- Product Details
- {{item.text}}
Quick Details
-
Power:
-
420KW-3000KW
-
Dimension(L*W*H):
-
Customizable
-
Weight:
-
100000 kg
-
Product Name:
-
Mini Cement Plant
-
Color:
-
Customers' Requirements
-
Application:
-
Cement Clinker, Limestone
-
After Sale Service:
-
Engineer Overseas Service
-
Motor:
-
Chinese Brand
-
Factory:
-
50,000 Square Meters Closed Workshops
-
Installation and Trial:
-
We Can Send Engineer for Guidance
-
Fuel:
-
Coal, Mazut, Gas etc.
-
Certification:
-
ISO9001 CE, ISO9001:14000
-
Advantage:
-
Timely Delivery and Installation, Fast Technical Support
Quick Details
-
Place of Origin:
-
Henan, China
-
Brand Name:
-
ZOOMJO
-
Voltage:
-
220v, 380v, 440v
-
Power:
-
420KW-3000KW
-
Dimension(L*W*H):
-
Customizable
-
Weight:
-
100000 kg
-
Product Name:
-
Mini Cement Plant
-
Color:
-
Customers' Requirements
-
Application:
-
Cement Clinker, Limestone
-
After Sale Service:
-
Engineer Overseas Service
-
Motor:
-
Chinese Brand
-
Factory:
-
50,000 Square Meters Closed Workshops
-
Installation and Trial:
-
We Can Send Engineer for Guidance
-
Fuel:
-
Coal, Mazut, Gas etc.
-
Certification:
-
ISO9001 CE, ISO9001:14000
-
Advantage:
-
Timely Delivery and Installation, Fast Technical Support
Product Description
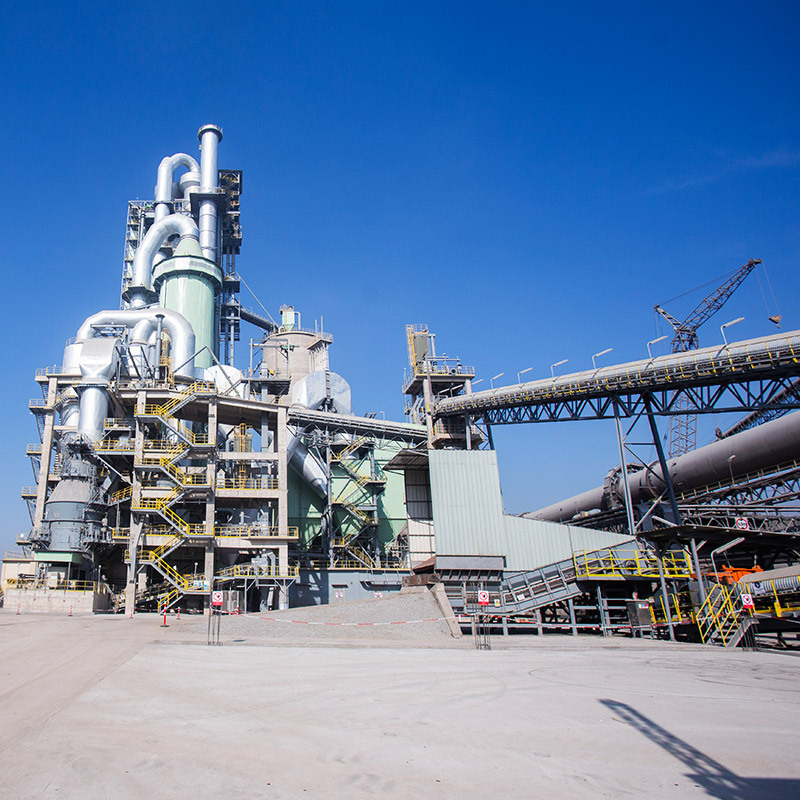
Cement production line is the process of producing cement by crushing, preheating, calcining and grinding the raw materials limestone, clay and iron ore.
Cement production line is the main process of cement production, including the following main steps:
1. raw material crushing:
the raw material limestone, clay and iron ore are crushed into a certain particle size by crusher.
2. raw material preheating:
the crushed raw materials will be heated to a certain temperature through the preheating furnace to
remove the moisture and impurities.
3. Calcination of raw materials:
The preheated raw materials are calcined into cement clinker by rotary kiln.
4. Cement clinker grinding:
cement clinker is ground into cement powder by ball mill.
5. Cement packing:
the cement powder is packed into cement bags through packing machine.
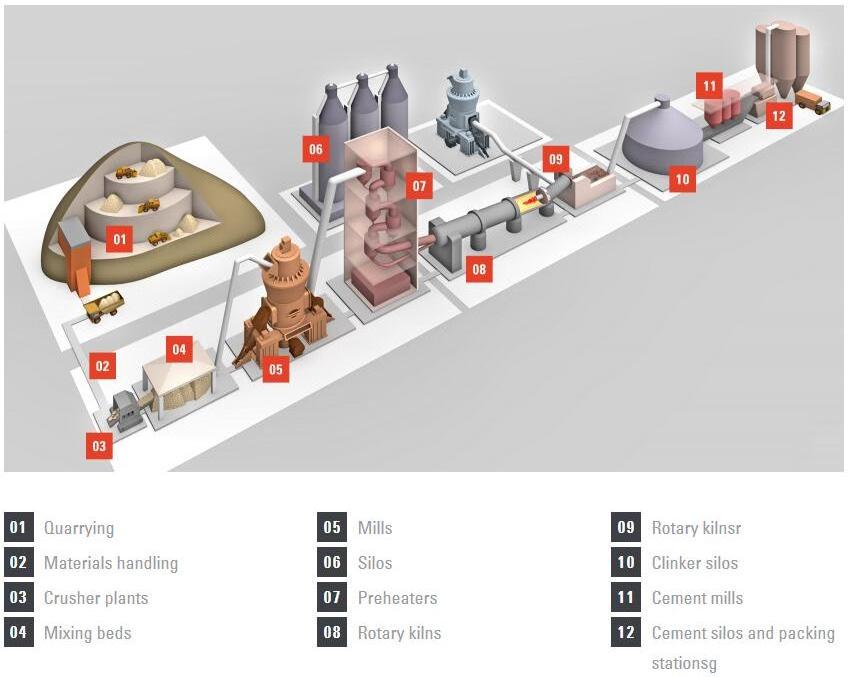
The cement production line produced by ZOOMJO has the following advantages.
1. Adoption of advanced technology to ensure high level of technical indexes.
2. Using energy-saving equipment such as chain conveyor to reduce energy consumption
3. Setting up high efficient dust removal system to control the pollution emission.
4. Realize automatic operation of self-grinding system to improve stability.
We provide total solution for designing, manufacturing and installing cement production line.
We have self-developed advanced dry process cement production line with daily output of 50-3000 tons, which can be customized.
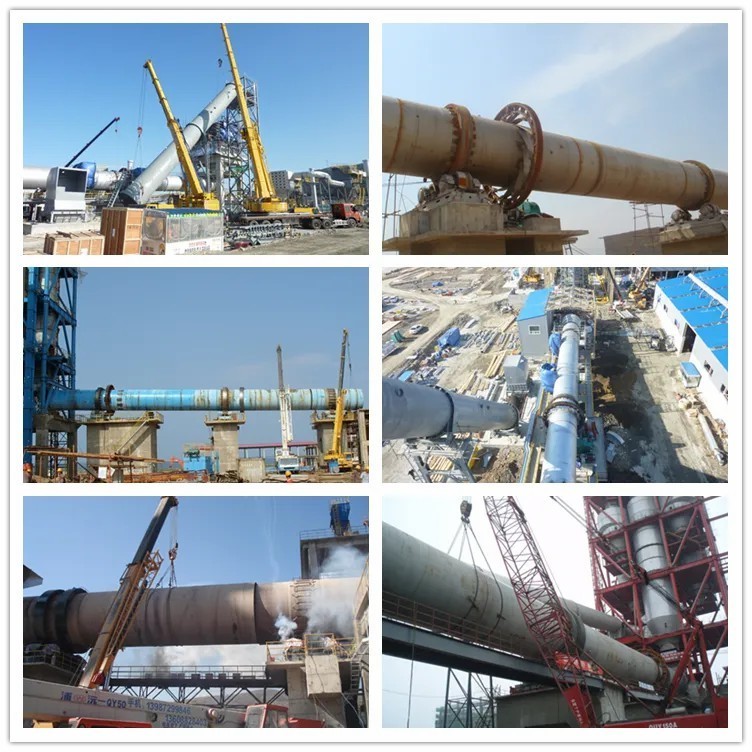
There are two main methods used in the blending process of cement manufacturing, namely, the dry process and the wet process.
a) Dry process:
1. The calcareous and muddy raw materials are firstly put into the gyratory crusher for crushing to get blocks of 2-5 cm size.
2. The crushed material is put into ball mill or tube mill again for fine grinding to get fine particles.
3. The finely ground material is screened and stored in a hopper.
4. Next, these powdered minerals are mixed in the required proportions to form a dry raw meal mixture which is stored in silos ready to be fed into the rotary kiln.
5. In the rotary kiln, the raw materials are mixed in specific proportions to ensure that the average composition of the final product remains appropriate.
b) Wet Process:
1. Raw materials are first crushed and made into powder form and then stored in silos.
2. the clay is washed in a scrubber mill to remove the organic matter adhering to the clay.
3. the powdered limestone and washed clay are fed into a channel, flowed and transferred to a mill where they are thoroughly mixed to form a paste known as slurry.
4. The grinding process can be carried out in a ball mill or a tube mill or even both.
5. The slurry is then introduced into a collection tank where its composition can be adjusted.
6. The slurry, which contains about 38-40% water, is stored in tanks and is ready for the rotary kiln.
It is important to note that the above process only covers the blending stage of the cement manufacturing process, the actual production process also includes other important steps such as calcination and cooling to obtain the final cement product.
Working Flow
Which one is better?
If we consider the quality and rate then wet process is better and if we consider fuel consumption and time of process then dry process is better. Difference between dry and wet process in table form:
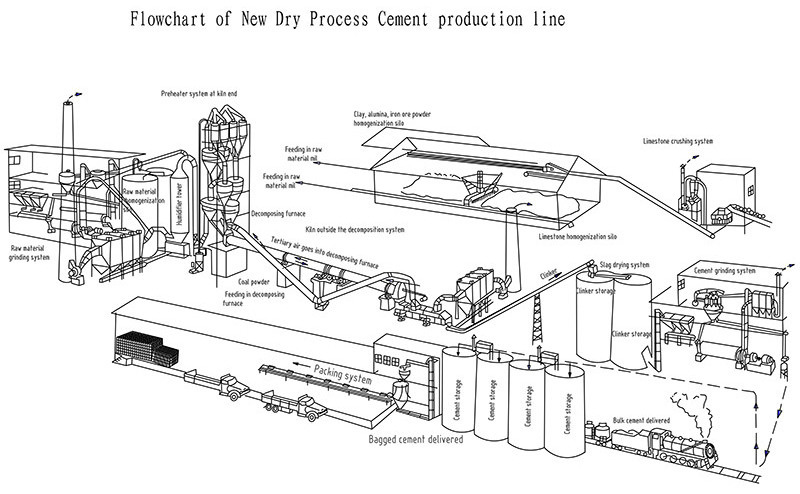
Dry Process
|
Wet Process
|
1. Mixing of raw material in dry state in blenders.
|
1. Mixing of Raw materials in wash mill with 35 to 50% water.
|
2. The dry materials exiting the mill are called “kiln feed”.
|
2. Materials exiting the mill are called “slurry” and have flowability characteristics.
|
3. Fuel consumption is low i.e., 100 kg of coal per tonne of cement produced
|
3. Fuel consumption is high i.e., 350 kg of coal per tonne of cement produced
|
4. Cost of production is less.
|
4. Cost of production is high
|
5. Capital cost is high due to blenders.
|
5. Capital cost (Cost of establishment) is comparatively less
|
6. Size of the kiln needed for manufacturing of cement is smaller.
|
6. Size of the kiln needed for manufacturing of cement is bigger.
|
7. Difficult to control mixing of Raw materials, so it is difficult to obtain a better homogeneous material.
|
7. Raw material can be mixed easily, so a better homogeneous material can be obtained
|
Main Equipment
Cement m
aking machinery
mainly includes crushing equipment, grinding equipment, calcination equipment, dust removal equipment, packaging equipment and preheater, coal mill, cooler, steel silo.
1. Crushing & Proportioning
Primary crushing involves limestone rock fed through large capacity crushers. This reduces the rock to a maximum size of approximately 150 mm. Secondary crushing further reduces this to 75mm or under. Residule material is stacked and reclaimed with a bridge reclaimer in a cross section so that the homogeneous limestone is fed further in the process. This averages the limestone quality.
Primary crushing involves limestone rock fed through large capacity crushers. This reduces the rock to a maximum size of approximately 150 mm. Secondary crushing further reduces this to 75mm or under. Residule material is stacked and reclaimed with a bridge reclaimer in a cross section so that the homogeneous limestone is fed further in the process. This averages the limestone quality.
2. Raw milling & Blending
Crushed particles are ground to 90 microns or less in a closed circuit ball mill with high efficiency separator. The raw meal is transferred to continuous blending silos (CFC) for homogenization ,extracted by load cell hopper for feeding to the kiln preheaters.
Crushed particles are ground to 90 microns or less in a closed circuit ball mill with high efficiency separator. The raw meal is transferred to continuous blending silos (CFC) for homogenization ,extracted by load cell hopper for feeding to the kiln preheaters.
3. Pyro processing
Raw material is heated to over 1,450 °C in a pre-heater tower,then through a pre-calciner and finally to the rotary kiln.
Raw material is heated to over 1,450 °C in a pre-heater tower,then through a pre-calciner and finally to the rotary kiln.
4. Burning
As the material progresses through the kiln, certain elements areremoved in the form of gases. The remaining elements unite to form a new substance (clinker) with new physical and chemical characteristics. Clinker is formed in small marble sized pieces
As the material progresses through the kiln, certain elements areremoved in the form of gases. The remaining elements unite to form a new substance (clinker) with new physical and chemical characteristics. Clinker is formed in small marble sized pieces
5. Cooling, Milling, Storage & Packing
Clinker is discharged from the kiln and the temperature is reduced in grate coolers. The hot air from the coolers is redirected back to the kiln, this saves fuel and increases burning efficiency.
Portland cement, the basic ingredient of concrete, is a combination of calcium, silicon, aluminum, iron and small amounts of other ingredients to which gypsum is added in the final grinding process to regulate the setting time of the concrete.
Our Advantages
Since the establishment of the company in 1995, it has developed into a large-scale enterprise integrating scientific research, production and sales. Our factory can produce cement production line equipment with various outputs, ensuring quality, timely delivery, and timely and efficient after-sales service.
Our senior technical engineers can provide solutions to the problems you encounter through online or quickly arrive at your production site at any time, and our experienced installation team can quickly and efficiently build and install your cement line factory, allowing you Produce cement products that meet the requirements in the shortest time, allowing you to see benefits in the shortest time.
Packing & Delivery
Customer Cases
500TPD Cement Production Line in
Philippines
1000TPD Cement Production Line in
Peru
2000TPD Cement Production Line in Oman
800TPD
Cement Production Line
in
Uzbekistan
Hot Searches