydraulic cementitious material, Portland cement is suitable for AAC.
Sand /Fly ash
|
Cement
|
Lime
|
Gypsum
|
Aluminum powder
|
65-70%
|
10-12%
|
12-15%
|
3%
|
0.5kg/CBM
|
Finished products and application
AAC has the characteristics of light weight and good thermal insulation performance. panels and blocks are widely used in industrial and civil buildings,
Such as hospitals, schools, shopping malls, etc.
Production Process Introduction
The production process includes raw material preparation, batching pouring, static stop curing, cutting, autoclaving curing, , exiting from the kettle and packing .
Raw Material Preparation
1.
Raw materials need to be ground before being processed. In order to meet the fineness requirements of the feed, block materials such as quicklime and natural gypsum need to be crushed.
Material Batching and Pouring
1.Measure various raw materials, adjust the temperature and concentration, and feed materials to the mixing equipment in sequence according to the process requirements
2.
The pouring process is one of the unique processes that distinguish aerated concrete from other concretes. The prepared raw materials are stirred to meet the specified time temperature and consistency requirements to obtain slurry, then pour into the mold.
3.
Pouring and batching can be controlled separately or centrally, and different degrees of automation can be realized
Static Maintenance
1.The poured mold is pushed into the resting room with a conveyor chain for initial gas generation and initial setting. The room temperature is 50-70°C, and the time is 1.5-2 hours.
2.
The resting process is mainly to promote the slurry to continue to complete the hardening process, so that the embryo body reaches a certain hardness for cutting
Cutting
The cutting process is to divide and shape the AAC body to meet the appearance and size requirements. The cutting process reflects the characteristics of air-entrained concrete, which is convenient for large-volume molding, flexible and diverse in shape and size, and large-scale mechanized production
Autoclaving Curing
The autoclave curing process is to perform high-pressure steam curing on the cut aerated concrete body, and complete the hydrothermal reaction of CaO-SiO2-H2O in the kettle
Packing
This is the last process of production, including
pull out the finished products form kettle
, lifting, inspection, packaging and cleaning and oiling of the bottom plate of the trolley
Specification
Ball Mill
Main body: Q235B, plate thickness: δ22mm;
Large gear material: ZG45#; small gear material: ZG40Cr
Liner material: rubber liner; tile body: rolling bearing.
Pouring Mixer
Double cross impellers are used to achieve high-speed mixing. The mixing impellers are cast with high-strength hard nickel alloy, which has high strength and wear resistance.
Mold
The bottom frame of the mold is processed as a whole, and it is assembled and welded by professional tooling. The mold adopts the butterfly spring rocker locking method to ensure that the mold is completely attached to the side plate
Somersault demoulding machine
Lifting, unlocking and turning of the spreader are all driven by hydraulic pressure
Driven by servo drive
Cutting Machine Group
*The side cutting machine realizes the automatic advance and retreat of the knife according to the different width requirements of the plate and the block
*Horizontal cutting machine adopts full-column wire groove
*The vertical cutting machine adopts the frame pendulum hanging cage type
Lifting board breaking machine
The clamping and splitting of this equipment are all driven by hydraulic pressure.
The separation of the plate breaking machine adopts the servo motor hydraulic station, which is energy-saving and environmentally friendly, and the flow pressure is well controllable
Customer Case
Our Service
Three quality inspections will be carried out before the equipment leaves the factory to ensure that each process is kept improving
During the installation process, the technical department will participate in the review of the drawings to prevent errors caused by the installation
When debugging the equipment, the internal technical personnel of the company will be organized for acceptance evaluation
Provide pre-sale data analysis, process planning, raw material testing
Provide a project team during the sale to assist in the acceptance of civil engineering process debugging and formula, management and practical training
After-sales provides engineers with regular return visits and new word An County maintenance upgrade plan
Certifications
Packing & Shipping
Our Factory
Hot Searches