Traditional paint contains organic solvents (VOCs) that are harmful to the environment. The powder coating does not contain any organic solvent and is a powdery substance with the advantage of zero VOC emission, and is one of the best choices to replace traditional paint. In addition, as countries pay more and more attention to environmental protection, powder coating is one of the future development trends of the coatings industry.
In the filed of automotive, the wheel base powder coating changes from the traditional 4 coats to 3 coats, cancel the base paint, and use the base powder that integrates the bottom surface, which has become a new development direction. With the use of this process, the zero VOC characteristics of powder coatings can reduce VOC emissions by about 20% during the entire coating process, reduce coating processes, increase efficiency, and increase yield.
The wheel base powder coating developed by KINTE has high leveling and good air permeability. It is suitable for curing at 180°C, which can greatly reduce the energy consumption and production cost of manufacturers. This product has good physical properties and chemical resistance, and can meet the requirements of various wheel manufacturers for high leveling, low baking temperature, good chemical resistance and excellent physical properties
Explore More Products
- Product Details
- {{item.text}}
Quick Details
-
EINECS No.:
-
/
-
Place of Origin:
-
Guangdong, China
-
Brand Name:
-
Kinte
-
Model Number:
-
JW-A1701B
-
Color:
-
Black Matt
-
Apperance:
-
Smooth and Flat
-
Advantages:
-
Good Physical Properties and Chemical Resistance
-
Application:
-
Inner Wheel-hub Protection
-
Application Craft:
-
Electrostatic Spraying Method (50-80Kv)
-
Curing Conditions:
-
180°C/8-15min (Actual temperature of workpiece)
-
Film Thickness:
-
80 ~ 100 μm
-
Storage:
-
6 Months in dry cool conditions below 28°C
Quick Details
-
CAS No.:
-
/
-
Other Names:
-
/
-
MF:
-
/
-
EINECS No.:
-
/
-
Place of Origin:
-
Guangdong, China
-
Brand Name:
-
Kinte
-
Model Number:
-
JW-A1701B
-
Color:
-
Black Matt
-
Apperance:
-
Smooth and Flat
-
Advantages:
-
Good Physical Properties and Chemical Resistance
-
Application:
-
Inner Wheel-hub Protection
-
Application Craft:
-
Electrostatic Spraying Method (50-80Kv)
-
Curing Conditions:
-
180°C/8-15min (Actual temperature of workpiece)
-
Film Thickness:
-
80 ~ 100 μm
-
Storage:
-
6 Months in dry cool conditions below 28°C
Products Description
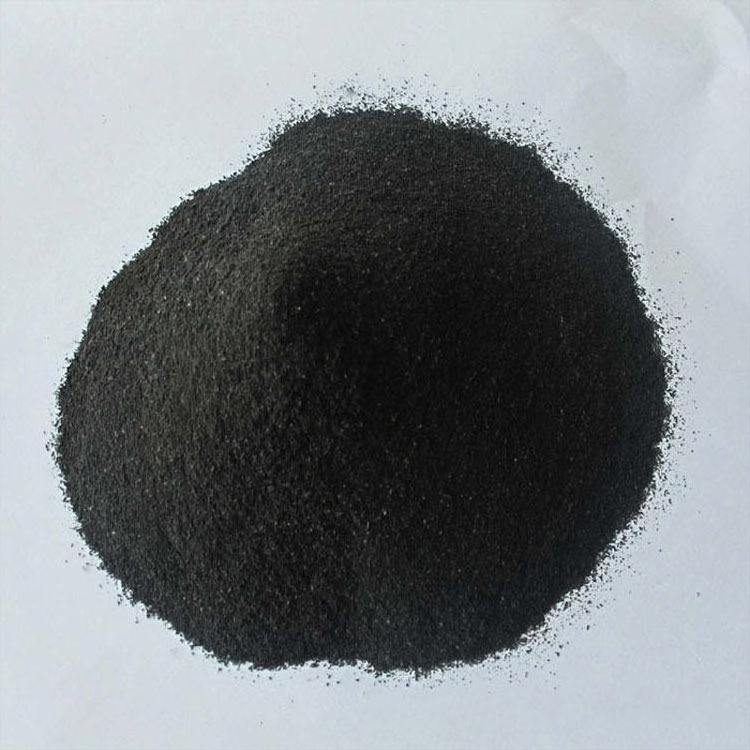
Introduction
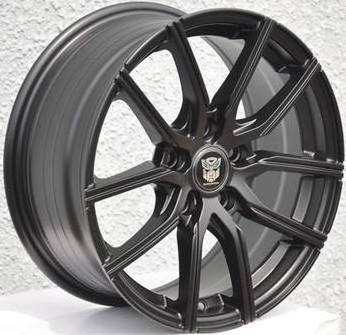
Basic Features
1. Better scratch resistance. The surface of the aluminum alloy wheel hub is mostly rough casting surface. Because the powder is solvent-free, it shows good "filling and concealing properties", and is applied to the first coating of the wheel hub to cover surface defects.
2. Better stone resistance. Because it does not contain solvents, powder coatings are not easy to sag, and it is easy to achieve "single-layer high film thickness". Compared with the complex multi-coat liquid paint process, the single-layer powder primer shows better stone resistance performance.
Application
A range of automotive wheel hubs for different requirements and coating characteristics
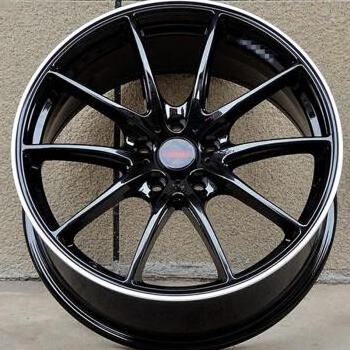
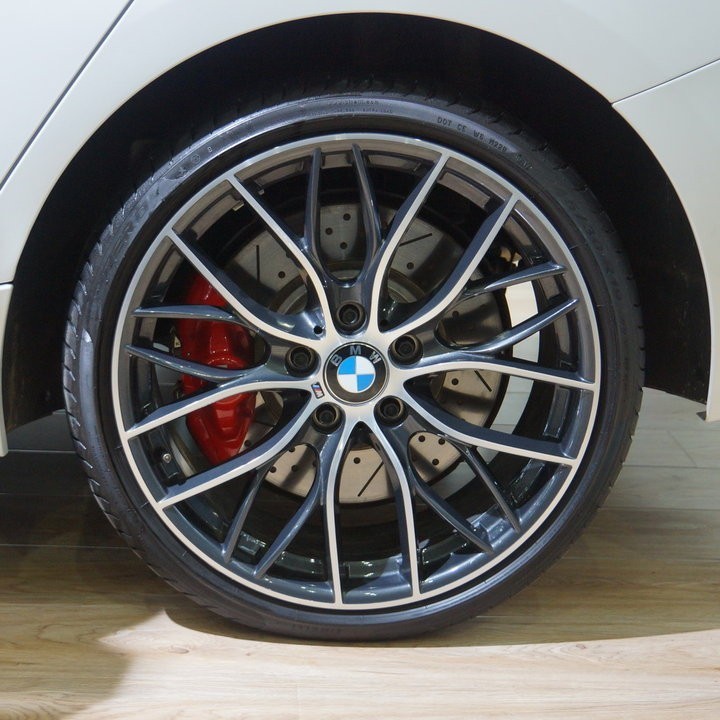
Specifications
Properties
|
Test Method
|
Test Result
|
Color
|
Visual inspection
|
Black
|
Appearance
|
Visual inspection
|
Smooth and flat
|
Gloss
|
GB/T 9754-2007
|
15-25 (60°)
|
Adhesion
|
GB/T 9286-1998
|
Grade 0
|
Hardness
|
GB/T 6739-2006
|
H (Pencil Hardness)
|
Impact Resistance
|
GB/T 1732-1993
|
50Kg·cm
|
Flexibility
|
GB/T 1731-1993
|
2mm
|
CASS
|
GB/T 10125
|
240 hours pass
|
Water Resistant
|
GB/T 1733-1993
|
240 hours pass
|
Salt Spray
|
GB/T 1771-2007
|
1000 hours pass
|
Spray Process Parameters
Application Craft: Electrostatic Spraying Method (50-80Kv)
Humidity of Spraying Work Environment: ≤ 85%
Spraying Working Environment Temperature: 0°C - 35°C
Powder Supply Air Pressure: 0.2~0.4MPa
Atomizing Air Pressure: 0.01~0.1MPa
Distance between Workpiece and Nozzle: 20~30cm
Recommended Baking Conditions: 180°C/8-15min (Actual temperature of workpiece)
Volatile Organic Compounds: Basically zero
Density: 1.2-1.7 g/cc
Theoretical Coating Area: 9-12m
2
/Kg
Dust Explosion Safety: Ignition point 470°C, explosion limit: 20~30 g/m
3
Shelf Life: 28°C/ 6 months
Healthe and Safety: The operator should wear a dust mask, and try to minimize the long-term contact between the skin and the powder coating. The coating attached to the skin can be washed with soap.
Package and Transportation
Carton packaging, net weight 20 or 25kg, 1000kg per pallet.
Non-dangerous goods, no special transportation requirements.
Store in a cool, dry place below 28°C.
Shelf Life: 6 months.
Hot Searches